The Importance of PCBs in Aerospace
PCBs are the backbone of modern electronic systems, providing the interconnections and support for electronic components such as integrated circuits, resistors, capacitors, and connectors. In the aerospace industry, PCBs are used in a wide range of applications, including:
- Avionics systems
- Navigation and communication equipment
- Flight control systems
- Engine control units
- Sensor systems
- Radar and surveillance systems
- Satellite systems
The reliability and performance of these electronic systems are critical to the safety and success of aerospace missions. PCBs must be designed and manufactured to withstand extreme temperatures, vibrations, shocks, and exposure to radiation and vacuum conditions. Failure of a PCB in an aerospace application can have catastrophic consequences, making aerospace PCB assembly a highly specialized and demanding field.
Challenges in Aerospace PCB Assembly
Aerospace PCB assembly faces several unique challenges compared to PCB assembly for other industries. Some of the key challenges include:
Harsh Environmental Conditions
Aerospace PCBs must operate reliably in extreme environmental conditions, including:
- Wide temperature ranges (-55°C to +125°C)
- High levels of vibration and shock
- Exposure to radiation and vacuum conditions
- Exposure to moisture and corrosive agents
To withstand these conditions, aerospace PCBs must be designed with robust materials, such as high-temperature laminates, and use specialized components and assembly techniques.
Miniaturization and High Density
As aerospace systems become more complex and compact, there is a growing demand for miniaturized and high-density PCBs. This requires the use of advanced PCB design techniques, such as:
- High-density interconnect (HDI) technology
- Embedded components
- Blind and buried vias
- Fine-pitch components
These techniques allow for the integration of more functionality into smaller PCB form factors, reducing weight and volume, which is critical in aerospace applications.
Reliability and Quality Control
Aerospace PCBs must meet stringent reliability and quality control requirements to ensure the safety and success of aerospace missions. This involves:
- Rigorous testing and qualification processes
- Adherence to industry standards and certifications (e.g., IPC Class 3, AS9100)
- Traceability and documentation of materials and processes
- Specialized inspection and testing techniques (e.g., X-ray, thermal cycling)
Aerospace PCB assembly providers must have robust quality management systems in place to ensure consistent and reliable production of high-quality PCBs.
Advanced Technologies in Aerospace PCB Assembly
To meet the challenges of aerospace PCB assembly, manufacturers employ a range of advanced technologies and techniques, including:
High-Temperature Materials
Aerospace PCBs use high-temperature laminates and solder masks to withstand the extreme temperature ranges encountered in aerospace applications. Some commonly used high-temperature materials include:
- Polyimide (PI) laminates
- Liquid crystalline polymer (LCP) laminates
- High-temperature solder masks
These materials provide excellent thermal stability, mechanical strength, and chemical resistance, ensuring reliable performance in harsh environments.
Embedded Components
Embedded component technology involves integrating passive components, such as resistors and capacitors, within the layers of a PCB. This technique offers several advantages for aerospace PCBs, including:
- Reduced PCB size and weight
- Improved signal integrity and reduced parasitic effects
- Enhanced thermal management
- Increased reliability and resistance to vibration and shock
Embedded components are particularly useful in high-density aerospace PCBs, where space is at a premium.
Advanced Interconnect Technologies
Aerospace PCBs use advanced interconnect technologies to achieve high-density interconnections and improve signal integrity. Some examples include:
- High-density interconnect (HDI) technology: Uses micro-vias and fine-pitch traces to achieve high interconnect density
- Rigid-flex PCBs: Combines rigid and flexible PCB sections to enable 3D packaging and improve reliability in dynamic environments
- Embedded trace technology: Uses traces embedded within the PCB layers to reduce crosstalk and improve signal integrity
These technologies enable the development of compact, high-performance aerospace PCBs that can reliably operate in demanding environments.
Additive Manufacturing
Additive manufacturing, also known as 3D printing, is an emerging technology that holds promise for aerospace PCB assembly. Additive manufacturing techniques, such as inkjet printing and aerosol jet printing, can be used to directly deposit conductive traces and components onto PCB substrates. This offers several potential benefits, including:
- Rapid prototyping and customization
- Reduced material waste and environmental impact
- Ability to create complex 3D structures and non-planar PCBs
- Integration of multiple materials and functionalities
While additive manufacturing is still in the early stages of adoption for aerospace PCBs, it has the potential to revolutionize PCB design and assembly in the future.
