Characteristics of Polyimide PCB
Thermal Stability
One of the most notable characteristics of polyimide PCBs is their excellent thermal stability. Polyimide has a glass transition temperature (Tg) of approximately 360°C and a decomposition temperature of around 620°C. This means that polyimide PCBs can withstand high temperatures without deteriorating or losing their structural integrity.
The thermal stability of polyimide PCBs is particularly advantageous in applications that involve extreme temperature conditions, such as aerospace, automotive, and high-power electronics. Polyimide PCBs can operate reliably in temperature ranges from -269°C to +400°C, making them suitable for both cryogenic and high-temperature environments.
Chemical Resistance
Polyimide PCBs exhibit excellent chemical resistance, making them resistant to a wide range of chemicals, solvents, and acids. This property is crucial in applications where the PCB may be exposed to harsh chemical environments, such as in the chemical processing industry or in medical equipment.
The chemical resistance of polyimide PCBs also contributes to their long-term reliability. They are less susceptible to degradation caused by exposure to chemicals, which helps to extend their operational lifespan and reduce the need for frequent replacements.
Mechanical Strength
Polyimide PCBs possess outstanding mechanical strength and durability. Polyimide has a high tensile strength and a low coefficient of thermal expansion (CTE), which means that it can withstand significant mechanical stress without cracking or breaking.
The mechanical strength of polyimide PCBs is particularly beneficial in applications that involve vibration, shock, or physical stress. They are less likely to suffer from mechanical failures, such as cracking or delamination, which can lead to electrical failures and system downtime.
Dielectric Properties
Polyimide has excellent dielectric properties, making it suitable for high-frequency and high-speed applications. It has a low dielectric constant (Dk) and a low dissipation factor (Df), which helps to minimize signal loss and maintain signal integrity.
The dielectric properties of polyimide PCBs are especially important in applications that involve high-speed data transmission, such as in telecommunications, networking, and radar systems. The low dielectric constant and dissipation factor of polyimide help to reduce signal attenuation and distortion, ensuring reliable and efficient signal transmission.
Applications of Polyimide PCB
Polyimide PCBs find applications in various industries and sectors due to their unique properties and performance characteristics. Some of the common applications of polyimide PCBs include:
Aerospace and Aviation
Polyimide PCBs are widely used in the aerospace and aviation industry due to their ability to withstand extreme temperatures, vibrations, and exposure to chemicals. They are used in avionics systems, satellite communications, and aircraft control systems.
The thermal stability and mechanical strength of polyimide PCBs make them suitable for use in high-altitude and space applications, where the PCBs may be subjected to extreme temperature fluctuations and mechanical stresses.
Automotive Electronics
In the automotive industry, polyimide PCBs are used in various electronic systems, such as engine control units (ECUs), transmission control modules, and power management systems. The high-temperature resistance and reliability of polyimide PCBs make them suitable for use in the harsh operating conditions found in automotive environments.
Polyimide PCBs can withstand the high temperatures generated by automotive engines and exhaust systems, ensuring reliable performance and reducing the risk of failure.
Medical Equipment
Polyimide PCBs are used in medical equipment and devices that require high reliability, chemical resistance, and biocompatibility. They are used in medical imaging systems, implantable devices, and diagnostic equipment.
The chemical resistance of polyimide PCBs is particularly important in medical applications, as they may be exposed to bodily fluids, disinfectants, and sterilization processes. Polyimide PCBs can withstand these harsh conditions without degrading or releasing harmful substances.
Industrial Equipment
Polyimide PCBs are used in various industrial equipment and systems, such as power electronics, motor drives, and process control systems. The thermal stability and mechanical strength of polyimide PCBs make them suitable for use in industrial environments where high temperatures and vibrations are common.
Polyimide PCBs can withstand the high operating temperatures and mechanical stresses found in industrial equipment, ensuring reliable performance and minimizing the risk of failure.
Telecommunications and Networking
Polyimide PCBs are used in telecommunications and networking equipment, such as routers, switches, and fiber optic systems. The low dielectric constant and low dissipation factor of polyimide make it suitable for high-frequency and high-speed applications.
The excellent dielectric properties of polyimide PCBs help to minimize signal loss and maintain signal integrity, ensuring reliable and efficient data transmission in telecommunications and networking systems.
Advantages of Polyimide PCB
Polyimide PCBs offer several advantages over other types of PCBs, making them a preferred choice for many applications. Some of the key advantages of polyimide PCBs include:
-
High-temperature resistance: Polyimide PCBs can withstand extreme temperatures, making them suitable for use in high-temperature environments.
-
Chemical resistance: Polyimide PCBs are resistant to a wide range of chemicals, solvents, and acids, ensuring reliable performance in harsh chemical environments.
-
Mechanical strength: Polyimide PCBs possess high tensile strength and low CTE, making them resistant to mechanical stress and less prone to failure.
-
Excellent dielectric properties: Polyimide has a low dielectric constant and low dissipation factor, making it suitable for high-frequency and high-speed applications.
-
Long-term reliability: The thermal stability, chemical resistance, and mechanical strength of polyimide PCBs contribute to their long-term reliability and reduced need for replacements.
-
Lightweight and flexible: Polyimide PCBs can be made thin and lightweight, making them suitable for applications where weight and space are critical factors. They also offer a degree of flexibility, allowing for the design of flexible circuits.
