Types of PCB Plating
There are several types of PCB plating used in the industry, each with its own advantages and applications. The most common types include:
Electroless Plating
Electroless plating is a chemical process that deposits a thin layer of metal onto the PCB surface without the use of an electric current. This method is often used for plating non-conductive surfaces or creating a uniform coating on complex geometries. The most common metals used in electroless plating are copper, nickel, and gold.
Electrolytic Plating
Electrolytic plating, also known as electroplating, uses an electric current to deposit metal ions onto the PCB surface. This process requires a conductive surface and is typically used for thicker, more durable platings. Copper, nickel, gold, and tin are commonly used in electrolytic plating.
Immersion Plating
Immersion plating is a simple process that involves dipping the PCB into a solution containing metal ions. The metal ions then adhere to the PCB surface through a chemical reaction. This method is often used for creating thin, decorative coatings and is not suitable for functional platings. Common metals used in immersion plating include gold, silver, and tin.
PCB Plating Process Steps
The PCB plating process typically involves several steps to ensure a high-quality, durable finish. These steps may vary depending on the specific plating method and the desired outcome, but generally include:
1. Cleaning
The first step in the PCB plating process is to thoroughly clean the board surface to remove any contaminants, such as dirt, grease, or oxidation. This is usually done using a combination of chemical cleaning agents and mechanical scrubbing.
2. Surface Preparation
After cleaning, the PCB surface is prepared for plating by roughening it to improve adhesion. This can be done through a process called micro-etching, which uses a chemical solution to create small pits and grooves in the surface.
3. Activation
The next step is to activate the PCB surface to ensure that the plating adheres properly. This is typically done by dipping the board in a solution containing a catalyst, such as palladium or titanium.
4. Plating
The actual plating process involves depositing a layer of metal onto the PCB surface. The specific method used will depend on the type of plating being performed (electroless, electrolytic, or immersion). The thickness of the plating can be controlled by adjusting the duration of the process or the concentration of the plating solution.
5. Rinsing and Drying
After plating, the PCB is rinsed with water to remove any excess plating solution and then dried using hot air or a centrifuge.
6. Inspection and Quality Control
The final step in the PCB plating process is to inspect the board for any defects or inconsistencies in the plating. This is typically done using visual inspection, microscopy, or electrical testing methods. If any issues are found, the board may need to be reworked or scrapped.
Advantages of PCB Plating
PCB plating offers several key benefits that make it an essential part of the electronics manufacturing process. These advantages include:
-
Improved Electrical Conductivity
Plating the PCB surface with a layer of metal, such as copper, significantly improves its electrical conductivity. This allows for better signal transfer and reduces the risk of electrical interference or signal loss. -
Enhanced Durability
Plated PCBs are more resistant to wear, corrosion, and environmental factors, such as humidity and temperature fluctuations. This makes them suitable for use in harsh industrial or outdoor environments. -
Better Solderability
Plating the PCB surface with a solderable metal, such as tin or silver, improves its ability to form strong, reliable solder joints. This is critical for ensuring the long-term reliability of the electronic device. -
Increased Aesthetic Appeal
Plated PCBs often have a more attractive, professional appearance than unplated boards. This can be important for consumer electronics or other applications where visual appeal is a key consideration.
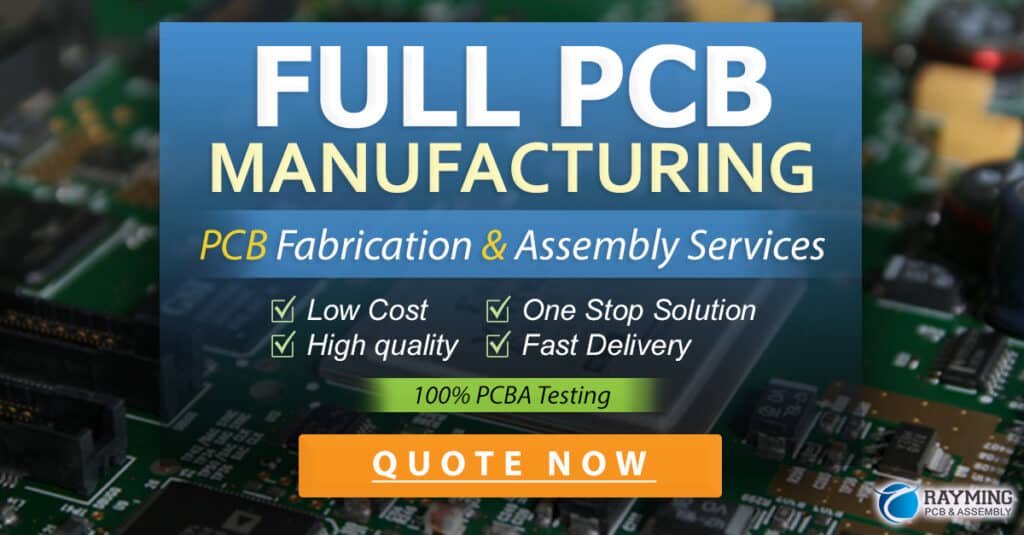
Common PCB Plating Materials
Several metals are commonly used in PCB plating, each with its own unique properties and advantages. The most popular plating materials include:
Copper
Copper is the most widely used plating material in the PCB industry due to its excellent electrical conductivity, solderability, and relatively low cost. It is often used as a base layer for other platings, such as nickel or gold.
