Introduction to PCB Potting
Potting a printed circuit board (PCB) is a process of encapsulating electronic components or an entire PCB assembly using a compound material. The potting compound, which can be made of epoxy, silicone, urethane, or other materials, provides protection from environmental factors, mechanical stress, and tampering.
Potting is commonly used in applications where the PCB will be exposed to harsh conditions, such as in automotive, aerospace, military, and industrial settings. It can also be used to improve the security of sensitive electronic devices by preventing unauthorized access to the internal components.
In this article, we will explore the various aspects of PCB potting, including the materials used, the potting process, the benefits and drawbacks, and some common applications.
What is a Potting Compound?
A potting compound is a material used to encapsulate electronic components or entire PCB assemblies. The purpose of the potting compound is to provide protection from environmental factors, such as moisture, dust, and temperature extremes, as well as to improve the mechanical strength and durability of the PCB.
There are several types of potting compounds available, each with its own set of properties and characteristics. Some of the most common potting compounds include:
Potting Compound | Description |
---|---|
Epoxy | A two-part compound that cures to form a hard, rigid material. Epoxy is known for its excellent adhesion, chemical resistance, and mechanical strength. |
Silicone | A flexible, rubber-like material that remains soft even after curing. Silicone is resistant to high temperatures and provides good electrical insulation. |
Urethane | A versatile compound that can range from soft and flexible to hard and rigid, depending on the formulation. Urethane offers good resistance to abrasion, impact, and chemicals. |
Polyester | A cost-effective option that provides good electrical insulation and resistance to moisture and chemicals. Polyester is often used in less demanding applications. |
The choice of potting compound depends on the specific requirements of the application, such as the expected environmental conditions, the desired mechanical properties, and the compatibility with the PCB materials and components.
The PCB Potting Process
The PCB potting process involves several steps to ensure a proper and effective encapsulation of the electronic components or the entire PCB assembly. Here is a general overview of the potting process:
1. Preparation
Before potting, the PCB assembly must be thoroughly cleaned to remove any contaminants, such as flux residue, dust, or oils. The cleanliness of the PCB is critical to ensure good adhesion between the potting compound and the PCB surface.
2. Masking
If certain areas of the PCB need to remain exposed, such as connectors or test points, they must be masked off using tape, plugs, or other suitable materials. This prevents the potting compound from covering these areas.
3. Mixing
The potting compound is typically supplied as a two-part system consisting of a resin and a hardener. These components must be mixed in the proper ratio as specified by the manufacturer. The mixing process should be done carefully to avoid introducing air bubbles, which can weaken the final potted assembly.
4. Potting
The mixed potting compound is then poured or dispensed into the housing or mold containing the PCB assembly. The potting compound should be filled to the desired level, ensuring that all components are completely encapsulated.
5. Curing
After potting, the assembly is allowed to cure, which is the process of the potting compound solidifying and reaching its final properties. The curing time and temperature depend on the specific potting compound used and can range from several hours to several days.
6. Final Inspection
Once the potting compound has fully cured, the potted assembly is removed from the housing or mold and inspected for any defects, such as voids, cracks, or incomplete filling. If the potted assembly passes inspection, it is ready for use.
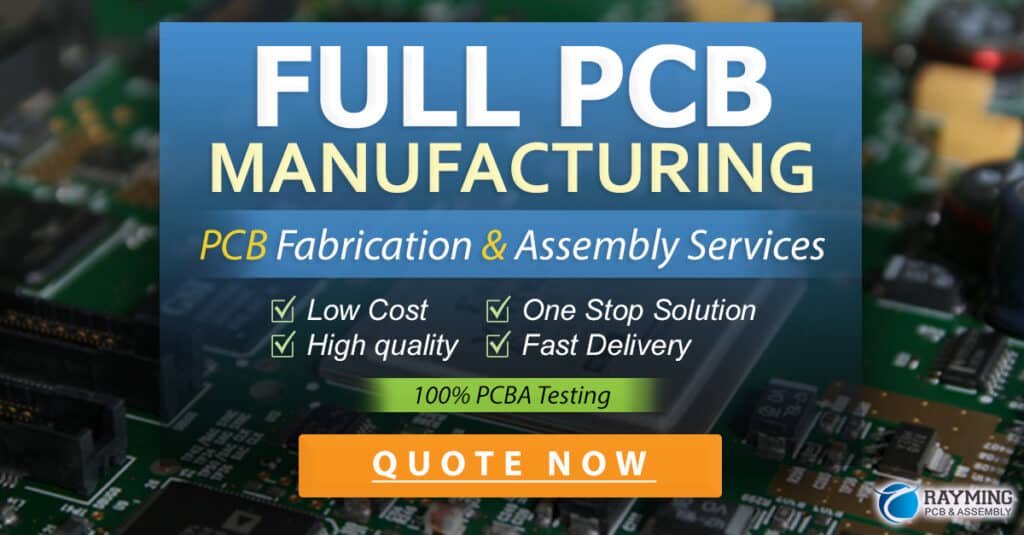
Benefits of PCB Potting
PCB potting offers several key benefits that make it a valuable technique in various electronic applications. Some of the main advantages of potting include:
1. Environmental Protection
Potting provides a barrier against environmental factors, such as moisture, dust, chemicals, and temperature extremes. By encapsulating the electronic components, potting prevents these harmful elements from reaching and damaging the sensitive parts of the PCB.
2. Mechanical Strength
Potting adds mechanical strength to the PCB assembly by distributing stresses and loads across the entire potted structure. This can help prevent damage from vibrations, shocks, and impacts, making the PCB more durable and reliable.
