How are PCBs Fabricated?
The pcb fabrication process can be broken down into several key steps:
-
Design: The first step is to design the circuit schematic and layout using PCB design software. This involves determining the placement of components and routing of copper traces that will form the electrical connections on the board.
-
Printing the Circuit Pattern: The circuit design is printed onto a transparent plastic sheet called a photomask or film. The photomask is used to transfer the circuit pattern onto copper-clad boards.
-
Exposing and Developing: The copper-clad board is coated with a light-sensitive resist material and then the photomask is placed on top. The board is exposed to ultraviolet light, which hardens the resist where the circuit pattern allows light to pass through. The unexposed resist is then removed in a chemical bath, leaving the circuit pattern etched onto the board.
-
Etching: The exposed copper is removed using a chemical etching process, typically with an acidic solution like ferric chloride or ammonium persulfate. This leaves only the copper traces of the circuit pattern on the board.
-
Drilling: Holes are drilled into the board to accommodate through-hole components or to create vias for multilayer boards. The drilling is done using computer-controlled drill machines.
-
Plating and Coating: A thin layer of copper is chemically deposited onto the board, covering the traces and walls of the drilled holes. This is followed by a solder mask which is applied to the board and exposed, leaving the areas that need to be soldered exposed. A silkscreen is then applied to add labels, logos, and other marks to the board.
-
Surface Finishing: The exposed copper areas are coated with a thin layer of metal, typically gold, nickel, or tin, to protect the copper and enhance solderability.
-
Electrical Testing: The finished board is electrically tested to ensure that all connections are correct and there are no short circuits or open connections.
-
Assembly: Finally, the electronic components are soldered onto the board using through-hole or surface mount assembly techniques.
Types of PCBs
There are several types of PCBs, each with their own fabrication process and use cases:
PCB Type | Layers | Fabrication | Uses |
---|---|---|---|
Single-sided | 1 | Simplest and cheapest. Circuits on one side only. | Simple circuits, low-cost devices |
Double-sided | 2 | Circuits on both sides, connected with through-hole vias | More complex circuits, lower cost than multilayer |
Multilayer | 4+ | Multiple layers of circuits laminated together with insulating material | High-density, complex circuits like motherboards and smartphones |
Flexible | Varies | Uses flexible substrate materials like polyimide | Wearables, interconnects between boards or assemblies |
Rigid-Flex | Varies | Combination of rigid and flexible sections | High-reliability applications, aerospace, medical devices |
Benefits of PCBs
PCBs offer several benefits over other types of circuit construction:
- Compact: PCBs allow for very compact and dense circuit designs, enabling smaller devices.
- Reliable: Properly designed and fabricated PCBs are highly reliable, with a low failure rate.
- Consistent: Automated pcb fabrication processes ensure consistent quality and reproducibility.
- Cost-effective: Mass production of PCBs is very cost-effective compared to other methods.
- Efficient assembly: PCBs are designed for efficient automated assembly, reducing time and cost.
Challenges in PCB Fabrication
While pcb fabrication is a well-established process, there are still several challenges that manufacturers face:
Miniaturization
As devices continue to shrink in size, PCBs need to become smaller and denser. This requires advanced fabrication techniques and high-precision equipment to produce very fine traces and small vias.
High-Frequency Circuits
High-frequency circuits, such as those used in 5G devices, require special pcb materials and design techniques to minimize signal loss and interference. This can increase the complexity and cost of fabrication.
Environmental Concerns
Traditional pcb fabrication processes use hazardous chemicals and generate waste that can harm the environment. There is increasing pressure on manufacturers to adopt greener fabrication methods and materials.
Supply Chain Disruptions
The COVID-19 pandemic has highlighted the vulnerability of global supply chains, including those for PCB materials and components. Manufacturers need to be prepared for potential disruptions and have contingency plans in place.
