The Role of a PCB Factory
The primary function of a PCB factory is to manufacture high-quality PCBs according to the specifications provided by their clients. This process involves several steps, including:
- Design and Engineering
- Material Selection
- Fabrication
- Assembly
- Testing and Quality Control
Design and Engineering
Before the manufacturing process begins, the PCB factory works closely with the client to design and engineer the PCB. This involves creating a detailed schematic and layout of the PCB using specialized software, such as Altium Designer or Eagle CAD. The design team ensures that the PCB meets the client’s requirements, including functionality, size, and compatibility with other components.
Material Selection
PCBs are made from a variety of materials, depending on the specific application and environment in which they will be used. The most common base material for PCBs is FR-4, a glass-reinforced epoxy laminate. However, other materials, such as polyimide or ceramic, may be used for high-temperature or high-frequency applications. The PCB factory selects the appropriate materials based on the client’s requirements and industry standards.
Fabrication
The fabrication process involves several sub-processes, including:
- Printing the circuit pattern onto the copper-clad laminate using a photoresist and exposure to UV light
- Etching away the unwanted copper to leave the desired circuit pattern
- Drilling holes for through-hole components and vias
- Applying a solder mask to protect the copper traces and prevent short circuits
- Applying a silkscreen to add labels, logos, and other markings to the PCB
Fabrication Sub-Processes
Sub-Process | Description |
---|---|
Printing | Transferring the circuit pattern onto the copper-clad laminate using a photoresist and exposure to UV light |
Etching | Removing unwanted copper to leave the desired circuit pattern |
Drilling | Creating holes for through-hole components and vias |
Solder Mask | Applying a protective layer to the copper traces to prevent short circuits |
Silkscreen | Adding labels, logos, and other markings to the PCB |
Assembly
Once the PCB has been fabricated, it moves to the assembly stage. This involves soldering electronic components, such as resistors, capacitors, and integrated circuits, onto the PCB. There are two main types of assembly: through-hole and surface mount.
- Through-hole assembly involves inserting component leads through the drilled holes in the PCB and soldering them to the copper traces on the opposite side.
- Surface mount assembly involves placing components directly onto the surface of the PCB and soldering them to the copper traces.
Many PCB factories use automated assembly processes, such as pick-and-place machines and reflow ovens, to increase efficiency and accuracy.
Testing and Quality Control
Before the PCBs are shipped to the client, they undergo rigorous testing and quality control to ensure that they meet the required specifications and are free from defects. This may include:
- Visual inspection
- Automated Optical Inspection (AOI)
- X-ray inspection
- Electrical testing
- Functional testing
The PCB factory maintains detailed records of the testing and quality control processes to ensure traceability and accountability.
Types of PCB Factories
PCB factories can be categorized based on their size, capabilities, and specializations. Some common types of PCB factories include:
Small to Medium-Sized PCB Factories
These factories typically have a smaller production capacity and may specialize in specific types of PCBs or cater to a particular industry. They often offer more personalized service and may be more flexible in accommodating custom designs or low-volume orders.
Large-Scale PCB Factories
Large-scale PCB factories have a higher production capacity and often serve a wide range of industries. They may offer a broader range of services, including design, fabrication, assembly, and testing. These factories typically invest in state-of-the-art equipment and automation to increase efficiency and maintain consistent quality.
Specialized PCB Factories
Some PCB factories specialize in particular types of PCBs or manufacturing processes. For example:
- High-Density Interconnect (HDI) PCB factories focus on producing PCBs with high component density and fine pitch features.
- Flexible PCB factories specialize in manufacturing flexible and rigid-flex PCBs for applications that require bendable or conformable circuit boards.
- Metal Core PCB (MCPCB) factories produce PCBs with a metal core substrate for improved thermal management in high-power applications.
Choosing a PCB Factory
When selecting a PCB factory for your project, there are several factors to consider:
- Experience and Expertise: Look for a factory with a proven track record in manufacturing PCBs similar to your requirements.
- Quality and Certifications: Ensure that the factory adheres to industry standards and holds relevant certifications, such as ISO 9001, UL, or IPC.
- Production Capacity: Consider the factory’s production capacity and lead times to ensure they can meet your project’s timeline and volume requirements.
- Communication and Support: Choose a factory that maintains clear communication and offers responsive support throughout the manufacturing process.
- Price and Value: While cost is an important consideration, it should be balanced against the factory’s capabilities, quality, and overall value proposition.