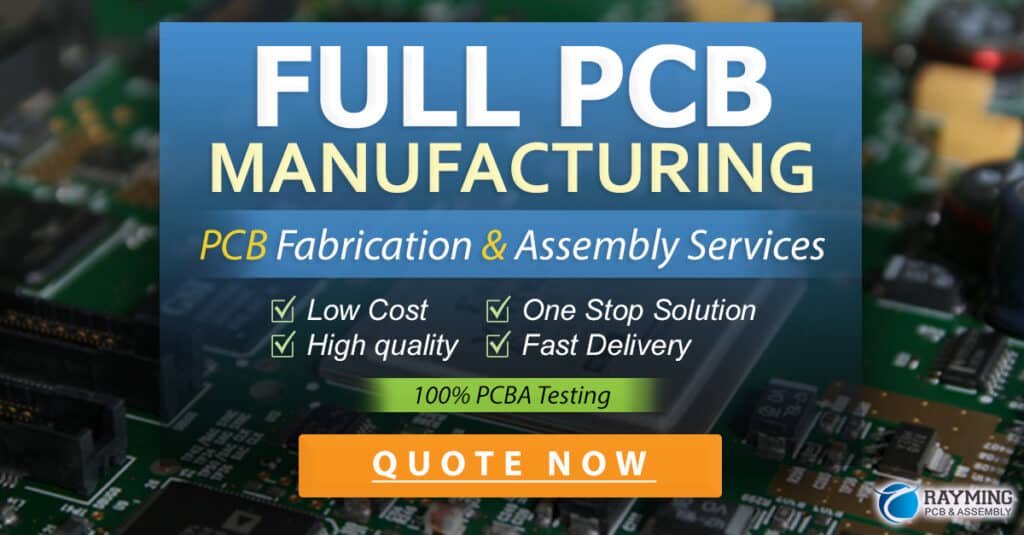
Challenges and Considerations
While polyimide PCBs offer numerous advantages, there are also some challenges and considerations to keep in mind when using them:
-
Higher cost: Polyimide PCBs are generally more expensive than other types of PCBs due to the high cost of polyimide material and the specialized manufacturing processes required.
-
Manufacturing complexity: The manufacturing process for polyimide PCBs is more complex compared to standard PCBs, requiring specialized equipment and expertise. This can lead to longer lead times and higher manufacturing costs.
-
Limited availability: Not all PCB manufacturers have the capability to produce polyimide PCBs, which can limit the availability and sourcing options for designers and engineers.
-
Design considerations: Designing with polyimide PCBs may require additional considerations, such as accounting for the material’s thermal expansion and ensuring proper adhesion between layers.
Despite these challenges, the benefits of polyimide PCBs often outweigh the drawbacks, particularly in applications where high performance and reliability are critical.
Frequently Asked Questions (FAQ)
-
What is the operating temperature range of polyimide PCBs?
Polyimide PCBs can operate reliably in temperature ranges from -269°C to +400°C, making them suitable for both cryogenic and high-temperature environments. -
Are polyimide PCBs resistant to chemicals?
Yes, polyimide PCBs exhibit excellent chemical resistance and are resistant to a wide range of chemicals, solvents, and acids. -
What industries commonly use polyimide PCBs?
Polyimide PCBs are commonly used in industries such as aerospace, automotive, medical equipment, industrial equipment, and telecommunications. -
How do polyimide PCBs compare to other types of PCBs in terms of cost?
Polyimide PCBs are generally more expensive than other types of PCBs due to the high cost of polyimide material and the specialized manufacturing processes required. -
Can polyimide PCBs be made flexible?
Yes, polyimide PCBs can be made thin and lightweight, offering a degree of flexibility that allows for the design of flexible circuits.
Conclusion
Polyimide PCB is a high-performance printed circuit board material that offers exceptional thermal stability, chemical resistance, and mechanical strength. These properties make polyimide PCBs ideal for applications that require reliable performance in demanding environments, such as aerospace, automotive, medical equipment, industrial equipment, and telecommunications.
While polyimide PCBs may have higher costs and manufacturing complexity compared to standard PCBs, their unique properties and performance characteristics often justify their use in critical applications. As technology continues to advance and the demand for high-performance electronics grows, polyimide PCBs are likely to play an increasingly important role in enabling reliable and efficient systems across various industries.
Property | Polyimide PCB | Standard FR-4 PCB |
---|---|---|
Glass Transition Temperature (Tg) | ~360°C | ~130°C |
Decomposition Temperature | ~620°C | ~300°C |
Operating Temperature Range | -269°C to +400°C | -40°C to +140°C |
Chemical Resistance | Excellent | Good |
Tensile Strength | High | Moderate |
Coefficient of Thermal Expansion (CTE) | Low | Moderate |
Dielectric Constant (Dk) | Low | Moderate |
Dissipation Factor (Df) | Low | Moderate |
Cost | High | Moderate |
Table 1: Comparison of properties between polyimide PCB and standard FR-4 PCB.
As evident from the comparison table, polyimide PCBs offer superior properties in terms of thermal stability, chemical resistance, mechanical strength, and dielectric properties compared to standard FR-4 PCBs. However, these enhanced properties come at a higher cost.
When selecting between polyimide PCBs and other types of PCBs, designers and engineers must carefully consider the specific requirements of their application, weighing the benefits of polyimide PCBs against the associated costs and manufacturing complexities. In applications where high performance and reliability are paramount, polyimide PCBs are often the preferred choice.
Leave a Reply