Understanding PCB and BMS
What is a PCB?
A Printed Circuit Board (PCB) is a fundamental component in modern electronic devices. It is a flat board made of insulating material, typically fiberglass or composite epoxy, with conductive pathways etched or printed onto its surface. These pathways, also known as traces, connect various electronic components such as resistors, capacitors, and integrated circuits, allowing them to function as a complete electronic system.
PCBs offer several advantages over traditional point-to-point wiring:
- Compact design: PCBs allow for a more compact and organized layout of electronic components, reducing the overall size of the device.
- Reliability: The use of PCBs minimizes the risk of loose connections and short circuits, improving the reliability of the electronic system.
- Mass production: PCBs are designed for automated assembly, making mass production of electronic devices more efficient and cost-effective.
What is a BMS?
A Battery Management System (BMS) is an electronic system that monitors and manages the performance of a rechargeable battery pack. It is designed to ensure the safe and efficient operation of the battery by monitoring various parameters such as voltage, current, and temperature. The primary functions of a BMS include:
- Overcharge protection: The BMS prevents the battery from being charged beyond its maximum voltage limit, which can cause damage or even fire.
- Overdischarge protection: The BMS ensures that the battery is not discharged below its minimum voltage limit, which can lead to permanent damage.
- Temperature monitoring: The BMS monitors the temperature of the battery pack and takes appropriate actions, such as reducing the charging current or shutting down the system, if the temperature exceeds safe limits.
- State of Charge (SoC) estimation: The BMS calculates the remaining capacity of the battery pack, allowing the user to estimate the remaining runtime of the device.
- Cell balancing: In multi-cell battery packs, the BMS ensures that all cells are at the same voltage level, maximizing the overall capacity and lifespan of the pack.
The Role of PCB in BMS
PCB Design for BMS
The PCB is a critical component in the design and implementation of a BMS. It serves as the physical platform on which the various electronic components of the BMS are mounted and interconnected. The PCB design for a BMS must take into account several factors:
- Component selection: The PCB must accommodate the specific components required for the BMS, such as voltage and current sensors, temperature sensors, and microcontrollers.
- Layout optimization: The placement of components on the PCB should be optimized to minimize the length of traces, reduce electromagnetic interference (EMI), and ensure proper heat dissipation.
- Signal integrity: The PCB layout must ensure that the signals transmitted between components maintain their integrity, minimizing noise and distortion.
- Power management: The PCB must be designed to handle the power requirements of the BMS, including the provision of appropriate power planes and ground planes.
BMS PCB Assembly
Once the PCB design is finalized, the next step is to assemble the components onto the board. This process typically involves the following steps:
- Solder paste application: A thin layer of solder paste is applied to the pads on the PCB where the components will be placed.
- Component placement: The electronic components are placed onto the PCB using automated pick-and-place machines or manual placement for smaller batches.
- Reflow soldering: The PCB with the placed components is passed through a reflow oven, which melts the solder paste and creates a permanent electrical and mechanical connection between the components and the PCB.
- Inspection and testing: The assembled PCB is inspected visually and tested electrically to ensure proper functionality and adherence to quality standards.
BMS PCB Testing and Validation
Before a BMS PCB can be integrated into a final product, it must undergo thorough testing and validation to ensure its reliability and performance. This process typically involves the following steps:
- Functional testing: The BMS PCB is subjected to various functional tests to verify that it performs all the required tasks, such as voltage and current monitoring, temperature sensing, and cell balancing.
- Environmental testing: The PCB is exposed to different environmental conditions, such as temperature extremes, humidity, and vibration, to ensure that it can operate reliably in the intended application.
- EMC testing: Electromagnetic Compatibility (EMC) testing is performed to ensure that the BMS PCB does not generate excessive electromagnetic interference and can function properly in the presence of external electromagnetic fields.
- Safety testing: The BMS PCB is tested to ensure compliance with relevant safety standards, such as UL or IEC, to minimize the risk of fire or electrical hazards.
BMS PCB Applications
Electric Vehicles
One of the most prominent applications of BMS PCBs is in electric vehicles (EVs). EVs rely on large, high-voltage battery packs to power their motors, and a robust BMS is essential to ensure the safe and efficient operation of these packs. The BMS PCB in an EV is responsible for:
- Monitoring the voltage and current of each individual cell in the battery pack.
- Balancing the cells to ensure that they all have the same state of charge, maximizing the pack’s overall capacity and lifespan.
- Protecting the battery pack from overcharge, overdischarge, and thermal runaway.
- Communicating with the vehicle’s onboard computer to provide information about the battery pack’s state of health and remaining range.
Parameter | Typical Value |
---|---|
Battery Pack Voltage | 300-800 V |
Number of Cells in Series | 96-200 |
Cell Chemistry | Lithium-ion (NMC, LFP) |
BMS PCB Dimensions | 200 x 150 x 50 mm |
Operating Temperature Range | -40°C to +85°C |
Energy Storage Systems
BMS PCBs are also used in stationary energy storage systems, such as those found in residential or commercial solar power installations. These systems typically use large battery packs to store excess energy generated by solar panels during the day, allowing it to be used during periods of low or no sunlight. The BMS PCB in an energy storage system is responsible for:
- Monitoring the voltage, current, and temperature of the battery pack.
- Protecting the battery pack from overcharge, overdischarge, and thermal runaway.
- Estimating the state of charge and state of health of the battery pack.
- Communicating with the system’s inverter and control electronics to optimize the charging and discharging of the battery pack.