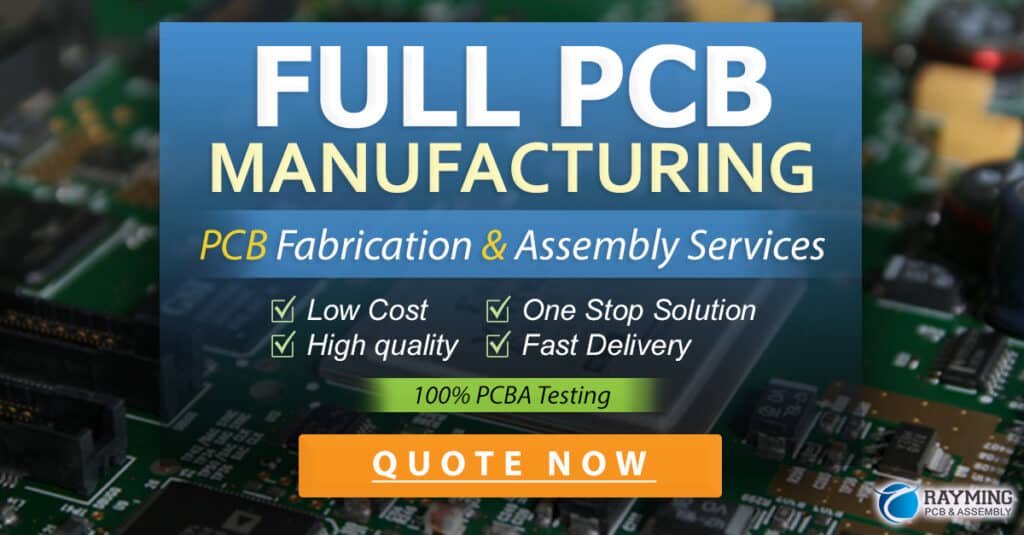
The Future of PCB Manufacturing
As the electronics industry continues to evolve, PCB factories must adapt to new technologies and trends. Some key developments shaping the future of PCB manufacturing include:
Miniaturization and High-Density Interconnect (HDI)
The demand for smaller, more compact electronic devices is driving the need for PCBs with higher component density and finer pitch features. PCB factories are investing in advanced manufacturing processes and equipment to produce HDI PCBs that can accommodate these requirements.
Additive Manufacturing and 3D Printing
Additive manufacturing techniques, such as 3D printing, are being explored as potential alternatives to traditional PCB fabrication methods. While still in the early stages, these technologies could enable faster prototyping, greater design flexibility, and more efficient use of materials.
Environmental Sustainability
As environmental concerns grow, PCB factories are facing increasing pressure to adopt eco-friendly practices and materials. This includes using lead-free solders, minimizing waste, and implementing energy-efficient manufacturing processes.
Industry 4.0 and Smart Manufacturing
PCB factories are embracing Industry 4.0 technologies, such as the Internet of Things (IoT), artificial intelligence (AI), and machine learning (ML), to optimize their manufacturing processes. Smart factories can collect and analyze real-time data to improve efficiency, reduce downtime, and enhance quality control.
Frequently Asked Questions (FAQ)
-
What is the typical lead time for PCB manufacturing?
Lead times can vary depending on the complexity of the PCB, the factory’s workload, and the order volume. Typical lead times range from 1-2 weeks for standard PCBs to 4-6 weeks for more complex or custom designs. -
What is the minimum order quantity (MOQ) for PCBs?
The MOQ varies between factories and depends on the PCB’s complexity and the factory’s production setup. Some factories may accept low-volume orders of 1-50 pieces, while others may require a minimum of 100 or more. -
What file formats are required for PCB manufacturing?
Most PCB factories require Gerber files, which contain the PCB’s design information, including the copper layers, solder mask, and silkscreen. Additionally, factories may request drill files, Bill of Materials (BOM), and assembly drawings. -
How can I ensure the quality of my PCBs?
To ensure the quality of your PCBs, work with a reputable PCB factory that adheres to industry standards and has a proven track record. Clearly communicate your requirements and specifications, and request regular updates and quality control reports throughout the manufacturing process. -
What is the difference between a PCB prototype and a production run?
A PCB prototype is a small batch of boards, typically used for testing and validation before mass production. Prototypes may be manufactured using different processes or materials compared to the final production run, which is optimized for larger volumes and cost-efficiency.
Conclusion
PCB factories play a vital role in the electronics industry, enabling the production of high-quality PCBs for a wide range of applications. By understanding the manufacturing process, types of PCB factories, and key considerations when choosing a factory, you can ensure that your PCB project is successful. As the industry continues to evolve, PCB factories must adapt to new technologies and trends to remain competitive and meet the changing needs of their clients.
Leave a Reply