Understanding PCB Quality
Printed Circuit boards (PCBs) are the backbone of modern electronics. They are used in almost every electronic device, from smartphones and computers to industrial equipment and medical devices. The quality of a PCB directly impacts the performance, reliability, and longevity of the electronic device it is used in. Therefore, ensuring high PCB quality is crucial for manufacturers and consumers alike.
What is a PCB?
A PCB is a flat board made of insulating materials, such as fiberglass or plastic, with conductive pathways etched or printed onto its surface. These pathways, also known as traces, connect various electronic components, such as resistors, capacitors, and integrated circuits (ICs), to form a complete electronic circuit.
PCBs come in various types, depending on their construction and the number of layers they contain:
PCB Type | Description |
---|---|
Single-layer | A PCB with conductive traces on one side only |
Double-layer | A PCB with conductive traces on both sides |
Multi-layer | A PCB with multiple layers of conductive traces separated by insulating layers |
Flexible | A PCB made of flexible materials, allowing it to bend and flex |
Rigid-Flex | A combination of rigid and flexible PCBs, offering both stability and flexibility |
Factors Affecting PCB Quality
Several factors contribute to the overall quality of a PCB. These include:
-
Material selection: The choice of materials used in PCB fabrication, such as the substrate, copper foil, and solder mask, can significantly impact the board’s performance and durability.
-
Design and layout: A well-designed PCB layout ensures optimal signal integrity, minimizes electromagnetic interference (EMI), and reduces the risk of manufacturing defects.
-
Manufacturing process: The quality of the PCB manufacturing process, including etching, drilling, plating, and soldering, directly affects the board’s reliability and functionality.
-
Quality control: Stringent quality control measures, such as visual inspections, electrical testing, and environmental testing, help identify and eliminate defects before the PCBs are assembled into electronic devices.
PCB Quality Standards and Certifications
To ensure consistent PCB quality across the industry, various standards and certifications have been developed. These include:
IPC Standards
The Association Connecting Electronics Industries (IPC) is a global trade association that develops standards for the electronic interconnect industry. Some of the key IPC standards related to PCB quality include:
Standard | Description |
---|---|
IPC-A-600 | Acceptability of Printed Boards |
IPC-6011 | Generic Performance Specification for Printed Boards |
IPC-6012 | Qualification and Performance Specification for Rigid Printed Boards |
IPC-6013 | Qualification and Performance Specification for Flexible Printed Boards |
IPC-6018 | Microwave End Product Board Inspection and Test |
These standards provide guidelines for PCB fabrication, assembly, and testing, ensuring consistent quality across manufacturers.
ISO Certifications
The International Organization for Standardization (ISO) develops and publishes standards for various industries, including electronics. Some of the relevant ISO certifications for PCB manufacturers include:
Certification | Description |
---|---|
ISO 9001 | Quality Management Systems |
ISO 14001 | Environmental Management Systems |
ISO 45001 | Occupational Health and Safety Management Systems |
PCB manufacturers with these certifications demonstrate their commitment to quality, environmental responsibility, and employee safety.
UL Certification
Underwriters Laboratories (UL) is a global safety certification company that tests and certifies products, including PCBs, for safety and performance. UL certification ensures that PCBs meet specific safety and quality standards, which is particularly important for applications in industries such as automotive, medical, and aerospace.
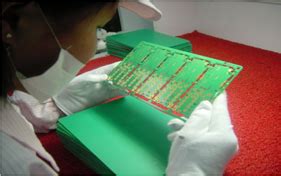
PCB Quality Inspection Techniques
To maintain high PCB quality, manufacturers employ various inspection techniques throughout the fabrication process. Some common inspection methods include:
Visual Inspection
Visual inspection is the most basic form of PCB quality control. Trained inspectors examine the boards for visible defects, such as scratches, dents, and discoloration, using magnifying lenses or microscopes.
Automated Optical Inspection (AOI)
AOI systems use high-resolution cameras and advanced image processing algorithms to detect surface-level defects, such as missing components, incorrect component placement, and solder bridging. AOI is faster and more consistent than manual visual inspection.
X-Ray Inspection
X-ray inspection is used to detect internal defects in PCBs, such as voids in solder joints, broken traces, and delamination. This non-destructive testing method is particularly useful for inspecting multi-layer boards and ball grid array (BGA) packages.
