The History of PCB Production
The concept of printed circuits dates back to the early 20th century when inventors began experimenting with methods to simplify the wiring of electronic devices. In 1925, Charles Ducas filed a patent for a method of creating an electrical path directly on an insulated surface by printing through a stencil with electrically conductive inks. This laid the groundwork for the development of modern PCBs.
During World War II, the United States military heavily invested in PCB technology to improve the reliability and efficiency of electronic equipment used in warfare. In the 1950s and 1960s, PCB production techniques advanced rapidly, with the introduction of double-sided boards, plated-through holes, and photoresist methods.
Key Milestones in PCB Production
- 1925: Charles Ducas patents a method for creating electrical paths on an insulated surface
- 1943: Paul Eisler develops the first operational printed circuit board
- 1950s: Double-sided PCBs and plated-through holes are introduced
- 1960s: Photoresist methods and multilayer PCBs are developed
- 1980s: Surface mount technology (SMT) becomes widely adopted
- 1990s-present: High-density interconnect (HDI) PCBs and advanced materials are developed
The PCB Production Process
The PCB production process involves several key steps, each requiring precision and adherence to strict quality control measures. These steps include:
- Design and Layout
- Substrate Selection
- Copper Deposition
- Photoresist Application
- Exposure and Development
- Etching
- Drill and Plating
- Solder Mask and Silkscreen
- Surface Finish
- Electrical Testing and Inspection
1. Design and Layout
The PCB production process begins with the design and layout of the electronic circuit. Engineers use specialized software, such as Altium Designer or Eagle, to create a schematic diagram of the circuit and then convert it into a physical layout. The layout determines the size, shape, and placement of the components, as well as the routing of the conductive tracks.
2. Substrate Selection
The substrate is the non-conductive base material of the PCB, typically made from glass-reinforced epoxy laminate (FR-4). Other substrate materials include polyimide, ceramic, and metal-core laminates, each with unique properties suited for specific applications. The choice of substrate depends on factors such as the operating environment, required electrical properties, and cost.
3. Copper Deposition
A thin layer of copper is uniformly deposited onto the substrate using either electroless or electrolytic plating methods. This copper layer will form the conductive tracks and pads of the PCB.
4. Photoresist Application
A photosensitive resist material is applied to the copper-clad substrate. The photoresist can be either liquid or dry film and is typically applied using a roller or spray coating process.
5. Exposure and Development
The PCB layout design is printed onto a photomask, which is then placed on top of the photoresist-coated substrate. The photomask is exposed to ultraviolet (UV) light, causing the exposed areas of the photoresist to harden. The unexposed areas are then removed using a chemical developer solution, revealing the copper layer beneath.
6. Etching
The exposed copper areas are etched away using a chemical solution, typically ferric chloride or ammonium persulfate. This process removes the unwanted copper, leaving only the desired conductive tracks and pads.
7. Drill and Plating
Holes are drilled through the PCB to accommodate through-hole components and enable electrical connections between layers in multi-layer boards. The holes are then plated with copper to ensure electrical continuity.
8. Solder Mask and Silkscreen
A solder mask, usually green in color, is applied to the PCB to protect the copper tracks from oxidation and prevent solder bridges during the assembly process. A silkscreen layer is then added to print component labels, logos, and other identifying marks on the PCB.
9. Surface Finish
A surface finish, such as HASL (Hot Air Solder Leveling), ENIG (Electroless Nickel Immersion Gold), or OSP (Organic Solderability Preservative), is applied to the exposed copper areas to improve solderability and protect against corrosion.
10. Electrical Testing and Inspection
The completed PCB undergoes rigorous electrical testing and visual inspection to ensure it meets the required specifications and is free from defects. Automated optical inspection (AOI) systems and electrical test fixtures are used to verify the quality of the PCB.
Types of PCBs
PCBs can be classified based on various factors, such as the number of layers, component mounting method, and manufacturing technology. Some common types of PCBs include:
Single-Sided PCBs
Single-sided PCBs have conductive tracks and components on only one side of the substrate. These boards are the simplest and most cost-effective to manufacture but have limitations in terms of circuit complexity and density.
