The Importance of Outer layer etching in PCB Manufacturing
Outer layer etching plays a vital role in the production of high-quality PCBs. Some of the key reasons why this process is so important include:
- Creating electrical connections: Outer layer etching allows for the creation of precise electrical connections between components on the PCB.
- Ensuring proper functionality: By removing unwanted copper and creating the desired patterns, outer layer etching ensures that the PCB will function as intended.
- Improving reliability: Properly etched outer layers contribute to the overall reliability and durability of the PCB.
- Enabling miniaturization: Outer layer etching allows for the creation of fine features and small traces, enabling the miniaturization of electronic devices.
The Outer Layer Etching Process
The outer layer etching process typically involves several steps, including:
- Cleaning: The PCB is thoroughly cleaned to remove any contaminants that could interfere with the etching process.
- Applying a photoresist: A light-sensitive material called photoresist is applied to the outer layers of the PCB.
- Exposure: The photoresist is exposed to light through a photomask, which contains the desired pattern for the copper traces.
- Developing: The exposed photoresist is developed, removing the areas that were exposed to light and leaving behind a protective layer in the desired pattern.
- Etching: The PCB is immersed in an etching solution, which removes the copper that is not protected by the photoresist.
- Stripping: The remaining photoresist is stripped away, leaving behind the etched copper pattern.
Cleaning
Before the outer layer etching process can begin, the PCB must be thoroughly cleaned to remove any contaminants that could interfere with the process. This typically involves using a combination of chemical and mechanical cleaning methods, such as:
- Degreasing: The PCB is immersed in a degreasing solution to remove oils, greases, and other organic contaminants.
- Micro-etching: A mild etching solution is used to remove any oxides or surface contaminants from the copper.
- Mechanical scrubbing: The PCB may be mechanically scrubbed to remove any remaining contaminants.
Applying a Photoresist
Once the PCB is clean, a light-sensitive material called photoresist is applied to the outer layers. This is typically done using one of two methods:
- Dry film photoresist: A pre-made film of photoresist is laminated onto the PCB using heat and pressure.
- Liquid photoresist: A liquid photoresist is applied to the PCB using a spin coating process, which ensures an even coating.
The type of photoresist used will depend on factors such as the desired feature size, the type of etching process being used, and the manufacturing capabilities of the PCB fabricator.
Exposure
After the photoresist has been applied, it is exposed to light through a photomask. The photomask contains the desired pattern for the copper traces and is typically made of glass or film with opaque and transparent areas.
During exposure, the areas of the photoresist that are exposed to light undergo a chemical change, making them more soluble in the developer solution. The exposure process is critical to the success of the outer layer etching process, as it determines the accuracy and resolution of the final copper pattern.
Developing
After exposure, the PCB is immersed in a developer solution, which removes the areas of the photoresist that were exposed to light. This leaves behind a protective layer of photoresist in the desired pattern.
The developing process must be carefully controlled to ensure that the correct amount of photoresist is removed. Over-developing can lead to the loss of fine features, while under-developing can result in incomplete etching.
Etching
With the desired pattern now protected by the photoresist, the PCB is ready for etching. The etching process involves immersing the PCB in an etching solution, which chemically removes the copper that is not protected by the photoresist.
There are several types of etching solutions that can be used, including:
- Ferric chloride: A common etching solution that is effective for removing copper.
- Cupric chloride: Another popular etching solution that is known for its ability to produce fine features.
- Alkaline etchants: These etchants are less common but can be used for specific applications.
The choice of etching solution will depend on factors such as the type of copper being etched, the desired etch rate, and the environmental and safety considerations.
During the etching process, the PCB is typically agitated to ensure that the etching solution is evenly distributed and to prevent the formation of gas bubbles, which can interfere with the etching process.
Stripping
After etching, the remaining photoresist is no longer needed and must be removed from the PCB. This is typically done using a stripping solution, which chemically dissolves the photoresist.
The stripping process must be carefully controlled to ensure that all of the photoresist is removed without damaging the newly etched copper features. Any remaining photoresist can interfere with subsequent processing steps and impact the reliability of the final PCB.
