Definition and Function of the Outer Annular Ring
An Outer Annular Ring is a circular structure that is positioned around the outer periphery of a mechanical system, such as a bearing or a gear assembly. Its primary function is to provide support and stability to the system, as well as to facilitate the smooth rotation of the moving parts. The OAR is designed to withstand the forces and stresses generated during the operation of the machinery, ensuring that the system remains stable and efficient.
Applications of the Outer Annular Ring
The Outer Annular Ring finds applications in various industries, including:
1. Aerospace Industry
In the aerospace industry, OARs are used in the construction of aircraft engines, landing gear, and other critical components. These rings help to distribute the loads evenly and provide the necessary support to the system, ensuring that the aircraft operates safely and efficiently.
2. Automotive Industry
In the automotive industry, Outer Annular Rings are used in the manufacturing of vehicle transmissions, drivetrain components, and wheel bearings. They help to reduce friction and wear, while also providing the necessary support to the moving parts, resulting in improved vehicle performance and fuel efficiency.
3. Industrial Machinery
OARs are also used in various industrial machinery, such as pumps, compressors, and turbines. They help to maintain the alignment of the rotating components and prevent excessive vibrations, which can lead to premature wear and failure of the machinery.
Advantages of Using Outer Annular Rings
The use of Outer Annular Rings in mechanical systems offers several advantages, including:
-
Enhanced Stability: OARs provide the necessary support and stability to the system, ensuring that the moving parts remain aligned and function efficiently.
-
Reduced Friction and Wear: The use of OARs helps to reduce friction and wear between the moving parts, resulting in increased component life and reduced maintenance costs.
-
Improved Load Distribution: Outer Annular Rings help to distribute the loads evenly across the system, preventing excessive stress on any particular component and enhancing the overall performance of the machinery.
-
Versatility: OARs can be customized to suit the specific requirements of different mechanical systems, making them highly versatile and adaptable to various applications.
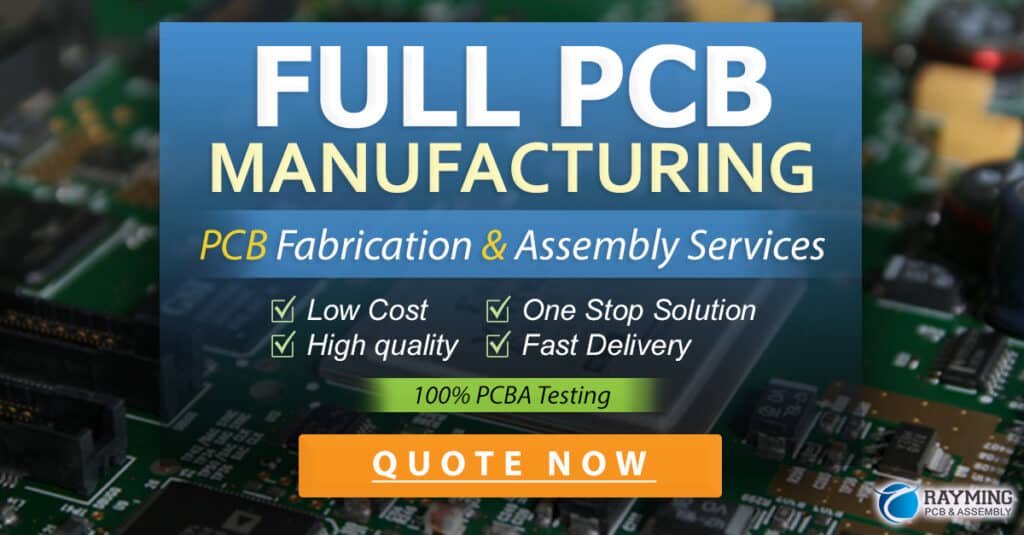
Materials Used in Manufacturing Outer Annular Rings
The choice of material for manufacturing an Outer Annular Ring depends on the specific application and the operating conditions of the mechanical system. Some of the commonly used materials include:
1. Steel
Steel is the most widely used material for manufacturing OARs due to its high strength, durability, and cost-effectiveness. Different grades of steel, such as carbon steel, alloy steel, and stainless steel, can be used depending on the specific requirements of the application.
2. Aluminum
Aluminum is another popular material for manufacturing OARs, particularly in applications where weight reduction is crucial, such as in the aerospace industry. Aluminum OARs offer excellent corrosion resistance and good thermal conductivity, making them suitable for use in high-temperature environments.
3. Titanium
Titanium is a high-strength, lightweight material that is often used in the manufacturing of OARs for critical applications, such as in aerospace and defense industries. Titanium OARs offer excellent corrosion resistance and can withstand extreme temperatures and pressures.
