Understanding Impedance in PCBs
Impedance is a measure of the opposition that a circuit presents to a current when a voltage is applied. In the context of PCBs, impedance is determined by the physical characteristics of the traces, such as width, thickness, spacing, and the properties of the dielectric material. Controlled impedance PCB design aims to maintain a consistent impedance value along the signal path to ensure optimal signal quality and minimize signal distortion.
Types of Impedance in PCBs
There are two main types of impedance in PCBs:
-
Characteristic Impedance (Z0): This is the impedance of a transmission line in a PCB, which is determined by the geometry of the trace and the properties of the dielectric material. The characteristic impedance is essential for maintaining signal integrity and minimizing reflections.
-
Differential Impedance: Differential impedance is the impedance between two coupled traces in a PCB, such as in a differential pair. It is crucial for maintaining signal integrity in high-speed differential signaling applications, such as USB, HDMI, and Ethernet.
Importance of Controlled Impedance in PCB Design
Controlled impedance PCB design is essential for several reasons:
-
Signal Integrity: By maintaining a consistent impedance along the signal path, controlled impedance PCBs minimize signal reflections, distortions, and crosstalk. This ensures that the transmitted signals reach their destination with minimal degradation, reducing the risk of data corruption and errors.
-
EMI Reduction: Controlled impedance PCBs help reduce electromagnetic interference (EMI) by minimizing the radiation of high-frequency signals. This is particularly important in applications that must comply with strict EMI regulations, such as medical devices and automotive electronics.
-
High-Speed Applications: As digital systems operate at increasingly higher frequencies, the need for controlled impedance PCBs becomes more critical. Proper impedance control ensures that high-speed signals can propagate through the PCB without significant losses or distortions, enabling faster data transfer rates and improved system performance.
Designing for Controlled Impedance
Designing a controlled impedance PCB involves several key considerations:
Stack-up Design
The PCB stack-up refers to the arrangement of copper layers, dielectric materials, and their thicknesses. A well-designed stack-up is crucial for achieving controlled impedance. Factors to consider include:
- The number of copper layers
- The thickness of each copper layer
- The type and thickness of dielectric materials
- The placement of signal, ground, and power planes
Trace Geometry
The geometry of the PCB traces directly affects their impedance. Key parameters include:
- Trace width
- Trace thickness
- Spacing between traces
- Distance from traces to reference planes (e.g., ground or power planes)
To achieve the desired impedance, designers must carefully calculate and adjust these parameters based on the dielectric properties of the PCB substrate.
Dielectric Material Selection
The choice of dielectric material significantly impacts the impedance of PCB traces. Important dielectric properties include:
- Dielectric constant (Dk)
- Dissipation factor (Df)
- Thickness tolerance
- Thermal stability
Common dielectric materials for controlled impedance PCBs include FR-4, Rogers, and Isola substrates, each with unique properties suited for different applications.
Impedance Calculation and Simulation
To design a controlled impedance PCB, engineers use specialized software tools to calculate and simulate the impedance of traces based on the stack-up, trace geometry, and dielectric properties. These tools help optimize the design and ensure that the target impedance is achieved across the entire signal path.
Some popular impedance calculation and simulation software include:
- Polar SI9000
- Mentor Graphics HyperLynx
- Cadence Allegro PCB SI
- Altium Designer
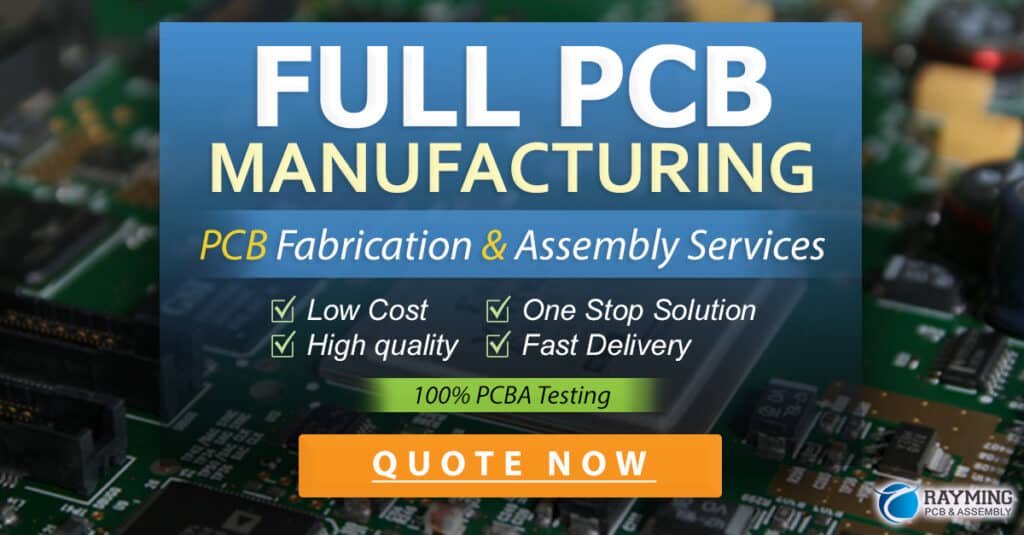
Manufacturing Controlled Impedance PCBs
Manufacturing controlled impedance PCBs requires strict process control and specialized equipment to ensure that the design specifications are met consistently. Key aspects of the manufacturing process include:
Impedance Control Methods
There are two primary methods for controlling impedance during PCB manufacturing:
-
Trace Width Control: This method involves adjusting the width of the PCB traces to achieve the target impedance. The manufacturing process must maintain tight tolerances on trace width to ensure consistent impedance across the board.
