What is PCB Prepreg Made Of?
PCB Prepreg is made of two main components:
-
Base Fabric: The base fabric is usually made of glass fibers, which are woven into a specific pattern. The most common types of glass fibers used in PCB Prepreg are E-glass and S-glass. E-glass is the most widely used due to its good electrical insulation properties and cost-effectiveness, while S-glass offers higher strength and better performance at elevated temperatures.
-
Resin System: The resin system used in PCB Prepreg is typically an epoxy-based material. The resin is partially cured, meaning that it is in a semi-solid state, allowing it to be easily handled and stored. When the Prepreg is subjected to heat and pressure during the PCB manufacturing process, the resin fully cures, bonding the layers together and providing a strong, stable structure.
Properties of PCB Prepreg
PCB Prepreg has several key properties that make it an essential material in the manufacturing of high-quality PCBs:
Electrical Insulation
One of the most important properties of PCB Prepreg is its excellent electrical insulation. The base fabric and resin system work together to provide a high dielectric strength, preventing electrical current from passing between the conductive layers of the PCB. This is crucial for maintaining signal integrity and preventing short circuits.
Mechanical Strength
PCB Prepreg provides mechanical strength to the PCB, helping to prevent warping, twisting, and other deformations that can occur during the manufacturing process and in use. The glass fiber base fabric contributes to the overall strength and stability of the PCB, while the resin system helps to distribute stress evenly throughout the board.
Thermal Stability
PCB Prepreg is designed to withstand the high temperatures encountered during the PCB manufacturing process, as well as the operating temperatures of the finished product. The resin system used in PCB Prepreg is formulated to have a high glass transition temperature (Tg), which is the temperature at which the material transitions from a rigid, glassy state to a softer, rubbery state. A higher Tg ensures that the PCB remains stable and maintains its mechanical properties at elevated temperatures.
Dimensional Stability
PCB Prepreg helps to maintain the dimensional stability of the PCB throughout the manufacturing process and in use. The base fabric and resin system work together to minimize shrinkage and expansion, ensuring that the PCB maintains its intended shape and size. This is particularly important for high-density PCBs with fine pitch components, where even small dimensional changes can lead to reliability issues.
Types of PCB Prepreg
There are several types of PCB Prepreg available, each with its own unique properties and applications. Some of the most common types include:
FR-4 Prepreg
FR-4 Prepreg is the most widely used type of PCB Prepreg. It is made with an E-glass base fabric and an epoxy resin system. FR-4 Prepreg offers good electrical insulation, mechanical strength, and thermal stability, making it suitable for a wide range of applications, including consumer electronics, telecommunications equipment, and industrial control systems.
High Tg Prepreg
High Tg Prepreg is designed for use in applications that require higher thermal stability than standard FR-4 Prepreg. These materials typically have a glass transition temperature (Tg) of 170°C or higher, compared to around 130°C for standard FR-4. High Tg Prepreg is often used in automotive electronics, aerospace systems, and other applications where the PCB may be exposed to elevated temperatures.
Low Dk/Df Prepreg
Low Dk/Df Prepreg is designed for use in high-speed digital applications, where signal integrity is critical. These materials have a low dielectric constant (Dk) and low dissipation factor (Df), which helps to minimize signal loss and distortion. Low Dk/Df Prepreg is often used in high-speed networking equipment, 5G telecommunications infrastructure, and advanced radar systems.
Halogen-Free Prepreg
Halogen-free Prepreg is made with resin systems that do not contain halogens, such as bromine and chlorine. These materials are designed to meet increasingly stringent environmental regulations, such as the Restriction of Hazardous Substances (RoHS) directive. Halogen-free Prepreg offers similar performance to traditional FR-4 Prepreg, but with reduced environmental impact.
