The Importance of Round-Edge Plating
Round-edge plating offers several benefits that make it an essential process in metal fabrication:
- Improved safety: Rounded edges minimize the risk of injuries caused by sharp or jagged edges on metal components.
- Enhanced durability: The plating process protects the edges from wear and tear, increasing the overall lifespan of the component.
- Corrosion resistance: Round-edge plating helps prevent corrosion by sealing the exposed edges and creating a barrier against environmental factors.
- Aesthetic appeal: Smooth, rounded edges provide a more polished and visually appealing appearance to the metal component.
The Round-Edge Plating Process
The round-edge plating process typically involves the following steps:
- Surface preparation: The metal component is cleaned and degreased to remove any contaminants that may interfere with the plating process.
- Edge rounding: The edges of the component are mechanically rounded using specialized tools, such as abrasive wheels, belts, or brushes.
- Masking: Areas of the component that do not require plating are masked off to prevent the plating solution from adhering to them.
- Plating: The component is immersed in an electrolytic bath containing the desired plating material, such as nickel, chrome, or zinc. An electric current is applied, causing the plating material to bond to the surface of the component.
- Rinsing and drying: After plating, the component is rinsed with water to remove any excess plating solution and then dried.
- Inspection: The plated component is inspected for quality, ensuring that the plating is even, adheres well, and meets the specified thickness requirements.
Factors Affecting Round-Edge Plating Quality
Several factors can influence the quality of round-edge plating:
- Edge geometry: The shape and complexity of the edges can affect the uniformity of the plating. Sharp corners or intricate designs may require specialized techniques to ensure even coverage.
- Surface preparation: Proper cleaning and degreasing are critical to ensure good adhesion of the plating material to the metal surface.
- Plating solution composition: The concentration and purity of the plating solution, as well as the pH and temperature, must be carefully controlled to achieve the desired plating quality.
- Current density: The amount of electric current applied during the plating process affects the deposition rate and the quality of the plating.
- Plating time: The duration of the plating process determines the thickness of the plating layer and must be adjusted based on the specific requirements of the application.
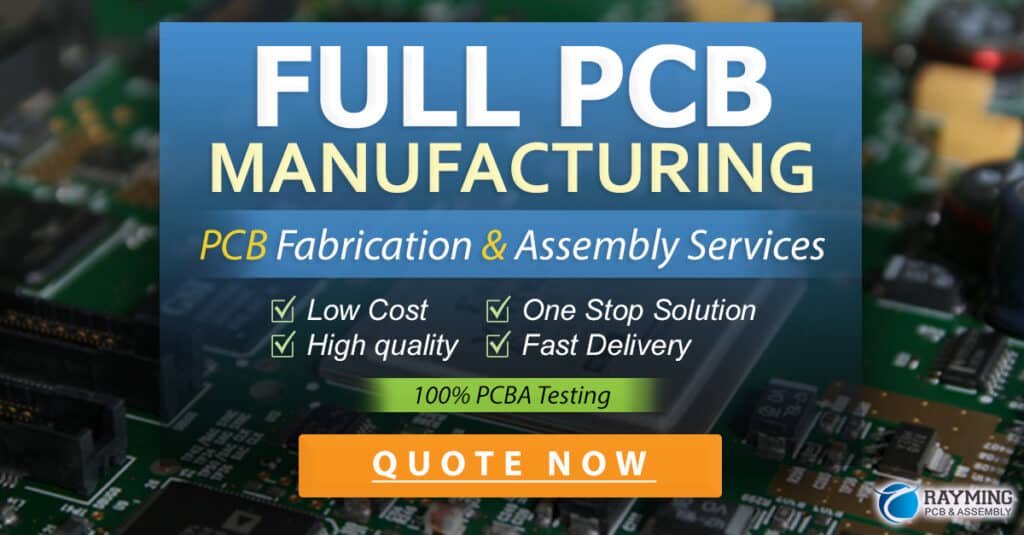
Common Materials Used in Round-Edge Plating
Various metals can be used for round-edge plating, depending on the desired properties and aesthetic requirements:
Material | Properties | Applications |
---|---|---|
Nickel | Hard, corrosion-resistant, wear-resistant | Automotive components, machinery parts, decorative finishes |
Chrome | Highly reflective, hard, wear-resistant | Automotive trim, hydraulic cylinders, decorative finishes |
Zinc | Corrosion-resistant, sacrificial protection | Automotive parts, fasteners, outdoor equipment |
Copper | Conductive, ductile, corrosion-resistant | Electrical components, heat exchangers, decorative finishes |
Gold | Conductive, corrosion-resistant, aesthetically appealing | Electronic components, jewelry, high-end decorative finishes |
Applications of Round-Edge Plating
Round-edge plating finds applications in various industries:
Automotive Industry
In the automotive industry, round-edge plating is used to:
– Enhance the durability and corrosion resistance of critical components, such as brake calipers, suspension parts, and engine components.
– Improve the aesthetic appeal of decorative elements, such as trim pieces, grilles, and wheels.