4. Composites
Composite materials, such as carbon fiber and glass fiber reinforced polymers, are increasingly being used in the manufacturing of OARs for specialized applications. These materials offer high strength-to-weight ratios, excellent fatigue resistance, and good dimensional stability, making them suitable for use in demanding operating conditions.
Manufacturing Process of Outer Annular Rings
The manufacturing process of Outer Annular Rings involves several steps, including:
-
Material Selection: The first step in the manufacturing process is to select the appropriate material for the OAR based on the specific application and operating conditions.
-
Forging or Casting: Depending on the material and the size of the OAR, the ring can be either forged or cast. Forging involves shaping the material using compressive forces, while casting involves pouring molten metal into a mold and allowing it to solidify.
-
Machining: Once the basic shape of the OAR is obtained through forging or casting, it undergoes machining to achieve the desired dimensions and tolerances. This process involves turning, milling, drilling, and grinding operations.
-
Heat Treatment: The machined OAR may undergo heat treatment to improve its mechanical properties, such as hardness, strength, and toughness. The specific heat treatment process depends on the material used and the desired properties.
-
Surface Finishing: The final step in the manufacturing process is surface finishing, which involves processes such as polishing, coating, or plating to improve the appearance and corrosion resistance of the OAR.
Quality Control and Testing
To ensure the quality and reliability of Outer Annular Rings, manufacturers employ various quality control and testing procedures. These include:
-
Dimensional Inspection: The dimensions of the OAR are checked using precision measuring instruments to ensure that they meet the specified tolerances.
-
Non-Destructive Testing (NDT): NDT methods, such as ultrasonic testing, magnetic particle inspection, and radiography, are used to detect any internal defects or discontinuities in the OAR.
-
Mechanical Testing: Mechanical tests, such as tensile testing, hardness testing, and fatigue testing, are conducted to evaluate the mechanical properties of the OAR and ensure that it meets the required performance standards.
-
Metallurgical Testing: Metallurgical tests, such as chemical composition analysis and microstructure examination, are performed to verify the material properties of the OAR and ensure that it meets the specified requirements.
Innovations and Future Trends
As the demand for high-performance mechanical systems continues to grow, manufacturers are constantly seeking ways to improve the design and performance of Outer Annular Rings. Some of the recent innovations and future trends in this field include:
-
Advanced Materials: Researchers are exploring the use of advanced materials, such as ceramic matrix composites and metal matrix composites, for manufacturing OARs with improved thermal stability, wear resistance, and strength-to-weight ratios.
-
Additive Manufacturing: Additive manufacturing techniques, such as 3D printing, are being investigated for the production of OARs with complex geometries and customized properties, which can lead to improved performance and reduced manufacturing costs.
-
Intelligent Monitoring Systems: The integration of sensors and intelligent monitoring systems into OARs can enable real-time monitoring of the system’s performance and health, allowing for predictive maintenance and improved operational efficiency.
-
Lightweight Design: The development of lightweight OARs using advanced materials and optimized designs can help to reduce the overall weight of mechanical systems, leading to improved fuel efficiency and reduced environmental impact.
Frequently Asked Questions (FAQ)
-
What is the primary function of an Outer Annular Ring?
The primary function of an Outer Annular Ring is to provide support and stability to a mechanical system, while facilitating the smooth rotation of the moving parts. -
In which industries are Outer Annular Rings commonly used?
Outer Annular Rings are commonly used in the aerospace, automotive, and industrial machinery industries. -
What are the advantages of using Outer Annular Rings in mechanical systems?
The advantages of using Outer Annular Rings include enhanced stability, reduced friction and wear, improved load distribution, and versatility in design. -
What materials are commonly used for manufacturing Outer Annular Rings?
Common materials used for manufacturing Outer Annular Rings include steel, aluminum, titanium, and composite materials, such as carbon fiber and glass fiber reinforced polymers. -
What quality control and testing procedures are employed to ensure the reliability of Outer Annular Rings?
Quality control and testing procedures for Outer Annular Rings include dimensional inspection, non-destructive testing, mechanical testing, and metallurgical testing.
Conclusion
The Outer Annular Ring is a critical component in the design and construction of various mechanical systems, playing a vital role in ensuring their proper functioning, stability, and longevity. With its wide range of applications in industries such as aerospace, automotive, and industrial machinery, the OAR has become an indispensable part of modern engineering.
As the demand for high-performance mechanical systems continues to grow, manufacturers are constantly seeking ways to improve the design and performance of Outer Annular Rings through the use of advanced materials, innovative manufacturing techniques, and intelligent monitoring systems. By staying at the forefront of these developments, engineers and manufacturers can ensure that the Outer Annular Ring remains a key component in the evolution of mechanical systems for years to come.
Leave a Reply