Types of Outer Layer Etching
There are two main types of outer layer etching: subtractive etching and pattern plating.
Subtractive Etching
Subtractive etching is the most common type of outer layer etching and involves the selective removal of copper from a fully copper-clad PCB. The process follows the steps outlined above, with the photoresist being applied to the entire copper surface and then selectively removed to expose the areas to be etched.
Subtractive etching is known for its simplicity and versatility, as it can be used to create a wide range of feature sizes and shapes. However, it can be more wasteful than pattern plating, as a significant amount of copper is removed during the etching process.
Pattern Plating
Pattern plating, also known as additive etching, involves the selective deposition of copper onto the PCB rather than the removal of copper. In this process, a thin layer of copper is first deposited onto the entire PCB surface. A photoresist is then applied and exposed, leaving behind a protective layer in the areas where copper is not desired.
The PCB is then electroplated with additional copper, which only adheres to the areas not protected by the photoresist. Finally, the photoresist is stripped away, leaving behind the desired copper pattern.
Pattern plating is known for its ability to create very fine features and its material efficiency, as less copper is wasted compared to subtractive etching. However, it can be more complex and time-consuming than subtractive etching.
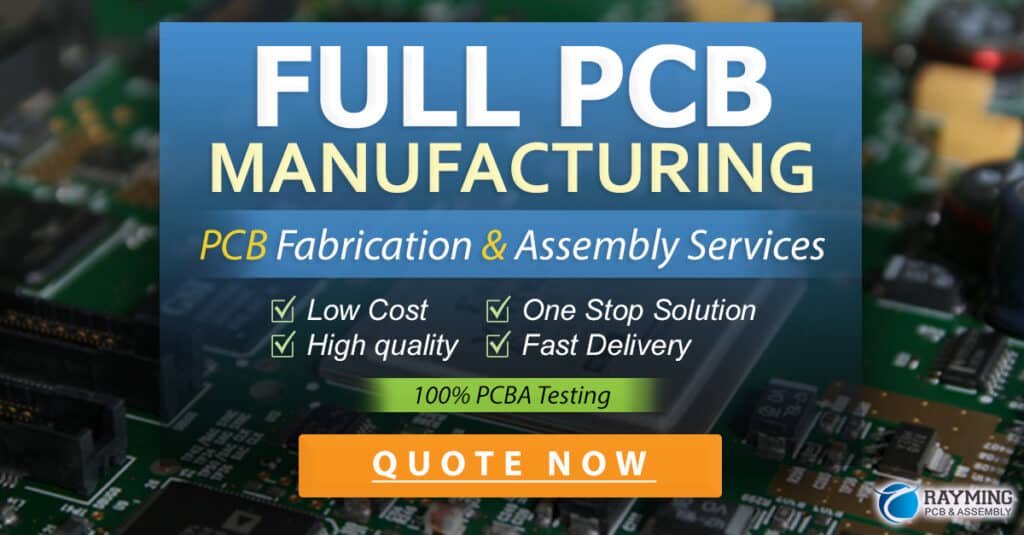
Factors Affecting Outer Layer Etching Quality
Several factors can impact the quality of the outer layer etching process, including:
- Copper thickness: The thickness of the copper on the PCB can affect the etching time and the resolution of the final features.
- Etchant type and concentration: The type and concentration of the etching solution can impact the etch rate and the quality of the etched features.
- Etching temperature: Higher temperatures can increase the etch rate but may also lead to undercutting or over-etching.
- Agitation: Proper agitation is necessary to ensure an even distribution of the etching solution and to prevent gas bubbles from interfering with the etching process.
- Photoresist quality: The quality and consistency of the photoresist can impact the resolution and accuracy of the final etched features.
Challenges in Outer Layer Etching
Despite advancements in technology and process control, outer layer etching still presents several challenges for PCB manufacturers. Some of these challenges include:
- Miniaturization: As electronic devices continue to shrink in size, PCB manufacturers must be able to create ever-smaller features and traces. This requires precise control over the etching process and the use of advanced materials and technologies.
- Material compatibility: The increasing use of advanced materials, such as high-frequency laminates and flexible substrates, can present challenges for outer layer etching. These materials may require specialized etching solutions or process modifications to ensure proper etching.
