Introduction to Plating Index
Plating index is a critical parameter in the electroplating industry that measures the efficiency and quality of the plating process. It is a numerical value that indicates the amount of metal deposited on the substrate surface during the electroplating process. The plating index is influenced by various factors such as current density, temperature, pH, and the composition of the plating solution.
Importance of Plating Index
The plating index is an essential factor in determining the quality and performance of the electroplated coating. A high plating index indicates a thicker and more uniform coating, while a low plating index may result in a thin and uneven coating. The plating index also affects the adhesion, hardness, and corrosion resistance of the coating.
Factors Affecting Plating Index
Several factors can influence the plating index during the electroplating process. These factors include:
-
Current Density: The current density is the amount of electric current flowing through the plating solution per unit area. A higher current density generally results in a higher plating index.
-
Temperature: The temperature of the plating solution can affect the plating index. Higher temperatures typically increase the plating index, while lower temperatures may decrease it.
-
pH: The pH of the plating solution can also influence the plating index. The optimal pH range varies depending on the type of metal being plated and the composition of the plating solution.
-
Composition of the Plating Solution: The composition of the plating solution, including the concentration of metal ions and additives, can affect the plating index. The presence of impurities or contaminants in the solution may also impact the plating index.
Measuring Plating Index
Methods for Measuring Plating Index
There are several methods for measuring the plating index, including:
-
Weight Gain Method: In this method, the weight of the substrate is measured before and after the electroplating process. The difference in weight is used to calculate the plating index.
-
Thickness Measurement: The thickness of the electroplated coating can be measured using techniques such as microscopy, profilometry, or X-ray fluorescence. The measured thickness is then used to determine the plating index.
-
Coulometric Method: This method involves measuring the amount of electric charge passed through the plating solution during the electroplating process. The plating index can be calculated based on the charge and the surface area of the substrate.
Plating Index Calculation
The plating index can be calculated using the following formula:
Plating Index = (Weight of Metal Deposited) / (Surface Area of Substrate)
The weight of metal deposited is typically expressed in milligrams (mg), while the surface area of the substrate is expressed in square centimeters (cm²).
For example, if 50 mg of nickel is deposited on a substrate with a surface area of 10 cm², the plating index would be:
Plating Index = 50 mg / 10 cm² = 5 mg/cm²
Plating Index Solutions
Optimizing Plating Index
To achieve the desired plating index and ensure the quality of the electroplated coating, it is essential to optimize the various factors that influence the plating process. Some strategies for optimizing the plating index include:
-
Adjusting the current density: By increasing or decreasing the current density, the plating index can be controlled. Higher current densities generally result in a higher plating index, but excessive current densities may lead to poor coating quality or substrate damage.
-
Controlling the temperature: Maintaining the plating solution at the optimal temperature range can help achieve a consistent plating index. Temperature control systems, such as heating or cooling coils, can be used to regulate the solution temperature.
-
Maintaining the pH: Regularly monitoring and adjusting the pH of the plating solution can ensure that it remains within the optimal range for the specific metal being plated. pH buffers or automated pH control systems can be employed to maintain a stable pH.
-
Selecting appropriate additives: The use of additives in the plating solution can enhance the plating index and improve the quality of the coating. Brighteners, levelers, and stress reducers are common additives used in electroplating processes.
Troubleshooting Plating Index Issues
If the plating index is not meeting the desired specifications, several troubleshooting steps can be taken:
-
Check the composition of the plating solution: Ensure that the metal ion concentration and the levels of additives are within the recommended ranges. Contamination or depletion of the solution components can adversely affect the plating index.
-
Verify the current density: Confirm that the current density is set correctly and that the power supply is functioning properly. Fluctuations in the current density can lead to inconsistent plating index values.
-
Inspect the substrate surface: The surface of the substrate should be clean, free from contaminants, and properly pretreated before electroplating. Poor surface preparation can result in a low plating index or poor adhesion of the coating.
-
Evaluate the plating time: Insufficient or excessive plating times can impact the plating index. Adjust the plating time based on the desired thickness and the plating rate of the specific metal being deposited.