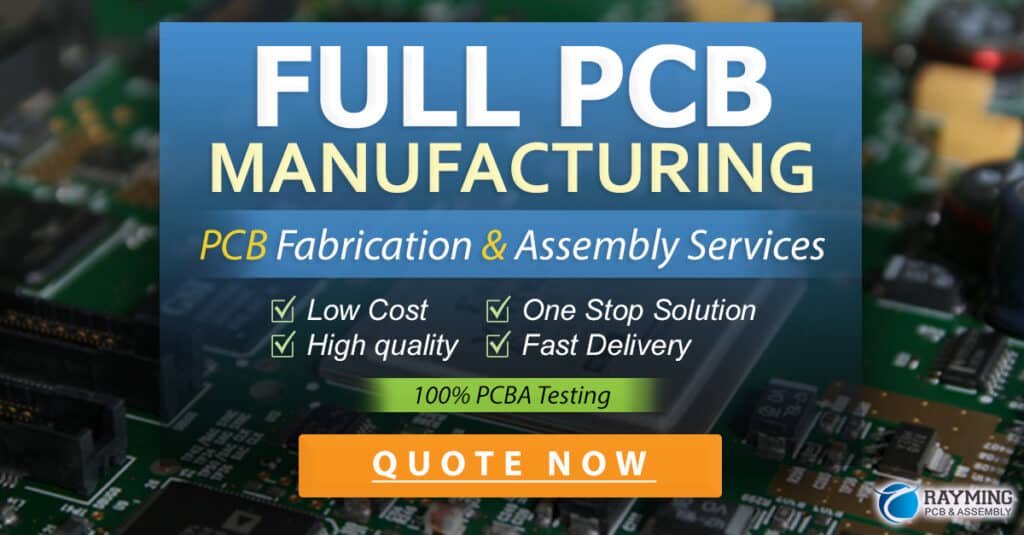
PCB Prepreg Manufacturing Process
The manufacturing process for PCB Prepreg involves several key steps:
-
Glass Fiber Production: The glass fibers used in PCB Prepreg are typically produced using a drawing process, where molten glass is drawn through a series of dies to create thin, continuous filaments. These filaments are then bundled together to form strands, which are woven into a specific pattern to create the base fabric.
-
Resin Formulation: The resin system used in PCB Prepreg is carefully formulated to provide the desired electrical, mechanical, and thermal properties. The resin is typically an epoxy-based material, which is mixed with various additives and fillers to achieve the required performance characteristics.
-
Impregnation: The base fabric is impregnated with the resin system using a process called dip-coating. The fabric is passed through a bath of the resin, which is then squeezed between rollers to ensure even distribution and remove excess material.
-
Partial Curing: After impregnation, the Prepreg is subjected to a partial curing process, where it is heated to a specific temperature for a set time. This process causes the resin to partially polymerize, transforming it into a semi-solid state. The partially cured Prepreg is then cooled and stored for later use.
-
Cutting and Packaging: The partially cured Prepreg is cut to the desired size and shape, and then packaged for shipping to PCB manufacturers. The Prepreg is typically stored in a controlled environment to prevent premature curing and maintain its quality.
Role of PCB Prepreg in PCB Manufacturing
PCB Prepreg plays a critical role in the manufacturing of multilayer PCBs. The process involves several key steps:
-
Inner Layer Processing: The inner layers of the PCB are etched with the desired circuit pattern using a photolithographic process. These layers are typically made of copper-clad laminate, which consists of a thin layer of copper bonded to a base material, such as FR-4.
-
Layup: The inner layers are stacked together with sheets of PCB Prepreg between them. The number and arrangement of the layers depend on the specific design of the PCB.
-
Lamination: The stack of inner layers and Prepreg is placed in a lamination press, where it is subjected to high temperature and pressure. During this process, the resin in the Prepreg fully cures, bonding the layers together and creating a solid, unified structure.
-
Drilling: After lamination, holes are drilled through the PCB to accommodate through-hole components and provide interconnections between layers.
-
Outer Layer Processing: The outer layers of the PCB are then processed, which involves etching the circuit pattern, applying solder mask, and adding silkscreen markings.
Throughout this process, the PCB Prepreg provides the necessary insulation and mechanical support to ensure the reliability and performance of the finished PCB.
Factors Affecting PCB Prepreg Selection
When selecting PCB Prepreg for a specific application, several factors must be considered:
Dielectric Constant (Dk)
The dielectric constant (Dk) is a measure of a material’s ability to store electrical energy. In the context of PCB Prepreg, a lower Dk is generally desirable, as it helps to minimize signal loss and distortion, particularly at high frequencies. The Dk of PCB Prepreg can vary depending on the specific formulation of the resin system and the type of base fabric used.
Dissipation Factor (Df)
The dissipation factor (Df) is a measure of a material’s ability to dissipate electrical energy as heat. A lower Df is desirable in PCB Prepreg, as it helps to minimize signal loss and maintain signal integrity. Like Dk, the Df of PCB Prepreg can vary depending on the specific formulation of the resin system and the type of base fabric used.
Glass Transition Temperature (Tg)
The glass transition temperature (Tg) is the temperature at which a material transitions from a rigid, glassy state to a softer, rubbery state. In the context of PCB Prepreg, a higher Tg is generally desirable, as it ensures that the material maintains its mechanical and electrical properties at elevated temperatures. The Tg of PCB Prepreg can vary depending on the specific formulation of the resin system.
Thickness
The thickness of PCB Prepreg is another important consideration, as it affects the overall thickness of the finished PCB. Thinner Prepreg allows for the production of thinner PCBs, which can be important for applications where space is limited. However, thinner Prepreg may also be more challenging to work with during the PCB manufacturing process.
