The Importance of PCB Fabrication
PCBs are an essential component in modern electronics, found in virtually every electronic device we use today. They provide a reliable and efficient means of connecting electronic components, allowing for the creation of complex circuits in a compact and organized manner. The fabrication process is crucial to ensuring that these boards function as intended, meeting the specific requirements of each application.
Key Benefits of Professional PCB Fabrication
- Reliability: Professional PCB fabricators adhere to strict quality control standards, ensuring that the final product is reliable and functions as expected.
- Consistency: By utilizing advanced manufacturing techniques and equipment, PCB fabricators can produce consistent results across multiple boards.
- Cost-effectiveness: Outsourcing PCB fabrication to a professional company can be more cost-effective than attempting to produce boards in-house, especially for large-scale production.
- Expertise: PCB fabricators possess the knowledge and experience necessary to handle complex designs and troubleshoot any issues that may arise during the manufacturing process.
The PCB Fabrication Process
The PCB fabrication process consists of several stages, each of which plays a critical role in the creation of a functional printed circuit board. Let’s take a closer look at each stage:
1. Design and Layout
The first step in PCB fabrication is the design and layout of the circuit board. This involves creating a schematic diagram of the circuit and then translating that schematic into a physical layout using specialized PCB design software. The layout must take into account factors such as component placement, trace routing, and signal integrity to ensure optimal performance of the final product.
2. Material Selection
Once the design is finalized, the next step is to select the appropriate materials for the PCB. The most common material used for PCBs is FR-4, a glass-reinforced epoxy laminate. However, depending on the specific requirements of the application, other materials such as polyimide or ceramic may be used. The choice of material will impact the board’s durability, thermal stability, and dielectric properties.
3. Printing and Etching
With the design and materials selected, the next stage is to print and etch the circuit pattern onto the PCB substrate. This is typically done using a photolithographic process, which involves applying a light-sensitive resist to the substrate, exposing it to UV light through a photomask, and then developing the resist to reveal the desired circuit pattern. The exposed areas are then etched away using a chemical solution, leaving only the copper traces that form the actual circuit.
4. Drilling and Plating
After the circuit pattern has been etched, the next step is to drill holes in the board for component leads and vias. These holes are then plated with a conductive material, typically copper, to ensure electrical connectivity between the layers of the board. The plating process also helps to protect the copper traces from oxidation and corrosion.
5. Solder Mask Application
A solder mask is a protective layer applied to the surface of the PCB to prevent accidental short circuits and to protect the copper traces from damage during the soldering process. The solder mask is typically applied using a silkscreen printing process and then cured using UV light.
6. Surface Finish
The final step in the PCB fabrication process is to apply a surface finish to the exposed copper areas of the board. This helps to prevent oxidation and improves the solderability of the board. Common surface finishes include HASL (Hot Air Solder Leveling), ENIG (Electroless Nickel Immersion Gold), and OSP (Organic Solderability Preservative).
The Role of a Professional PCB Fabricator
A professional PCB fabricator plays a crucial role in ensuring the quality and reliability of the final product. They possess the expertise, equipment, and facilities necessary to handle every stage of the fabrication process, from design to final inspection.
Advantages of Working with a Professional PCB Fabricator
- State-of-the-art equipment: Professional PCB fabricators invest in the latest manufacturing equipment and technology to ensure the highest quality results.
- Experienced personnel: PCB fabricators employ skilled technicians and engineers with extensive experience in the industry, ensuring that every project is handled with expertise and precision.
- Quality control: Stringent quality control measures are implemented throughout the fabrication process to identify and correct any defects or issues before the final product is delivered.
- Rapid prototyping: Many PCB fabricators offer rapid prototyping services, allowing for quick turnaround times on prototype boards for testing and validation purposes.
- Scalability: Professional PCB fabricators have the capacity to handle both small and large-scale production runs, making them suitable for a wide range of projects and applications.
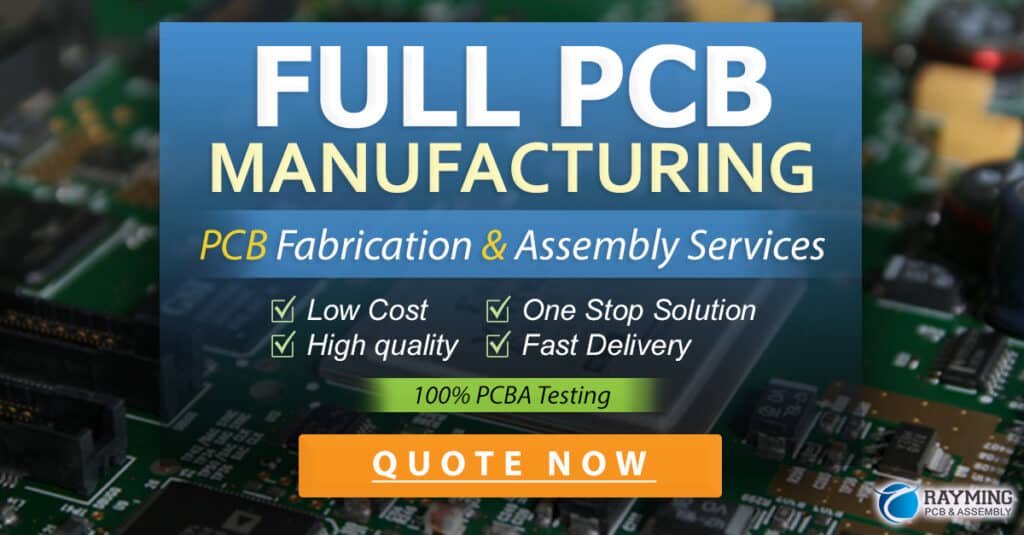
Choosing the Right PCB Fabricator
When selecting a PCB fabricator for your project, there are several key factors to consider to ensure that you choose the right partner for your needs.
