Understanding PCB Prototyping
What is a PCB?
A Printed Circuit Board (PCB) is a fundamental component of modern electronic devices. It is a flat, insulating board made of materials such as fiberglass, composite epoxy, or other laminate material, with conductive pathways etched or printed onto its surface. These pathways, known as traces, connect various electronic components, such as resistors, capacitors, and integrated circuits (ICs), to create a functional electronic circuit.
The Importance of PCB Prototyping
PCB prototyping is an essential step in the development of electronic devices for several reasons:
-
Design Validation: Prototyping allows engineers to test their designs in real-world conditions, ensuring that the circuit functions as intended and identifying any potential issues or areas for improvement.
-
Cost Savings: By identifying and addressing design flaws early in the development process, prototyping can help avoid costly mistakes and rework during full-scale production.
-
Iterative Improvement: Prototyping enables designers to refine their designs through multiple iterations, incorporating feedback and making necessary adjustments to optimize performance, reliability, and manufacturability.
-
Proof of Concept: A working prototype serves as a tangible demonstration of the device’s functionality, which can be valuable for securing funding, attracting investors, or obtaining customer buy-in.
Prototype PCB Assembly Techniques
There are several techniques used in prototype PCB assembly, each with its own advantages and limitations. The choice of technique depends on factors such as the complexity of the design, the required turnaround time, and the available budget.
Manual Assembly
Manual assembly involves hand-placing and soldering components onto the PCB. This technique is suitable for simple designs with relatively few components and is often used for very low-volume prototypes or quick proof-of-concept builds. However, manual assembly is time-consuming, labor-intensive, and prone to human error, making it less suitable for complex designs or higher volumes.
Solder Paste Stenciling
Solder paste stenciling is a technique that involves applying a thin layer of solder paste onto the PCB using a stencil. The stencil, typically made of stainless steel or polyester, has openings that correspond to the component pads on the PCB. Solder paste is applied through these openings, depositing a precise amount of paste onto each pad. This technique ensures consistent solder paste application and is suitable for surface-mount components.
Pick-and-Place Machine Assembly
Pick-and-place (PnP) machines are automated systems that place surface-mount components onto the PCB with high speed and precision. These machines use computer-aided design (CAD) data to determine the placement locations and orientations of the components. PnP machines are ideal for assembling complex designs with a large number of components and can significantly reduce assembly time compared to manual methods.
Reflow Soldering
After the components are placed onto the PCB, the board undergoes reflow soldering. In this process, the PCB is heated in a reflow oven, causing the solder paste to melt and form a permanent connection between the components and the board. Reflow soldering ensures consistent and reliable solder joints and is suitable for surface-mount components.
Wave Soldering
Wave soldering is a technique used for through-hole components. In this process, the PCB is passed over a molten solder wave, which flows through the holes in the board and forms a connection between the component leads and the PCB pads. Wave soldering is an efficient method for assembling through-hole components but requires careful design considerations to ensure proper solder joint formation.
Prototype PCB Assembly Technologies
In addition to the various assembly techniques, several technologies are used in prototype PCB assembly to enhance the functionality, reliability, and performance of the final product.
Surface Mount Technology (SMT)
Surface Mount Technology (SMT) refers to the method of mounting electronic components directly onto the surface of a PCB. SMT components are smaller and more compact than through-hole components, allowing for higher component density and smaller board sizes. SMT also enables faster assembly speeds and better performance at higher frequencies.
Through-Hole Technology (THT)
Through-Hole Technology (THT) involves mounting components by inserting their leads through holes drilled in the PCB and soldering them to pads on the opposite side of the board. THT components are generally larger and more robust than SMT components and are often used for high-power or mechanical stress applications. However, THT assembly is slower and requires more manual intervention compared to SMT.
Mixed Technology
Mixed technology PCB assembly combines both SMT and THT components on a single board. This approach allows designers to leverage the advantages of both technologies, using SMT for high-density and high-performance areas of the board while employing THT for components that require greater mechanical stability or power handling capabilities.
Flexible PCBs
Flexible PCBs, also known as flex circuits, are designed to bend and flex without damaging the conductive pathways or components. These PCBs are made using flexible substrates, such as polyimide or polyester, and are often used in applications that require compact packaging, such as wearable devices, medical equipment, or aerospace systems.