Parameter | Typical Value |
---|---|
Battery Pack Voltage | 48-1000 V |
Number of Cells in Series | 16-200 |
Cell Chemistry | Lithium-ion (LFP, NMC), Lead-Acid |
BMS PCB Dimensions | 300 x 200 x 100 mm |
Operating Temperature Range | -20°C to +60°C |
Portable Electronics
BMS PCBs are found in a wide range of portable electronic devices, such as smartphones, tablets, and laptops. In these applications, the BMS PCB is typically integrated into the device’s main PCB and is responsible for:
- Monitoring the voltage and current of the device’s battery.
- Protecting the battery from overcharge, overdischarge, and short-circuit conditions.
- Estimating the battery’s state of charge and communicating this information to the device’s operating system.
- Managing the charging process to ensure optimal battery health and lifespan.
Parameter | Typical Value |
---|---|
Battery Voltage | 3.7-7.4 V |
Number of Cells in Series | 1-2 |
Cell Chemistry | Lithium-ion (LCO, NMC) |
BMS PCB Dimensions | 20 x 20 x 5 mm |
Operating Temperature Range | 0°C to +45°C |
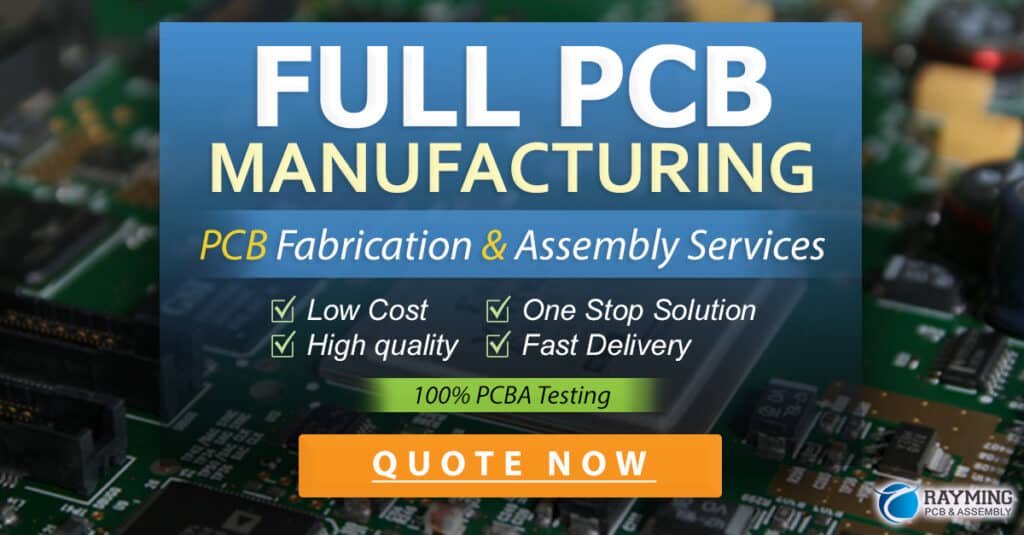
Frequently Asked Questions (FAQ)
1. What is the difference between a BMS and a battery charger?
A battery charger is a device that supplies electrical energy to a battery, allowing it to be recharged. A BMS, on the other hand, is a more comprehensive system that not only manages the charging process but also monitors the battery’s performance, protects it from unsafe conditions, and estimates its state of charge and health.
2. Can a BMS be used with different battery chemistries?
Yes, BMS PCBs can be designed to work with various battery chemistries, such as lithium-ion, lead-acid, and nickel-metal hydride. However, the specific design and configuration of the BMS will depend on the characteristics and requirements of the chosen battery chemistry.
3. How does a BMS estimate the state of charge of a battery?
A BMS typically estimates the state of charge of a battery using one or more of the following methods:
- Coulomb counting: This method involves measuring the current flowing into and out of the battery over time and integrating it to determine the change in the battery’s charge.
- Voltage measurement: The BMS can estimate the state of charge by measuring the battery’s voltage and comparing it to a known voltage-to-charge relationship for the specific battery chemistry.
- Kalman filtering: This is a more advanced method that combines coulomb counting and voltage measurement with a mathematical model of the battery to provide a more accurate estimate of the state of charge.
4. What is cell balancing, and why is it important?
Cell balancing is the process of equalizing the state of charge of individual cells in a multi-cell battery pack. This is important because cells in a pack may have slightly different capacities and self-discharge rates, which can lead to imbalances over time. If left unchecked, these imbalances can reduce the overall capacity and lifespan of the battery pack. A BMS with cell balancing capabilities can actively transfer charge from cells with higher voltages to those with lower voltages, ensuring that all cells remain at the same state of charge.
5. How does a BMS protect a battery from overcharge and overdischarge?
A BMS protects a battery from overcharge and overdischarge by continually monitoring the voltage of each cell in the pack. If the voltage of any cell exceeds the maximum safe limit during charging, the BMS will take action to stop or reduce the charging current to prevent damage to the cell. Similarly, if the voltage of any cell drops below the minimum safe limit during discharging, the BMS will disconnect the load to prevent further discharge and potential damage to the cell.
Conclusion
PCB plays a crucial role in the design and implementation of Battery Management Systems (BMS). The BMS PCB serves as the physical platform on which the various electronic components are mounted and interconnected, enabling the system to monitor and manage the performance of rechargeable battery packs. From electric vehicles and energy storage systems to portable electronics, BMS PCBs are essential for ensuring the safe, efficient, and reliable operation of battery-powered devices. As battery technologies continue to advance, the importance of well-designed and thoroughly tested BMS PCBs will only continue to grow.
Leave a Reply