Introduction to OSP in PCB
OSP, or Organic Solderability Preservative, is a surface finish that is commonly used in the manufacturing of printed circuit boards (PCBs). It is a cost-effective and environmentally friendly alternative to other surface finishes such as Hot Air Solder Leveling (HASL), Electroless Nickel Immersion Gold (ENIG), and Immersion Silver (IAg).
What is OSP?
OSP is a chemical coating that is applied to the copper surfaces of a PCB to prevent oxidation and maintain solderability. It is a thin, transparent layer that is typically composed of organic compounds such as imidazoles, benzotriazoles, and other proprietary ingredients.
How does OSP work?
The OSP coating works by forming a protective barrier on the copper surface of the PCB. This barrier prevents the copper from reacting with oxygen and other contaminants in the environment, which can cause oxidation and reduce solderability.
Advantages of OSP
OSP has several advantages over other surface finishes, including:
- Cost-effectiveness: OSP is one of the most affordable surface finishes available, making it a popular choice for high-volume production.
- Environmental friendliness: OSP is a lead-free and halogen-free surface finish, making it a more environmentally friendly option than other finishes that contain toxic substances.
- Good solderability: OSP provides good solderability and wettability, ensuring reliable solder joints.
- Flatness: OSP has a very thin coating, which helps to maintain the flatness of the PCB and prevent warping.
Disadvantages of OSP
Despite its many advantages, OSP also has some disadvantages, including:
- Limited shelf life: OSP has a limited shelf life compared to other surface finishes, typically around 6-12 months depending on storage conditions.
- Sensitivity to handling: OSP is sensitive to handling and can be easily contaminated or damaged, which can reduce its effectiveness.
- Not suitable for all applications: OSP may not be suitable for certain applications that require a more robust surface finish, such as high-temperature or high-reliability applications.
OSP vs. Other Surface Finishes
OSP is just one of many surface finishes available for PCBs. Here is a comparison of OSP with some of the other common surface finishes:
Surface Finish | Advantages | Disadvantages |
---|---|---|
OSP | Cost-effective, environmentally friendly, good solderability, flat | Limited shelf life, sensitive to handling, not suitable for all applications |
HASL | Low cost, good solderability, easy to inspect | Not suitable for fine-pitch components, can cause thermal shock, contains lead |
ENIG | Excellent solderability, long shelf life, suitable for fine-pitch components | Expensive, can cause black pad, contains nickel |
IAg | Good solderability, long shelf life, suitable for fine-pitch components | Expensive, can tarnish over time, not suitable for high-temperature applications |
OSP vs. HASL
HASL is another common surface finish that is often compared to OSP. While HASL is low cost and provides good solderability, it has some disadvantages compared to OSP. HASL involves dipping the PCB in molten solder, which can cause thermal shock and damage to the board. It also contains lead, which is a toxic substance that is being phased out in many countries. Additionally, HASL is not suitable for fine-pitch components due to the unevenness of the solder coating.
OSP vs. ENIG
ENIG is a high-end surface finish that provides excellent solderability and a long shelf life. However, it is also one of the most expensive surface finishes available. ENIG involves plating the copper surface with a layer of nickel and then a thin layer of gold. While this provides excellent protection against oxidation and corrosion, it can also cause a phenomenon known as “black pad,” where the nickel layer separates from the copper surface.
OSP vs. IAg
IAg is another high-end surface finish that provides good solderability and a long shelf life. Like ENIG, it is also more expensive than OSP. IAg involves plating the copper surface with a thin layer of silver. While this provides good protection against oxidation, it can also tarnish over time and is not suitable for high-temperature applications.
OSP Application Process
The OSP application process involves several steps to ensure a high-quality finish. Here is a general overview of the process:
Cleaning
The first step in the OSP application process is to thoroughly clean the PCB to remove any contaminants or residues that may interfere with the coating. This typically involves a combination of chemical and mechanical cleaning processes.
Microetching
After cleaning, the PCB is often subjected to a microetching process to roughen the copper surface and improve adhesion of the OSP coating. This involves dipping the PCB in a mild acid solution for a short period of time.
OSP Application
The actual OSP coating is applied using a dipping process. The PCB is dipped into a bath containing the OSP solution for a specific amount of time and at a specific temperature. The exact parameters of the dipping process depend on the specific OSP formulation being used.
Drying
After the OSP coating is applied, the PCB is dried using hot air or infrared heating to remove any excess moisture and ensure a uniform coating.
Inspection
Finally, the PCB is inspected to ensure that the OSP coating is of high quality and free of defects. This may involve visual inspection, thickness measurements, and other quality control tests.