Rigid-Flex PCBs
Rigid-flex PCBs combine the benefits of both rigid and flexible PCBs. These boards consist of rigid sections connected by flexible sections, allowing for three-dimensional packaging and improved reliability in applications that require frequent flexing or folding of the circuit.
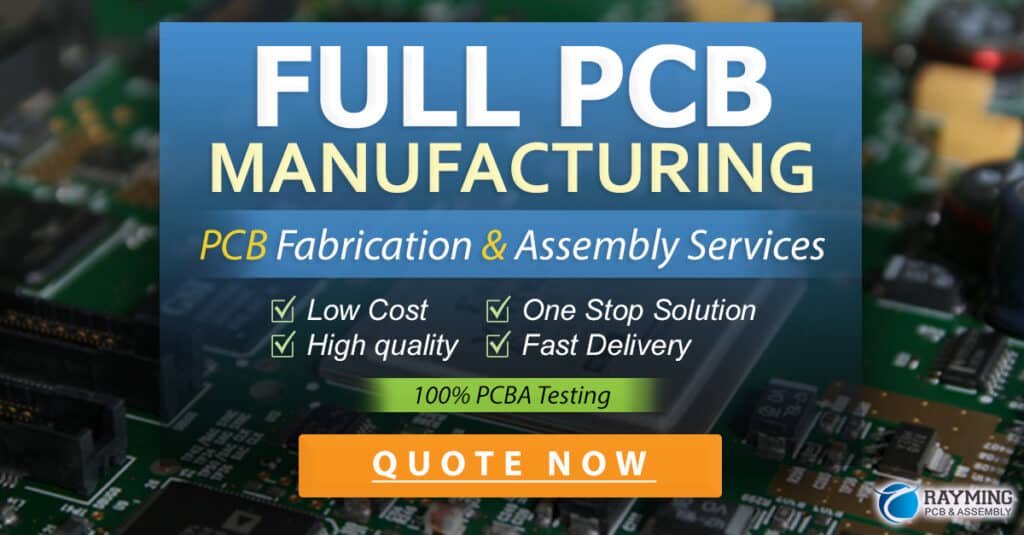
Prototype PCB Assembly Process
The prototype PCB assembly process typically involves the following steps:
-
Design: The PCB design is created using electronic design automation (EDA) software, which generates the necessary CAD files, including schematic diagrams, component layouts, and routing information.
-
PCB Fabrication: The PCB is manufactured according to the design specifications, including the number of layers, material type, and surface finish.
-
Solder Paste Stenciling: If using SMT components, a solder paste stencil is applied to the PCB, depositing precise amounts of solder paste onto the component pads.
-
Component Placement: Components are placed onto the PCB, either manually or using a pick-and-place machine, depending on the assembly technique chosen.
-
Soldering: The PCB undergoes reflow soldering for SMT components or wave soldering for THT components, creating permanent electrical connections between the components and the board.
-
Inspection and Testing: The assembled PCB is visually inspected for any defects or irregularities, and electrical tests are performed to ensure proper functionality and performance.
-
Rework and Debugging: If any issues are identified during inspection or testing, the PCB may undergo rework or debugging to address the problems and improve its functionality.
Advantages of Prototype PCB Assembly
Prototype PCB assembly offers several key advantages in the development of electronic devices:
-
Reduced Time-to-Market: By enabling rapid design iteration and validation, prototype PCB assembly can significantly reduce the time required to bring a new product to market.
-
Improved Design Quality: Prototyping allows for the identification and correction of design flaws early in the development process, resulting in a higher-quality final product.
-
Cost Savings: Identifying and addressing issues during the prototyping phase can help avoid costly mistakes and rework during full-scale production.
-
Enhanced Collaboration: A physical prototype serves as a tangible representation of the design, facilitating better communication and collaboration among team members, stakeholders, and potential customers.
Challenges in Prototype PCB Assembly
Despite its many benefits, prototype PCB assembly also presents some challenges:
-
Component Availability: Sourcing components for prototype builds can be challenging, as some components may have long lead times or minimum order quantities that exceed the needs of a prototype run.
