Introduction to PCB Milling
PCB milling, also known as PCB routing or PCB drilling, is a subtractive manufacturing process used to create printed circuit boards (PCBs). It involves using a milling machine or router to remove copper from a copper-clad substrate to create the desired electrical connections and circuit patterns on the PCB.
PCB milling is an alternative to traditional PCB manufacturing methods like etching and is often used for prototyping, low-volume production, and creating custom PCBs. It offers several advantages, such as quick turnaround times, low setup costs, and the ability to easily modify designs.
How PCB Milling Works
The PCB milling process involves several steps:
-
Design: The PCB design is created using computer-aided design (CAD) software, such as Eagle, KiCad, or Altium Designer. The design includes the component layout, electrical connections, and any necessary drill holes.
-
Toolpath Generation: The CAD design is then converted into a set of instructions for the milling machine, known as a toolpath. This toolpath specifies the movement of the milling bit and the areas where copper needs to be removed.
-
Milling: The copper-clad substrate is placed on the bed of the milling machine, and the milling bit is used to remove copper according to the generated toolpath. The milling bit is typically made of carbide or diamond and comes in various sizes and shapes to accommodate different trace widths and PCB features.
-
Drilling: After milling, any necessary drill holes for through-hole components or vias are created using a drill bit.
-
Cleaning: The milled PCB is cleaned to remove any debris or burrs resulting from the milling process.
-
Finishing: Additional finishing steps may be required, such as applying a solder mask, silkscreening component labels, or applying a surface finish to protect the copper traces and improve solderability.
Advantages of PCB Milling
PCB milling offers several advantages over traditional PCB manufacturing methods:
-
Quick Turnaround: PCB milling allows for faster prototyping and shorter lead times compared to etching or sending designs to a PCB manufacturer. This is particularly useful for iterative design processes or when time-to-market is critical.
-
Low Setup Costs: Unlike etching, which requires the creation of a photomask, PCB milling can be done directly from the CAD design, eliminating the need for additional tooling or setup costs.
-
Design Flexibility: PCB milling allows for easy modifications to the PCB design, as the milling process can be quickly adjusted to accommodate changes. This flexibility is valuable for prototyping and testing different design iterations.
-
In-House Production: With a PCB milling machine, designers and engineers can create PCBs in-house, reducing reliance on external PCB manufacturers and providing greater control over the manufacturing process.
-
Environmental Benefits: PCB milling is a cleaner process compared to etching, as it does not involve the use of harsh chemicals or generate hazardous waste.
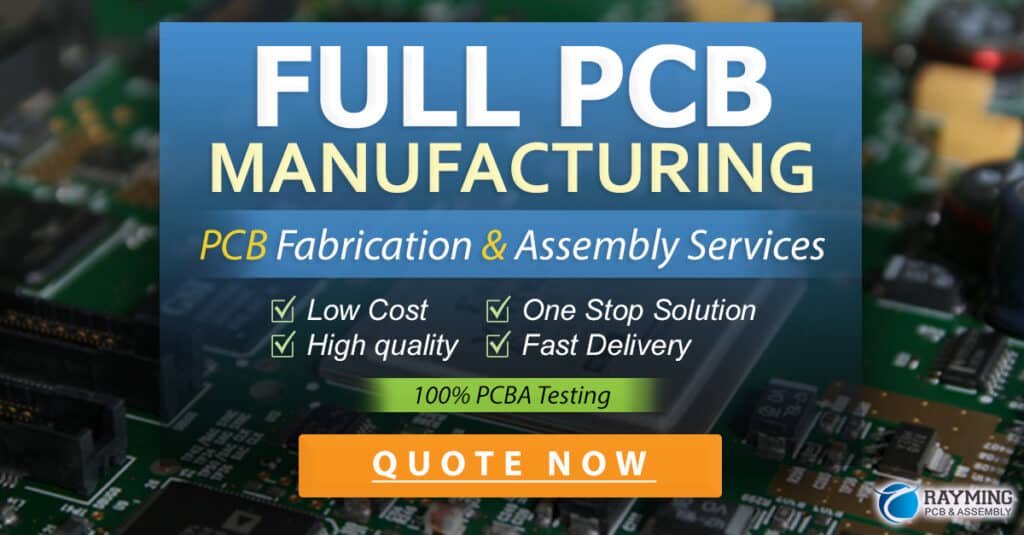
Limitations of PCB Milling
While PCB milling has its advantages, it also has some limitations:
-
Limited Resolution: The minimum trace width and spacing achievable with PCB milling are typically larger compared to etching or professional PCB manufacturing processes. This limitation is due to the size of the milling bit and the mechanical nature of the process.