- Environmental concerns: Traditional etching solutions, such as ferric chloride, can be harmful to the environment and present disposal challenges. PCB manufacturers are increasingly looking for more environmentally friendly alternatives, such as cupric chloride or alkaline etchants.
- Process control: Maintaining consistent process control is essential for producing high-quality PCBs. This requires strict monitoring and control of factors such as etchant concentration, temperature, and agitation.
Advancements in Outer Layer Etching Technology
To address these challenges and improve the efficiency and quality of outer layer etching, PCB manufacturers are turning to advanced technologies and processes. Some of these advancements include:
- Direct imaging: Direct imaging technology allows for the direct transfer of the circuit pattern onto the photoresist, eliminating the need for a photomask. This can improve the accuracy and resolution of the etched features and reduce process time.
- Laser direct imaging (LDI): LDI uses a laser to directly expose the photoresist, allowing for even finer feature sizes and improved accuracy.
- Plasma etching: Plasma etching uses a plasma to remove the copper, rather than a chemical etching solution. This can provide better control over the etching process and reduce the environmental impact.
- Inkjet printing: Inkjet printing technology can be used to selectively deposit a protective ink onto the PCB, replacing the need for a photoresist. This can simplify the etching process and reduce material waste.
The Future of Outer Layer Etching
As the demand for smaller, more complex electronic devices continues to grow, outer layer etching will remain a critical process in PCB manufacturing. To meet these demands, PCB manufacturers will need to continue to invest in advanced technologies and processes that can improve the accuracy, efficiency, and environmental sustainability of outer layer etching.
Some of the trends and developments that are likely to shape the future of outer layer etching include:
- Increased adoption of additive manufacturing: Additive manufacturing technologies, such as 3D printing, may play a larger role in PCB manufacturing in the future. These technologies could potentially replace traditional etching processes for certain applications.
- Development of new materials: The development of new, high-performance materials for PCBs will require corresponding advancements in outer layer etching processes to ensure compatibility and optimal results.
- Emphasis on sustainability: As environmental concerns continue to grow, there will be an increasing emphasis on developing and adopting more sustainable outer layer etching processes and materials.
- Integration of artificial intelligence (AI) and machine learning: AI and machine learning technologies may be used to optimize and automate outer layer etching processes, improving efficiency and reducing the potential for human error.
Frequently Asked Questions (FAQ)
-
What is the difference between subtractive and pattern plating etching?
Subtractive etching involves the selective removal of copper from a fully copper-clad PCB, while pattern plating involves the selective deposition of copper onto the PCB. Subtractive etching is more common and versatile, while pattern plating can create finer features and is more material-efficient. -
What factors can affect the quality of outer layer etching?
Factors that can affect the quality of outer layer etching include copper thickness, etchant type and concentration, etching temperature, agitation, and photoresist quality. Precise control over these factors is necessary to ensure high-quality results. -
What are some of the challenges in outer layer etching?
Challenges in outer layer etching include miniaturization, material compatibility, environmental concerns, and maintaining consistent process control. As PCBs become smaller and more complex, these challenges will continue to drive advancements in outer layer etching technology. -
What are some of the advanced technologies being used in outer layer etching?
Advanced technologies being used in outer layer etching include direct imaging, laser direct imaging (LDI), plasma etching, and inkjet printing. These technologies can improve the accuracy, efficiency, and environmental sustainability of the etching process. -
How is the future of outer layer etching likely to evolve?
The future of outer layer etching is likely to be shaped by trends such as the increased adoption of additive manufacturing, the development of new PCB materials, an emphasis on sustainability, and the integration of AI and machine learning technologies. These developments will help PCB manufacturers meet the growing demand for smaller, more complex electronic devices.
In conclusion, outer layer etching is a critical process in the manufacturing of PCBs, enabling the creation of precise electrical connections and patterns that ensure the proper functionality and reliability of electronic devices. As the electronics industry continues to evolve, outer layer etching technologies and processes will need to advance to keep pace with the demands for smaller, more complex, and more sustainable PCBs.
Leave a Reply