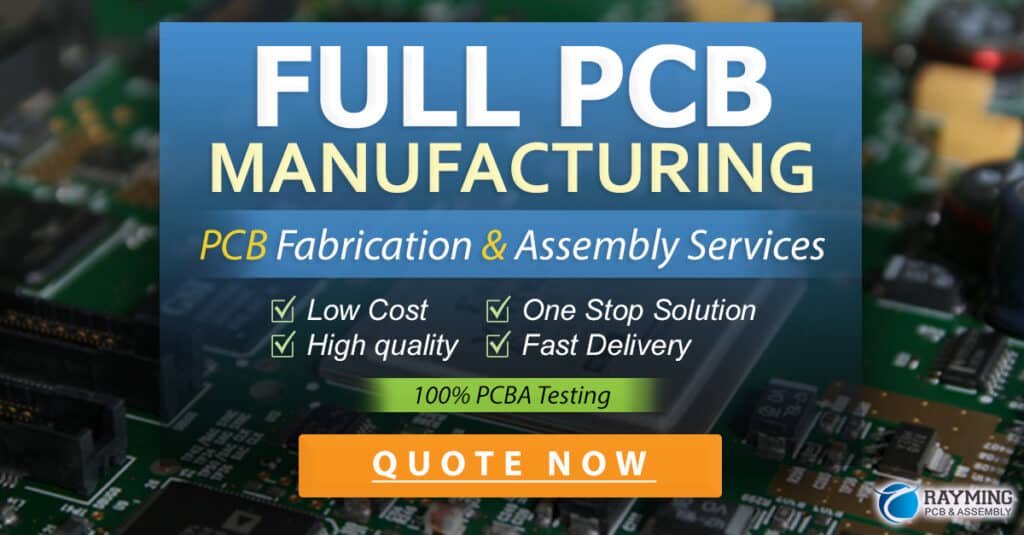
Future of PCB Fabrication
The pcb fabrication industry is constantly evolving to meet the changing needs of electronics. Some of the trends and developments shaping the future of PCBs include:
3D Printing
3D printing technology is being adapted for PCB fabrication, allowing for rapid prototyping and customization. This could enable new types of circuit designs and faster time-to-market for products.
Embedded Components
Instead of mounting components on the surface of the board, they can be embedded within the layers of the PCB. This can save space, improve reliability, and reduce assembly costs.
Advanced Materials
New materials, such as graphene and carbon nanotubes, are being explored for use in PCBs. These materials could enable higher performance, flexibility, and thermal management.
Artificial Intelligence
AI and machine learning are being applied to PCB design and fabrication, enabling optimization of circuit layouts, prediction of failures, and quality control.
FAQ
What is the difference between PCB and PCBA?
PCB stands for printed circuit board, which is the bare board without any components. PCBA stands for printed circuit board assembly, which is the PCB with all the components soldered onto it, ready for use in a device.
How long does it take to fabricate a PCB?
The time required for pcb fabrication depends on the complexity of the design, the fabrication process used, and the manufacturer’s capacity. Simple, single-sided boards can be fabricated in a few days, while complex multilayer boards can take several weeks.
What is the minimum trace width and spacing for PCBs?
The minimum trace width and spacing depends on the pcb fabrication process and the capabilities of the manufacturer. For standard PCBs, the minimum trace width is typically around 0.006 inches (0.15mm), and the minimum spacing is around 0.008 inches (0.20mm). Advanced processes can achieve much finer traces and spacing.
What is the typical cost of PCB fabrication?
The cost of pcb fabrication varies widely depending on the type of board, the quantity ordered, and the manufacturer. Simple, single-sided boards in large quantities can cost less than $1 per board, while complex multilayer boards in small quantities can cost hundreds of dollars per board.
What are the environmental impacts of PCB fabrication?
Traditional pcb fabrication processes use hazardous chemicals, such as acids, solvents, and heavy metals, which can pollute water and soil if not properly managed. The process also generates waste, such as used etchant and drill bits, which needs to be disposed of safely. However, the industry is shifting towards greener fabrication methods, such as using less hazardous chemicals and recycling materials where possible.
Leave a Reply