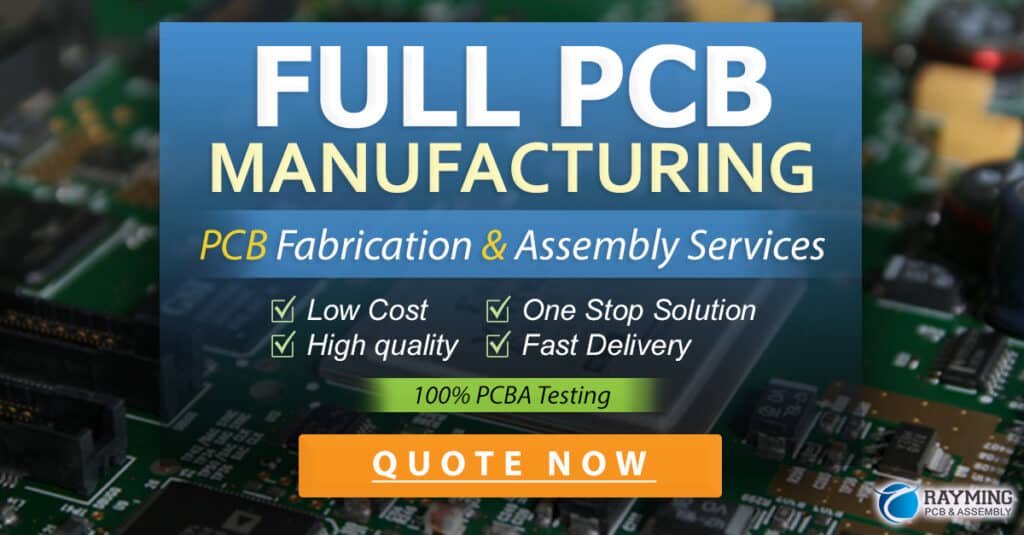
Quality Assurance and Testing
To ensure the reliability and performance of aerospace PCBs, manufacturers employ a range of quality assurance and testing techniques, including:
Visual Inspection
Visual inspection is the first line of defense in detecting PCB defects and ensuring conformance to design specifications. This involves:
- Automated optical inspection (AOI): Uses cameras and image processing algorithms to detect surface defects, such as solder bridging and component misalignment
- Manual visual inspection: Involves trained operators visually inspecting PCBs for defects and workmanship issues
Visual inspection is critical for identifying defects early in the manufacturing process and preventing defective PCBs from reaching later stages of assembly.
X-Ray Inspection
X-ray inspection is used to detect internal defects and verify the integrity of hidden features, such as:
- Solder joints and connections
- Vias and plated through-holes
- Embedded components
X-ray inspection uses high-resolution X-ray imaging to create detailed images of the internal structure of a PCB, allowing for the detection of defects that are not visible to the naked eye.
Electrical Testing
Electrical testing is used to verify the functionality and performance of a PCB, including:
- Continuity testing: Verifies the integrity of electrical connections and traces
- Insulation resistance testing: Measures the resistance between conductors to ensure adequate insulation
- Functional testing: Verifies the operation of the PCB under normal and extreme conditions
Electrical testing is critical for ensuring that aerospace PCBs meet their specified performance requirements and can reliably operate in their intended environment.
Environmental Testing
Environmental testing is used to simulate the harsh conditions that aerospace PCBs will encounter in operation, including:
- Thermal cycling: Exposes the PCB to repeated cycles of high and low temperatures to verify its thermal stability and resistance to thermal stress
- Vibration and shock testing: Simulates the vibration and shock loads encountered in aerospace environments to verify the PCB’s mechanical integrity
- Altitude and vacuum testing: Simulates the low-pressure and vacuum conditions encountered at high altitudes to verify the PCB’s resistance to outgassing and other vacuum effects
Environmental testing is critical for ensuring that aerospace PCBs can withstand the rigors of their intended operating environment and maintain reliable performance over their expected lifetime.
Aerospace PCB Assembly Standards and Certifications
To ensure the quality and reliability of aerospace PCBs, manufacturers must adhere to a range of industry standards and certifications, including:
IPC Standards
IPC (Association Connecting Electronics Industries) is a global trade association that develops standards for the electronic interconnect industry. Key IPC standards for aerospace PCB assembly include:
- IPC-6012: Qualification and Performance Specification for Rigid Printed Boards
- IPC-6013: Qualification and Performance Specification for Flexible Printed Boards
- IPC-A-600: Acceptability of Printed Boards
- IPC J-STD-001: Requirements for Soldered Electrical and Electronic Assemblies
These standards provide detailed requirements for PCB design, fabrication, assembly, and acceptance, ensuring a consistent level of quality and reliability across the industry.
