Introduction to pcb panelization
PCB panelization is a process in the printed circuit board (PCB) manufacturing industry that involves grouping multiple identical or different PCB designs onto a single panel for efficient fabrication and assembly. This technique helps to optimize production time, reduce costs, and improve the overall quality of the final product.
What is a PCB Panel?
A PCB panel, also known as a PCB array or PCB matrix, is a larger board that contains multiple individual PCB designs arranged in a specific pattern. The panel is designed to fit the dimensions of the manufacturing equipment, such as pick-and-place machines, solder paste printers, and reflow ovens, to ensure efficient processing.
Benefits of PCB Panelization
PCB panelization offers several advantages to manufacturers and customers alike:
-
Cost reduction: By grouping multiple PCBs on a single panel, manufacturers can reduce the overall cost per unit, as the setup time and material costs are shared among the individual boards.
-
Faster production: Panelization allows for the simultaneous fabrication and assembly of multiple PCBs, significantly reducing the overall production time.
-
Improved quality: Panelized PCBs undergo the same manufacturing processes together, ensuring consistent quality across all boards in the panel.
-
Easier handling: Panels are easier to handle and transport compared to individual small pcbs, reducing the risk of damage during the manufacturing process.
PCB Panelization Techniques
There are several techniques used in PCB panelization, each with its own advantages and limitations. The choice of technique depends on factors such as the PCB design, material, thickness, and the intended application.
Tab Routing
Tab routing is one of the most common panelization techniques. In this method, individual PCBs are connected to the main panel through small tabs, which are cut off after the assembly process is complete. The tabs are designed to be strong enough to hold the PCBs in place during manufacturing but weak enough to be easily broken off without damaging the boards.
Advantages of tab routing:
– Simple and cost-effective
– Suitable for most PCB designs and materials
– Easy to depanelize using manual or automated methods
Limitations of tab routing:
– Tabs can leave behind small protrusions on the PCB edges
– Not suitable for very thin or fragile PCBs
Mouse Bites
Mouse bites, also known as perforations, are small, closely spaced holes drilled along the perimeter of each individual PCB. These holes weaken the connection between the PCB and the main panel, allowing for easy separation after the assembly process.
Advantages of mouse bites:
– Cleaner PCB edges compared to tab routing
– Suitable for thin and fragile PCBs
– Easy to depanelize using manual methods
Limitations of mouse bites:
– Higher cost compared to tab routing due to additional drilling
– Not suitable for thick or high-density PCBs
V-Scoring
V-scoring involves creating V-shaped grooves along the perimeter of each individual PCB using a special cutting tool. These grooves weaken the connection between the PCB and the main panel, allowing for easy separation after the assembly process.
Advantages of V-scoring:
– Clean and smooth PCB edges
– Suitable for thin and fragile PCBs
– Easy to depanelize using manual methods
Limitations of V-scoring:
– Higher cost compared to tab routing and mouse bites
– Not suitable for thick or high-density PCBs
– Risk of PCB damage if the V-score is too deep
Combination of Techniques
In some cases, manufacturers may use a combination of panelization techniques to achieve the best results. For example, a panel may use tab routing for the majority of the PCBs and mouse bites for smaller or more fragile boards.
PCB Panelization Design Considerations
When designing a PCB panel, several factors must be considered to ensure optimal manufacturability and quality.
Panel Size and Material
The panel size and material should be selected based on the manufacturing equipment capabilities and the specific requirements of the PCB design. Common panel sizes include:
Panel Size | Dimensions (mm) |
---|---|
Small | 200 x 250 |
Medium | 300 x 400 |
Large | 450 x 600 |
The most common panel materials are FR-4, aluminum, and flexible substrates like polyimide.
Tooling Holes and Fiducials
Tooling holes and fiducials are essential features in a PCB panel design. Tooling holes are used to secure the panel during the manufacturing process, while fiducials serve as reference points for aligning the panel in the manufacturing equipment.
PCB Orientation and Spacing
The orientation and spacing of the individual PCBs on the panel should be optimized to maximize the panel utilization and minimize waste. PCBs should be arranged in a way that allows for efficient routing and minimizes the risk of manufacturing defects.