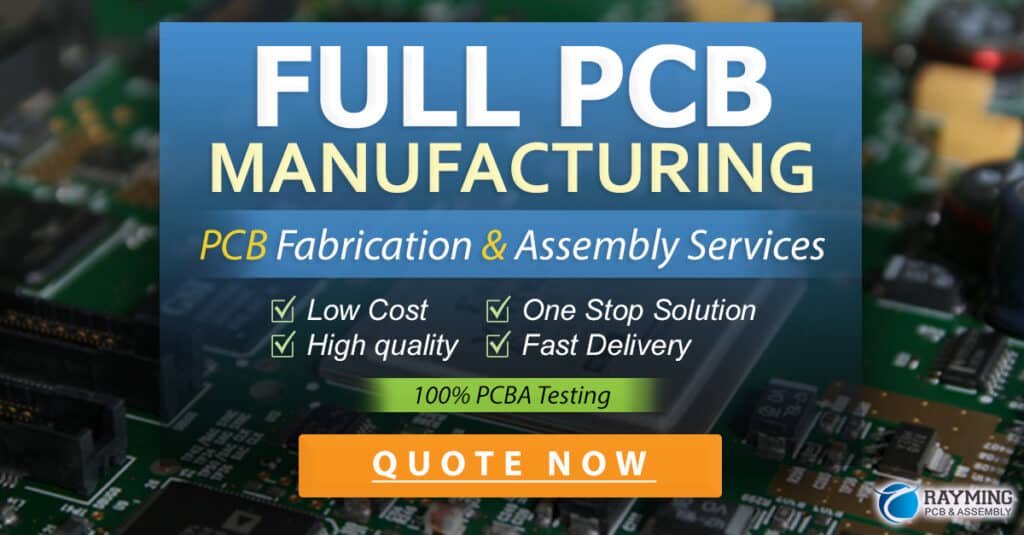
OSP Handling and Storage
To ensure the effectiveness and longevity of the OSP coating, proper handling and storage procedures must be followed.
Handling
OSP-coated PCBs should be handled with care to avoid contamination or damage to the coating. This includes:
- Wearing gloves to avoid transferring oils and other contaminants from the skin to the PCB surface.
- Avoiding touching the OSP-coated areas of the PCB as much as possible.
- Using proper ESD (electrostatic discharge) protection measures to prevent damage from static electricity.
Storage
OSP-coated PCBs should be stored in a cool, dry environment to prevent degradation of the coating. This includes:
- Storing PCBs in sealed bags or containers with desiccants to absorb moisture.
- Avoiding exposure to direct sunlight or other sources of UV light, which can cause the OSP coating to deteriorate.
- Storing PCBs at a temperature between 20-30°C (68-86°F) and a relative humidity of less than 60%.
Shelf Life
As mentioned earlier, OSP has a limited shelf life compared to other surface finishes. The exact shelf life depends on the specific OSP formulation and storage conditions, but is typically around 6-12 months.
To ensure the best possible solderability, it is recommended to use OSP-coated PCBs as soon as possible after manufacturing. If the PCBs need to be stored for an extended period of time, they should be stored in optimal conditions and tested for solderability before use.
Frequently Asked Questions (FAQ)
1. Is OSP suitable for all PCB applications?
No, OSP may not be suitable for certain applications that require a more robust surface finish, such as high-temperature or high-reliability applications. In these cases, other surface finishes such as ENIG or IAg may be more appropriate.
2. Can OSP be used with lead-free solder?
Yes, OSP is compatible with lead-free solder and is often used in lead-free PCB assembly processes.
3. How long does the OSP coating last?
The shelf life of OSP is typically around 6-12 months, depending on the specific formulation and storage conditions. After this time, the solderability of the coating may degrade and the PCBs may need to be reworked or replaced.
4. Can OSP be reworked if it becomes contaminated or damaged?
Yes, OSP can be stripped and reapplied if necessary. However, this process can be time-consuming and may not be cost-effective for large-scale production.
5. Is OSP more environmentally friendly than other surface finishes?
Yes, OSP is generally considered to be a more environmentally friendly option than other surface finishes that contain toxic substances such as lead or nickel. However, the environmental impact of OSP still depends on the specific chemicals used in the coating and the disposal methods employed.
Conclusion
In conclusion, OSP is a popular and cost-effective surface finish for PCBs that provides good solderability and environmental friendliness. While it has some limitations compared to other surface finishes, such as a limited shelf life and sensitivity to handling, it remains a viable option for many PCB applications.
When considering OSP for a PCB design, it is important to carefully evaluate the specific requirements of the application and weigh the advantages and disadvantages of OSP against other surface finishes. Proper handling and storage procedures must also be followed to ensure the effectiveness and longevity of the OSP coating.
As with any PCB manufacturing process, it is recommended to work with an experienced and reliable PCB manufacturer who can provide guidance and support in selecting the best surface finish for a given application.
Leave a Reply