Introduction to PCBs
A printed circuit board (PCB) is a board made of fiberglass or other rigid material used to mechanically support and electrically connect electronic components using conductive traces and pads. PCBs allow electrical components and circuits to be packed closely together without wires or cables between components. They provide the foundation for almost every modern electronic device.
Some key points about PCBs:
- PCBs provide the mechanical structure to mount and hold components
- Conductive copper traces on the PCB connect mounted components
- pcb layout involves carefully positioning components and routing traces
- Good PCB layout is crucial for electrical performance, manufacturing, and serviceability
Types of PCBs
There are several types of PCBs, differentiated by the number of conductive layers:
PCB Type | Number of Layers | Description |
---|---|---|
Single-sided | 1 | Conductive traces on one side only |
Double-sided | 2 | Conductive traces on both sides |
Multilayer | 3 or more | Alternating layers of fiberglass and copper traces |
HDI (High Density Interconnect) | Generally more than 6 | Very thin layers and trace spacing allowing high component density |
Flexible circuits | 1 or more | Flexible substrate material allowing bending and flexing |
What is PCB Layout?
PCB layout involves taking electronic circuits and physically designing a PCB to implement them. This includes:
- Positioning electronic components on the PCB
- Routing conductive copper traces to interconnect components
- Ensuring the layout meets design rules and manufacturability requirements
The end goal of PCB layout is creating fabrication data the pcb manufacturer can use to produce the bare boards.
Well executed PCB layout is critical to:
- Electrical performance
- Manufacturability
- Reliability and product lifecycle
- Unit cost and total cost
PCB Layout Stages
PCB layout for a new design usually progresses through several key stages:
Schematic Capture
A schematic diagram or schematic capture involves drawing electronic circuits using symbols to represent each component and lines to represent electrical connections between them. Schematic capture abstracts away physical form and focuses on electrical function.
Schematic diagram example (image source: researchgate.net)
The schematic drives many aspects of PCB layout and planning. Good schematic practices, like partitioning major functional blocks, helps PCB layout.
Board Planning
Before layout, critical planning helps avoid issues later:
- Partition schematic by functional blocks
- Determine board layer stackup (number of layers and their purposes)
- Create a board outline with connectors and major components placed
- Identify high-speed signals and bus routes
- Plan power distribution strategy early
Thorough planning makes actual layout faster and less problematic.
Placement
The placement stage involves mapping schematic components to physical footprints and ‘placing’ them on the board outline. Component placement has a profound impact on routing complexity, signal quality, EMI control, and manufacturability.
Goals for component placement typically include:
- Logical grouping by function
- Minimizing overall trace lengths
- Accessible testpoints
- Ease of assembly and servicing
Placement often iterates as layout progresses and issues emerge.
Routing
Routing creates conductive copper traces between the pinned connections of placed components. The main goals are completing all electrical connections while meeting:
- Electrical requirements – impedance, cross-talk, current capacity
- Manufacturing requirements – trace widths/spacing, via styles
- Signal integrity – minimizing length for high-speed signals
- EMI control – minimizing loop areas, return paths
Routing complexity scales up quickly with higher component densities and more layout layers.
Final Checks
Before manufacturing PCB layouts, final checks help avoid costly mistakes:
- Electrical rule checking (ERC) – confirm no missing connections
- Design rule checking (DRC) – confirm manufacturing requirements are met
- Generate manufacturing/assembly files – Gerbers, drill data, pick-and-place, etc.
Iterating layout to fix any issues found improves quality and avoidability.
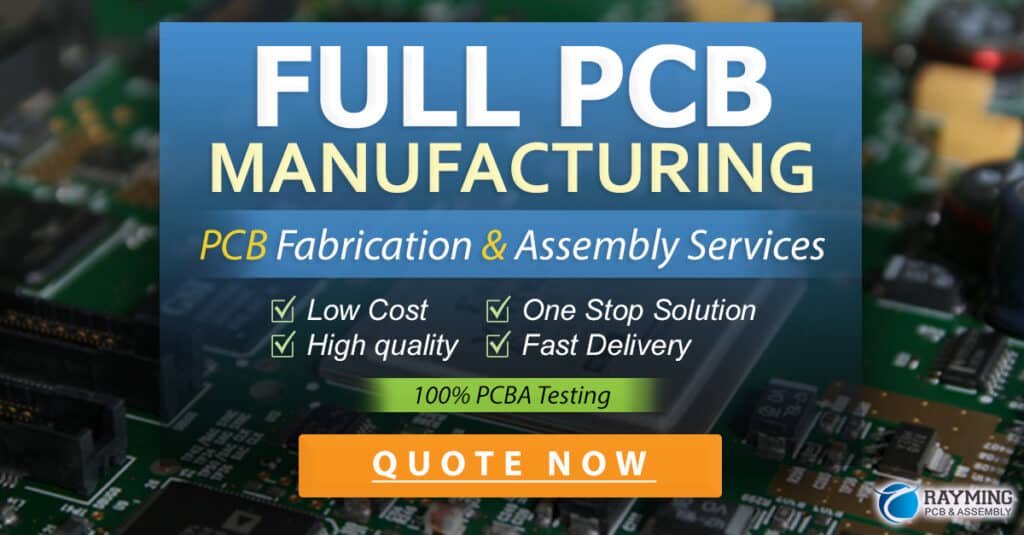
PCB Layout Tools
PCB layout leverages electronic design automation (EDA) software tools for planning, placement, and routing. Many options exist ranging from free to extremely advanced professional tools.
