What is Silkscreen on PCB?
Silkscreen, also known as legend or nomenclature, is a layer of text, symbols, and graphics printed on the surface of a PCB. This layer is typically white, although other colors can be used for specific applications or to enhance visibility. The silkscreen layer serves several important functions, which we will discuss in detail throughout this article.
The Purpose of Silkscreen on PCB
The primary purpose of silkscreen on PCB is to provide clear and concise information about the board’s components, connectors, and other features. This information is crucial for several reasons:
-
Assembly: Silkscreen guides the assembly process, ensuring that components are placed in the correct locations and orientations. This is particularly important for surface-mount devices (SMDs) and other small components that can be easily misplaced.
-
Debugging and Troubleshooting: When a PCB malfunctions, the silkscreen layer helps technicians identify components and trace connections, making it easier to diagnose and fix issues.
-
User Interaction: Silkscreen often includes labels for connectors, switches, and LEDs, making it easier for users to interact with the device and understand its functions.
-
Branding and Aesthetics: In addition to functional information, silkscreen can also include company logos, product names, and other branding elements, enhancing the overall appearance of the PCB.
The Silkscreen Printing Process
Silkscreen printing on PCBs is a specialized process that involves several steps to ensure high-quality, durable results. The process typically follows these stages:
-
Artwork Preparation: The silkscreen artwork is created using PCB design software, such as Altium Designer or KiCad. The artwork includes all the text, symbols, and graphics that will be printed on the PCB surface.
-
Screen Preparation: A fine mesh screen, usually made of polyester or stainless steel, is coated with a light-sensitive emulsion. The silkscreen artwork is then exposed onto the emulsion, creating a stencil of the desired pattern.
-
Ink Application: A squeegee is used to push the ink through the stencil onto the PCB surface. The ink is specially formulated to adhere to the PCB material and withstand the harsh conditions of the electronic manufacturing process.
-
Curing: After printing, the ink is cured using heat or ultraviolet (UV) light to ensure a strong bond with the PCB surface and prevent smudging or fading.
Silkscreen Ink Types
There are two main types of ink used for silkscreen printing on PCBs:
-
Epoxy-based Ink: This type of ink is the most common and offers excellent durability, adhesion, and resistance to chemicals and abrasion. Epoxy-based inks are cured using heat and provide a long-lasting, high-quality finish.
-
UV-curable Ink: UV-curable inks are a newer alternative that offer faster curing times and improved environmental friendliness. These inks are cured using UV light and provide similar durability and resistance to epoxy-based inks.
Silkscreen Design Considerations
When designing the silkscreen layer for a PCB, several factors must be considered to ensure optimal readability, clarity, and manufacturability. Some key considerations include:
Font Selection
Choosing the right font for your silkscreen design is crucial for ensuring legibility and consistency. Some guidelines for font selection include:
- Use sans-serif fonts for better readability at small sizes
- Maintain consistent font sizes and styles throughout the design
- Avoid overly decorative or complex fonts that may be difficult to read
Character Size and Spacing
To ensure that the silkscreen text is easily readable, it’s important to adhere to minimum character sizes and spacing requirements. The following table provides general guidelines for silkscreen character sizes:
Height (mm) | Width (mm) | Thickness (mm) |
---|---|---|
1.0 | 0.8 | 0.15 |
1.5 | 1.0 | 0.20 |
2.0 | 1.5 | 0.25 |
In addition to character size, it’s important to maintain adequate spacing between characters and lines of text to prevent crowding and improve readability.