3. Electrical Insulation
Most potting compounds have good electrical insulation properties, which can help prevent short circuits, arcing, and other electrical issues. This is particularly important in high-voltage or high-current applications.
4. Tamper Resistance
Potting can make it difficult for unauthorized individuals to access or tamper with the internal components of a PCB. The potting compound creates a solid, opaque barrier that conceals the PCB layout and components, deterring reverse engineering attempts.
5. Reduced EMI/RFI
Some potting compounds have electromagnetic interference (EMI) and radio frequency interference (RFI) shielding properties. By encapsulating the PCB, these compounds can help reduce the emission or susceptibility of the electronic device to EMI/RFI.
Drawbacks of PCB Potting
While PCB potting offers many benefits, there are also some potential drawbacks to consider:
1. Increased Weight and Size
Potting adds material to the PCB assembly, which can increase its overall weight and size. This may be a concern in applications where space and weight are critical factors, such as in aerospace or portable devices.
2. Thermal Management Challenges
Potting can make it more difficult to dissipate heat generated by the electronic components. The potting compound acts as a thermal insulator, which can lead to higher operating temperatures and reduced performance or reliability if not properly addressed.
3. Rework Difficulties
Once a PCB is potted, it becomes very challenging to rework or repair. If a component fails or needs to be replaced, the potting compound must be removed, which can be a time-consuming and delicate process. In some cases, the entire PCB assembly may need to be replaced.
4. Material Compatibility
Not all potting compounds are compatible with all PCB materials and components. Some potting compounds may react with certain plastics, metals, or adhesives, causing degradation or failure over time. Careful selection and testing of the potting compound are necessary to ensure compatibility.
Common Applications of PCB Potting
PCB potting is used in a wide range of electronic applications, particularly those that require protection from harsh environments or enhanced security. Some common applications include:
1. Automotive Electronics
Potting is widely used in automotive electronics, such as engine control units, sensors, and power modules. These devices are exposed to extreme temperatures, vibrations, and moisture, making potting essential for reliable operation.
2. Aerospace and Military
In aerospace and military applications, PCBs are subjected to severe environmental conditions, including high altitudes, extreme temperatures, and exposure to chemicals and radiation. Potting helps ensure the reliability and durability of these critical electronic systems.
3. Industrial Controls
Industrial control systems, such as programmable logic controllers (PLCs) and motor drives, often operate in harsh factory environments. Potting protects these devices from dust, moisture, and other contaminants, ensuring long-term reliability.
4. Medical Devices
Medical devices, such as implantable electronics and diagnostic equipment, require a high level of protection from moisture and other environmental factors. Potting helps maintain the sterility and reliability of these devices.
5. Security Systems
In security systems, such as access control devices and encryption modules, potting is used to prevent tampering and reverse engineering. The opaque potting compound makes it difficult for unauthorized individuals to access or analyze the internal components.
FAQ
1. What is the difference between potting and encapsulation?
Potting and encapsulation are often used interchangeably, but there is a subtle difference between the two terms. Potting generally refers to the process of filling a housing or mold containing the PCB assembly with a compound material. Encapsulation, on the other hand, can refer to a broader range of techniques, including potting, conformal coating, and overmolding, used to protect electronic components or assemblies.
2. Can potting be removed if rework is necessary?
Removing potting can be a challenging and time-consuming process, but it is possible in some cases. The method for removing potting depends on the type of potting compound used. Some compounds can be softened with heat or dissolved with solvents, while others may require mechanical removal, such as cutting or grinding. However, the removal process can be risky and may damage the PCB or components.
3. How does potting affect the thermal management of a PCB?
Potting can have both positive and negative effects on the thermal management of a PCB. On one hand, potting can help distribute heat more evenly across the PCB, preventing hot spots and thermal stress. On the other hand, potting compounds are typically thermal insulators, which can make it more difficult for heat to escape from the PCB. To mitigate this issue, thermally conductive potting compounds or additional heat sinking measures may be necessary.
4. Can potting be used for waterproofing a PCB?
Yes, potting is an effective method for waterproofing a PCB. By completely encapsulating the PCB and its components, potting prevents water and other liquids from reaching and damaging the sensitive electronic parts. However, it is important to choose a potting compound that is specifically designed for waterproofing and has good adhesion to the PCB materials.
5. What are the curing methods for potting compounds?
Potting compounds can be cured using various methods, depending on the specific material and application requirements. Some common curing methods include:
- Room temperature curing: The potting compound cures at ambient temperatures over a period of several hours to several days.
- Heat curing: The potted assembly is placed in an oven or subjected to a heat source to accelerate the curing process.
- UV curing: The potting compound contains a photoinitiator that allows it to cure when exposed to ultraviolet (UV) light.
The choice of curing method depends on factors such as the desired curing time, the heat sensitivity of the PCB components, and the production environment.
Conclusion
Potting is a valuable technique for protecting PCBs and electronic components from environmental factors, mechanical stress, and tampering. By encapsulating the PCB in a compound material, potting provides a barrier against moisture, dust, chemicals, and other harmful elements. Potting also enhances the mechanical strength and durability of the PCB, making it more resistant to vibrations, shocks, and impacts.
However, potting also has some drawbacks, such as increased weight and size, thermal management challenges, and rework difficulties. The choice to use potting depends on the specific requirements and constraints of the application, as well as the selection of an appropriate potting compound.
PCB potting is widely used in various industries, including automotive, aerospace, military, industrial, medical, and security. As electronic devices continue to become more complex and are deployed in increasingly harsh environments, the importance of potting will only continue to grow.
By understanding the basics of PCB potting, including the materials, process, benefits, and drawbacks, engineers and manufacturers can make informed decisions about when and how to implement this critical protection technique.
Leave a Reply