– Ensure the safety of vehicle occupants by eliminating sharp edges on interior components, such as seat frames and dashboard parts.
Aerospace Industry
Round-edge plating is employed in the aerospace industry to:
– Protect critical components, such as landing gear, actuators, and fasteners, from corrosion and wear.
– Enhance the fatigue resistance of high-stress components, such as engine mounts and structural parts.
– Improve the aerodynamic performance of aircraft by reducing drag caused by sharp edges.
Electronics Industry
In the electronics industry, round-edge plating is used to:
– Improve the electrical conductivity and solderability of components, such as connectors and circuit boards.
– Protect sensitive electronic components from corrosion and electromagnetic interference.
– Enhance the aesthetic appeal of consumer electronics, such as smartphones, tablets, and laptops.
Manufacturing Industry
Round-edge plating is widely used in the manufacturing industry to:
– Improve the durability and wear resistance of machinery components, such as gears, shafts, and bearings.
– Protect tools and dies from corrosion and wear, extending their lifespan and reducing maintenance costs.
– Enhance the safety of workers by eliminating sharp edges on equipment and workpieces.
Advantages of Round-Edge Plating
Round-edge plating offers several advantages over other metal finishing techniques:
- Versatility: Round-edge plating can be applied to a wide range of metal components, regardless of their size, shape, or complexity.
- Cost-effectiveness: Compared to other edge-finishing methods, such as machining or grinding, round-edge plating is a more cost-effective solution for large-scale production.
- Compatibility: Round-edge plating is compatible with various base metals, including steel, aluminum, and copper alloys, making it suitable for a broad range of applications.
- Customization: The plating process can be customized to achieve specific properties, such as increased hardness, improved corrosion resistance, or enhanced electrical conductivity.
Challenges in Round-Edge Plating
Despite its numerous benefits, round-edge plating also presents some challenges:
- Edge uniformity: Achieving a consistent and uniform plating thickness along the entire edge can be difficult, especially for complex geometries or sharp corners.
- Adhesion issues: Poor surface preparation or incompatible base metals can lead to adhesion problems, resulting in flaking or peeling of the plating layer.
- Environmental concerns: Some plating processes involve the use of hazardous chemicals, such as cyanide or hexavalent chromium, which pose environmental and health risks and require strict regulation and control.
- Process control: Maintaining consistent plating quality requires strict control over various process parameters, such as solution composition, temperature, and current density, which can be challenging in large-scale production.
Future Trends in Round-Edge Plating
As industries continue to evolve, round-edge plating technologies are also advancing to meet new challenges and demands:
- Environmentally friendly processes: There is a growing trend towards the development of eco-friendly plating solutions and processes that minimize the use of hazardous chemicals and reduce environmental impact.
- Nanotechnology: The incorporation of nanomaterials into plating solutions can enhance the properties of the plated layer, such as hardness, wear resistance, and corrosion resistance.
- Additive manufacturing: The integration of round-edge plating with additive manufacturing techniques, such as 3D printing, can enable the creation of complex, high-performance components with optimized edge geometries.
- Automation: The increasing automation of the plating process, including the use of robotics and machine vision systems, can improve efficiency, consistency, and quality control in large-scale production.
Frequently Asked Questions (FAQ)
-
What is the difference between round-edge plating and other edge-finishing methods?
Round-edge plating involves the application of a protective or decorative coating to the edges of a metal component, while other methods, such as machining or grinding, physically remove material to create a rounded edge profile. -
Can round-edge plating be applied to non-metallic components?
No, round-edge plating is specifically designed for metal components. Non-metallic materials, such as plastics or composites, require different edge-finishing techniques. -
How long does the round-edge plating process take?
The duration of the round-edge plating process depends on various factors, such as the size and complexity of the component, the desired plating thickness, and the specific plating material. Typically, the process can take anywhere from a few minutes to several hours. -
Is round-edge plating suitable for high-temperature applications?
The suitability of round-edge plating for high-temperature applications depends on the specific plating material and the operating conditions. Some plating materials, such as nickel or chromium, can withstand higher temperatures than others. However, in extreme cases, alternative edge-finishing methods may be more appropriate. -
How can I ensure the quality and consistency of round-edge plating in my production process?
To ensure the quality and consistency of round-edge plating, it is essential to: - Establish and maintain strict process controls, including solution composition, temperature, and current density.
- Implement regular quality inspections and testing to verify plating thickness, adhesion, and uniformity.
- Train operators and technicians to follow best practices and maintain equipment properly.
- Work with experienced plating service providers who have a proven track record of delivering high-quality results.
In conclusion, round-edge plating is a versatile and valuable metal finishing process that offers numerous benefits, including improved safety, enhanced durability, corrosion resistance, and aesthetic appeal. By understanding the process, its applications, and the factors affecting plating quality, manufacturers can leverage round-edge plating to create high-performance, visually appealing metal components for a wide range of industries. As technology advances, the future of round-edge plating looks promising, with the development of eco-friendly processes, the integration of nanotechnology, and the increasing automation of the plating process.
Leave a Reply