-
Slower for High Volumes: PCB milling is slower than etching or other mass production methods, making it less suitable for high-volume production runs. It is best suited for prototyping and low-volume production.
-
Material Limitations: PCB milling is primarily used with FR-4 substrates and copper-clad boards. Some advanced substrate materials or very thin substrates may be challenging to mill without causing damage.
-
Wear and Tear: The milling bits used in PCB milling are subject to wear and tear over time, which can affect the quality of the milled traces and require regular replacement.
PCB Milling Machines
There are various types of PCB milling machines available, ranging from desktop models suitable for hobbyists and small workshops to larger, industrial-grade machines for professional use. Some popular desktop PCB milling machines include:
-
Bantam Tools Desktop PCB Milling Machine: A compact, user-friendly machine that is ideal for prototyping and educational purposes.
-
Othermill Pro: A versatile desktop CNC machine that can mill PCBs, as well as other materials like wood, plastic, and metal.
-
Prometheus PCB Milling Machine: A desktop machine designed specifically for PCB milling, offering high precision and a user-friendly interface.
-
LPKF ProtoMat Series: A range of professional-grade PCB milling machines that offer high-speed milling, automatic tool changes, and advanced features for more complex PCB designs.
When choosing a PCB milling machine, consider factors such as the maximum milling area, spindle speed, resolution, ease of use, and compatibility with your preferred CAD software.
PCB Milling Software
To create PCB designs and generate toolpaths for milling machines, various software options are available:
-
Eagle: A widely used PCB design software that offers a free version for non-commercial use and a subscription-based version with advanced features.
-
KiCad: An open-source PCB design software that is free to use and supports a wide range of features and plugins.
-
Altium Designer: A professional-grade PCB design software that offers advanced features and integrations with mechanical design tools.
-
FlatCAM: An open-source software that converts PCB designs into toolpaths for milling machines and supports various file formats.
-
Autodesk Fusion 360: A cloud-based CAD/CAM software that includes PCB design capabilities and can generate toolpaths for milling machines.
When selecting PCB milling software, consider factors such as ease of use, compatibility with your preferred milling machine, available features, and cost.
Tips for Successful PCB Milling
To achieve the best results when milling PCBs, consider the following tips:
-
Use the Right Milling Bits: Choose milling bits that are appropriate for your PCB design, considering factors such as trace width, substrate material, and desired surface finish.
-
Optimize Feedrate and Spindle Speed: Adjust the feedrate and spindle speed of your milling machine based on the material being milled, the size of the milling bit, and the desired surface finish. Consult the manufacturer’s recommendations or experiment to find the optimal settings.
-
Secure the Substrate: Ensure that the copper-clad substrate is securely fastened to the bed of the milling machine to prevent movement during the milling process, which can lead to inaccuracies or damage.
-
Use Dust Extraction: PCB milling generates dust and debris, which can interfere with the milling process and cause respiratory issues. Use a dust extraction system or vacuum to keep the milling area clean and safe.
-
Regularly Maintain Your Machine: Perform regular maintenance on your PCB milling machine, such as cleaning, lubricating, and replacing worn parts, to ensure optimal performance and prolong the life of the machine.
-
Double-Check Your Design: Before generating toolpaths and starting the milling process, carefully review your PCB design for any errors, such as incorrect trace widths, missing connections, or design rule violations.
-
Test and Iterate: After milling your PCB, test it thoroughly to ensure that it functions as intended. If issues are found, make necessary adjustments to your design and mill a new prototype until you achieve the desired results.
PCB Milling Applications
PCB milling is used in various applications, including:
-
Prototyping: PCB milling is an excellent choice for quickly creating prototypes of new PCB designs, allowing designers and engineers to test and validate their concepts before committing to mass production.
