Introduction to PCB Panels
A printed circuit board (PCB) panel, also known as a PCB array, is a large board that contains multiple identical PCB designs arranged in a matrix. The purpose of using PCB panels is to maximize the efficiency and cost-effectiveness of the PCB manufacturing process by producing multiple boards simultaneously.
Key Benefits of Using PCB Panels
- Reduced manufacturing costs
- Increased production efficiency
- Consistent quality across all boards
- Simplified handling and assembly
PCB Panel Design Considerations
When designing a PCB panel, several factors must be taken into account to ensure optimal results:
Panel Size and Layout
The size of the PCB panel is determined by the dimensions of the individual PCB designs and the number of boards to be produced. Common panel sizes include:
Panel Size | Dimensions (mm) |
---|---|
Small | 100 x 100 |
Medium | 200 x 200 |
Large | 300 x 300 |
The layout of the PCB designs within the panel should be carefully planned to maximize the number of boards while maintaining adequate spacing for tooling, registration marks, and other necessary features.
Tooling and Registration Marks
Tooling holes and registration marks are essential for aligning the PCB panel during the manufacturing process. These features ensure that each individual PCB is accurately positioned and consistent in quality.
- Tooling holes: Used to secure the panel during drilling, routing, and other machining operations.
- Registration marks: Used to align the panel during solder mask application, silk screen printing, and component placement.
Panelization Methods
There are several methods for panelizing PCB designs, each with its own advantages and disadvantages:
-
V-Scoring: V-shaped grooves are cut between the individual PCBs, allowing for easy separation after manufacturing. This method is suitable for simple designs and low-volume production.
-
Tab Routing: Small tabs are left connecting the individual PCBs, which can be easily broken off after manufacturing. This method provides a clean edge and is suitable for medium to high-volume production.
-
Perforated Tabs: Similar to tab routing, but with perforations added to the tabs for even easier separation. This method is ideal for high-volume production and automated assembly processes.
PCB Panel Fabrication Process
The fabrication of PCB panels involves several key steps:
-
PCB Design: The individual PCB designs are created using specialized software, taking into account the specific requirements of the intended application.
-
Panelization: The individual PCB designs are arranged into a panel layout, incorporating tooling holes, registration marks, and the chosen panelization method.
-
Drilling: Holes are drilled into the panel for through-hole components, mounting, and tooling purposes.
-
Plating: The panel is plated with copper to create the conductive traces and pads.
-
Etching: Unwanted copper is removed from the panel, leaving only the desired traces and pads.
-
Solder Mask Application: A protective solder mask is applied to the panel, covering the areas that should not be soldered.
-
Silk Screen Printing: Text, logos, and other markings are printed onto the panel using a silk screen process.
-
Surface Finish: A surface finish, such as HASL, lead-free HASL, or ENIG, is applied to the exposed copper to prevent oxidation and enhance solderability.
-
Routing and Separation: The individual PCBs are routed out of the panel using the chosen panelization method.
-
Quality Control: The finished PCBs are inspected for defects and tested to ensure proper functionality.
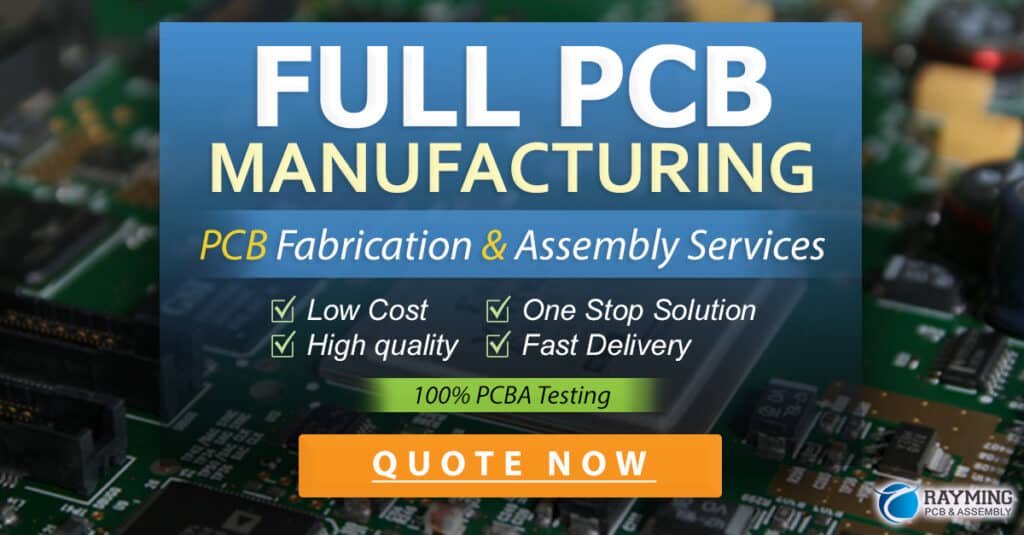
Advantages of Using PCB Panels in Manufacturing
Using PCB panels in the manufacturing process offers several significant advantages:
-
Cost Reduction: By producing multiple PCBs simultaneously, the cost per board is reduced, making it more economical for both the manufacturer and the customer.
