The Importance of PCB Etching
PCB etching plays a vital role in the production of electronic devices. Some of the key reasons why PCB etching is important include:
-
Creating Conductive Patterns: PCB etching allows for the creation of intricate conductive patterns on the PCB substrate. These patterns form the electrical connections between components, enabling the transfer of signals and power within the device.
-
Ensuring Precision and Accuracy: The etching process enables the creation of precise and accurate conductive patterns. This is crucial for the proper functioning of electronic devices, as even minor deviations in the patterns can lead to signal integrity issues or device failure.
-
Facilitating Miniaturization: As electronic devices become smaller and more compact, PCB etching techniques have evolved to accommodate the need for higher density and finer pitch connections. Advanced etching methods allow for the creation of smaller and more intricate patterns, enabling the miniaturization of electronic devices.
-
Enabling High-Volume Production: PCB etching is a scalable process that can be automated for high-volume production. This allows manufacturers to produce large quantities of PCBs efficiently and cost-effectively, meeting the demands of the electronics industry.
The PCB Etching Process
The PCB etching process typically involves the following steps:
-
PCB Design and Artwork Creation: The first step in PCB etching is to design the desired conductive patterns using specialized PCB design software. The design is then used to create the artwork, which is a high-resolution representation of the conductive patterns.
-
Substrate Preparation: The PCB substrate, usually a copper-clad laminate, is cleaned and prepared for the etching process. This may involve surface treatment to improve adhesion and ensure a clean surface for the subsequent steps.
-
Photoresist Application: A photoresist, which is a light-sensitive material, is applied to the copper surface of the PCB substrate. The photoresist can be applied through various methods, such as spin coating, spray coating, or dry film lamination.
-
Exposure and Development: The artwork is used to create a photomask, which is placed on top of the photoresist-coated PCB substrate. The substrate is then exposed to UV light, which causes the exposed areas of the photoresist to become soluble (for positive photoresist) or insoluble (for negative photoresist) in a developer solution. After exposure, the substrate is developed, removing the soluble portions of the photoresist and leaving the desired pattern.
-
Etching: The developed PCB substrate is then subjected to the etching process. The most common etching method is chemical etching, where the substrate is immersed in an etchant solution, typically ferric chloride or ammonium persulfate. The etchant selectively removes the copper from the areas not protected by the photoresist, creating the desired conductive patterns.
-
Resist Removal and Cleaning: After etching, the remaining photoresist is removed from the PCB substrate using a stripping solution. The substrate is then cleaned to remove any residues and prepare it for the subsequent processes, such as drilling, plating, and solder mask application.
Types of PCB Etching
There are several types of PCB etching methods used in the industry, each with its own advantages and limitations. Some of the common PCB etching methods include:
-
Chemical Etching: This is the most widely used method for PCB etching. It involves immersing the PCB substrate in an etchant solution, which selectively removes the copper from the areas not protected by the photoresist. Chemical etching is relatively simple, cost-effective, and suitable for high-volume production.
-
Plasma Etching: Plasma etching uses a plasma, which is an ionized gas, to remove the copper from the PCB substrate. This method is known for its high precision and the ability to create fine pitch patterns. Plasma etching is often used for advanced PCB applications that require high accuracy and resolution.
-
Laser Etching: Laser etching utilizes a high-powered laser to selectively remove the copper from the PCB substrate. This method offers high precision and the ability to create very fine patterns. Laser etching is often used for specialized applications that require intricate designs or rapid prototyping.
-
Mechanical Etching: Mechanical etching involves the use of abrasive particles or tools to physically remove the copper from the PCB substrate. This method is less common compared to chemical and plasma etching but may be used for specific applications or in combination with other etching methods.
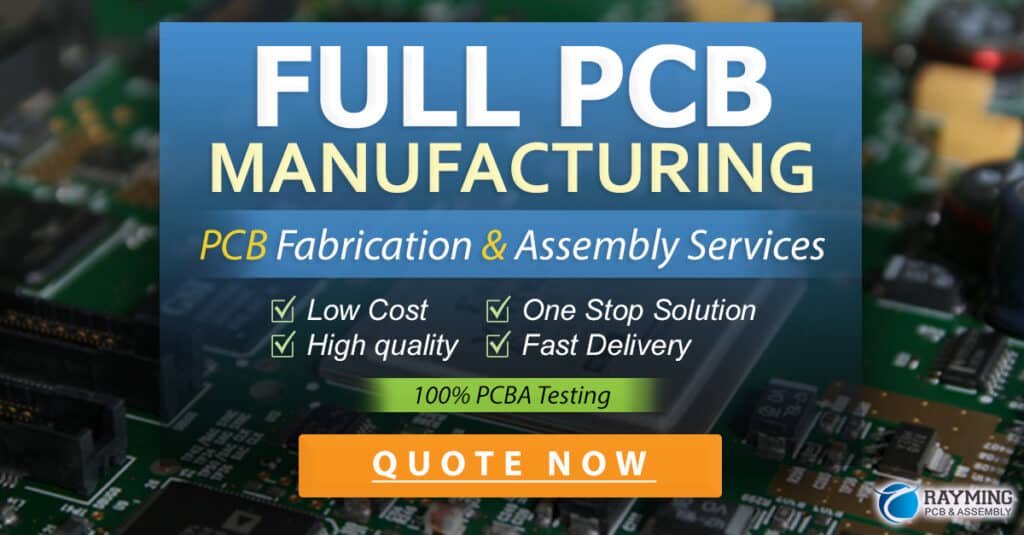
Factors Affecting PCB Etching Quality
Several factors can influence the quality and accuracy of PCB etching. Some of these factors include:
-
Photoresist Quality: The quality and consistency of the photoresist play a crucial role in the etching process. A high-quality photoresist ensures accurate pattern transfer and reduces the risk of defects or inconsistencies in the etched patterns.
