The Importance of PCB Prototyping
PCB prototyping serves several essential purposes in the electronics industry:
-
Design Validation: Prototyping allows engineers to test the PCB design and ensure it meets the desired specifications and requirements.
-
Functionality Testing: By assembling and testing a prototype, engineers can verify that the PCB functions as intended and identify any potential issues.
-
Manufacturing Feasibility: Prototyping helps determine whether the PCB design is suitable for mass production and identifies any manufacturing challenges that need to be addressed.
-
Cost Optimization: Identifying and resolving issues during the prototyping stage can help avoid costly redesigns and production delays.
The PCB Prototyping Process
The PCB prototyping process typically involves the following steps:
1. Schematic Design
The first step in PCB prototyping is to create a schematic diagram of the circuit. This diagram represents the electrical connections and components of the PCB. Engineers use electronic design automation (EDA) software to create the schematic, such as:
- OrCAD
- Altium Designer
- KiCad
- Eagle
2. PCB Layout Design
Once the schematic is complete, engineers proceed to design the physical layout of the PCB. This involves determining the placement of components, routing the traces, and defining the board dimensions. The layout design must consider factors such as:
- Component footprints
- Signal integrity
- Power distribution
- Thermal management
- Manufacturing constraints
EDA software is also used for PCB layout design, with popular options including:
- Altium Designer
- Cadence Allegro
- Mentor Graphics PADS
- KiCad
3. Design Rule Check (DRC)
After completing the PCB layout, engineers perform a design rule check (DRC) to ensure the design meets the manufacturing requirements. DRC verifies aspects such as:
- Minimum trace width and spacing
- Drill hole sizes
- Copper pour clearances
- Solder mask and silkscreen requirements
EDA software typically includes built-in DRC tools to automate this process.
4. Gerber File Generation
Once the PCB layout passes the DRC, engineers generate Gerber files, which are the industry-standard format for PCB fabrication. Gerber files contain information such as:
- Copper layers
- Solder mask
- Silkscreen
- Drill data
These files are sent to the PCB manufacturer for fabrication.
5. Bill of Materials (BOM) Creation
In parallel with Gerber file generation, engineers create a bill of materials (BOM), which lists all the components required to assemble the PCB. The BOM typically includes:
- Component reference designators
- Manufacturer part numbers
- Quantities
- Descriptions
The BOM is used for component procurement and assembly.
6. PCB Fabrication
The PCB manufacturer uses the Gerber files to fabricate the prototype PCBs. The fabrication process involves several steps:
- Copper Cladding: Applying a thin layer of copper to the substrate material.
- Photoresist Application: Coating the copper layer with a light-sensitive material.
- Exposure: Transferring the PCB pattern onto the photoresist using UV light.
- Etching: Removing unwanted copper from the board, leaving only the desired traces.
- Drilling: Creating holes for through-hole components and vias.
- Solder Mask Application: Applying a protective layer over the copper traces.
- Silkscreen Printing: Adding text and symbols to the PCB for component identification.
- Surface Finish: Applying a protective coating to the exposed copper to prevent oxidation.
7. PCB Assembly
After fabrication, the PCB prototype is assembled with the components specified in the BOM. This process can be done manually or using automated assembly equipment, depending on the complexity of the board and the quantity required.
Common assembly techniques include:
- Through-hole assembly (THA): Components are inserted into drilled holes and soldered on the opposite side of the board.
- Surface-mount technology (SMT): Components are placed and soldered directly onto the surface of the board.
8. Testing and Debugging
Once the PCB prototype is assembled, engineers perform various tests to verify its functionality and performance. Common testing methods include:
- Visual inspection
- Continuity testing
- Power-on testing
- Functional testing
- Boundary scan testing
If issues are identified during testing, engineers debug the PCB to determine the root cause and implement necessary design changes.
9. Iteration and Refinement
Based on the testing results, engineers may need to iterate on the PCB design to resolve issues or improve performance. This may involve:
- Schematic modifications
- Component changes
- Layout adjustments
- Manufacturing process improvements
The prototyping process is repeated until the PCB meets all requirements and is ready for mass production.
