Introduction to Soldering PCB
Soldering PCB (Printed Circuit Board) is a critical process in the manufacturing of electronic devices. It involves joining electronic components to the conductive traces on a PCB using a molten metal alloy called solder. The solder creates a strong electrical and mechanical bond between the components and the PCB, ensuring reliable functionality of the electronic device.
The Importance of Soldering PCB
Soldering PCB is essential for several reasons:
- Electrical Connectivity: Soldering ensures a secure electrical connection between components and the PCB, allowing the device to function as intended.
- Mechanical Stability: Soldered joints provide mechanical strength to the components, preventing them from moving or detaching from the PCB during use or handling.
- Reliability: Properly soldered joints ensure the long-term reliability of the electronic device, minimizing the risk of failure due to loose or broken connections.
Types of Soldering Techniques
There are two primary soldering techniques used in PCB assembly:
Through-Hole Soldering
Through-hole soldering involves inserting component leads through pre-drilled holes in the PCB and soldering them on the opposite side. This technique is used for larger components, such as connectors, transformers, and some types of capacitors and resistors.
Advantages of through-hole soldering:
– Stronger mechanical bond
– Easier to inspect and repair
– Suitable for high-power applications
Disadvantages of through-hole soldering:
– Requires more manual labor
– Consumes more space on the PCB
– Slower assembly process compared to surface mount soldering
Surface Mount Soldering
Surface mount soldering involves placing components directly onto the surface of the PCB and soldering them in place. Surface mount components (SMDs) are smaller and have shorter leads or no leads at all, allowing for higher component density on the PCB.
Advantages of surface mount soldering:
– Smaller PCB size and higher component density
– Faster assembly process
– Lower cost for high-volume production
Disadvantages of surface mount soldering:
– Requires specialized equipment for placement and soldering
– More difficult to inspect and repair
– Not suitable for high-power applications
Soldering PCB Process
The soldering PCB process involves several steps:
-
PCB Design and Fabrication: The PCB is designed using CAD software and fabricated according to the design specifications.
-
Solder Paste Application: Solder paste, a mixture of tiny solder particles and flux, is applied to the PCB pads using a stencil or syringe.
-
Component Placement: Components are placed onto the PCB, either manually or using automated pick-and-place machines.
-
Reflow Soldering: The PCB with the placed components is passed through a reflow oven, which melts the solder paste and creates a strong bond between the components and the PCB.
-
Inspection and Testing: The soldered PCB is visually inspected for defects and tested for proper functionality.
Soldering PCB Equipment
To perform soldering PCB effectively, the following equipment is commonly used:
Equipment | Description |
---|---|
Soldering Iron | A hand tool that heats up to melt the solder and create a joint between the component and the PCB. |
Solder | A metal alloy, typically consisting of tin, lead, and other elements, used to create the electrical and mechanical bond. |
Flux | A chemical agent that helps to remove oxides from the surfaces being soldered and improves the wetting of the solder. |
Solder Wick | A braided copper wire used to remove excess solder from joints or to desolder components. |
Solder Paste | A mixture of tiny solder particles and flux used in surface mount soldering. |
Reflow Oven | An oven that heats the PCB and components to a specific temperature profile to melt the solder paste and create the solder joints. |
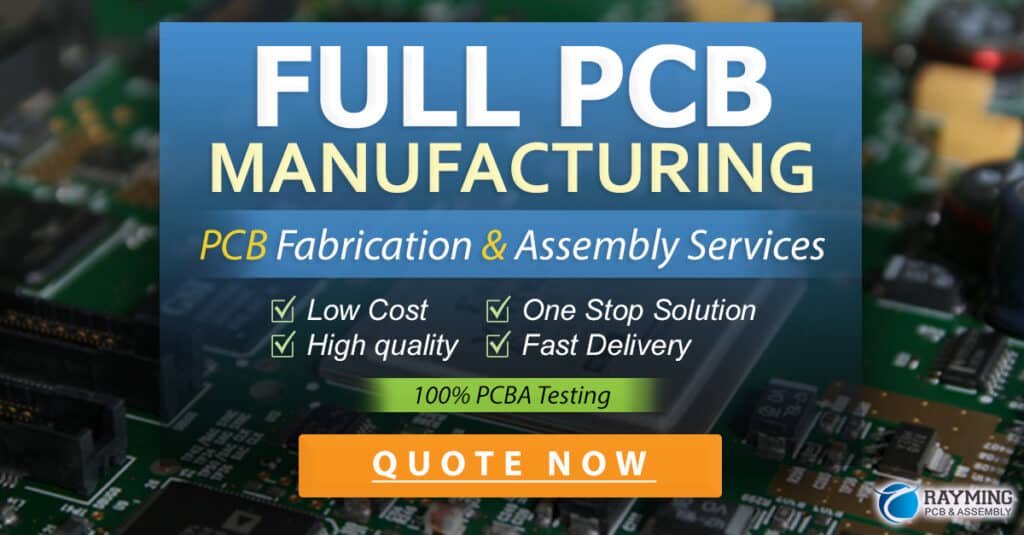
Soldering PCB Best Practices
To ensure high-quality soldering PCB, follow these best practices:
- Use the appropriate solder and flux for the application.
