Introduction to Solder Mask in PCB
Solder mask, also known as solder resist or solder stop, is a crucial component in the manufacturing of printed circuit boards (PCBs). It is a thin, protective layer applied to the copper traces and pads on a PCB, leaving only the areas that need to be soldered exposed. The primary purpose of the solder mask is to prevent solder bridges from forming between adjacent traces during the soldering process, which could lead to short circuits and other issues.
Key Functions of Solder Mask in PCB
- Insulation: Solder mask acts as an insulating layer, preventing accidental contact between components and traces.
- Protection: It protects the copper traces from oxidation, corrosion, and other environmental factors that could degrade the PCB’s performance over time.
- Aesthetics: Solder mask gives the PCB a clean, professional appearance and can be used to add branding or other visual elements.
Types of Solder Mask
There are several types of solder mask available, each with its own unique properties and advantages. The most common types include:
Liquid Photoimageable Solder Mask (LPISM)
LPISM is the most widely used type of solder mask in the PCB industry. It is applied as a liquid coating and then exposed to UV light through a photomask, which hardens the exposed areas while leaving the unexposed areas soluble. The soluble areas are then removed using a developer solution, revealing the copper pads and traces that need to be soldered.
Advantages of LPISM:
– High resolution and accuracy
– Excellent adhesion to the PCB surface
– Good resistance to chemicals and solvents
– Available in a variety of colors
Dry Film Solder Mask (DFSM)
DFSM is a solid film that is laminated onto the PCB surface using heat and pressure. Like LPISM, it is exposed to UV light through a photomask and then developed to remove the unexposed areas.
Advantages of DFSM:
– Faster application process compared to LPISM
– Consistent thickness across the entire PCB surface
– Good resistance to chemicals and solvents
– Suitable for high-volume production
Liquid Ink Solder Mask
Liquid ink solder mask is applied using a screen printing process, where the ink is forced through a mesh screen onto the PCB surface. It is then cured using heat or UV light to harden the mask.
Advantages of Liquid Ink Solder Mask:
– Lower cost compared to LPISM and DFSM
– Faster application process
– Suitable for low-volume production and prototype PCBs
Solder Mask Application Process
The solder mask application process varies depending on the type of mask being used, but the general steps are as follows:
-
PCB Cleaning: The PCB surface is thoroughly cleaned to remove any dirt, grease, or other contaminants that could affect the adhesion of the solder mask.
-
Solder Mask Application: The chosen type of solder mask is applied to the PCB surface, either as a liquid coating (LPISM), a dry film (DFSM), or a screen-printed ink.
-
Exposure: The solder mask is exposed to UV light through a photomask, which hardens the exposed areas while leaving the unexposed areas soluble (for LPISM and DFSM) or uncured (for liquid ink).
-
Development: The unexposed or uncured areas of the solder mask are removed using a developer solution (for LPISM and DFSM) or washed away (for liquid ink), revealing the copper pads and traces that need to be soldered.
-
Curing: The remaining solder mask is fully cured using heat or UV light to ensure good adhesion and durability.
-
Inspection: The PCB is inspected for any defects or imperfections in the solder mask, such as pinholes, bubbles, or misalignment.
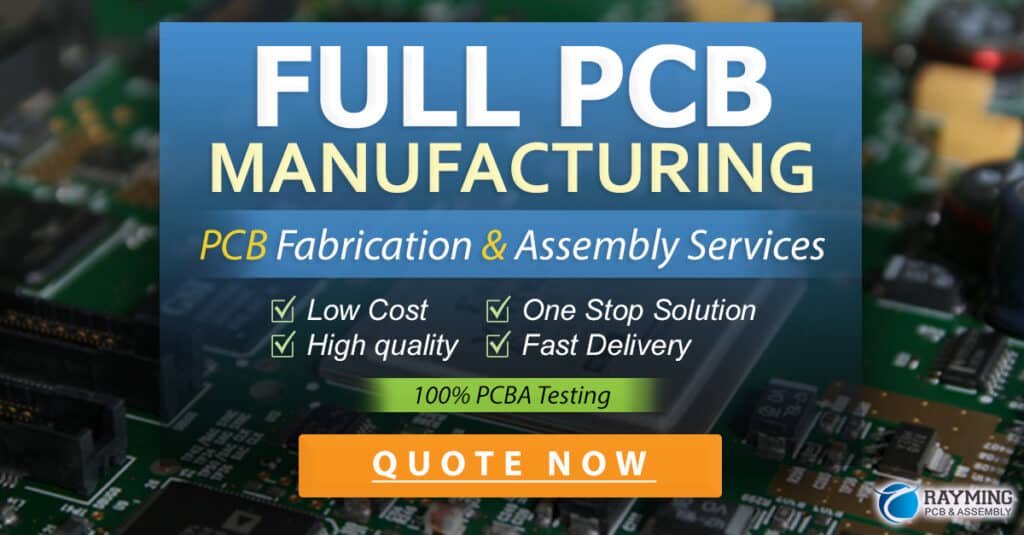
Solder Mask Color Options
Solder mask is available in a variety of colors, with green being the most common. Other popular color options include:
- Blue
- Red
- Yellow
- Black
- White
- Purple
The choice of solder mask color is often based on aesthetic preferences or for functional purposes, such as improving the visibility of certain components or making it easier to identify different versions of a PCB.