-
Low-Volume Production: For projects that require a small number of PCBs, such as custom electronics or limited-run products, PCB milling can be a cost-effective and efficient production method.
-
Education and Research: PCB milling is often used in educational settings, such as universities and makerspaces, to teach students about PCB design and manufacturing processes. It is also used in research labs for creating custom PCBs for experimental setups.
-
Hobby and DIY Projects: Hobbyists and DIY enthusiasts can use PCB milling to create custom PCBs for their projects, such as Arduino shields, sensor boards, or custom electronic devices.
-
RF and High-Frequency Applications: PCB milling can be used to create PCBs for radio frequency (RF) and high-frequency applications, as it allows for precise control over trace geometries and impedance matching.
Future of PCB Milling
As PCB milling technology continues to advance, we can expect to see improvements in several areas:
-
Increased Precision: Advancements in machine design, motion control systems, and milling bit technology will enable higher precision milling, allowing for finer trace widths and more complex PCB designs.
-
Faster Milling Speeds: Improvements in spindle technology and optimized toolpaths will lead to faster milling speeds, reducing the time required to mill PCBs and increasing production throughput.
-
Expanded Material Compatibility: Research and development in milling bit materials and machine capabilities will enable the milling of a wider range of substrate materials, including advanced composite materials and flexible substrates.
-
Integration with Additive Manufacturing: The combination of PCB milling with additive manufacturing techniques, such as 3D printing, will enable the creation of more complex, three-dimensional PCB structures and embedded electronics.
-
Automation and Intelligent Systems: The integration of artificial intelligence, computer vision, and automation technologies will lead to smarter, more efficient PCB milling systems that can adapt to changing design requirements and optimize the milling process in real-time.
As these advancements unfold, PCB milling will continue to play an essential role in PCB prototyping and low-volume production, while also finding new applications in emerging technologies and industries.
Frequently Asked Questions (FAQ)
1. What is the difference between PCB milling and PCB etching?
PCB milling is a subtractive process that removes copper from a copper-clad substrate using a milling machine or router to create the desired circuit pattern. In contrast, PCB etching is a chemical process that removes unwanted copper from the substrate using an etchant solution, leaving behind the desired circuit pattern defined by a photomask.
2. Can I use a regular CNC machine for PCB milling?
While it is possible to use a regular CNC machine for PCB milling, it is recommended to use a machine specifically designed for PCB milling. PCB milling machines typically have higher spindle speeds, more precise motion control, and are equipped with vacuum tables or other workholding solutions suitable for PCB substrates.
3. What is the minimum trace width and spacing achievable with PCB milling?
The minimum trace width and spacing achievable with PCB milling depend on several factors, such as the size of the milling bit, the precision of the milling machine, and the quality of the substrate material. Typically, desktop PCB milling machines can achieve trace widths and spacing down to around 0.2mm (8mil), while industrial-grade machines can achieve even finer resolutions.
4. How long does it take to mill a PCB?
The time required to mill a PCB depends on the complexity of the design, the size of the PCB, and the capabilities of the milling machine. Simple designs can be milled in a matter of minutes, while more complex designs with fine trace widths and intricate patterns may take several hours.
5. Can I use PCB milling for high-volume production?
PCB milling is generally not suitable for high-volume production due to its slower speed compared to etching and other mass production methods. It is best suited for prototyping and low-volume production runs. For high-volume production, methods like etching, or outsourcing to a professional PCB manufacturer, are more appropriate.
Conclusion
PCB milling is a versatile and accessible method for creating custom PCBs, offering several advantages over traditional PCB manufacturing processes. Its ability to quickly turn PCB designs into physical prototypes, combined with its low setup costs and design flexibility, makes it an essential tool for electronics designers, engineers, and hobbyists alike.
As PCB milling technology continues to evolve, we can expect to see improvements in precision, speed, and material compatibility, further expanding its applications and potential. By understanding the basics of PCB milling, selecting the right tools and software, and following best practices, anyone can harness the power of this innovative manufacturing process to bring their electronic ideas to life.
Leave a Reply