Double-Sided PCBs
Double-sided PCBs have conductive tracks and components on both sides of the substrate, allowing for more complex circuits and higher component density compared to single-sided boards. The two layers are connected using plated-through holes.
Multi-Layer PCBs
Multi-layer PCBs consist of three or more layers of conductive tracks, separated by insulating layers. These boards offer the highest level of circuit complexity and density, making them suitable for advanced applications such as high-speed digital devices and aerospace systems.
PCB Type | Layers | Complexity | Cost |
---|---|---|---|
Single-Sided | 1 | Low | Low |
Double-Sided | 2 | Medium | Medium |
Multi-Layer | 3+ | High | High |
Rigid PCBs
Rigid PCBs are the most common type, using a solid, inflexible substrate material such as FR-4. These boards provide excellent mechanical stability and are suitable for a wide range of applications.
Flexible PCBs
Flexible PCBs use a thin, flexible substrate material such as polyimide, allowing the board to bend and conform to various shapes. These boards are ideal for applications requiring compact packaging or movable parts, such as mobile devices and wearable electronics.
Rigid-Flex PCBs
Rigid-flex PCBs combine the benefits of both rigid and flexible PCBs, featuring rigid sections for component mounting and flexible sections for interconnections. This hybrid design offers enhanced reliability and space savings in complex, multi-board systems.
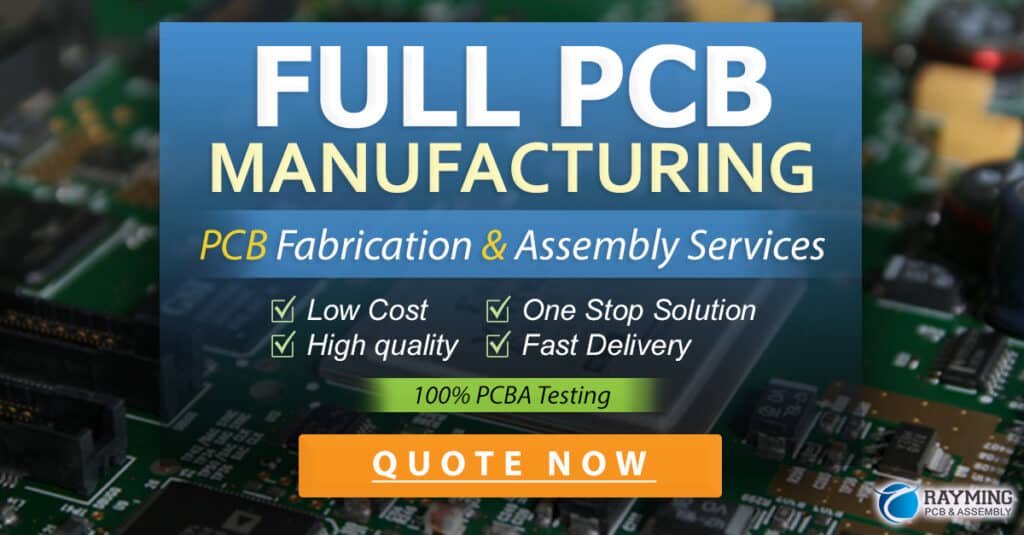
PCB Manufacturing Technologies
Several manufacturing technologies have emerged to address the increasing demands for miniaturization, high-speed performance, and cost-effectiveness in PCB production. Some notable technologies include:
Surface Mount Technology (SMT)
SMT is a method of mounting electronic components directly onto the surface of a PCB, as opposed to through-hole mounting. SMT components are smaller and can be placed on both sides of the board, enabling higher component density and improved high-frequency performance.
High-Density Interconnect (HDI)
HDI PCBs feature finer trace widths, smaller vias, and higher connection pad density compared to traditional PCBs. This technology allows for the miniaturization of electronic devices and improved signal integrity in high-speed applications.
Embedded Component Technology
Embedded component technology involves placing passive components, such as resistors and capacitors, inside the layers of a multi-layer PCB. This approach saves space on the board surface, reduces signal paths, and improves overall system performance.