Depaneling Methods
The depaneling method should be selected based on the panelization technique used and the specific requirements of the PCB design. Common depaneling methods include:
- Manual breakaway
- Hydraulic or pneumatic punching
- Laser cutting
- Routing
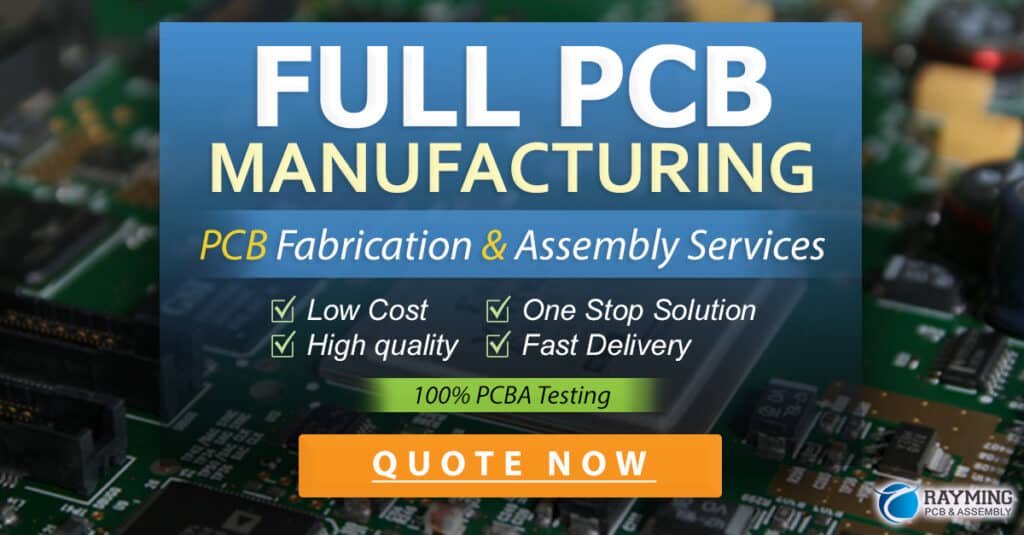
PCB Panelization and Assembly Process
The PCB panelization and assembly process typically involves the following steps:
-
Panel design: The panel layout is designed, taking into account the PCB design, manufacturing equipment capabilities, and panelization technique.
-
PCB fabrication: The panel is fabricated using standard PCB manufacturing processes, such as etching, drilling, and plating.
-
Solder paste printing: Solder paste is applied to the panel using a stencil or solder paste printer.
-
Component placement: Components are placed on the panel using a pick-and-place machine.
-
Reflow soldering: The panel undergoes reflow soldering to permanently attach the components to the PCBs.
-
Inspection and testing: The assembled panel is inspected and tested to ensure the quality and functionality of the individual PCBs.
-
Depaneling: The individual PCBs are separated from the panel using the selected depaneling method.
-
Final inspection and packaging: The individual PCBs undergo a final inspection and are packaged for shipping.
Frequently Asked Questions (FAQ)
-
What is the minimum spacing between PCBs on a panel?
The minimum spacing between PCBs on a panel depends on the panelization technique used and the manufacturing equipment capabilities. Generally, a minimum spacing of 2-3 mm is recommended to ensure proper separation and avoid manufacturing defects. -
Can different PCB designs be combined on the same panel?
Yes, different PCB designs can be combined on the same panel, as long as they share similar characteristics, such as material, thickness, and copper weight. This technique is known as “mixed panelization” and can help to further optimize production efficiency and cost. -
What is the maximum panel size that can be manufactured?
The maximum panel size depends on the manufacturing equipment capabilities and the specific PCB fabrication facility. Typical maximum panel sizes range from 450 x 600 mm to 600 x 800 mm, but larger sizes may be possible in some cases. -
How does PCB thickness affect panelization?
PCB thickness is an important consideration in panelization, as it affects the choice of panelization technique and the overall panel design. Thinner PCBs (less than 1.0 mm) may require special techniques like mouse bites or V-scoring to ensure clean and damage-free separation, while thicker PCBs can generally be panelized using tab routing. -
Can panelization be used for flexible PCBs?
Yes, panelization can be used for flexible PCBs, but the process requires special considerations. Flexible PCBs are typically panelized using a technique called “sheet panelization,” where the individual PCBs are arranged on a larger sheet of flexible material. The panelization design must account for the unique properties of the flexible substrate, such as its tendency to stretch or deform during handling.
Conclusion
PCB panelization is a crucial process in the PCB manufacturing industry, offering numerous benefits such as cost reduction, faster production, improved quality, and easier handling. By understanding the various panelization techniques, design considerations, and the overall assembly process, manufacturers can optimize their production efficiency and deliver high-quality PCBs to their customers.
As the electronics industry continues to evolve, with the increasing demand for smaller, more complex, and more affordable PCBs, the importance of effective PCB panelization will only continue to grow. By staying up-to-date with the latest panelization techniques and best practices, PCB manufacturers can remain competitive and meet the ever-changing needs of their customers.
Leave a Reply