Introduction to PCB Schematics
A printed circuit board (PCB) schematic is a visual representation of the electrical connections and components in a circuit. It serves as a blueprint for designing and manufacturing a PCB, providing a clear and concise way to understand the circuit’s functionality and layout.
PCB schematics use standardized symbols to represent various electronic components, such as resistors, capacitors, transistors, and integrated circuits. These symbols are connected by lines, which represent the electrical connections between the components. The schematic also includes information about the component values, such as resistance, capacitance, and voltage ratings.
The Importance of PCB Schematics
PCB schematics play a crucial role in the design and development of electronic devices. They serve several important purposes:
-
Circuit design: Schematics allow engineers to design and analyze the circuit before physical implementation, ensuring that the circuit functions as intended and identifying potential issues early in the design process.
-
Communication: Schematics provide a common language for engineers, technicians, and manufacturers to communicate about the circuit design, making collaboration and troubleshooting more efficient.
-
Documentation: Schematics serve as a permanent record of the circuit design, which can be referred to for future modifications, repairs, or upgrades.
-
Manufacturing: PCB manufacturers use schematics to create the physical PCB, ensuring that the components are placed correctly and the connections are made according to the design.
Components of a PCB Schematic
A typical PCB schematic consists of several key components:
1. Symbols
Schematic symbols represent the various electronic components used in the circuit. These symbols are standardized, making it easy for engineers and technicians to identify the components and their functions. Some common symbols include:
Symbol | Component |
---|---|
Resistor | |
Capacitor | |
Transistor | |
Integrated circuit |
2. Connections
Connections in a schematic are represented by lines, which show the electrical paths between components. These lines can be straight or bent, depending on the layout of the schematic. Connection points, or nodes, are represented by dots or small circles where lines intersect.
3. Labels and Values
Components in a schematic are labeled with their reference designators, such as R1 for a resistor or C2 for a capacitor. These labels help identify specific components within the circuit. Additionally, component values, such as resistance in ohms or capacitance in farads, are indicated next to the corresponding symbol.
4. Power and Ground Symbols
Power and ground connections are represented by specific symbols in a schematic. The most common symbols are:
Symbol | Connection |
---|---|
Power supply (e.g., VCC, +5V) | |
Ground (GND) |
These symbols help identify the power and ground connections within the circuit, making it easier to understand the overall power distribution.
Creating a PCB Schematic
Creating a PCB schematic involves several steps:
-
Define the circuit requirements: Determine the functionality, inputs, outputs, and power requirements of the circuit.
-
Select the components: Choose the appropriate components that meet the circuit requirements, considering factors such as voltage and current ratings, tolerance, and package size.
-
Draw the schematic: Use a schematic capture tool, such as KiCad, Eagle, or Altium Designer, to create the schematic. Place the component symbols and connect them with lines according to the circuit design.
-
Assign component values: Add the appropriate values for each component, such as resistance, capacitance, and voltage ratings.
-
Add labels and annotations: Label the components with their reference designators and add any necessary annotations, such as component names, values, or special instructions.
-
Verify the schematic: Check the schematic for errors, such as missing connections, incorrect component values, or inconsistencies with the circuit requirements. Use the schematic capture tool’s built-in error checking features or perform a manual review.
-
Create a bill of materials (BOM): Generate a list of all the components used in the schematic, including their reference designators, values, and quantities. This BOM will be used for sourcing components and during the pcb assembly process.
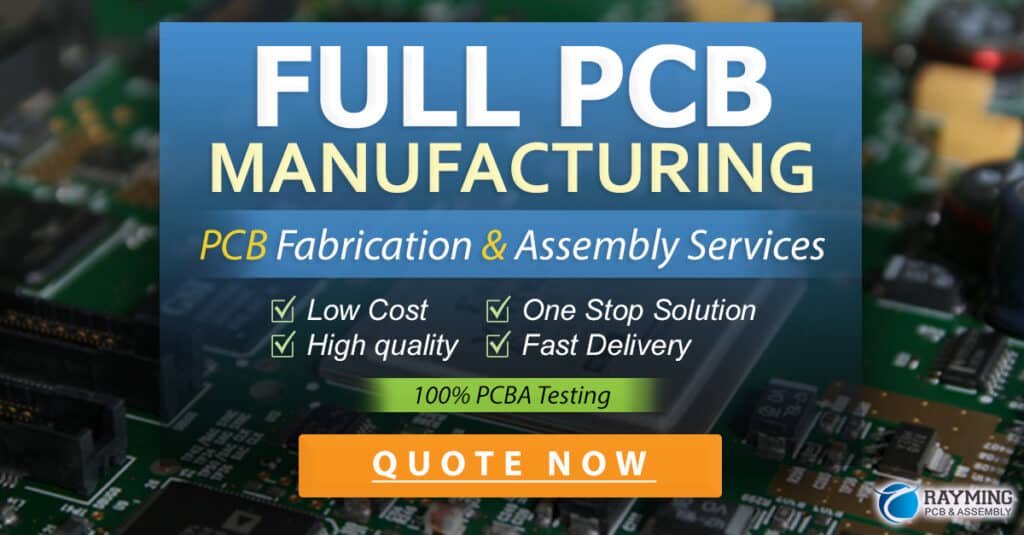
From Schematic to PCB Layout
Once the schematic is complete, the next step is to create the PCB layout. The PCB layout is a physical representation of the schematic, showing the actual size, shape, and placement of components on the PCB.
