Types of PCB Materials
There are several types of PCB materials available, each with its own unique characteristics and benefits. The most common PCB materials include:
FR-4
FR-4 (Flame Retardant 4) is the most widely used PCB material. It is a composite material made of woven fiberglass cloth with an epoxy resin binder. FR-4 offers good mechanical strength, electrical insulation, and thermal stability. It is suitable for a wide range of applications, including consumer electronics, industrial control systems, and telecommunications equipment.
High-Frequency Materials
For applications that involve high-frequency signals, such as RF (Radio Frequency) and microwave circuits, specialized PCB materials are required. These materials have low dielectric constant and low loss tangent to minimize signal loss and distortion at high frequencies. Examples of high-frequency PCB materials include:
- Rogers RO4000 series
- Taconic TLX
- Isola IS680-280
Flexible PCB Materials
Flexible PCBs are designed to bend and flex without losing their electrical properties. They are commonly used in wearable devices, medical equipment, and aerospace applications. Flexible PCB materials include:
- Polyimide (PI)
- Polyester (PET)
- Flexible copper-clad laminates (FCCL)
Metal Core PCB Materials
Metal core PCBs (MCPCBs) are designed for applications that require efficient heat dissipation. They consist of a metal base layer, typically aluminum, with a thin layer of dielectric material and a copper circuit layer on top. MCPCBs are commonly used in high-power LED lighting, automotive electronics, and power electronics.
Properties of PCB Materials
When selecting a PCB material, several key properties need to be considered. These properties determine the performance and reliability of the PCB in various operating conditions.
Dielectric Constant (Dk)
The dielectric constant (Dk) is a measure of a material’s ability to store electrical energy. It represents the ratio of the permittivity of the material to the permittivity of vacuum. A lower Dk value indicates better signal integrity and reduced crosstalk between traces. Typical Dk values for common PCB materials are:
Material | Dielectric Constant (Dk) |
---|---|
FR-4 | 4.2 – 4.6 |
Rogers RO4350B | 3.48 |
Isola IS680-280 | 2.80 |
Dissipation Factor (Df)
The dissipation factor (Df), also known as loss tangent, represents the amount of energy lost as heat when an alternating electric field is applied to the material. A lower Df value indicates lower signal loss and better high-frequency performance. Typical Df values for common PCB materials are:
Material | Dissipation Factor (Df) |
---|---|
FR-4 | 0.02 |
Rogers RO4350B | 0.0037 |
Isola IS680-280 | 0.0028 |
Thermal Conductivity
Thermal conductivity is a measure of a material’s ability to conduct heat. It is an important property for PCBs that generate significant heat, such as power electronics or high-performance digital circuits. Materials with higher thermal conductivity can efficiently dissipate heat, preventing component overheating and improving reliability.
Material | Thermal Conductivity (W/mK) |
---|---|
FR-4 | 0.3 – 0.4 |
Aluminum (for MCPCBs) | 150 – 200 |
Copper (for thermal vias) | 385 |
Coefficient of Thermal Expansion (CTE)
The coefficient of thermal expansion (CTE) represents the amount of dimensional change a material undergoes when subjected to a change in temperature. It is important to consider CTE when designing PCBs, as mismatches in CTE between different materials can lead to mechanical stress and potential failure. PCB materials with similar CTE values to that of the components and solder joints are preferred to minimize thermal stress.
Material | CTE (ppm/°C) |
---|---|
FR-4 | 12 – 16 |
Copper | 17 |
Solder (SnPb) | 24 |
Mechanical Strength
PCB materials should have sufficient mechanical strength to withstand the stresses encountered during manufacturing, assembly, and operation. This includes resistance to bending, twisting, and vibration. FR-4 is known for its good mechanical strength, making it suitable for a wide range of applications.
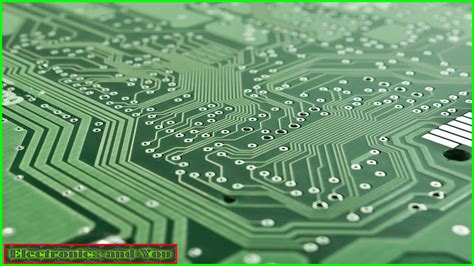
Manufacturing Considerations
When designing and manufacturing PCBs, several factors related to the PCB material need to be considered to ensure successful production and reliable performance.
Lamination Process
The lamination process involves bonding the copper foil to the base material under high temperature and pressure. The choice of lamination parameters, such as temperature, pressure, and duration, depends on the specific PCB material being used. Proper lamination ensures good adhesion between the layers and minimizes the risk of delamination.
Drilling and Routing
PCB materials have different drilling and routing characteristics. Some materials, such as high-frequency laminates, may be more brittle and prone to chipping or cracking during drilling. The choice of drill bits, feed rates, and speeds should be optimized based on the PCB material to achieve clean and accurate holes.
Solder Mask and Silkscreen
Solder mask and silkscreen are applied to the PCB surface to protect the copper traces and provide labeling and identification. The solder mask and silkscreen materials should be compatible with the base PCB material and have good adhesion to prevent peeling or flaking.
