Understanding the Basics of Rigid Flex PCB Stackup
Rigid PCB Layers
A rigid flex PCB stackup typically consists of several rigid PCB layers, which are made from a solid substrate material, such as FR-4. These layers provide structural support and house the majority of the electronic components and circuitry. The number of rigid layers in a stackup can vary depending on the complexity and requirements of the design.
Flexible PCB Layers
In addition to the rigid layers, a rigid flex PCB stackup incorporates one or more flexible PCB layers. These layers are made from a thin, flexible substrate material, such as polyimide. The flexible layers allow the PCB to bend and fold, enabling the creation of unique form factors and the ability to fit the PCB into tight spaces.
Adhesive Layers
To bond the rigid and flexible layers together, adhesive layers are used in the stackup. These adhesive layers, often made from acrylic or epoxy-based materials, ensure a strong and reliable connection between the different layers of the PCB.
Copper Foil
Copper foil is used to create the conductive traces and pads on both the rigid and flexible layers of the PCB. The thickness of the copper foil can vary depending on the current carrying requirements and the desired signal integrity of the design.
Coverlay
A coverlay is a protective layer that is applied to the flexible portions of the PCB. It serves to insulate and protect the exposed copper traces and pads from damage and environmental factors.
Benefits of Rigid Flex PCB Stackup
Increased Reliability
By combining rigid and flexible layers in a single PCB, rigid flex PCB stackups offer increased reliability compared to traditional PCBs. The flexible layers allow for greater mechanical stress absorption, reducing the risk of cracking or breaking under repeated bending or vibration.
Space Savings
Rigid flex PCB stackups enable the creation of more compact and space-efficient electronic devices. By allowing the PCB to fold and conform to the available space, designers can reduce the overall size of the device without compromising functionality.
Reduced Assembly Costs
With a rigid flex PCB stackup, multiple separate PCBs can be consolidated into a single board. This reduction in the number of interconnects and connectors leads to lower assembly costs and a more streamlined manufacturing process.
Improved Signal Integrity
The close proximity of the layers in a rigid flex PCB stackup helps to minimize signal loss and interference. This improved signal integrity is particularly beneficial in high-speed and high-frequency applications.
Applications of Rigid Flex PCB Stackup
Wearable Electronics
Rigid flex PCB stackups are ideal for wearable electronics, such as smartwatches, fitness trackers, and medical monitoring devices. The flexibility of the PCB allows it to conform to the contours of the human body, providing a comfortable and ergonomic fit.
Aerospace and Defense
In the aerospace and defense industries, rigid flex PCB stackups are used in a variety of applications, including avionics, missiles, and satellites. The ability to withstand extreme temperatures, vibrations, and shocks makes rigid flex PCBs well-suited for these demanding environments.
Automotive Electronics
Rigid flex PCB stackups are increasingly being used in automotive electronics, such as infotainment systems, driver assistance features, and vehicle networking. The compact size and reliability of rigid flex PCBs make them an attractive option for the space-constrained and harsh environments found in vehicles.
Medical Devices
Medical devices, such as implantable devices, surgical instruments, and diagnostic equipment, often rely on rigid flex PCB stackups. The flexibility and biocompatibility of the materials used in these stackups ensure safe and reliable operation within the human body.
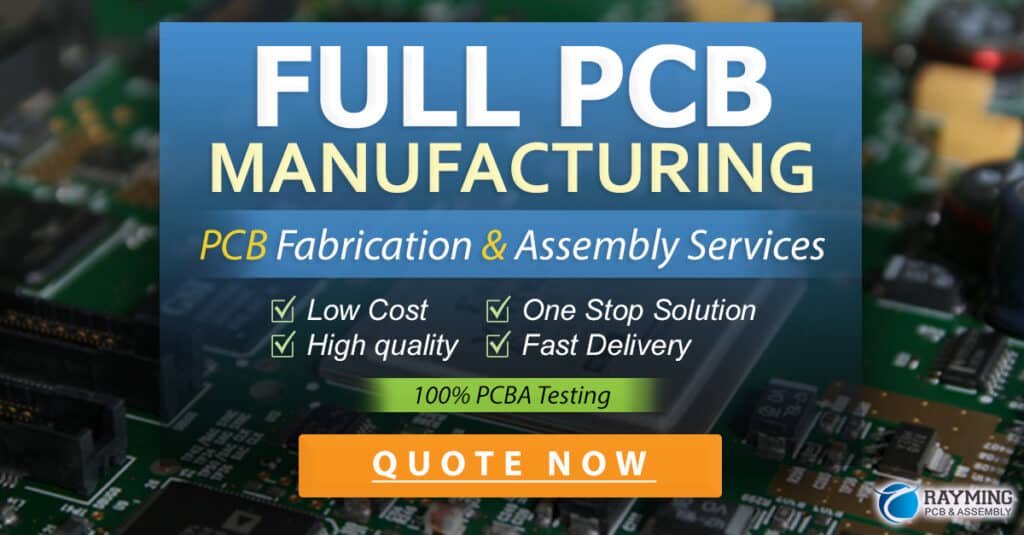
Designing a Rigid Flex PCB Stackup
Layer Arrangement
When designing a rigid flex PCB stackup, careful consideration must be given to the arrangement of the layers. The placement of the rigid and flexible layers, as well as the adhesive and coverlay layers, will impact the overall performance and reliability of the PCB.