Symbol and Graphic Design
Silkscreen symbols and graphics should be clear, concise, and easily recognizable. Some tips for designing effective symbols and graphics include:
- Use simple, geometric shapes when possible
- Maintain consistent line weights and styles
- Avoid overly complex or detailed designs that may be difficult to print or interpret
Placement and Orientation
When placing silkscreen elements on the PCB, it’s important to consider the following factors:
- Avoid placing text or graphics over component pads or other critical features
- Maintain adequate clearance between silkscreen elements and board edges
- Orient text and symbols for optimal readability based on the board’s intended orientation during use
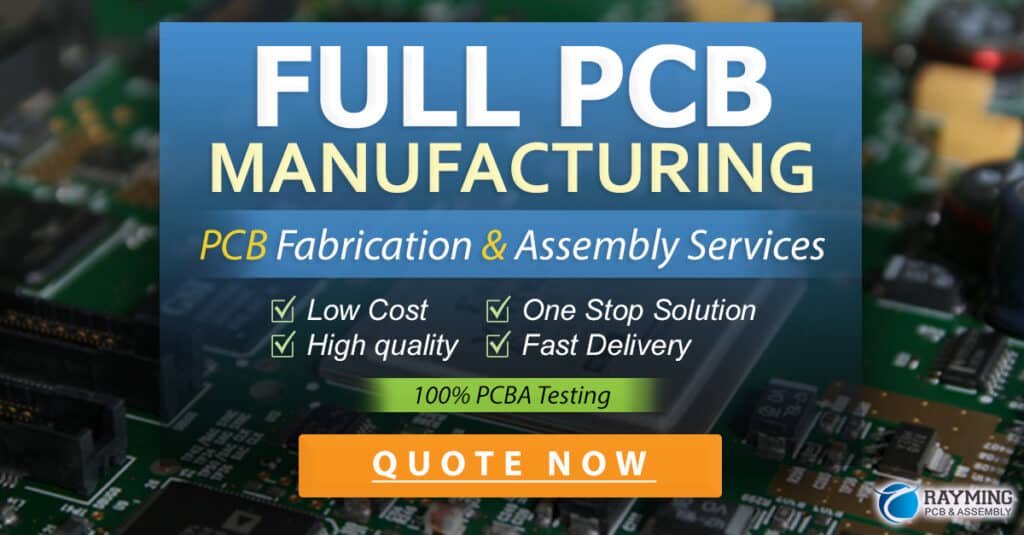
Advantages of Silkscreen on PCB
Incorporating a well-designed silkscreen layer offers several key advantages for PCB manufacturers, assemblers, and end-users:
-
Improved Assembly Efficiency: Clear and concise silkscreen information helps streamline the assembly process, reducing errors and increasing throughput.
-
Enhanced Troubleshooting and Maintenance: A well-labeled PCB makes it easier for technicians to identify components and trace connections during debugging and repair, saving time and effort.
-
Better User Experience: Clear labeling of connectors, switches, and indicators helps users interact with the device more effectively, improving overall user satisfaction.
-
Professional Appearance: High-quality silkscreen printing enhances the visual appeal of the PCB, giving the end product a more polished and professional look.
Frequently Asked Questions (FAQ)
-
What is the difference between silkscreen and legend on a PCB?
Silkscreen and legend are two terms used interchangeably to refer to the layer of text, symbols, and graphics printed on the surface of a PCB. -
Can silkscreen be printed in colors other than white?
Yes, while white is the most common color for silkscreen printing, other colors such as black, yellow, or red can be used for specific applications or to improve visibility. -
What is the minimum font size for silkscreen text on a PCB?
The minimum recommended font size for silkscreen text is 1.0mm in height, with a width of 0.8mm and a thickness of 0.15mm. However, larger sizes may be necessary for improved readability, depending on the application. -
Can silkscreen be applied to both sides of a PCB?
Yes, silkscreen can be printed on both the top and bottom surfaces of a PCB, depending on the design requirements and intended use of the board. -
Is silkscreen required for all PCBs?
While silkscreen is highly recommended for most PCBs, it is not always strictly necessary. Some very simple or low-cost designs may omit the silkscreen layer to reduce manufacturing costs. However, for the majority of applications, the benefits of including a well-designed silkscreen layer far outweigh the minimal added cost.
In conclusion, silkscreen on PCB plays a vital role in the electronic manufacturing process, providing clear and concise information that improves assembly efficiency, troubleshooting, user experience, and overall product quality. By understanding the purpose, process, and design considerations involved in silkscreen printing, PCB designers and manufacturers can create boards that are both functional and visually appealing, ultimately leading to better end products for consumers.
Leave a Reply