Solder Mask Design Considerations
When designing a PCB with solder mask, there are several important considerations to keep in mind:
Solder Mask Clearance
Solder mask clearance refers to the distance between the edge of a copper pad or trace and the edge of the solder mask opening. It is important to maintain adequate clearance to ensure proper soldering and to avoid solder mask encroachment, which can lead to poor solder joints or difficulties in component placement.
Typical solder mask clearance values range from 0.1 mm to 0.25 mm, depending on the size of the pads and the precision of the solder mask application process.
Solder Mask Thickness
The thickness of the solder mask can affect its insulating properties and durability. Typical solder mask thicknesses range from 0.01 mm to 0.03 mm, with thicker masks providing better insulation and protection against scratches and other mechanical damage.
However, thicker solder masks can also make it more difficult to achieve fine details and small openings, so a balance must be struck based on the specific requirements of the PCB design.
Solder Mask Finish
The surface finish of the solder mask can impact its appearance and performance. Common solder mask finishes include:
- Glossy: A smooth, shiny surface that provides good protection against moisture and other environmental factors.
- Matte: A non-reflective surface that reduces glare and improves the readability of text and markings on the PCB.
- Semi-matte: A compromise between glossy and matte finishes, offering good protection and readability.
The choice of solder mask finish depends on the intended use of the PCB and any specific aesthetic or functional requirements.
Solder Mask and PCB Assembly
The presence of solder mask on a PCB has a significant impact on the assembly process, particularly during soldering.
Solder Mask and Solderability
Solder mask plays a crucial role in ensuring good solderability by preventing the formation of solder bridges between adjacent pads and traces. By limiting the spread of molten solder, solder mask helps to create clean, well-defined solder joints that are both electrically and mechanically sound.
However, solder mask can also impede solderability if it is not applied correctly or if the openings in the mask are too small. This can lead to poor wetting of the pads and difficulty in achieving reliable solder joints.
Solder Mask and Component Placement
Solder mask also affects the placement of components on the PCB. The openings in the solder mask must be large enough to accommodate the component leads or pads, while still providing adequate clearance to prevent shorts and other issues.
In some cases, specialized solder mask designs may be required to accommodate specific component packages or to enable certain assembly techniques, such as surface mount technology (SMT) or through-hole mounting.
Solder Mask Defects and Quality Control
Solder mask defects can have a significant impact on the reliability and performance of a PCB. Common solder mask defects include:
- Pinholes: Small holes in the solder mask that expose the underlying copper, which can lead to shorts or corrosion.
- Bubbles: Air pockets trapped in the solder mask during application, which can cause localized thinning or cracking of the mask.
- Misalignment: Incorrect positioning of the solder mask relative to the copper pads and traces, which can result in exposed copper or insufficient clearance.
- Contamination: Foreign particles or residues embedded in the solder mask, which can affect its insulating properties or cause adhesion issues.
To ensure the quality of solder mask on PCBs, manufacturers employ various quality control measures, such as:
- Visual inspection: Manual or automated inspection of the PCB surface to identify any visible defects or irregularities in the solder mask.
- Electrical testing: Continuity and insulation resistance tests to verify the integrity of the solder mask and the absence of shorts or leakage paths.
- Adhesion testing: Peel tests or cross-hatch tests to assess the bond strength between the solder mask and the PCB surface.
- Thickness measurement: Verification of solder mask thickness using optical or mechanical methods to ensure compliance with specifications.