Factors to Consider When Selecting a PCB Fabricator
- Experience and expertise: Look for a fabricator with a proven track record in the industry and experience handling projects similar to yours.
- Manufacturing capabilities: Ensure that the fabricator has the necessary equipment and facilities to handle your specific project requirements, such as multi-layer boards or advanced surface finishes.
- Quality control: Inquire about the fabricator’s quality control processes and certifications to ensure that they adhere to industry standards and best practices.
- Turnaround time: Consider the fabricator’s typical turnaround times and whether they can accommodate your project timeline.
- Customer support: Choose a fabricator that offers responsive and knowledgeable customer support to assist you throughout the fabrication process.
The Future of PCB Fabrication
As electronic devices continue to evolve and become more complex, the PCB fabrication industry must adapt to keep pace with these changes. Emerging trends and technologies are shaping the future of PCB fabrication, presenting both challenges and opportunities for the industry.
Emerging Trends and Technologies in PCB Fabrication
- Miniaturization: The demand for smaller, more compact electronic devices is driving the need for miniaturized PCBs with higher component densities.
- High-speed applications: As data rates continue to increase, PCB fabricators must adapt to handle the challenges associated with high-speed signal integrity and EMI/EMC considerations.
- Advanced materials: New materials, such as high-frequency laminates and flexible substrates, are being developed to meet the demands of emerging applications.
- Additive manufacturing: 3D printing technologies are being explored as a potential alternative to traditional subtractive PCB fabrication methods, offering greater design flexibility and faster prototyping.
- Sustainability: There is a growing emphasis on environmentally friendly PCB fabrication processes and materials to reduce the industry’s ecological footprint.
Frequently Asked Questions (FAQ)
-
What is the difference between a PCB and a PCBA?
A PCB (Printed Circuit Board) is the bare board without any components attached, while a PCBA (Printed Circuit Board Assembly) is a PCB with electronic components soldered onto it, ready for use in an electronic device. -
How long does the PCB fabrication process typically take?
The turnaround time for PCB fabrication can vary depending on the complexity of the design, the fabricator’s workload, and the specific manufacturing options selected. Standard lead times can range from a few days to several weeks, but many fabricators offer expedited services for faster turnaround times. -
What is the minimum order quantity (MOQ) for PCB fabrication?
The minimum order quantity for PCB fabrication varies among fabricators and often depends on the complexity of the design and the manufacturing options selected. Some fabricators may offer low MOQs for prototype runs, while others may require higher quantities for production runs. It’s best to consult with your chosen fabricator to determine their specific MOQ requirements. -
Can I fabricate my own PCBs at home?
While it is possible to fabricate simple PCBs at home using methods such as etching or milling, the process can be time-consuming, and the results may not be as professional or reliable as those obtained from a professional PCB fabricator. For more complex designs or higher quantities, it is generally recommended to work with a professional fabricator to ensure the best results. -
How much does PCB fabrication cost?
The cost of PCB fabrication depends on several factors, including the size and complexity of the board, the number of layers, the chosen materials and surface finishes, and the quantity ordered. Professional PCB fabricators typically provide instant online quotes based on these parameters, allowing you to easily compare prices and select the most cost-effective option for your project.
Conclusion
PCB fabrication is a complex and critical process that plays a vital role in the creation of modern electronic devices. By understanding the various stages involved in the fabrication process and the importance of working with a professional PCB fabricator, you can ensure that your project benefits from the highest quality and reliability standards. As the electronics industry continues to evolve, PCB fabricators must adapt to new challenges and opportunities, driving innovation and shaping the future of this essential sector.
Stage | Description |
---|---|
Design and Layout | Creating a schematic diagram and physical layout of the circuit board |
Material Selection | Choosing the appropriate PCB substrate material based on application requirements |
Printing and Etching | Applying a photoresist, exposing it to UV light, and etching away unwanted copper to form the circuit pattern |
Drilling and Plating | Drilling holes for component leads and vias, then plating them with a conductive material |
Solder Mask Application | Applying a protective layer to prevent short circuits and protect copper traces during soldering |
Surface Finish | Applying a finish to exposed copper areas to prevent oxidation and improve solderability |
By partnering with a reputable PCB fabricator, you can leverage their expertise, state-of-the-art equipment, and commitment to quality to bring your electronic projects to life. As the demand for more advanced and miniaturized electronic devices continues to grow, the role of professional PCB fabricators in driving innovation and ensuring the reliability of these essential components will only become more critical in the years to come.
Leave a Reply