-
Design Complexity: As electronic devices become increasingly complex, prototype PCB assembly must adapt to accommodate higher component densities, smaller form factors, and more advanced technologies.
-
Cost Considerations: Prototype PCB assembly can be more expensive on a per-unit basis compared to full-scale production, due to the lower volumes and increased manual labor involved.
-
Skilled Labor: Prototype assembly often requires skilled technicians with expertise in various assembly techniques and technologies, which can be a challenge for some organizations to acquire and retain.
Future Trends in Prototype PCB Assembly
As the electronics industry continues to evolve, prototype PCB assembly is expected to adapt to new trends and technologies:
-
Miniaturization: The demand for smaller, more compact electronic devices will drive the need for advanced pcb design and assembly techniques, such as 3D printing and embedded components.
-
Increased Automation: The adoption of automated assembly technologies, such as advanced pick-and-place machines and robotic systems, will continue to grow, improving the speed, accuracy, and consistency of prototype assembly.
-
Sustainable Practices: There will be a growing emphasis on environmentally-friendly materials and processes in PCB assembly, such as lead-free solders, recyclable substrates, and energy-efficient manufacturing techniques.
-
Industry 4.0 Integration: The integration of Industry 4.0 technologies, such as the Internet of Things (IoT), artificial intelligence (AI), and machine learning (ML), will enable more intelligent and adaptive prototype PCB assembly processes, improving efficiency and quality control.
Prototype PCB Assembly FAQs
-
Q: What is the difference between prototype PCB assembly and full-scale production assembly?
A: Prototype PCB assembly focuses on creating a small number of boards for design validation, testing, and refinement, while full-scale production assembly involves manufacturing a large volume of boards for commercial distribution. Prototype assembly often involves more manual processes and lower volumes compared to full-scale production. -
Q: How long does prototype PCB assembly typically take?
A: The time required for prototype PCB assembly can vary depending on the complexity of the design, the chosen assembly techniques, and the availability of components. Simple prototypes may be assembled in a matter of days, while more complex designs can take several weeks. -
Q: What factors should I consider when choosing a prototype PCB assembly service provider?
A: When selecting a prototype PCB assembly service provider, consider factors such as their experience with your specific industry or application, their range of available assembly techniques and technologies, their turnaround times, and their ability to scale from prototyping to full-scale production. -
Q: Can I use the same design files for prototype PCB assembly and full-scale production?
A: In most cases, the design files used for prototype PCB assembly can also be used for full-scale production. However, it is essential to consider any design changes or optimizations that may be necessary to improve manufacturability, reliability, or cost-effectiveness when transitioning to full-scale production. -
Q: How can I reduce the cost of prototype PCB assembly?
A: To reduce the cost of prototype PCB assembly, consider strategies such as: - Optimizing your design for manufacturability and assembly
- Minimizing the number of unique components and using standard components where possible
- Leveraging automated assembly techniques when appropriate
- Choosing a pcb fabrication and assembly partner with competitive pricing and services tailored to your needs
Conclusion
Prototype PCB assembly is a vital step in the development of electronic devices, enabling designers and engineers to validate their designs, identify issues, and refine their products before committing to full-scale production. By understanding the various techniques, technologies, and processes involved in prototype PCB assembly, organizations can optimize their development cycles, reduce costs, and bring high-quality products to market more efficiently.
As the electronics industry continues to evolve, prototype PCB assembly will adapt to new challenges and opportunities, embracing advanced technologies and sustainable practices to meet the ever-growing demand for innovative, reliable, and cost-effective electronic solutions.
Prototype PCB Assembly Techniques | Advantages | Limitations |
---|---|---|
Manual Assembly | Suitable for simple designs and low volumes | Time-consuming, labor-intensive, prone to human error |
Solder Paste Stenciling | Consistent solder paste application, suitable for SMT components | Requires stencil fabrication, limited to SMT components |
Pick-and-Place Machine Assembly | High speed and precision, ideal for complex designs and large component counts | Higher initial investment, requires CAD data and machine programming |
Reflow Soldering | Consistent and reliable solder joints, suitable for SMT components | Requires precise temperature control and profile optimization |
Wave Soldering | Efficient for THT components, suitable for high volumes | Requires careful design considerations, limited to THT components |
Leave a Reply