What are Spring-loaded Pins?
Spring-loaded pins are electrical connectors that consist of a cylindrical pin and a spring mechanism. The pin is typically made of a conductive material, such as brass or beryllium copper, and is plated with gold, silver, or other metals to enhance conductivity and durability. The spring mechanism, which is usually a coil spring or a flat spring, is housed inside the pin and provides a constant force to maintain contact between the pin and the mating surface.
When the spring-loaded pin is compressed, the spring mechanism allows the pin to retract, ensuring a stable connection even in the presence of vibrations, shocks, or misalignments. Once the compression force is removed, the spring pushes the pin back to its original position, breaking the electrical connection.
Construction of Spring-loaded Pins
The construction of spring-loaded pins involves several components:
Pin: The pin is the conductive element that establishes the electrical connection. It is typically made of a high-quality, conductive material and is plated to enhance its properties.
Spring: The spring mechanism is responsible for providing the necessary force to maintain a stable connection. Coil springs and flat springs are the most common types used in spring-loaded pins.
Barrel: The barrel is the housing that contains the pin and the spring. It is usually made of an insulating material, such as plastic or ceramic, to prevent short circuits and provide mechanical support.
Retainer: The retainer is a component that holds the pin and the spring in place within the barrel. It can be a separate piece or an integral part of the barrel.
Plunger: In some designs, a plunger is used to guide the pin and provide additional stability. The plunger is typically made of an insulating material and has a hole through which the pin can move.
Types of Spring-loaded Pins
There are several types of spring-loaded pins, each with its own characteristics and applications:
Pogo Pins: Pogo pins are the most common type of spring-loaded pins. They have a cylindrical shape and use a coil spring to provide the contact force. Pogo pins are widely used in test and measurement equipment, battery chargers, and docking stations.
Stamped Spring Pins: Stamped spring pins are made by stamping a flat metal sheet into the desired shape. They are more cost-effective than pogo pins and are often used in high-volume applications, such as automotive connectors and consumer electronics.
Telescopic Spring Pins: Telescopic spring pins consist of multiple sections that collapse into each other when compressed. They offer a longer stroke than pogo pins and are suitable for applications with significant misalignments or large gaps.
Butterfly Spring Pins: Butterfly spring pins have a unique design that resembles a butterfly shape. They provide a high contact force and are resistant to vibrations and shocks, making them ideal for automotive and industrial applications.
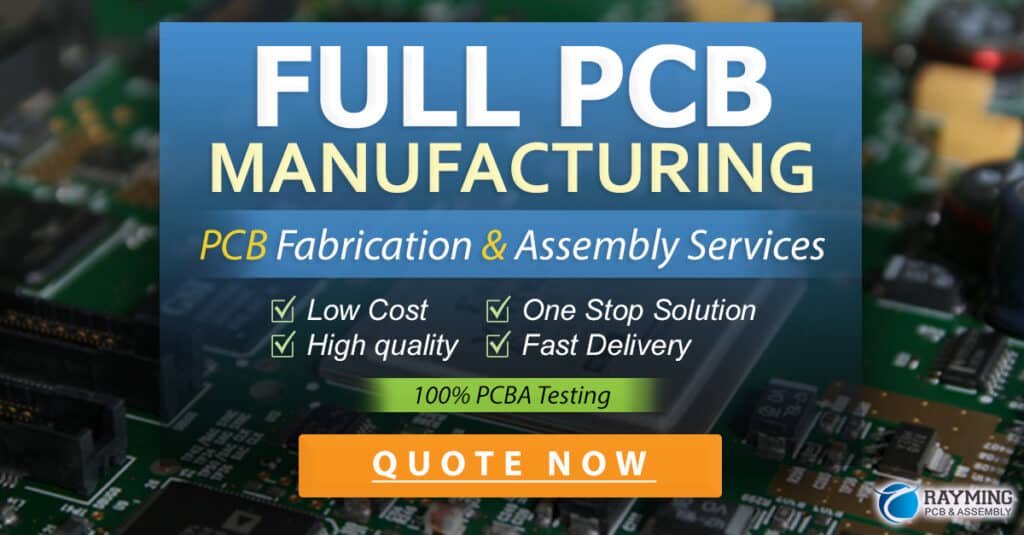
Applications of Spring-loaded Pins
Spring-loaded pins find applications in various industries and products:
- Consumer Electronics:
- Battery chargers
- Docking stations
- Wearable devices
Smartphones and tablets
Automotive:
- Airbag connectors
- Seat belt sensors
- Infotainment systems
Diagnostic tools
Medical Devices:
- Portable medical equipment
- Disposable sensors
- Defibrillators
Monitoring systems
Industrial Equipment:
- Test and measurement devices
- Robotics
- Automation systems
Sensors and transducers
Aerospace and Defense:
- Avionics
- Satellite communication systems
Military equipment
Telecommunications:
- Base stations
- Switching systems
- Routers and modems
Advantages of Spring-loaded Pins
Spring-loaded pins offer several advantages over other types of electrical connectors:
Reliability: The spring mechanism ensures a stable and reliable connection, even in the presence of vibrations, shocks, or misalignments. This reliability is crucial in applications where a loss of connection can lead to system failures or safety hazards.