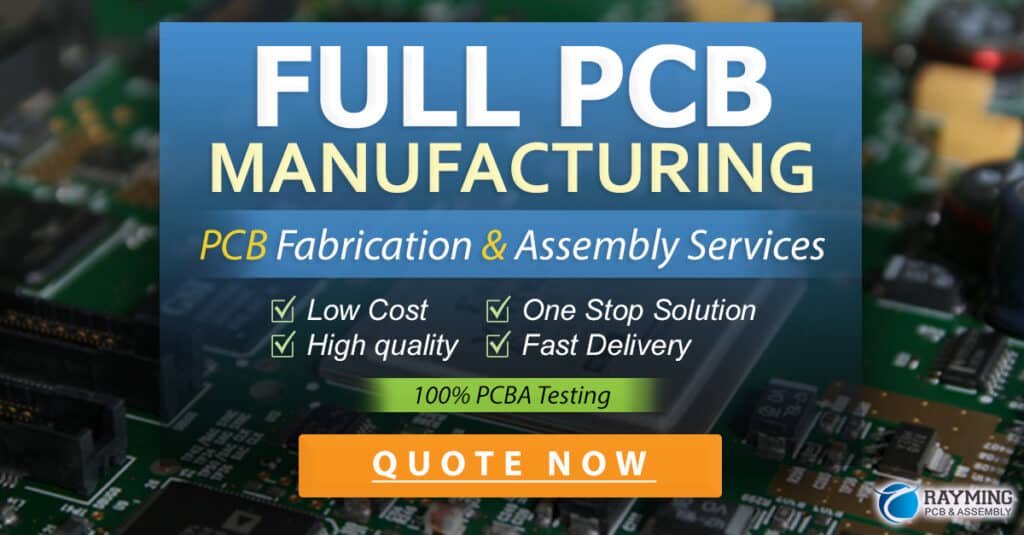
Plating Index Applications
Electronics Industry
In the electronics industry, electroplating is widely used for the fabrication of printed circuit boards (PCBs), connectors, and other components. The plating index plays a crucial role in ensuring the reliability and performance of these components.
Application | Metal | Typical Plating Index (mg/cm²) |
---|---|---|
PCB Copper Plating | Copper | 30-40 |
PCB Nickel Plating | Nickel | 5-10 |
PCB Gold Plating | Gold | 0.05-0.2 |
Automotive Industry
Electroplating is extensively employed in the automotive industry for decorative and functional purposes. The plating index is essential for achieving the desired appearance, durability, and corrosion resistance of automotive components.
Application | Metal | Typical Plating Index (mg/cm²) |
---|---|---|
Decorative Chrome Plating | Chromium | 0.2-0.4 |
Zinc Plating for Corrosion Protection | Zinc | 10-20 |
Hard Chrome Plating for Wear Resistance | Chromium | 50-100 |
Aerospace Industry
In the aerospace industry, electroplating is used for the protection and enhancement of various components, such as turbine blades, landing gear, and hydraulic systems. The plating index is critical for ensuring the performance and safety of these components under extreme conditions.
Application | Metal | Typical Plating Index (mg/cm²) |
---|---|---|
Cadmium Plating for Corrosion Protection | Cadmium | 5-15 |
Nickel Plating for High-Temperature Applications | Nickel | 20-40 |
Copper Plating for Electromagnetic Shielding | Copper | 30-50 |
Frequently Asked Questions (FAQ)
- What is the difference between plating thickness and plating index?
-
Plating thickness refers to the actual thickness of the metal coating deposited on the substrate, typically measured in micrometers (μm) or mils. Plating index, on the other hand, represents the amount of metal deposited per unit area of the substrate, expressed in milligrams per square centimeter (mg/cm²).
-
How does the plating index affect the quality of the electroplated coating?
-
The plating index directly influences the quality of the electroplated coating. A higher plating index generally results in a thicker, more uniform, and more protective coating. However, an excessively high plating index may lead to poor adhesion, increased internal stresses, or a rough surface finish. Achieving the optimal plating index is crucial for obtaining the desired coating properties.
-
Can the plating index be controlled during the electroplating process?
-
Yes, the plating index can be controlled by adjusting various parameters during the electroplating process. These parameters include the current density, temperature, pH, and composition of the plating solution. By carefully monitoring and regulating these factors, the plating index can be maintained within the desired range to ensure consistent coating quality.
-
What are the consequences of a low plating index?
-
A low plating index can result in several issues, such as thin and uneven coatings, poor corrosion protection, reduced wear resistance, and inadequate coverage of the substrate surface. These problems can compromise the performance and durability of the electroplated components, leading to premature failure or reduced service life.
-
How often should the plating index be measured during production?
- The frequency of plating index measurements depends on the specific requirements of the electroplating process and the industry standards. In general, it is recommended to measure the plating index at regular intervals, such as hourly or per shift, to ensure consistent coating quality. Additionally, plating index measurements should be performed whenever there are changes in the plating solution composition, substrate material, or process parameters.
Conclusion
The plating index is a vital parameter in the electroplating industry, as it directly influences the quality, performance, and reliability of the electroplated coatings. By understanding the factors that affect the plating index and implementing appropriate solutions, manufacturers can optimize their electroplating processes to achieve the desired coating properties consistently.
Measuring and monitoring the plating index regularly is essential for maintaining process control and ensuring the production of high-quality electroplated components. The plating index finds extensive applications in various industries, including electronics, automotive, and aerospace, where the performance and durability of the coatings are critical.
By leveraging the knowledge of plating index solutions and troubleshooting techniques, manufacturers can overcome challenges and improve the efficiency of their electroplating operations. Ultimately, a well-controlled plating index contributes to the production of superior electroplated components that meet the demanding requirements of modern industries.
Leave a Reply