Quality Control in PCB Production
Ensuring the quality and reliability of PCBs is critical for the success of electronic products. Quality control measures are implemented throughout the PCB production process, including:
-
Design Rule Checking (DRC): Verifying the PCB layout against a set of predefined design rules to identify potential issues before manufacturing.
-
Automated Optical Inspection (AOI): Using computer vision systems to inspect the PCB for defects such as shorts, opens, and incorrect component placement.
-
X-Ray Inspection: Utilizing X-ray imaging to detect internal defects, such as voids in solder joints and improper plating in vias.
-
Electrical Testing: Conducting various electrical tests, such as continuity, insulation resistance, and high-potential (hipot) tests, to ensure the PCB meets the required electrical specifications.
-
Burn-In Testing: Subjecting the PCB to elevated temperatures and electrical loads to identify potential early-life failures and ensure long-term reliability.
Environmental Considerations in PCB Production
As environmental concerns continue to grow, the PCB industry has been working towards adopting more eco-friendly practices. Some key initiatives include:
-
Lead-Free Manufacturing: Transitioning from lead-based to lead-free solder alloys to reduce the environmental impact of PCB production and disposal.
-
Halogen-Free Materials: Using halogen-free substrates and solder masks to minimize the release of toxic substances during PCB manufacturing and end-of-life disposal.
-
Waste Reduction and Recycling: Implementing waste reduction strategies, such as optimizing material usage and recycling waste materials, to minimize the environmental footprint of PCB production.
-
Green Packaging: Adopting eco-friendly packaging materials and practices, such as using biodegradable or recyclable packaging, to reduce waste and environmental impact.
Future Trends in PCB Production
As technology advances and market demands evolve, the PCB industry is embracing new trends and innovations to stay competitive. Some notable future trends include:
-
5G and High-Frequency Applications: The rollout of 5G networks and the increasing demand for high-frequency applications are driving the development of advanced PCB materials and manufacturing techniques to support higher signal speeds and lower latency.
-
Miniaturization and High-Density Packaging: The trend towards smaller, more compact electronic devices is pushing the boundaries of PCB miniaturization and high-density packaging technologies, such as 3D printing and embedded components.
-
Flexible and Wearable Electronics: The growing market for flexible and wearable electronic devices is driving the demand for flexible and stretchable PCBs, as well as the development of new materials and manufacturing processes to enable these applications.
-
Smart Factory and Industry 4.0: The adoption of smart factory technologies, such as automation, artificial intelligence, and the Internet of Things (IoT), is transforming PCB production by enabling more efficient, flexible, and quality-focused manufacturing processes.
Frequently Asked Questions (FAQ)
1. What is the difference between a PCB and a PCBA?
A PCB (Printed Circuit Board) is the bare board with conductive tracks and pads, while a PCBA (Printed Circuit Board Assembly) is a PCB populated with electronic components.
2. What is the most common PCB substrate material?
FR-4, a glass-reinforced epoxy laminate, is the most widely used PCB substrate material due to its excellent mechanical, thermal, and electrical properties, as well as its cost-effectiveness.
3. How long does it take to produce a PCB?
The lead time for PCB production can vary depending on factors such as board complexity, manufacturing technology, and order quantity. Typical lead times range from a few days for simple, quick-turn prototypes to several weeks for complex, high-volume production runs.
4. What is the minimum feature size in PCB production?
The minimum feature size in PCB production depends on the manufacturing technology and the capabilities of the specific PCB manufacturer. Advanced technologies, such as HDI and embedded components, can achieve feature sizes as small as 50 microns or less.
5. How can I ensure the quality and reliability of my PCBs?
To ensure the quality and reliability of your PCBs, work with a reputable PCB manufacturer that adheres to strict quality control standards and industry certifications, such as ISO 9001 and IPC-A-600. Clearly communicate your requirements and specifications, and consider implementing additional quality assurance measures, such as third-party inspections and testing.
In conclusion, PCB production is a complex and ever-evolving process that plays a critical role in the development of modern electronic devices. By understanding the key steps, technologies, and trends in PCB manufacturing, designers and engineers can make informed decisions to ensure the success of their projects and stay ahead of the curve in this dynamic industry.
Leave a Reply