-
Exposure and Development Parameters: Proper exposure and development of the photoresist are essential for achieving accurate patterns. Overexposure, underexposure, or improper development can lead to pattern distortions or defects.
-
Etchant Concentration and Temperature: The concentration and temperature of the etchant solution can affect the etching rate and the quality of the etched patterns. Maintaining the optimal concentration and temperature ensures consistent etching results and reduces the risk of over-etching or under-etching.
-
Etching Time: The etching time must be carefully controlled to achieve the desired pattern depth and avoid over-etching or under-etching. Insufficient etching time can result in incomplete copper removal, while excessive etching time can cause pattern widening or undercutting.
-
Substrate Surface Preparation: Proper cleaning and preparation of the PCB substrate surface are crucial for ensuring good adhesion of the photoresist and reducing the risk of defects or contamination during the etching process.
Advancements in PCB Etching Technology
PCB etching technology has evolved significantly over the years to meet the increasing demands for higher density, finer pitch, and improved signal integrity in electronic devices. Some of the notable advancements in PCB etching technology include:
-
Direct Imaging (DI): Direct imaging is a maskless exposure method that uses a high-resolution laser or LED to directly expose the photoresist on the PCB substrate. This eliminates the need for physical photomasks and enables faster and more flexible PCB prototyping and production.
-
Laser Direct Imaging (LDI): LDI is an advanced version of direct imaging that uses a high-powered laser to expose the photoresist. This method offers even higher resolution and accuracy compared to conventional DI, enabling the creation of ultra-fine pitch patterns and high-density PCBs.
-
Inkjet Printing: Inkjet printing is an emerging technology in PCB fabrication that allows for the direct printing of conductive patterns on the PCB substrate. This method eliminates the need for photoresist and etching processes, potentially simplifying the PCB manufacturing process and enabling faster prototyping.
-
Additive Manufacturing: Additive manufacturing, also known as 3D printing, is being explored as a potential alternative to traditional PCB fabrication methods. This technology allows for the direct printing of conductive patterns and even the embedding of components within the PCB structure, offering new possibilities for PCB design and manufacturing.
Challenges and Considerations in PCB Etching
While PCB etching is a well-established process, there are still challenges and considerations that need to be addressed:
-
Environmental Impact: Traditional chemical etching processes involve the use of hazardous chemicals, such as ferric chloride or ammonium persulfate, which can have a negative environmental impact if not properly handled and disposed of. The industry is actively seeking alternative, more environmentally friendly etching solutions and processes.
-
Waste Management: PCB etching generates waste in the form of spent etchant solutions and copper debris. Proper waste management, including treatment, recycling, and disposal, is crucial to minimize the environmental impact and comply with regulations.
-
Process Control and Monitoring: Maintaining consistent and reliable etching results requires strict process control and monitoring. This includes regular checks on etchant concentration, temperature, and etching time, as well as implementing quality control measures to detect and address any issues promptly.
-
High-Density and Fine Pitch Challenges: As PCBs become more complex and feature higher densities and finer pitch patterns, the etching process faces new challenges in terms of accuracy, resolution, and process control. Advances in etching technology and the adoption of new methods, such as direct imaging and laser etching, are helping to address these challenges.
Frequently Asked Questions (FAQ)
-
What is the purpose of PCB etching?
PCB etching is the process of selectively removing copper from a PCB substrate to create the desired conductive patterns that form the electrical connections between components. It is a crucial step in the manufacturing of PCBs and ensures the proper functioning of electronic devices. -
What are the most common methods used for PCB etching?
The most common methods used for PCB etching are chemical etching, plasma etching, and laser etching. Chemical etching is the most widely used method, involving the use of etchant solutions to selectively remove copper. Plasma etching uses ionized gas to remove copper, while laser etching utilizes a high-powered laser for precise copper removal. -
What factors influence the quality of PCB etching?
Several factors can influence the quality of PCB etching, including the quality of the photoresist, exposure and development parameters, etchant concentration and temperature, etching time, and substrate surface preparation. Careful control and monitoring of these factors are essential for achieving consistent and reliable etching results. -
How has PCB etching technology evolved over the years?
PCB etching technology has seen significant advancements, such as direct imaging (DI), laser direct imaging (LDI), inkjet printing, and additive manufacturing. These developments aim to improve resolution, accuracy, and flexibility in PCB fabrication, enabling the creation of high-density and fine pitch patterns. -
What are some of the challenges and considerations in PCB etching?
The main challenges and considerations in PCB etching include the environmental impact of hazardous chemicals used in traditional etching processes, waste management, process control and monitoring, and the increasing complexity of high-density and fine pitch PCBs. The industry is actively seeking solutions to these challenges through the development of more environmentally friendly processes and the adoption of advanced etching technologies.
Etching Method | Advantages | Limitations |
---|---|---|
Chemical Etching | – Cost-effective – Suitable for high-volume production |
– Environmental impact of hazardous chemicals – Limited resolution compared to advanced methods |
Plasma Etching | – High precision – Ability to create fine pitch patterns |
– Higher cost compared to chemical etching – Requires specialized equipment |
Laser Etching | – High precision – Ability to create intricate designs |
– Higher cost compared to chemical etching – Limited throughput compared to other methods |
In conclusion, PCB etching is a vital process in the manufacturing of electronic devices, enabling the creation of precise and reliable conductive patterns on PCB substrates. The industry continues to evolve and innovate, developing new technologies and methods to address the challenges of increasing PCB complexity, environmental concerns, and the demand for faster and more flexible production. As electronic devices continue to advance, PCB etching will remain a critical aspect of PCB fabrication, ensuring the proper functioning and performance of these devices.
Leave a Reply