Nickel
Nickel plating is commonly used as a barrier layer between the copper base and other plating materials, such as gold. It provides excellent corrosion resistance and helps to prevent the diffusion of copper into the outer plating layer.
Gold
Gold plating is often used in high-reliability applications, such as aerospace or military electronics, due to its excellent corrosion resistance and electrical conductivity. However, it is also the most expensive plating option.
Tin
Tin plating is commonly used as a solderable finish for PCBs. It provides good solderability and is relatively inexpensive compared to other plating options.
Silver
Silver plating is sometimes used as an alternative to gold in high-frequency applications due to its excellent electrical conductivity. However, it is less common than other plating materials due to its higher cost and lower durability.
PCB Plating Thickness
The thickness of the PCB plating is an important consideration, as it affects the board’s electrical and mechanical properties. Plating thickness is typically measured in micrometers (μm) and can range from a few microns to several dozen microns, depending on the application and the plating material used.
Plating Material | Typical Thickness Range (μm) |
---|---|
Copper | 5 – 150 |
Nickel | 1 – 10 |
Gold | 0.05 – 2.5 |
Tin | 0.5 – 15 |
Silver | 0.05 – 2.5 |
Thicker platings generally provide better durability and corrosion resistance, but may also increase the cost and weight of the PCB. Thinner platings, on the other hand, may be sufficient for less demanding applications and can help to reduce costs.
PCB Plating Challenges and Considerations
While PCB plating is a well-established process, there are several challenges and considerations that must be taken into account to ensure a successful outcome. These include:
-
Surface Preparation
Proper surface preparation is critical for ensuring good plating adhesion and avoiding defects. This includes cleaning the board thoroughly and roughening the surface to improve adhesion. -
Plating Uniformity
Achieving a uniform plating thickness across the entire PCB surface can be challenging, particularly for complex geometries or large boards. Careful control of the plating process parameters, such as current density and solution concentration, is necessary to ensure consistent results. -
Stress and Deformation
The plating process can introduce stress into the PCB, which can cause warping or other deformations. This is particularly problematic for thin or flexible boards. Proper process control and the use of stress-relieving techniques, such as annealing, can help to mitigate these issues. -
Environmental Concerns
Many PCB plating processes involve the use of hazardous chemicals, such as strong acids or cyanide-based solutions. Proper handling, storage, and disposal of these chemicals are essential to ensure the safety of workers and the environment. -
Cost Considerations
PCB plating can be a significant cost driver, particularly for high-reliability applications that require expensive materials like gold. Balancing performance requirements with cost constraints is an ongoing challenge in the industry.
Frequently Asked Questions (FAQ)
-
What is the difference between electroless and electrolytic plating?
Electroless plating is a chemical process that does not require an electric current, while electrolytic plating uses an electric current to deposit metal ions onto the PCB surface. Electroless plating is often used for non-conductive surfaces or complex geometries, while electrolytic plating is used for thicker, more durable platings. -
Why is copper the most common PCB plating material?
Copper is widely used in PCB plating due to its excellent electrical conductivity, solderability, and relatively low cost. It also serves as a good base layer for other platings, such as nickel or gold. -
What is the purpose of nickel plating in PCBs?
Nickel plating is often used as a barrier layer between the copper base and other plating materials, such as gold. It provides excellent corrosion resistance and helps to prevent the diffusion of copper into the outer plating layer. -
How does PCB plating thickness affect performance?
Thicker platings generally provide better durability and corrosion resistance, but may also increase the cost and weight of the PCB. Thinner platings may be sufficient for less demanding applications and can help to reduce costs. The specific thickness required will depend on the application and the plating material used. -
What environmental concerns are associated with PCB plating?
Many PCB plating processes involve the use of hazardous chemicals, such as strong acids or cyanide-based solutions. Proper handling, storage, and disposal of these chemicals are essential to ensure the safety of workers and the environment. The industry is continuously working to develop more environmentally friendly plating processes and materials.
In conclusion, PCB plating is a critical process in the manufacturing of electronic devices, providing improved electrical conductivity, durability, and solderability. By understanding the different types of plating, the process steps involved, and the common materials and challenges associated with PCB plating, engineers and manufacturers can ensure the production of high-quality, reliable electronic products.
Leave a Reply