Introduction to SMT PCB Assembly
Surface Mount Technology (SMT) PCB assembly is a popular method for manufacturing printed circuit boards (PCBs) in the electronics industry. This process involves placing and soldering electronic components directly onto the surface of a PCB, as opposed to the traditional through-hole method, where components are inserted into drilled holes and soldered on the opposite side of the board.
SMT PCB assembly has revolutionized the electronics manufacturing industry by enabling the production of smaller, lighter, and more densely populated pcbs. This technology has become increasingly important as consumer demand for compact and high-performance electronic devices continues to grow.
Advantages of SMT PCB Assembly
- Miniaturization: SMT components are smaller than through-hole components, allowing for more compact PCB designs.
- Increased component density: More components can be placed on a single PCB, resulting in higher functionality and reduced overall device size.
- Improved performance: SMT components have shorter lead lengths, reducing parasitic capacitance and inductance, thus improving high-frequency performance.
- Faster assembly: Automated SMT assembly processes are faster than manual through-hole assembly, enabling higher production rates.
- Cost-effective: SMT assembly requires less drilling and consumes less board space, reducing material costs and increasing production efficiency.
The SMT PCB Assembly Process
The SMT PCB assembly process consists of several key steps, each of which is crucial for ensuring the quality and reliability of the final product.
Step 1: PCB Design and Fabrication
Before SMT assembly can begin, the PCB must be designed and fabricated. This process involves creating a schematic diagram, converting it into a PCB layout, and generating the necessary files for manufacturing. The PCB is then fabricated using a variety of techniques, such as photolithography, etching, and drilling.
Step 2: Solder Paste Application
Once the PCB is fabricated, solder paste is applied to the pads where the SMT components will be placed. This is typically done using a stencil printing process, where a metal stencil with apertures corresponding to the component pads is aligned with the PCB. Solder paste is then applied over the stencil, filling the apertures and depositing the paste onto the pads.
Step 3: Component Placement
After solder paste application, SMT components are placed onto the PCB using an automated pick-and-place machine. These machines use vacuum nozzles to pick up components from feeders and place them precisely on the solder paste-covered pads. Modern pick-and-place machines can place thousands of components per hour with high accuracy.
Step 4: Reflow Soldering
Once all the components are placed, the PCB undergoes a reflow soldering process. The assembled PCB is passed through a reflow oven, which heats the board according to a predetermined temperature profile. This melts the solder paste, forming a permanent electrical and mechanical connection between the components and the PCB pads.
Step 5: Inspection and Testing
After reflow soldering, the assembled PCB undergoes various inspection and testing procedures to ensure quality and functionality. These may include:
- Automated Optical Inspection (AOI): A camera-based system that checks for component placement accuracy, solder joint quality, and other defects.
- X-ray Inspection: Used to inspect solder joints hidden under components, such as Ball Grid Arrays (BGAs).
- In-Circuit Testing (ICT): A bed-of-nails fixture that tests the PCB for short circuits, open circuits, and component functionality.
- Functional Testing: Verifies the overall functionality of the assembled PCB according to its design specifications.
SMT Component Packages
SMT components come in various package types, each with its own characteristics and advantages. Some common SMT component packages include:
- Chip Components: Resistors, capacitors, and inductors in small, rectangular packages (e.g., 0201, 0402, 0603, 0805, 1206).
- Small Outline Packages (SOPs): Integrated circuits with gull-wing leads on two sides of the package (e.g., SOIC, TSOP).
- Quad Flat Packages (QFPs): ICs with gull-wing leads on all four sides of the package.
- Ball Grid Arrays (BGAs): ICs with an array of solder balls on the underside of the package for high-density interconnections.
- Chip Scale Packages (CSPs): Miniaturized packages with dimensions close to the size of the die inside.
