Understanding the Basics of PCB Development
Before we dive into the specifics of the PCB development process, it’s essential to understand the fundamentals of PCBs. A PCB is a flat board made of insulating materials, such as fiberglass or composite epoxy, with conductive copper tracks printed on one or both sides. These tracks connect various electronic components, such as resistors, capacitors, and integrated circuits (ICs), to form a complete electronic circuit.
PCBs offer several advantages over traditional point-to-point wiring:
- Compact size: PCBs allow for the miniaturization of electronic devices by accommodating a large number of components in a small space.
- Reliability: The fixed layout of PCBs reduces the chances of loose connections and short circuits, improving the overall reliability of the electronic device.
- Mass production: PCBs are designed for automated assembly, enabling the mass production of electronic devices at a lower cost per unit.
Types of PCBs
PCBs can be classified based on the number of layers and the density of components:
- Single-sided PCBs: These have conductive tracks on only one side of the board and are suitable for simple, low-density circuits.
- Double-sided PCBs: These have conductive tracks on both sides of the board, allowing for higher component density and more complex circuits.
- Multi-layer PCBs: These consist of multiple layers of conductive tracks separated by insulating layers, enabling even higher component density and complex circuitry.
PCB Type | Layers | Component Density | Typical Applications |
---|---|---|---|
Single-sided | 1 | Low | Simple circuits, low-cost devices |
Double-sided | 2 | Medium | Moderately complex circuits, consumer electronics |
Multi-layer | 3+ | High | Complex circuits, high-performance devices, aerospace, and military applications |
Stages of PCB Development Process
The PCB development process can be broadly divided into five main stages:
- Design and schematic capture
- PCB layout
- Fabrication
- Assembly
- Testing and validation
Let’s explore each stage in detail.
1. Design and Schematic Capture
The first stage of PCB development involves creating a schematic diagram that represents the electronic circuit. The schematic captures the logical connections between components without considering their physical placement on the board. This stage typically involves the following steps:
- Defining the circuit requirements: The designer must understand the purpose, functionality, and constraints of the electronic device.
- Selecting components: Based on the circuit requirements, the designer selects appropriate electronic components, such as resistors, capacitors, ICs, and connectors.
- Creating the schematic: Using electronic design automation (EDA) software, such as Altium Designer, Eagle, or KiCad, the designer creates a schematic diagram that represents the interconnections between the selected components.
- Simulating the circuit: The designer may perform simulations to verify the functionality and performance of the circuit before proceeding to the next stage.
2. PCB Layout
Once the schematic is finalized, the next stage is to create the physical layout of the PCB. This involves determining the placement of components and routing the conductive tracks to connect them. The PCB layout stage includes the following steps:
- Importing the schematic: The schematic is imported into the PCB layout software, which converts the logical connections into physical footprints for each component.
- Placing components: The designer arranges the components on the board, considering factors such as signal integrity, thermal management, and mechanical constraints.
- Routing tracks: Using the PCB layout software’s autorouter or manual routing tools, the designer creates the conductive tracks that connect the components according to the schematic.
- Adding copper pours and planes: Copper pours and planes are added to the PCB layout to improve signal integrity, reduce electromagnetic interference (EMI), and dissipate heat.
- Generating manufacturing files: Once the layout is finalized, the designer generates the necessary manufacturing files, such as Gerber files and drill files, which are used by the fabrication house to manufacture the PCB.
3. Fabrication
The fabrication stage involves the actual manufacturing of the PCB based on the files generated during the layout stage. The fabrication process typically includes the following steps:
- Printing the circuit pattern: The conductive tracks and pads are printed onto the insulating substrate using a photolithographic process.
- Etching: The unwanted copper is removed from the substrate using a chemical etching process, leaving only the desired conductive tracks and pads.
- Drilling: Holes are drilled through the board to accommodate through-hole components and to create vias that connect tracks on different layers.
- Plating: The holes are plated with copper to ensure electrical connectivity between layers.
- Applying solder mask and silkscreen: A protective solder mask is applied to the board to prevent short circuits, and a silkscreen layer is added to label components and provide assembly instructions.
4. Assembly
Once the PCB is fabricated, the electronic components are mounted onto the board during the assembly stage. This stage can be performed manually for low-volume production or using automated equipment for high-volume production. The assembly process typically involves the following steps:
- Solder paste application: Solder paste, a mixture of tiny solder particles and flux, is applied to the pads on the PCB using a stencil or syringe.
- Component placement: The electronic components are placed onto the PCB, either manually or using automated pick-and-place machines.
- Reflow soldering: The PCB with the placed components is passed through a reflow oven, which melts the solder paste and creates a permanent electrical and mechanical connection between the components and the board.
- Inspection: The assembled PCB is visually inspected for defects, such as misaligned components, solder bridges, or insufficient solder joints.
5. Testing and Validation
The final stage of the PCB development process involves testing and validating the assembled board to ensure it functions as intended. This stage may include the following steps:
- Functional testing: The PCB is powered on, and its functionality is tested using test fixtures or automated test equipment (ATE) to verify that it meets the design specifications.
- Environmental testing: The PCB may be subjected to various environmental stresses, such as temperature cycling, humidity, and vibration, to assess its reliability and durability.
- Compliance testing: If the PCB is intended for use in a regulated industry, such as medical devices or aerospace, it may need to undergo additional compliance testing to meet specific standards and regulations.
- Debugging and rework: If any issues are identified during testing, the PCB may need to be debugged and reworked to resolve the problems.