PCB Prototyping Technologies
Several technologies are used in PCB prototyping, each with its own advantages and limitations. The choice of technology depends on factors such as design complexity, turnaround time, and budget.
1. Traditional PCB Prototyping
Traditional PCB prototyping involves the standard fabrication process, as described earlier. This method is suitable for most PCB designs and offers good reliability and performance. However, it may have longer lead times and higher costs compared to other prototyping technologies.
2. rapid pcb prototyping
Rapid PCB prototyping technologies aim to reduce turnaround times and costs for prototype fabrication. Some common rapid prototyping methods include:
2.1 pcb milling
PCB milling uses a computer-controlled milling machine to remove unwanted copper from a pre-laminated PCB substrate. This method is suitable for simple to medium complexity designs and offers fast turnaround times. However, it has limitations in terms of trace width, spacing, and via size.
2.2 Laser PCB Prototyping
Laser PCB prototyping uses a laser to ablate unwanted copper from the PCB substrate. This method offers high precision and can handle complex designs with fine features. However, it is generally more expensive than PCB milling and may have limitations in terms of materials and surface finishes.
2.3 Desktop PCB Prototyping
Desktop PCB prototyping involves using small-scale, office-friendly equipment to fabricate PCBs in-house. This includes PCB milling machines, 3D printers, and vinyl cutters. While desktop prototyping offers quick turnaround times and low costs, it is limited in terms of design complexity and quality compared to professional PCB fabrication services.
3. High-Density Interconnect (HDI) PCB Prototyping
hdi pcbs feature higher wiring density and smaller feature sizes compared to traditional PCBs. They are used in applications that require miniaturization, high performance, and increased functionality. HDI PCB prototyping involves specialized fabrication processes, such as:
- Microvias: Small-diameter vias that connect inner layers of the PCB.
- Buried vias: Vias that connect inner layers but do not extend to the outer layers.
- Blind vias: Vias that connect an outer layer to an inner layer but do not extend to the opposite side of the board.
- Sequential lamination: Building up the PCB in multiple lamination cycles to create complex multilayer structures.
HDI PCB prototyping offers benefits such as reduced board size, improved signal integrity, and higher component density. However, it also comes with higher costs and longer lead times compared to traditional PCB prototyping.
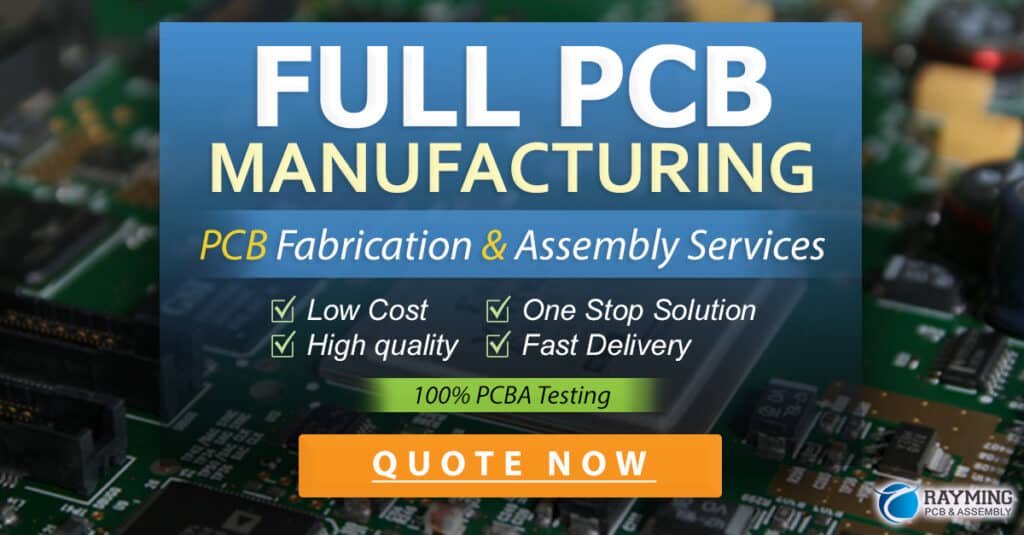
Choosing a PCB Prototyping Service
When selecting a PCB prototyping service, consider the following factors:
-
Capabilities: Ensure the service provider can handle your design complexity, layer count, and special requirements (e.g., HDI, flex PCBs).