Cost
The cost of PCB Prepreg is also a factor to consider, particularly for high-volume production. While higher-performance materials may offer better electrical and mechanical properties, they may also come at a higher cost. It is important to balance the requirements of the application with the cost of the materials to ensure a cost-effective solution.
Choosing the Right PCB Prepreg
Choosing the right PCB Prepreg for a specific application requires careful consideration of the electrical, mechanical, and thermal requirements of the finished product. Some key factors to consider include:
-
Operating Environment: The operating environment of the finished product, including temperature, humidity, and exposure to chemicals or other harsh conditions, can impact the choice of PCB Prepreg. For example, applications exposed to high temperatures may require a Prepreg with a higher Tg, while applications exposed to moisture may require a Prepreg with enhanced moisture resistance.
-
Electrical Requirements: The electrical requirements of the application, including the frequency and speed of the signals, can also impact the choice of PCB Prepreg. For example, high-speed digital applications may require a Prepreg with a low Dk and Df to minimize signal loss and distortion, while high-voltage applications may require a Prepreg with a higher dielectric strength.
-
Mechanical Requirements: The mechanical requirements of the application, including the expected level of stress and strain on the PCB, can also impact the choice of PCB Prepreg. For example, applications subject to high levels of vibration or mechanical shock may require a Prepreg with enhanced mechanical strength and stability.
-
Cost and Availability: The cost and availability of different types of PCB Prepreg can also be a factor in the selection process. While higher-performance materials may offer better properties, they may also come at a higher cost and may not be readily available in all regions.
To help guide the selection process, PCB manufacturers often work closely with Prepreg suppliers to identify the most suitable materials for a given application. Many suppliers offer a range of standard and custom Prepreg formulations, allowing manufacturers to tailor the properties of the material to the specific needs of the application.
Conclusion
PCB Prepreg is a critical material in the production of high-quality, reliable PCBs. Its unique combination of electrical insulation, mechanical strength, and thermal stability makes it an essential component in a wide range of electronic applications, from consumer devices to advanced aerospace systems.
As the demand for higher-performance, more compact, and more reliable electronic systems continues to grow, the development of new and improved PCB Prepreg formulations will be essential. By working closely with Prepreg suppliers and staying up-to-date with the latest advances in materials science, PCB manufacturers can ensure that they have access to the best possible materials for their applications, helping to drive innovation and progress in the electronics industry.
Frequently Asked Questions (FAQ)
- What is the difference between PCB Prepreg and core material?
-
PCB Prepreg is a composite material made of a base fabric pre-impregnated with a partially cured resin system, while core material is a fully cured, rigid material used as a base for the copper layers in a PCB. Prepreg is used to bond the layers of a multilayer PCB together during the lamination process, while core material provides the foundation for the copper layers.
-
Can PCB Prepreg be stored for an extended period?
-
Yes, PCB Prepreg can be stored for an extended period, provided that it is kept in a controlled environment with stable temperature and humidity. Prepreg should be stored in a sealed container to prevent moisture absorption and should be used within the manufacturer’s recommended shelf life to ensure optimal performance.
-
What is the typical glass transition temperature (Tg) of FR-4 Prepreg?
-
The typical glass transition temperature (Tg) of standard FR-4 Prepreg is around 130°C. However, high Tg versions of FR-4 Prepreg are available with Tg values of 170°C or higher for applications that require enhanced thermal stability.
-
How does the dielectric constant (Dk) of PCB Prepreg affect signal integrity?
-
The dielectric constant (Dk) of PCB Prepreg can have a significant impact on signal integrity, particularly at high frequencies. A lower Dk helps to minimize signal loss and distortion, as it reduces the amount of electrical energy that is stored in the material. This is particularly important for high-speed digital applications, where maintaining signal integrity is critical.
-
Can PCB Prepreg be used in flexible PCBs?
- Yes, specialized PCB Prepreg formulations are available for use in flexible PCBs. These materials typically use a more flexible base fabric, such as polyimide, and a resin system that can withstand the bending and flexing encountered in flexible applications. Flexible PCB Prepreg helps to provide the necessary insulation and mechanical support while allowing the PCB to conform to the desired shape.
Property | FR-4 Prepreg | High Tg Prepreg | Low Dk/Df Prepreg |
---|---|---|---|
Glass Transition Temperature (Tg) | 130°C | 170°C or higher | Varies |
Dielectric Constant (Dk) | 4.2 – 4.5 | 4.2 – 4.5 | 3.0 – 3.5 |
Dissipation Factor (Df) | 0.02 – 0.03 | 0.02 – 0.03 | 0.002 – 0.01 |
Typical Applications | Consumer electronics, telecommunications equipment, industrial control systems | Automotive electronics, aerospace systems, high-temperature applications | High-speed digital applications, 5G telecommunications infrastructure, advanced radar systems |
Leave a Reply