What are Medical Devices?
Medical devices are instruments, apparatus, machines, implants, or other articles intended for use in the diagnosis, prevention, monitoring, treatment, or alleviation of disease or injury in humans or animals. They range from simple devices like thermometers and stethoscopes to complex systems such as MRI machines, pacemakers, and robotic surgical equipment.
The medical device industry is highly regulated to ensure patient safety and device effectiveness. In the United States, the Food and Drug Administration (FDA) classifies medical devices into three categories based on their risk level:
Class | Risk Level | Examples |
---|---|---|
I | Low | Bandages, tongue depressors, hand-held surgical instruments |
II | Moderate | Infusion pumps, surgical drapes, powered wheelchairs |
III | High | Pacemakers, implantable defibrillators, heart valves |
PCBs are found in many of these devices, particularly those with electronic components or sensing capabilities.
The Role of PCBs in Medical Devices
PCBs serve as the backbone of electronic medical devices, providing the interconnections and circuitry necessary for the device to function. They are responsible for:
-
Signal processing: PCBs route and process electrical signals from sensors, inputs, and other components to enable device functionality.
-
Power distribution: PCBs distribute power to the various components of the medical device, ensuring each part receives the appropriate voltage and current.
-
Component integration: PCBs provide a platform for mounting and interconnecting electronic components such as microprocessors, sensors, displays, and communication modules.
-
Miniaturization: PCBs enable the design of compact, portable, and implantable medical devices by allowing for high-density component placement and interconnections.
-
Reliability: Well-designed and manufactured PCBs contribute to the overall reliability and durability of medical devices, which is critical for patient safety and device longevity.
Examples of Medical Devices with PCBs
PCBs are found in a wide range of medical devices, including:
- Patient monitors (e.g., ECG, EEG, pulse oximeters)
- Diagnostic imaging equipment (e.g., X-ray, ultrasound, CT scanners)
- Infusion pumps and drug delivery systems
- Surgical instruments and robotics
- Implantable devices (e.g., pacemakers, neurostimulators, cochlear implants)
- Wearable devices (e.g., fitness trackers, continuous glucose monitors)
- Laboratory equipment (e.g., blood analyzers, DNA sequencers)
Requirements for medical pcb Assembly
Medical PCB assembly involves unique challenges and requirements due to the critical nature of the devices and the stringent regulations governing the industry. Some of the key requirements for medical PCB assembly include:
Reliability and Durability
Medical devices must function reliably and consistently to ensure patient safety and effective treatment. PCBs in these devices must be designed and manufactured to withstand the expected environmental conditions, such as temperature, humidity, and vibration, as well as the anticipated product lifespan.
Regulatory Compliance
Medical device manufacturers must comply with various regulations and standards to ensure product safety and effectiveness. Some of the key standards relevant to medical PCB assembly include:
- ISO 13485: Quality management systems for medical devices
- IEC 60601: Safety and performance standards for medical electrical equipment
- FDA 21 CFR Part 820: Quality System Regulation for medical devices in the United States
- RoHS (Restriction of Hazardous Substances) and REACH (Registration, Evaluation, Authorization, and Restriction of Chemicals) compliance for environmental safety
Cleanliness and Contamination Control
Medical PCBs must be assembled in a clean environment to minimize the risk of contamination, which could compromise device performance or patient safety. This typically involves the use of cleanrooms, specialized cleaning processes, and strict handling protocols.
Traceability and Documentation
Medical device manufacturers must maintain detailed records of the materials, processes, and tests involved in PCB assembly to ensure traceability and facilitate root cause analysis in case of device failures or recalls. This documentation is also essential for regulatory compliance and audits.
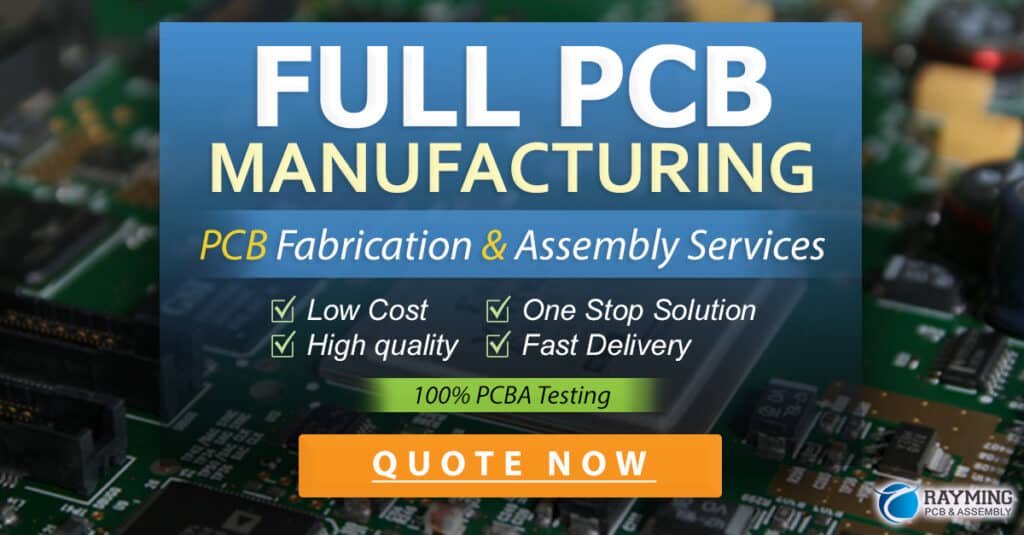
Challenges in Medical PCB Assembly
Designing and manufacturing PCBs for medical devices presents several unique challenges, including:
-
High reliability requirements: Medical PCBs must be designed and manufactured to extremely high reliability standards to ensure patient safety and device effectiveness.