Electrical Testing
Electrical testing verifies the functionality and performance of a PCB by measuring various electrical parameters, such as continuity, insulation resistance, and dielectric strength. Common electrical testing methods include:
Method | Description |
---|---|
Flying Probe Testing | A non-contact testing method that uses movable probes to test individual points on the PCB |
In-Circuit Testing (ICT) | A bed-of-nails testing method that uses a custom fixture to test the PCB’s components and interconnections |
Functional Testing | A test that verifies the overall functionality of the assembled PCB by simulating its intended application |
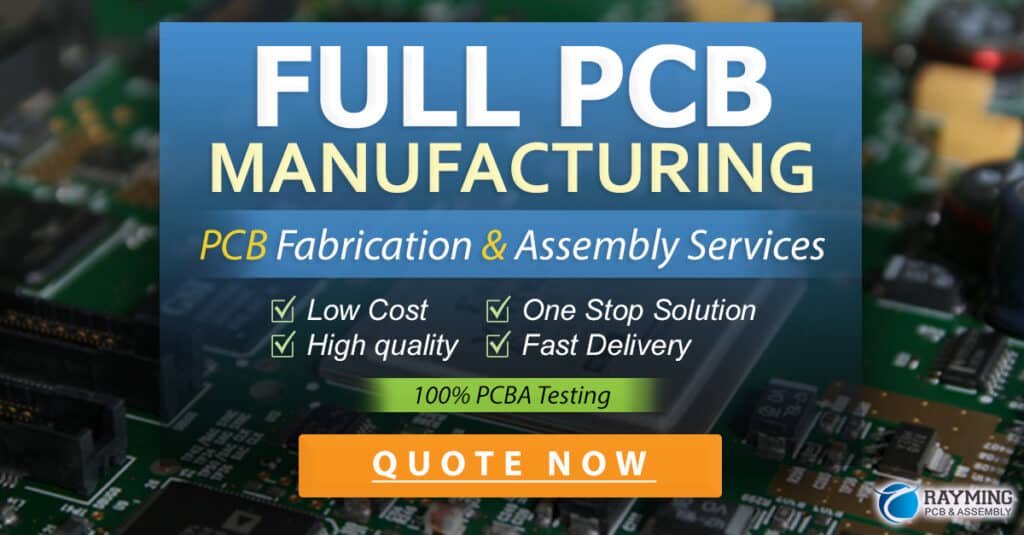
Benefits of High PCB Quality
Investing in high-quality PCBs offers numerous benefits for both manufacturers and end-users, including:
-
Improved reliability: High-quality PCBs are less likely to fail or malfunction, resulting in more reliable electronic devices and reduced warranty claims.
-
Enhanced performance: Well-designed and manufactured PCBs offer better signal integrity, lower EMI, and improved thermal management, leading to enhanced overall device performance.
-
Longer product lifespan: High-quality PCBs are more durable and resistant to environmental stresses, such as temperature fluctuations, vibrations, and moisture, extending the lifespan of the electronic devices they are used in.
-
Cost savings: While high-quality PCBs may have a higher initial cost, they can lead to significant long-term cost savings by reducing the need for repairs, replacements, and product recalls.
-
Competitive advantage: Manufacturers who consistently produce high-quality PCBs can differentiate themselves in the market, attracting more customers and building a strong reputation for quality and reliability.
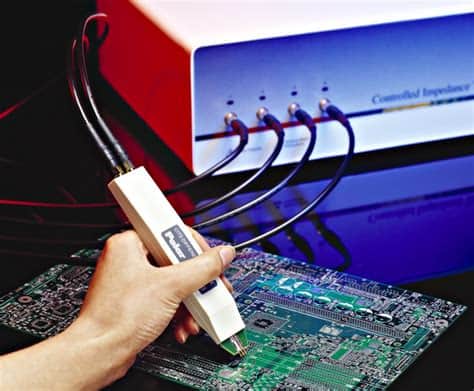
Frequently Asked Questions (FAQ)
-
Q: What is the difference between a single-layer and a multi-layer PCB?
A: A single-layer PCB has conductive traces on one side only, while a multi-layer PCB has multiple layers of conductive traces separated by insulating layers. Multi-layer PCBs offer higher component density and better signal integrity compared to single-layer PCBs. -
Q: Why is PCB quality important for electronic devices?
A: PCB quality directly impacts the performance, reliability, and longevity of electronic devices. High-quality PCBs ensure better signal integrity, lower EMI, and improved durability, resulting in more reliable and better-performing devices. -
Q: What are some common PCB defects?
A: Common PCB defects include missing or incorrect components, solder bridging, cold solder joints, trace damage, and delamination. These defects can lead to device malfunctions and failures. -
Q: How can manufacturers ensure high PCB quality?
A: Manufacturers can ensure high PCB quality by implementing stringent quality control measures, such as visual inspections, automated optical inspection (AOI), X-ray inspection, and electrical testing. Adhering to industry standards and obtaining relevant certifications also helps maintain consistent quality. -
Q: What should I look for when choosing a PCB manufacturer?
A: When choosing a PCB manufacturer, look for a company with a proven track record of producing high-quality PCBs, as well as relevant industry certifications, such as ISO 9001, ISO 14001, and UL certification. Additionally, consider factors such as the manufacturer’s experience, capabilities, and customer support.
In conclusion, PCB quality is a critical factor in the performance and reliability of electronic devices. By understanding the factors that affect PCB quality, adhering to industry standards, and implementing rigorous quality control measures, manufacturers can produce high-quality PCBs that meet the demands of today’s increasingly complex electronic systems. As a consumer or business, investing in high-quality PCBs can lead to improved device performance, longer product lifespan, and significant cost savings in the long run.
Leave a Reply