-
Dielectric Thickness Control: This method involves adjusting the thickness of the dielectric material to achieve the target impedance. Precise control of the dielectric thickness is critical for maintaining consistent impedance.
Process Control
To manufacture controlled impedance PCBs consistently, the following process control measures are essential:
- Strict control of copper etching processes to maintain trace width and thickness tolerances
- Precise control of dielectric material thickness and uniformity
- Continuous monitoring and adjustment of manufacturing parameters
- Regular calibration of manufacturing equipment
Material Handling and Storage
Proper handling and storage of PCB materials are crucial for maintaining consistent dielectric properties and ensuring reliable impedance control. This includes:
- Storing materials in a controlled environment with stable temperature and humidity
- Following manufacturer guidelines for material shelf life and handling
- Minimizing exposure to contaminants and moisture
Testing and Verification
After manufacturing, controlled impedance PCBs must undergo rigorous testing and verification to ensure that they meet the specified impedance requirements. Common testing methods include:
Time Domain Reflectometry (TDR)
TDR is a widely used technique for measuring impedance in PCBs. It involves sending a fast-rising pulse through the trace and analyzing the reflected signal to determine the impedance profile along the trace. TDR can identify impedance discontinuities, mismatches, and other anomalies that may affect signal integrity.
Frequency Domain Measurements
Frequency domain measurements, such as S-parameter measurements, can be used to characterize the impedance of PCB traces over a wide range of frequencies. This is particularly useful for RF and high-speed digital applications, where the impedance behavior across the operating frequency range is critical.
Manufacturing Test Coupons
Test coupons are small pcb sections that are manufactured alongside the main board and are used for destructive impedance testing. These coupons have the same stack-up and trace geometry as the main board and are used to verify that the manufacturing process is achieving the desired impedance consistently.
Frequently Asked Questions (FAQ)
-
What is the difference between controlled impedance and regular PCBs?
Controlled impedance PCBs are designed and manufactured to maintain a specific impedance value along the signal path, while regular PCBs do not have strict impedance requirements. Controlled impedance PCBs are essential for high-speed digital, RF, and telecommunications applications, where signal integrity is critical. -
How does the dielectric constant affect PCB impedance?
The dielectric constant (Dk) of the PCB substrate material directly affects the impedance of the traces. A higher Dk value results in lower impedance, while a lower Dk value leads to higher impedance. The dielectric constant must be carefully considered when designing controlled impedance PCBs to ensure that the target impedance is achieved. -
What are the most common impedance values used in PCB design?
Common controlled impedance values in PCB design include: - 50 ohms: Widely used in RF and high-speed digital applications
- 75 ohms: Used in video and cable television applications
- 90 ohms and 100 ohms: Used in differential signaling applications, such as USB and Ethernet
-
110 ohms: Used in some telecommunications applications
-
Why is impedance matching important in PCB design?
Impedance matching is crucial in PCB design to minimize signal reflections and ensure maximum power transfer between the source and the load. When the impedance of the source, transmission line (PCB trace), and load are matched, signal reflections are minimized, and signal integrity is maintained. Impedance mismatches can lead to signal distortions, reduced signal strength, and increased EMI. -
How can I ensure consistent impedance control in high-volume PCB production?
To ensure consistent impedance control in high-volume PCB production, consider the following: - Implement strict process controls and monitor manufacturing parameters closely
- Use statistical process control (SPC) techniques to identify and correct process deviations
- Regularly calibrate and maintain manufacturing equipment
- Conduct frequent impedance testing using test coupons and TDR measurements
- Collaborate closely with your PCB manufacturer and communicate your impedance requirements clearly
Conclusion
Controlled impedance PCB design is a critical aspect of modern electronics manufacturing, particularly in high-speed digital, RF, and telecommunications applications. By maintaining a consistent impedance along the signal path, controlled impedance PCBs ensure signal integrity, minimize reflections, and reduce EMI. Designing and manufacturing controlled impedance PCBs requires careful consideration of the stack-up, trace geometry, dielectric materials, and manufacturing processes. Rigorous testing and verification, using methods such as TDR and frequency domain measurements, are essential for ensuring that the manufactured PCBs meet the specified impedance requirements. As electronic systems continue to push the boundaries of speed and performance, the importance of controlled impedance PCB design will only continue to grow.
Leave a Reply