Durability: Spring-loaded pins are designed to withstand numerous mating cycles without significant wear or degradation. The use of high-quality materials and plating techniques further enhances their durability, making them suitable for long-term use.
Compact Size: Spring-loaded pins have a small footprint, allowing for high-density packaging in electronic devices. This is particularly important in applications where space is limited, such as smartphones, wearables, and medical devices.
Ease of Use: Spring-loaded pins do not require soldering or other permanent attachment methods. They can be easily inserted into and removed from their mating surfaces, simplifying the assembly and maintenance processes.
Versatility: Spring-loaded pins can be customized to meet specific application requirements. Factors such as pin size, spring force, stroke length, and plating materials can be tailored to optimize performance and reliability.
Cost-effectiveness: While the initial cost of spring-loaded pins may be higher than other connector types, their reliability, durability, and ease of use can lead to lower overall system costs by reducing maintenance and repair expenses.
Choosing the Right Spring-loaded Pin
When selecting a spring-loaded pin for a specific application, several factors should be considered:
Electrical Requirements: The pin should have the appropriate current carrying capacity, voltage rating, and contact resistance to meet the electrical demands of the application.
Mechanical Requirements: The pin should withstand the expected number of mating cycles, stroke length, and contact force without excessive wear or damage.
Environmental Conditions: The pin should be able to operate reliably in the expected environmental conditions, such as temperature, humidity, and chemical exposure.
Mating Surface: The pin should be compatible with the mating surface material and geometry to ensure proper contact and prevent damage.
Size and Packaging: The pin should fit within the available space and be compatible with the desired packaging method, such as through-hole or surface-mount.
Consulting with a qualified connector manufacturer or supplier can help in selecting the most suitable spring-loaded pin for a given application.
FAQ
What is the difference between a pogo pin and a spring-loaded pin?
Pogo pins are a specific type of spring-loaded pin that have a cylindrical shape and use a coil spring. The term “spring-loaded pin” is a broader category that includes pogo pins and other pin designs, such as stamped spring pins and telescopic spring pins.Can spring-loaded pins be used for high-current applications?
Yes, spring-loaded pins can be designed to carry high currents. The current carrying capacity depends on factors such as pin size, material, and plating. Consult with a connector manufacturer to determine the appropriate pin specifications for your application.How long do spring-loaded pins last?
The lifespan of spring-loaded pins depends on several factors, including the number of mating cycles, contact force, and environmental conditions. High-quality pins can withstand thousands to millions of mating cycles with proper design and maintenance.Are spring-loaded pins suitable for outdoor applications?
Spring-loaded pins can be used in outdoor applications if they are properly sealed and protected from environmental factors such as moisture, dirt, and corrosion. Special plating materials and sealing methods can be employed to enhance their durability in harsh environments.How do I choose the right spring force for my application?
The spring force should be selected based on the specific requirements of the application, such as the mating force, stroke length, and contact stability. A higher spring force provides a more stable connection but may increase wear and mating force. Consult with a connector manufacturer or supplier to determine the optimal spring force for your application.
Conclusion
Spring-loaded pins are versatile and reliable electrical connectors that are essential in a wide range of applications, from consumer electronics to industrial equipment. Their unique construction, which combines a conductive pin with a spring mechanism, enables them to establish stable connections even in challenging conditions. By understanding the types, applications, and advantages of spring-loaded pins, engineers and designers can select the most suitable connector for their specific needs, ensuring optimal performance and reliability in their products.
Type | Description | Applications |
---|---|---|
Pogo Pins | Cylindrical shape, coil spring | Test equipment, battery chargers, docking stations |
Stamped Spring Pins | Made by stamping a flat metal sheet | High-volume applications, automotive connectors, consumer electronics |
Telescopic Spring Pins | Multiple sections that collapse into each other | Applications with significant misalignments or large gaps |
Butterfly Spring Pins | Butterfly-shaped design, high contact force | Automotive and industrial applications |
When choosing a spring-loaded pin, it is essential to consider factors such as electrical and mechanical requirements, environmental conditions, mating surface compatibility, and packaging constraints. Working closely with a qualified connector manufacturer or supplier can help ensure the selection of the most appropriate spring-loaded pin for a given application, optimizing performance, reliability, and cost-effectiveness.
Leave a Reply