Package Type | Size Range (mm) | Lead Pitch (mm) | Advantages |
---|---|---|---|
Chip Components | 0.4 × 0.2 to 3.2 × 1.6 | N/A | Small size, low cost |
SOPs | 3.9 × 1.27 to 15.4 × 7.5 | 0.5 to 1.27 | Good thermal and electrical performance |
QFPs | 4 × 4 to 40 × 40 | 0.4 to 1.0 | High lead count, good thermal performance |
BGAs | 5 × 5 to 50 × 50 | 0.5 to 1.27 | High interconnection density, good thermal performance |
CSPs | 1 × 1 to 10 × 10 | 0.4 to 0.8 | Very small size, high-density interconnections |
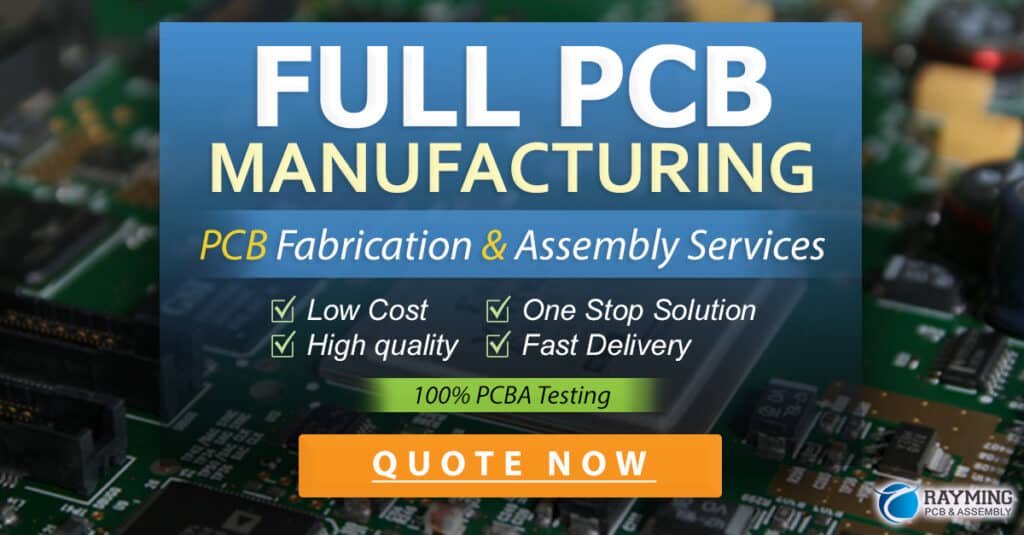
Challenges in SMT PCB Assembly
While SMT PCB assembly offers numerous advantages, it also presents some challenges that manufacturers must address to ensure high-quality and reliable products.
Miniaturization and High-Density Layouts
As electronic devices become smaller and more complex, PCBs must accommodate an increasing number of components in a limited space. This requires precise placement and soldering of miniature components, which can be challenging for both machines and human operators.
To overcome this challenge, manufacturers invest in advanced pick-and-place machines with high accuracy and precision, as well as fine-pitch stencils for solder paste application. Additionally, designing PCBs with manufacturability in mind, such as providing adequate spacing between components and using appropriate package types, can help mitigate the difficulties associated with miniaturization.
Thermal Management
With higher component densities and increased power consumption, thermal management becomes a critical concern in SMT PCB assembly. Inadequate heat dissipation can lead to component failure, reduced performance, and shortened product lifespan.
To address thermal management issues, manufacturers employ various strategies, such as:
- Using thermally conductive PCB materials, like metal core PCBs or thermal vias.
- Incorporating heat sinks or heat spreaders into the design.
- Optimizing component placement to minimize heat buildup and ensure proper airflow.
- Applying thermal interface materials (TIMs) between components and heat sinks.
Leadless Component Soldering
Leadless components, such as BGAs and QFNs, pose challenges in SMT assembly due to their lack of visible solder joints. This makes it difficult to inspect and rework these components, as the solder joints are hidden beneath the package.
To ensure reliable soldering of leadless components, manufacturers use advanced techniques like X-ray inspection to verify solder joint quality. They also employ specialized rework stations with precise temperature control and component alignment capabilities to facilitate the repair and replacement of leadless components.
Electrostatic Discharge (ESD) Protection
Many SMT components, particularly sensitive semiconductor devices, are vulnerable to damage from electrostatic discharge (ESD). ESD events can occur during handling, placement, or soldering, leading to latent defects or immediate component failure.
To protect components from ESD, manufacturers implement comprehensive ESD protection measures, including:
- Using ESD-safe workstations, tools, and packaging materials.
- Grounding operators and equipment to prevent static buildup.
- Maintaining a controlled environment with appropriate humidity levels.
- Training personnel in ESD awareness and handling procedures.