AS9100 Certification
AS9100 is a quality management system standard specific to the aerospace industry, based on the ISO 9001 standard. AS9100 certification demonstrates that a PCB manufacturer has a robust quality management system in place that meets the strict requirements of the aerospace industry, including:
- Risk management
- Configuration management
- Product safety
- Counterfeit parts prevention
- Traceability and documentation
AS9100 certification is often a prerequisite for aerospace PCB assembly providers to be approved as suppliers to major aerospace companies and defense contractors.
NADCAP Accreditation
NADCAP (National Aerospace and Defense Contractors Accreditation Program) is a global cooperative program for the aerospace industry that provides accreditation for special processes and products. NADCAP accreditation demonstrates that a PCB manufacturer has met the stringent requirements for processes such as:
- Soldering
- Conformal coating
- Surface mount technology
- Non-destructive testing
NADCAP accreditation is a recognition of a manufacturer’s commitment to quality and adherence to best practices in aerospace PCB assembly.
Future Trends in Aerospace PCB Assembly
As the aerospace industry continues to evolve, PCB assembly technologies and techniques must keep pace to meet the ever-increasing demands for performance, reliability, and functionality. Some of the key trends shaping the future of aerospace PCB assembly include:
Advanced Materials
The development of new, high-performance materials will enable the design of aerospace PCBs with enhanced thermal, mechanical, and electrical properties. Some promising materials include:
- Carbon nanotubes: Offer exceptional thermal and electrical conductivity, as well as high strength-to-weight ratios
- Graphene: Provides excellent thermal and electrical conductivity, as well as high mechanical strength and flexibility
- Ceramic substrates: Offer high thermal stability, low dielectric loss, and resistance to radiation and chemical attack
These advanced materials will enable the development of PCBs that can operate reliably in even more extreme environments and support the integration of advanced electronic functionalities.
3D Packaging and Integration
3D packaging and integration technologies will enable the development of more compact, high-performance aerospace electronic systems. Some key technologies include:
- 3D stacking: Involves vertically stacking multiple PCBs or integrated circuits to increase packaging density and reduce signal path lengths
- Wafer-level packaging: Involves packaging integrated circuits at the wafer level, before singulation into individual chips, to reduce packaging size and improve performance
- System-in-package (SiP): Involves integrating multiple electronic functions, such as processors, memory, and sensors, into a single package to create a complete system-on-a-package
These technologies will enable the development of highly integrated, miniaturized aerospace electronic systems with improved performance and reliability.
Artificial Intelligence and Machine Learning
Artificial intelligence (AI) and machine learning (ML) techniques will play an increasingly important role in aerospace PCB assembly, enabling the optimization of design, manufacturing, and testing processes. Some potential applications include:
- Generative design: Uses AI algorithms to automatically generate PCB layouts optimized for performance, manufacturability, and cost
- Predictive maintenance: Uses ML algorithms to analyze sensor data and predict when a PCB or electronic system is likely to fail, enabling proactive maintenance and reducing downtime
- Automated visual inspection: Uses AI-based image recognition algorithms to enhance the speed and accuracy of automated optical inspection systems
The integration of AI and ML techniques into aerospace PCB assembly will enable faster, more efficient, and more reliable production of high-quality PCBs.
FAQs
-
What makes aerospace PCBs different from PCBs used in other industries?
Aerospace PCBs are designed to withstand extreme environmental conditions, such as wide temperature ranges, high levels of vibration and shock, and exposure to radiation and vacuum conditions. They also require higher levels of reliability, traceability, and adherence to industry standards and certifications compared to PCBs used in other industries. -
What are some of the key challenges in aerospace PCB assembly?
Some of the key challenges in aerospace PCB assembly include designing for harsh environmental conditions, achieving high density and miniaturization, ensuring reliability and quality control, and meeting strict industry standards and certifications. -
What advanced technologies are used in aerospace PCB assembly?
Advanced technologies used in aerospace PCB assembly include high-temperature materials, embedded components, advanced interconnect technologies (such as HDI and rigid-flex), and additive manufacturing techniques. -
How is quality assured in aerospace PCB assembly?
Quality assurance in aerospace PCB assembly involves a range of techniques, including visual inspection (AOI and manual), X-ray inspection, electrical testing (continuity, insulation resistance, and functional testing), and environmental testing (thermal cycling, vibration and shock, and altitude and vacuum testing). -
What are some of the key standards and certifications for aerospace PCB assembly?
Key standards and certifications for aerospace PCB assembly include IPC standards (such as IPC-6012, IPC-6013, and IPC J-STD-001), AS9100 certification for quality management systems, and NADCAP accreditation for special processes and products.
Leave a Reply