-
Increased Efficiency: PCB panels allow for faster production times, as multiple boards can be processed in a single run, reducing setup time and labor costs.
-
Consistent Quality: Since all the PCBs on a panel are produced under the same conditions, the quality and consistency across the boards are maintained.
-
Simplified Handling: PCB panels are easier to handle and transport than individual boards, reducing the risk of damage and simplifying the assembly process.
Challenges and Considerations in PCB Panel Design
While PCB panels offer numerous benefits, there are also some challenges and considerations to keep in mind:
-
Design Complexity: Panelizing complex PCB designs can be challenging, as the layout must account for the specific requirements of the panel, such as tooling holes and registration marks.
-
Material Selection: The choice of PCB material can impact the panelization process, as some materials may be more prone to warping or other issues during manufacturing.
-
Breakout Method: The selected panelization method (v-scoring, tab routing, or perforated tabs) must be carefully considered based on the specific requirements of the PCB design and the intended application.
-
Panel Utilization: Maximizing panel utilization is essential for cost-effective production, but it must be balanced with the need for adequate spacing and tooling features.
-
Minimum Feature Size: The minimum feature size of the PCB design must be taken into account when panelizing, as smaller features may require more precise manufacturing techniques and tighter tolerances.
Best Practices for PCB Panel Design
To ensure the best results when designing PCB panels, consider the following best practices:
-
Collaborate with the Manufacturer: Work closely with the PCB manufacturer to understand their specific requirements and capabilities, ensuring that the panel design is optimized for their production process.
-
Use Standardized Panel Sizes: Whenever possible, use standardized panel sizes to reduce costs and simplify the manufacturing process.
-
Incorporate Adequate Spacing: Ensure that there is sufficient spacing between individual PCBs, tooling holes, and registration marks to prevent issues during manufacturing and assembly.
-
Minimize Waste: Optimize the panel layout to minimize waste material, reducing costs and environmental impact.
-
Test and Verify: Before finalizing the panel design, test and verify the layout to ensure that it meets all necessary requirements and functions as intended.
Future Trends in PCB Panel Design and Manufacturing
As technology continues to advance, several trends are shaping the future of PCB panel design and manufacturing:
-
Miniaturization: The demand for smaller, more compact electronic devices is driving the need for smaller PCBs and tighter tolerances in panel design.
-
Increased Complexity: PCB designs are becoming increasingly complex, with more layers, higher component densities, and advanced features like embedded components and high-speed interfaces.
-
Automation: Automated assembly processes are becoming more prevalent, requiring PCB panels to be designed with features that facilitate machine handling and placement.
-
Eco-Friendly Materials: There is a growing emphasis on using eco-friendly PCB materials and manufacturing processes to reduce environmental impact and comply with regulations.
-
Additive Manufacturing: Advances in additive manufacturing technologies, such as 3D printing, are opening up new possibilities for PCB panel design and fabrication, enabling faster prototyping and more complex geometries.
Conclusion
PCB panels play a critical role in the efficient and cost-effective manufacturing of printed circuit boards. By understanding the key considerations, best practices, and future trends in PCB panel design, engineers and manufacturers can optimize their production processes and deliver high-quality, reliable electronic products.
As technology continues to evolve, the importance of well-designed PCB panels will only grow, making it essential for professionals in the electronics industry to stay informed and adapt to the latest developments in this field.
Frequently Asked Questions (FAQ)
-
What is the purpose of using PCB panels in manufacturing?
PCB panels are used to maximize efficiency and cost-effectiveness in the PCB manufacturing process by producing multiple identical boards simultaneously. -
What are the common panelization methods for PCB designs?
The three common panelization methods are v-scoring, tab routing, and perforated tabs, each with its own advantages and suitable for different production volumes and requirements. -
How does the choice of PCB material affect the panelization process?
The choice of PCB material can impact the panelization process, as some materials may be more prone to warping or other issues during manufacturing. It’s essential to consider the material properties when designing the panel layout. -
What are the key benefits of using PCB panels?
The key benefits of using PCB panels include reduced manufacturing costs, increased production efficiency, consistent quality across all boards, and simplified handling and assembly. -
What are some future trends in PCB panel design and manufacturing?
Future trends in PCB panel design and manufacturing include miniaturization, increased complexity, automation, the use of eco-friendly materials, and the adoption of additive manufacturing technologies like 3D printing.
Leave a Reply