By implementing strict quality control procedures and addressing any identified defects, PCB manufacturers can ensure that the solder mask on their products meets the required standards of reliability and performance.
Future Trends in Solder Mask Technology
As PCB technology continues to advance, solder mask materials and application processes are also evolving to meet the changing needs of the industry. Some of the key trends and developments in solder mask technology include:
High-Temperature Solder Masks
With the increasing use of lead-free solders, which require higher reflow temperatures, there is a growing demand for solder masks that can withstand these elevated temperatures without degrading or losing their insulating properties. New high-temperature solder mask formulations are being developed to address this need, enabling the reliable assembly of lead-free PCBs.
Photoimageable Dielectric Materials
Photoimageable dielectric materials are a newer class of solder masks that offer improved resolution and finer pitch capabilities compared to traditional LPISM and DFSM. These materials are applied as a dry film and then photoimaged and developed to create the desired solder mask pattern, enabling the fabrication of high-density PCBs with smaller features and tighter tolerances.
Inkjet Solder Mask Printing
Inkjet printing technology is being adapted for the application of solder mask, offering several potential advantages over traditional methods. Inkjet printing allows for the precise deposition of solder mask material, reducing waste and enabling the creation of more complex patterns and designs. This technology also has the potential to simplify the solder mask application process and reduce costs, particularly for low-volume or prototype PCBs.
Environmentally Friendly Solder Masks
There is a growing focus on developing solder mask materials and processes that are more environmentally friendly and sustainable. This includes the use of water-based solder mask formulations, which reduce the need for harmful solvents, as well as the development of biodegradable or recyclable solder mask materials. These eco-friendly alternatives aim to minimize the environmental impact of PCB manufacturing while still providing the necessary protection and performance.
As these and other trends continue to shape the future of solder mask technology, PCB manufacturers and designers will need to stay informed and adapt their processes and materials accordingly to remain competitive and meet the evolving demands of the electronics industry.
Frequently Asked Questions (FAQ)
- What is the purpose of solder mask on a PCB?
-
The primary purpose of solder mask is to prevent solder bridges from forming between adjacent traces during the soldering process, which could lead to short circuits and other issues. Additionally, solder mask acts as an insulating layer, protects the copper traces from oxidation and corrosion, and provides a clean, professional appearance to the PCB.
-
What are the most common types of solder mask used in PCB manufacturing?
-
The most common types of solder mask are Liquid Photoimageable Solder Mask (LPISM), Dry Film Solder Mask (DFSM), and Liquid Ink Solder Mask. LPISM is the most widely used type, offering high resolution and accuracy, while DFSM is suitable for high-volume production. Liquid Ink Solder Mask is a lower-cost option for low-volume production and prototype PCBs.
-
What factors should be considered when choosing a solder mask color for a PCB?
-
The choice of solder mask color is often based on aesthetic preferences or for functional purposes, such as improving the visibility of certain components or making it easier to identify different versions of a PCB. Green is the most common color, but other popular options include blue, red, yellow, black, white, and purple.
-
How does solder mask affect the PCB assembly process, particularly during soldering?
-
Solder mask plays a crucial role in ensuring good solderability by preventing the formation of solder bridges between adjacent pads and traces. It helps to create clean, well-defined solder joints that are both electrically and mechanically sound. However, solder mask can also impede solderability if it is not applied correctly or if the openings in the mask are too small.
-
What are some common solder mask defects, and how can they be addressed through quality control measures?
- Common solder mask defects include pinholes, bubbles, misalignment, and contamination. To ensure the quality of solder mask on PCBs, manufacturers employ various quality control measures, such as visual inspection, electrical testing, adhesion testing, and thickness measurement. By implementing strict quality control procedures and addressing any identified defects, PCB manufacturers can ensure that the solder mask on their products meets the required standards of reliability and performance.
Solder Mask Type | Application Method | Advantages |
---|---|---|
Liquid Photoimageable Solder Mask (LPISM) | Applied as a liquid coating and exposed to UV light | High resolution and accuracy, excellent adhesion, good chemical resistance, available in various colors |
Dry Film Solder Mask (DFSM) | Laminated onto the PCB surface using heat and pressure | Faster application process, consistent thickness, good chemical resistance, suitable for high-volume production |
Liquid Ink Solder Mask | Applied using a screen printing process and cured with heat or UV light | Lower cost, faster application process, suitable for low-volume production and prototype PCBs |
Leave a Reply