-
Miniaturization and high-density assembly: Many medical devices require compact, high-density PCB designs to enable portability, implantability, or integration with other components.
-
Regulatory compliance: Navigating the complex web of regulations and standards governing medical devices can be challenging and time-consuming.
-
Rapid technological advancements: The medical device industry is constantly evolving, with new technologies and materials being developed at a rapid pace. PCB designers and manufacturers must stay up-to-date with these advancements to remain competitive.
-
Cost pressures: Despite the high-reliability requirements and regulatory hurdles, medical device manufacturers face pressure to control costs and maintain profitability.
Best Practices for Medical PCB Assembly
To overcome these challenges and ensure the successful design and manufacture of medical PCBs, consider the following best practices:
-
Engage experienced PCB design and manufacturing partners: Work with PCB design firms and contract manufacturers who have a proven track record in the medical device industry and are familiar with the relevant regulations and standards.
-
Implement a robust quality management system: Establish and maintain a comprehensive quality management system that covers all aspects of PCB design, manufacture, and testing to ensure consistency, reliability, and regulatory compliance.
-
Conduct thorough testing and validation: Perform rigorous testing and validation at various stages of the PCB assembly process, including incoming material inspection, in-circuit testing, functional testing, and environmental testing.
-
Utilize advanced manufacturing technologies: Leverage advanced PCB manufacturing technologies, such as 3D printing, embedded components, and flexible circuits, to enable miniaturization, improve reliability, and reduce costs.
-
Foster collaboration and communication: Encourage open communication and collaboration among PCB designers, manufacturers, and other stakeholders to identify potential issues early, streamline the development process, and ensure a successful outcome.
Frequently Asked Questions (FAQ)
1. What is the difference between medical PCBs and standard PCBs?
Medical PCBs are designed and manufactured to meet the unique requirements of the medical device industry, such as high reliability, regulatory compliance, and cleanliness standards. Standard PCBs may not be subject to the same rigorous requirements and may not be suitable for use in medical devices.
2. How long does it take to design and manufacture a medical PCB?
The time required to design and manufacture a medical PCB can vary widely depending on the complexity of the design, the regulatory requirements, and the manufacturing process. Simple designs may take a few weeks, while complex, highly regulated devices can take several months or even years to develop and bring to market.
3. What certifications should a medical PCB assembly partner have?
A medical PCB assembly partner should have certifications demonstrating their compliance with relevant quality management and regulatory standards, such as ISO 13485, ISO 9001, and IPC standards for PCB manufacturing. They should also have experience working with medical device manufacturers and be familiar with the unique requirements of the industry.
4. How can I ensure the reliability of my medical PCB?
To ensure the reliability of your medical PCB, work with experienced design and manufacturing partners, implement a robust quality management system, conduct thorough testing and validation, and utilize advanced manufacturing technologies where appropriate. Regularly review and update your design and manufacturing processes to identify opportunities for improvement.
5. What should I consider when selecting materials for my medical PCB?
When selecting materials for your medical PCB, consider factors such as biocompatibility, durability, thermal stability, and electrical performance. Work with your PCB design and manufacturing partners to select materials that meet the specific requirements of your device and comply with relevant regulations and standards.
Conclusion
PCBs play a critical role in the functionality, reliability, and safety of medical devices. Designing and manufacturing PCBs for the medical industry involves unique challenges and requirements, including high reliability standards, regulatory compliance, and cleanliness controls.
By understanding these challenges and implementing best practices such as engaging experienced partners, implementing robust quality management systems, and conducting thorough testing and validation, medical device manufacturers can ensure the successful development and production of high-quality, safe, and effective PCBs for their devices.
As the medical device industry continues to evolve and advance, PCB designers and manufacturers must stay at the forefront of technological developments to meet the ever-increasing demands for miniaturization, reliability, and cost-effectiveness. By fostering collaboration, innovation, and a commitment to quality, the medical PCB assembly industry can continue to support the development of life-saving and life-enhancing medical devices for patients around the world.
Leave a Reply