Material Selection
Choosing the appropriate materials for each layer of the stackup is crucial. Factors such as the dielectric constant, thermal expansion coefficient, and flexibility of the materials must be taken into account to ensure compatibility and optimal performance.
Bend Radius
The bend radius of the flexible layers in a rigid flex PCB stackup must be carefully calculated to prevent damage to the copper traces and ensure the long-term reliability of the PCB. The minimum bend radius will depend on the thickness and material properties of the flexible layers.
Via Placement
The placement of vias in a rigid flex PCB stackup requires special attention. Vias that transition between rigid and flexible layers must be designed to withstand the mechanical stresses associated with bending and flexing.
Impedance Control
Maintaining proper impedance control throughout the rigid flex PCB stackup is essential for ensuring signal integrity and minimizing reflections. This can be achieved through careful selection of materials, trace geometries, and layer thicknesses.
Manufacturing Considerations
Layer Bonding
The process of bonding the rigid and flexible layers together is a critical step in the manufacturing of a rigid flex PCB stackup. Proper bonding ensures the structural integrity and reliability of the final product.
Coverlay Application
Applying the coverlay to the flexible portions of the PCB requires precise alignment and lamination to ensure a smooth and uniform surface finish.
Drilling and Routing
Drilling and routing of a rigid flex PCB stackup must be performed with care to avoid damaging the flexible layers. Specialized equipment and techniques may be required to achieve the desired results.
Inspection and Testing
Thorough inspection and testing of a rigid flex PCB stackup is necessary to identify any potential defects or performance issues. This may include visual inspection, electrical testing, and mechanical stress testing.
Frequently Asked Questions (FAQ)
1. What is the typical layer count for a rigid flex PCB stackup?
The layer count for a rigid flex PCB stackup can vary widely depending on the specific application and design requirements. A typical stackup may range from 4 to 20 layers, with a combination of rigid and flexible layers.
2. Can rigid flex PCBs be used in high-temperature environments?
Yes, rigid flex PCBs can be designed to withstand high-temperature environments. The selection of appropriate materials, such as high-temperature substrates and adhesives, ensures reliable operation in elevated temperature conditions.
3. What is the minimum bend radius for a flexible PCB layer?
The minimum bend radius for a flexible PCB layer depends on the thickness and material properties of the layer. As a general rule, the minimum bend radius is typically 6 to 10 times the thickness of the flexible layer.
4. How does the cost of a rigid flex PCB compare to a traditional rigid PCB?
Rigid flex PCBs are generally more expensive than traditional rigid PCBs due to the additional materials, processing steps, and specialized equipment required for their manufacture. However, the cost can be offset by the benefits of reduced assembly time, improved reliability, and space savings.
5. What are the challenges associated with designing a rigid flex PCB stackup?
Designing a rigid flex PCB stackup presents several challenges, including ensuring proper layer bonding, maintaining signal integrity, and controlling impedance. Additionally, the mechanical stresses associated with bending and flexing must be carefully considered to prevent damage to the PCB.
Layer Type | Material | Thickness (mm) |
---|---|---|
Coverlay | Polyimide | 0.05 |
Flexible | Polyimide | 0.075 |
Adhesive | Acrylic | 0.05 |
Rigid | FR-4 | 0.2 |
Copper Foil | Copper | 0.035 |
Table 1: Example of a simple rigid flex PCB stackup
In conclusion, rigid flex PCB stackups offer a unique combination of flexibility and reliability, enabling the creation of compact and versatile electronic devices. By understanding the components, benefits, and design considerations associated with rigid flex PCBs, engineers and designers can unlock new possibilities in a wide range of applications, from wearable electronics to aerospace and defense systems.
As the demand for smaller, more reliable, and more complex electronic devices continues to grow, the importance of rigid flex PCB stackups will only continue to increase. By staying at the forefront of this technology and continuously refining design and manufacturing processes, the electronics industry can push the boundaries of what is possible and create innovative solutions to meet the challenges of the future.
Leave a Reply