Some examples of PCB layout EDA tools:
Tool | Description |
---|---|
Eagle | Popular lower-cost tool for simpler designs |
KiCad | Full-featured open-source layout tool |
Altium | Advanced professional tool for complex designs |
Pads | Full-featured mid-range cost tool |
OrCAD | Long-time cost-effective tool with extensive features |
Key criteria when selecting PCB layout tools include:
- Supported design complexity (2 layer to high-density, HDI, etc)
- Library availability
- Integration of schematic-board-3D environment
- Design rule awareness and assistance
- Automation capabilities
- Output: Gerbers, manufacturing files, etc.
- Pricing model
Using tools purpose-built for PCB layout greatly improves designer productivity and layout quality.
Role of the PCB Layout Engineer
PCB layout engineers leverage specialized EDA software tools to transform electronic circuit schematics into routed board layouts ready for manufacturing.
Being a PCB layout engineer requires an overlapping skill set including:
- Electronic design skills – reading/understanding schematics, attention to signal/power integrity
- PCB manufacturing process knowledge – design rules, capabilities and limitations
- Library management – obtaining, creating and organizing device symbols and footprints
- Mechanical design understanding – enclosure integration, thermals, tolerance stacks
- Communication skills – collaborating with electrical engineers, mechanical engineers, manufacturers
- Organizational skills – navigating complexity by partitioning effectively
- Time/Project management abilities – budget time properly over long layout projects
Good PCB layout engineers can significant improve a design’s performance, reliability, manufacturability, and cost profile. They play a vital role in transforming electronic innovations into manufacturable and testable products.
Significance of Good PCB Layout
Far from being just “connecting the dots”, excellent PCB layout exemplifies a skillful balancing of competing electrical and physical demands.
Benefits of good PCB layout work include:
Electrical Performance
- Minimized high-speed trace lengths
- Controlled impedance for signals
- Careful plane management for controlled impedance references
- Minimized ground loops, return loss and EMI
Manufacturability
- Higher yielding PCB panel utilization
- PCB manufacturer compatible trace geometries
- Easy visual inspection of solder joints
Reliability
- Accessible testpoints to validate operation
- Sufficient cooling air paths for heat generating components
- Avoidance of thermally incompatible component placements
- Careful routing of high-current traces
Project Schedule
- Thoughtful planning reducing iteration cycles
- Partitioning facilitating work distribution
- Effective organization and naming
Product Cost Savings
- Area utilization increasing PCB panel yield
- Simplified assembly steps with placement choices
- Serviceability considerations
For high-volume and complex designs, the cost of additional PCB layout effort pays for itself many times over through increased performance, manufacturability, and simplified assembly.
PCB Layout – Frequently Asked Questions
Here are answers to some common questions about PCB layout:
What are the most important things to focus on in PCB layout?
Some top priorities in PCB layout include: meeting design rules for manufacturability, minimizing trace lengths for high-speed signals, effective power distribution, grouping components logically, allowing sufficient cooling paths, ensuring testpoints can access key nodes.
What software tools are used for PCB layout?
Common software tools used for PCB layout work include: Eagle pcb design software, KiCad, Altium Designer, Cadence Allegro and OrCAD PCB Designer, Mentor Graphics PADS. There are a range of options from free tools to advanced professional solutions.
How long does it take to layout a PCB board?
The time required to layout a PCB design depends greatly on the complexity factors like: component density, number of layout layers, manufacturing tolerances, electrical constraints, etc. Simpler 2 layer boards may require just days while complex designs with high-speed signals or HDI layers can take many weeks.
What background is required to get into PCB layout?
The ideal background before getting into PCB layout includes: electrical engineering education with circuit design experience, knowledge of PCB manufacturing and tolerances, experience with analog and digital circuits, using EDA tools, collaborating on multi-disciplinary engineering teams.
How detailed should component footprints be in the library?
Component footprints model the exact physical interface and tolerances for mounting and soldering that component. Details like pad sizes, drill holes, device outlines, silkscreen, etc. must match both the datasheet recommendations and PCB manufacturing capabilities being targeted. Library quality is vital.
Leave a Reply