The PCB layout process involves several key steps:
-
Component placement: Arrange the components on the PCB based on the schematic, considering factors such as signal integrity, heat dissipation, and mechanical constraints.
-
Routing: Create the electrical connections between the components using copper traces. The routing process must consider factors such as signal integrity, electromagnetic compatibility (EMC), and manufacturing constraints.
-
Adding copper pours and planes: Add copper pours and planes to the PCB layout to provide a low-impedance path for power and ground connections, as well as to improve EMC and heat dissipation.
-
Design rule checking (DRC): Verify that the PCB layout meets the manufacturing and design constraints, such as minimum trace width, minimum clearance between components, and drilling tolerances.
-
Generate manufacturing files: Create the necessary files for PCB manufacturing, such as Gerber files, drill files, and pick-and-place files.
Importance of Accurate PCB Schematics
Accurate PCB schematics are essential for several reasons:
-
Functionality: An accurate schematic ensures that the circuit functions as intended, minimizing the risk of errors and reducing the need for costly rework.
-
Manufacturing: A precise schematic is necessary for creating an accurate PCB layout, which in turn is essential for successful manufacturing. Errors in the schematic can lead to manufacturing issues, such as incorrect component placement or missing connections.
-
Troubleshooting: An accurate schematic serves as a valuable reference for troubleshooting and repairs. It helps technicians identify potential issues and locate specific components within the circuit.
-
Future modifications: A well-documented schematic makes it easier to modify or upgrade the circuit in the future, as it provides a clear understanding of the original design intent.
Best Practices for Creating PCB Schematics
To create effective and accurate PCB schematics, consider the following best practices:
-
Use consistent and clear naming conventions: Adopt a consistent naming convention for components, nets, and labels to make the schematic easier to read and understand.
-
Organize the schematic logically: Arrange the components and subsystems in a logical manner, such as by function or signal flow, to make the schematic more intuitive and easier to follow.
-
Use hierarchical design: For complex circuits, use a hierarchical design approach, breaking the schematic into smaller, more manageable subsystems. This makes the schematic easier to navigate and understand.
-
Provide clear annotations: Include clear annotations and comments in the schematic to provide additional information, such as component specifications, design notes, or special instructions.
-
Verify the schematic: Always verify the schematic for errors and inconsistencies before proceeding to the PCB layout stage. Use the schematic capture tool’s built-in error checking features and perform a manual review to catch any issues.
Frequently Asked Questions (FAQ)
-
Q: What is the difference between a schematic and a PCB layout?
A: A schematic is a visual representation of the electrical connections and components in a circuit, while a PCB layout is a physical representation of the schematic, showing the actual size, shape, and placement of components on the PCB. -
Q: Can I create a PCB without a schematic?
A: While it is possible to create a simple PCB without a schematic, it is not recommended for complex circuits. A schematic is essential for designing, analyzing, and documenting the circuit, and it serves as a blueprint for creating the PCB layout. -
Q: What software is used for creating PCB schematics?
A: There are several software tools available for creating PCB schematics, such as KiCad, Eagle, Altium Designer, and OrCAD. These tools provide a user-friendly interface for placing components, creating connections, and verifying the schematic. -
Q: How do I choose the right components for my PCB schematic?
A: When selecting components for your PCB schematic, consider factors such as voltage and current ratings, tolerance, package size, and availability. Consult component datasheets and application notes to ensure that the chosen components meet the circuit requirements. -
Q: What should I do if I find an error in my PCB schematic?
A: If you find an error in your PCB schematic, correct it as soon as possible. Verify the schematic again to ensure that the error has been resolved and that no new issues have been introduced. If the error is discovered after the PCB has been manufactured, assess the impact of the error and determine if rework or redesign is necessary.
Conclusion
PCB schematics are an essential part of the electronic design process, providing a visual representation of the electrical connections and components in a circuit. They serve as a blueprint for designing, analyzing, and manufacturing PCBs, and are crucial for effective communication and collaboration among engineers, technicians, and manufacturers.
By understanding the components of a PCB schematic, following best practices for creating schematics, and using appropriate software tools, you can create accurate and effective schematics that streamline the PCB design and manufacturing process. Always remember to verify your schematics for errors and inconsistencies before proceeding to the PCB layout stage to ensure a successful outcome.
Leave a Reply