- Maintain proper soldering iron temperature and tip cleanliness.
- Apply the right amount of solder to create a strong joint without excess.
- Ensure proper component placement and alignment before soldering.
- Follow the recommended reflow temperature profile for the solder paste used.
- Inspect the soldered joints for defects, such as bridging, insufficient solder, or cold joints.
- Clean the PCB after soldering to remove flux residue and prevent corrosion.
Common Soldering PCB Defects and Solutions
Despite following best practices, soldering PCB defects can still occur. Some common defects and their solutions include:
Defect | Description | Solution |
---|---|---|
Bridging | Solder connecting adjacent pads or traces | Use solder wick to remove the excess solder |
Cold Joint | Dull, rough, or cracked solder joint caused by insufficient heat or poor wetting | Reheat the joint and apply additional solder if necessary |
Insufficient Solder | Too little solder, resulting in a weak joint | Apply more solder to the joint |
Tombstoning | One end of a surface mount component lifts off the PCB during reflow | Ensure proper solder paste application and component placement |
Solder Balls | Tiny balls of solder that can cause short circuits | Use a finer solder mesh or adjust the reflow profile |
Advanced Soldering PCB Techniques
As PCB designs become more complex, advanced soldering techniques may be required:
Selective Soldering
Selective soldering is a process that targets specific areas of the PCB for soldering, rather than the entire board. This technique is useful for soldering through-hole components on a board that primarily uses surface mount components.
Rework and Repair
Rework and repair involve removing and replacing defective components or correcting soldering defects on an assembled PCB. Specialized tools, such as hot air rework stations and desoldering pumps, are used for these tasks.
Automated Soldering
Automated soldering uses machines to perform the soldering process, improving consistency, speed, and accuracy. Examples include wave soldering for through-hole components and selective soldering machines for targeted areas.
FAQ
-
Q: What is the difference between lead-based and lead-free solder?
A: Lead-based solder contains a mixture of tin and lead, while lead-free solder is typically made of tin, silver, and copper. Lead-free solder is becoming more common due to environmental and health concerns associated with lead. -
Q: Can I mix different types of solder?
A: It is generally not recommended to mix different types of solder, as they may have different melting temperatures and properties. Mixing solders can lead to poor joint quality and reliability issues. -
Q: How do I choose the right soldering iron tip?
A: The choice of soldering iron tip depends on the size and type of components being soldered. Use a tip that is appropriately sized for the job – smaller tips for fine pitch components and larger tips for larger components or heat-sensitive areas. -
Q: What is the purpose of flux in soldering?
A: Flux is used to remove oxides from the surfaces being soldered, improving the wetting and flow of the solder. It also helps to prevent oxidation during the soldering process, ensuring a strong and reliable joint. -
Q: How can I improve my soldering PCB skills?
A: To improve your soldering PCB skills, practice regularly on scrap boards or practice kits, watch instructional videos or attend workshops, and always follow best practices for soldering. Experimenting with different techniques and tools can also help you develop your skills and find what works best for you.
Conclusion
Soldering PCB is a vital process in the manufacturing of electronic devices, ensuring strong electrical and mechanical connections between components and the PCB. By understanding the different soldering techniques, best practices, and common defects, you can create high-quality soldered joints and reliable electronic assemblies. As PCB designs continue to evolve, staying up-to-date with advanced soldering techniques and technologies will be essential for success in the field.
Leave a Reply