Future Trends in SMT PCB Assembly
As technology advances and market demands evolve, SMT PCB assembly continues to adapt and innovate. Some of the future trends shaping the industry include:
Advanced Materials
The development of new PCB materials, such as high-frequency laminates, flexible substrates, and 3D-printed materials, is enabling the creation of more complex and specialized PCB designs. These materials offer improved performance characteristics, like lower dielectric constants, higher thermal conductivity, and greater mechanical flexibility, expanding the possibilities for SMT PCB assembly.
Automated Optical Inspection (AOI) and Artificial Intelligence (AI)
AOI systems are becoming increasingly sophisticated, incorporating AI and machine learning algorithms to improve defect detection and classification. These advanced systems can learn from past data and adapt to new defect types, enabling more accurate and efficient inspection processes. As AOI and AI technologies continue to evolve, they will help manufacturers catch defects earlier, reduce rework costs, and improve overall product quality.
Industry 4.0 and Smart Manufacturing
The integration of Industry 4.0 technologies, such as the Internet of Things (IoT), big data analytics, and cloud computing, is transforming SMT PCB assembly into a more connected, data-driven process. Smart manufacturing systems can collect and analyze data from various sensors and machines, enabling real-time monitoring, predictive maintenance, and process optimization. This leads to increased efficiency, reduced downtime, and better decision-making throughout the production lifecycle.
Sustainability and Environmental Responsibility
As environmental concerns gain prominence, the electronics industry is focusing on developing more sustainable and eco-friendly SMT PCB assembly practices. This includes the adoption of lead-free soldering processes, the use of recyclable and biodegradable materials, and the implementation of energy-efficient manufacturing techniques. Manufacturers are also working to minimize waste, reduce their carbon footprint, and comply with international environmental regulations, such as RoHS and REACH.
Frequently Asked Questions (FAQ)
-
Q: What is the difference between SMT and through-hole assembly?
A: SMT (Surface Mount Technology) involves placing and soldering components directly onto the surface of a PCB, while through-hole assembly requires inserting component leads into drilled holes and soldering them on the opposite side of the board. SMT allows for smaller, denser PCBs and faster assembly, while through-hole is often used for larger components or in applications requiring greater mechanical strength. -
Q: Can SMT and through-hole components be used on the same PCB?
A: Yes, it is possible to use both SMT and through-hole components on the same PCB. This is called a mixed-technology or hybrid assembly. In such cases, the SMT components are typically placed and soldered first, followed by the through-hole components. -
Q: What is a stencil, and how is it used in SMT assembly?
A: A stencil is a thin metal sheet with apertures that correspond to the solder paste pads on a PCB. It is used to apply solder paste to the PCB before component placement. The stencil is aligned with the PCB, and solder paste is applied over the stencil, filling the apertures and depositing the paste onto the pads. This ensures precise and consistent solder paste application. -
Q: How are SMT components held in place during soldering?
A: SMT components are held in place during soldering by the surface tension of the molten solder. When the solder paste melts during the reflow soldering process, it forms a liquid pool that adheres to the component leads and PCB pads. As the solder cools and solidifies, it creates a strong mechanical and electrical bond, securing the components to the PCB. -
Q: What is the role of nitrogen in SMT reflow soldering?
A: Nitrogen is sometimes used in SMT reflow soldering to create an inert atmosphere inside the reflow oven. This helps to reduce oxidation on the solder joints, which can improve solder joint quality and reliability. Nitrogen also helps to minimize solder balling and other defects that can occur in the presence of oxygen. However, not all SMT assembly processes require the use of nitrogen, and its necessity depends on factors such as the type of solder paste used and the specific application requirements.
Conclusion
SMT PCB assembly is a crucial technology in the electronics manufacturing industry, enabling the production of smaller, faster, and more complex electronic devices. By placing and soldering components directly onto the surface of a PCB, SMT assembly offers numerous advantages, including miniaturization, increased component density, improved performance, and cost-effectiveness.
However, SMT PCB assembly also presents challenges, such as the need for precise placement and soldering of miniature components, thermal management, and ESD protection. Manufacturers must continually adapt and innovate to overcome these challenges and meet the evolving demands of the market.
As technology advances, the future of SMT PCB assembly is shaped by trends such as the adoption of advanced materials, the integration of AI and smart manufacturing techniques, and a focus on sustainability and environmental responsibility. By staying at the forefront of these developments, manufacturers can continue to produce high-quality, reliable, and innovative electronic products that meet the needs of an increasingly connected and technology-driven world.
Leave a Reply