Best Practices in PCB Development
To ensure a successful PCB development process, designers and manufacturers should adhere to the following best practices:
- Design for manufacturability (DFM): Consider the limitations and capabilities of the manufacturing process during the design stage to minimize the risk of fabrication issues and reduce costs.
- Use standard components: Whenever possible, use standard, readily available components to simplify sourcing and reduce lead times.
- Collaborate with fabrication and assembly partners: Engage with fabrication and assembly partners early in the development process to ensure that the design is compatible with their processes and to optimize the manufacturing workflow.
- Perform thorough design reviews: Conduct regular design reviews at each stage of the development process to catch and rectify any errors or potential issues.
- Document the process: Maintain clear and comprehensive documentation of the design, including schematics, layouts, and manufacturing files, to facilitate future revisions and troubleshooting.
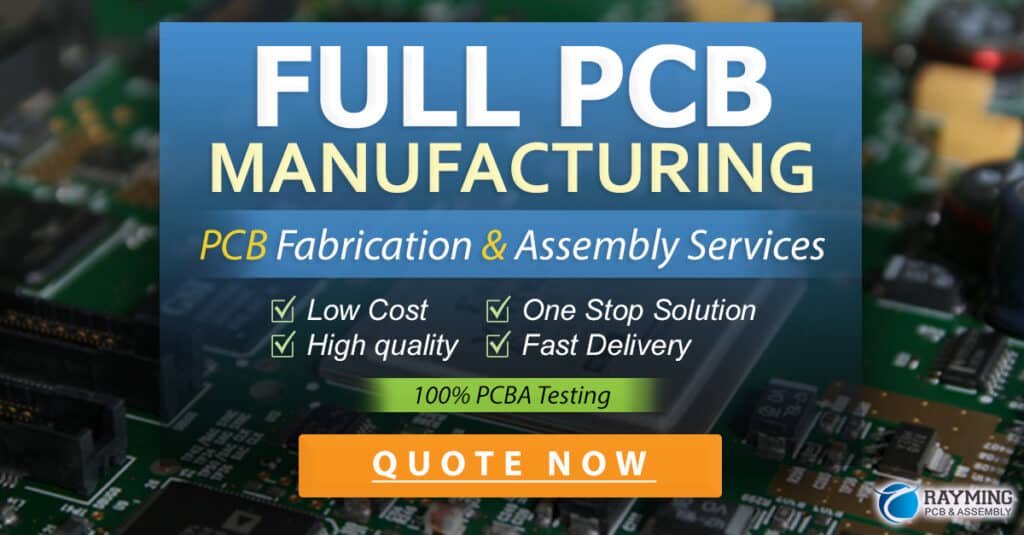
Common Challenges in PCB Development
Despite following best practices, PCB development can still encounter various challenges, such as:
- Signal integrity issues: As PCBs become more complex and operate at higher frequencies, maintaining signal integrity becomes increasingly challenging. Designers must carefully consider factors such as trace impedance, crosstalk, and EMI to ensure reliable performance.
- Thermal management: With the increasing power density of modern electronic components, effective thermal management is crucial to prevent overheating and ensure the long-term reliability of the PCB.
- Manufacturing defects: PCBs are susceptible to various manufacturing defects, such as open circuits, short circuits, and insufficient solder joints, which can lead to reliability issues and increased rework costs.
- Supply chain disruptions: The global nature of the electronics industry means that PCB development is vulnerable to supply chain disruptions, such as component shortages, logistics issues, and geopolitical events.
To mitigate these challenges, designers and manufacturers must stay up-to-date with the latest technologies, best practices, and industry trends. Collaboration and communication among all stakeholders in the development process are also essential to identify and resolve issues promptly.
Frequently Asked Questions (FAQ)
-
What is the typical turnaround time for PCB development?
The turnaround time for PCB development can vary depending on the complexity of the design, the availability of components, and the manufacturing process. Simple PCBs can be developed in a matter of days, while more complex boards may take several weeks or even months. -
How much does PCB development cost?
The cost of PCB development depends on factors such as the size of the board, the number of layers, the component density, and the manufacturing volume. Small, simple PCBs can cost a few dollars per unit, while large, complex boards can cost hundreds or even thousands of dollars per unit. -
What is the difference between through-hole and surface-mount components?
Through-hole components have leads that are inserted into holes drilled in the PCB and soldered to pads on the opposite side. Surface-mount components are mounted directly onto pads on the surface of the PCB. Surface-mount components are generally smaller and better suited for high-density designs, while through-hole components are more robust and easier to replace. -
Can I design my own PCB without formal training in electronic engineering?
While it is possible to design simple PCBs without formal training, more complex designs require a solid understanding of electronic principles, PCB design software, and manufacturing processes. It is recommended to seek guidance from experienced professionals or to undergo training in PCB design before attempting to create your own boards. -
How can I ensure the reliability and durability of my PCB?
To ensure the reliability and durability of your PCB, follow best practices in design, such as using appropriate component ratings, providing adequate cooling, and adhering to manufacturing guidelines. Thorough testing and validation, including environmental stress testing, can also help identify potential issues and improve the overall reliability of the board.
Conclusion
PCB development is a complex, multi-stage process that requires expertise in electronic design, materials science, and manufacturing techniques. By understanding the fundamentals of PCBs, the stages of the development process, and the best practices and common challenges involved, designers and manufacturers can create reliable, high-performance electronic devices that meet the ever-increasing demands of the modern world.
As technology continues to advance, the PCB development process will also evolve, incorporating new materials, manufacturing techniques, and design methodologies. By staying informed and adaptable, the electronics industry can continue to drive innovation and shape the future of technology.
Leave a Reply