Surface Finish
The choice of surface finish, such as HASL (Hot Air Solder Leveling), ENIG (Electroless Nickel Immersion Gold), or OSP (Organic Solderability Preservative), depends on the PCB material and the intended application. The surface finish should provide good solderability, corrosion resistance, and compatibility with the assembly process.
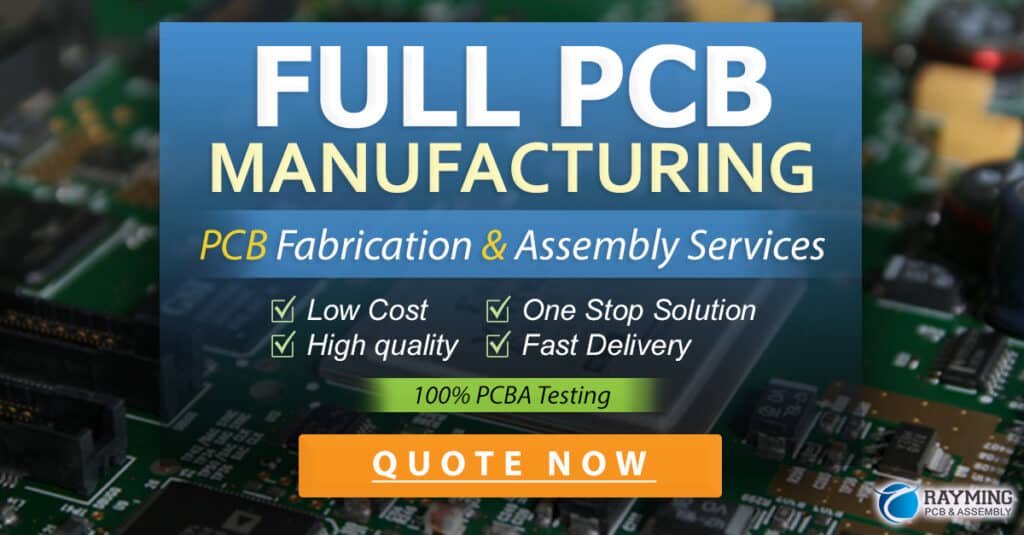
Environmental Considerations
PCB materials should also be evaluated based on their environmental impact and compliance with regulations.
RoHS Compliance
The Restriction of Hazardous Substances (RoHS) directive aims to limit the use of certain hazardous substances in electronic products. PCB materials used in RoHS-compliant products must meet the specified limits for restricted substances, such as lead, cadmium, and mercury.
Halogen-Free Materials
Some PCB materials, such as halogen-free FR-4 variants, are designed to reduce the environmental impact and improve fire safety. These materials do not contain halogens (chlorine and bromine) and release less toxic fumes in case of a fire.
Recyclability
The recyclability of PCB materials is becoming increasingly important as electronic waste continues to grow. Some PCB materials, such as aluminum-based MCPCBs, are more easily recyclable compared to traditional FR-4 laminates.
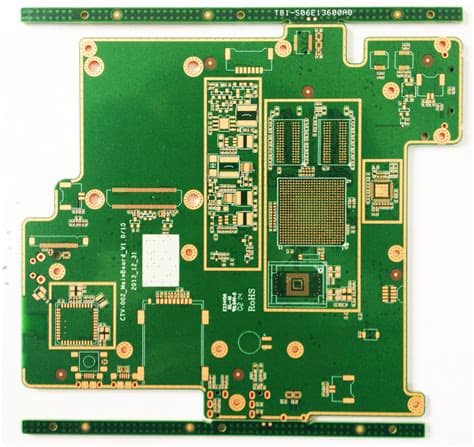
Frequently Asked Questions (FAQ)
- What is the most common PCB material?
- FR-4 is the most widely used PCB material due to its good balance of electrical, mechanical, and thermal properties, as well as its cost-effectiveness.
- What are high-frequency PCB materials used for?
- High-frequency PCB materials are used in applications that involve high-frequency signals, such as RF and microwave circuits. They have low dielectric constant and low loss tangent to minimize signal loss and distortion at high frequencies.
- What are the advantages of using flexible PCB materials?
- Flexible PCB materials allow for the design of bendable and flexible circuits, which are useful in applications such as wearable devices, medical equipment, and aerospace systems. They offer improved reliability and space savings compared to rigid PCBs.
- How does the dielectric constant affect PCB performance?
- The dielectric constant (Dk) of a PCB material influences signal integrity and crosstalk between traces. A lower Dk value indicates better signal integrity and reduced crosstalk, which is particularly important in high-speed and high-frequency applications.
- What should be considered when selecting a PCB material for a specific application?
- When selecting a PCB material, factors such as the operating frequency, environmental conditions, thermal requirements, mechanical stresses, and cost should be considered. The material’s properties, such as dielectric constant, dissipation factor, thermal conductivity, and CTE, should match the application’s requirements for optimal performance and reliability.
Conclusion
PCB materials play a critical role in the performance, reliability, and durability of electronic devices. Understanding the types of PCB materials, their properties, and manufacturing considerations is essential for designing and producing high-quality PCBs. From the widely used FR-4 to specialized high-frequency and flexible materials, the choice of PCB material depends on the specific application and its requirements. By carefully selecting the appropriate PCB material and considering environmental factors, designers and manufacturers can ensure the success of their electronic products.
Leave a Reply