-
Quality: Look for a provider with a proven track record of producing high-quality PCB prototypes. Request samples or references to assess their workmanship.
-
Turnaround Time: Consider the provider’s standard lead times and whether they offer expedited services if needed.
-
Cost: Compare pricing from multiple providers, but don’t sacrifice quality for lower costs.
-
Customer Support: Choose a provider with responsive and knowledgeable customer support to assist you throughout the prototyping process.
Some popular PCB prototyping service providers include:
- PCBWay
- JLCPCB
- OSH Park
- Seeed Studio
- Eurocircuits
PCB Prototyping Best Practices
To ensure a successful PCB prototyping experience, follow these best practices:
-
Thorough Design Review: Conduct a comprehensive review of your schematic and layout to catch any errors or potential issues before prototyping.
-
DFM Considerations: Design your PCB with manufacturing in mind, adhering to the fabrication capabilities and guidelines of your chosen service provider.
-
Clear Documentation: Provide clear and complete documentation, including Gerber files, BOMs, and assembly instructions, to avoid delays and miscommunications.
-
Component Availability: Verify the availability and lead times of critical components before finalizing your BOM.
-
Testing Plan: Develop a comprehensive testing plan to validate your prototype’s functionality, performance, and reliability.
-
Iterative Approach: Be prepared to iterate on your design based on prototype testing results. Incorporate feedback and make necessary improvements.
-
Collaboration: Foster open communication and collaboration among design, manufacturing, and testing teams to streamline the prototyping process.
PCB Prototyping vs. Mass Production
While PCB prototyping and mass production share some similarities, there are key differences to consider:
Aspect | Prototyping | Mass Production |
---|---|---|
Quantity | Low (1-100 units) | High (100+ units) |
Lead Time | Shorter (days to weeks) | Longer (weeks to months) |
Cost per Unit | Higher | Lower |
Design Changes | More flexible | Limited flexibility |
Testing | Focused on functionality and debugging | Focused on process control and quality assurance |
Documentation | Less formal | Formal and comprehensive |
Understanding these differences can help you plan your product development timeline and budget effectively.
Frequently Asked Questions (FAQ)
- How long does PCB prototyping take?
-
The turnaround time for PCB prototyping varies depending on the complexity of the design and the service provider. Typical lead times range from a few days to several weeks.
-
How much does PCB prototyping cost?
-
PCB prototyping costs depend on factors such as board size, layer count, quantity, and turnaround time. Prices can range from tens to thousands of dollars, depending on the project requirements.
-
What files are needed for PCB prototyping?
-
To start PCB prototyping, you typically need to provide Gerber files (RS-274X format), drill files (Excellon format), a bill of materials (BOM), and assembly instructions (if applicable).
-
Can I prototype a PCB at home?
-
Yes, it is possible to prototype simple PCBs at home using desktop equipment such as PCB milling machines or 3D printers. However, for more complex designs or higher-quality results, it is recommended to use professional PCB prototyping services.
-
What should I do if my PCB prototype doesn’t work?
- If your PCB prototype doesn’t function as intended, start by visually inspecting the board for any obvious defects or assembly issues. Use a multimeter to check for continuity and short circuits. If the problem persists, review your schematic and layout for design errors. If necessary, consult with your prototyping service provider or seek assistance from experienced engineers to debug the issue.
PCB prototyping is an essential step in the product development process, allowing engineers to validate and refine their designs before committing to mass production. By understanding the prototyping process, technologies, and best practices, you can create successful PCB prototypes that meet your project requirements and pave the way for a smooth transition to production.
Leave a Reply