Characteristics of Orange PCBs
Color and Appearance
The most distinguishing feature of orange PCBs is their vibrant orange color. This color is achieved through the use of a specific solder mask, which is a protective layer applied to the copper traces on the PCB. The orange solder mask not only provides a unique aesthetic appeal but also serves important functional purposes.
Solder Mask Properties
The orange solder mask used in orange PCBs possesses several key properties that contribute to its performance and reliability:
- Insulation: The solder mask acts as an insulating layer, preventing short circuits and protecting the copper traces from damage.
- Durability: Orange solder masks are known for their durability and resistance to wear and tear, ensuring the longevity of the PCB.
- Solderability: The solder mask is designed to allow for easy and reliable soldering of components onto the PCB.
- Contrast: The orange color provides excellent contrast against the copper traces, making it easier to inspect and troubleshoot the PCB.
Copper Thickness
Orange PCBs can be manufactured with various copper thicknesses, depending on the specific requirements of the application. The most common copper thicknesses used in orange PCBs are:
Copper Thickness (oz) | Thickness (mm) |
---|---|
0.5 oz | 0.018 mm |
1 oz | 0.035 mm |
2 oz | 0.070 mm |
3 oz | 0.105 mm |
The choice of copper thickness depends on factors such as current carrying capacity, heat dissipation, and mechanical strength required for the PCB.
Manufacturing Process of Orange PCBs
The manufacturing process of orange PCBs involves several steps, each critical to ensuring the quality and reliability of the final product.
PCB Design
The first step in manufacturing an orange PCB is designing the circuit layout using specialized PCB design software. The design includes the placement of components, routing of copper traces, and the creation of solder mask and silkscreen layers.
PCB Fabrication
Once the design is finalized, the PCB fabrication process begins. This involves several sub-steps:
- Substrate Preparation: The PCB substrate, typically made of fiberglass or other insulating materials, is cut to the required size and shape.
- Copper Lamination: Copper foil is laminated onto the substrate using heat and pressure.
- Drilling: Holes are drilled into the PCB for component mounting and vias.
- Plating: The drilled holes are plated with copper to establish electrical connectivity between layers.
- Etching: Unwanted copper is etched away, leaving behind the desired copper traces.
- Solder Mask Application: The orange solder mask is applied to the PCB, covering the copper traces while leaving the pads exposed.
- Silkscreen Printing: The silkscreen layer, which includes component labels and other markings, is printed onto the solder mask.
- Surface Finish: A surface finish, such as HASL (Hot Air Solder Leveling) or ENIG (Electroless Nickel Immersion Gold), is applied to the exposed pads to enhance solderability and protect the copper from oxidation.
PCB Assembly
After the fabrication process, the orange PCB is ready for assembly. This involves soldering components onto the PCB using techniques such as through-hole or surface-mount technology (SMT).
Advantages of Orange PCBs
Orange PCBs offer several advantages over other types of PCBs:
- Visibility: The bright orange color makes it easier to inspect the PCB for defects or issues during manufacturing and troubleshooting.
- Durability: Orange solder masks are known for their durability and resistance to wear and tear, ensuring the longevity of the PCB.
- Aesthetics: The vibrant orange color gives the PCB a distinctive and attractive appearance, which can be desirable in certain applications.
- Solderability: The orange solder mask is designed to allow for easy and reliable soldering of components onto the PCB.
- Insulation: The solder mask provides excellent insulation, protecting the copper traces from damage and preventing short circuits.
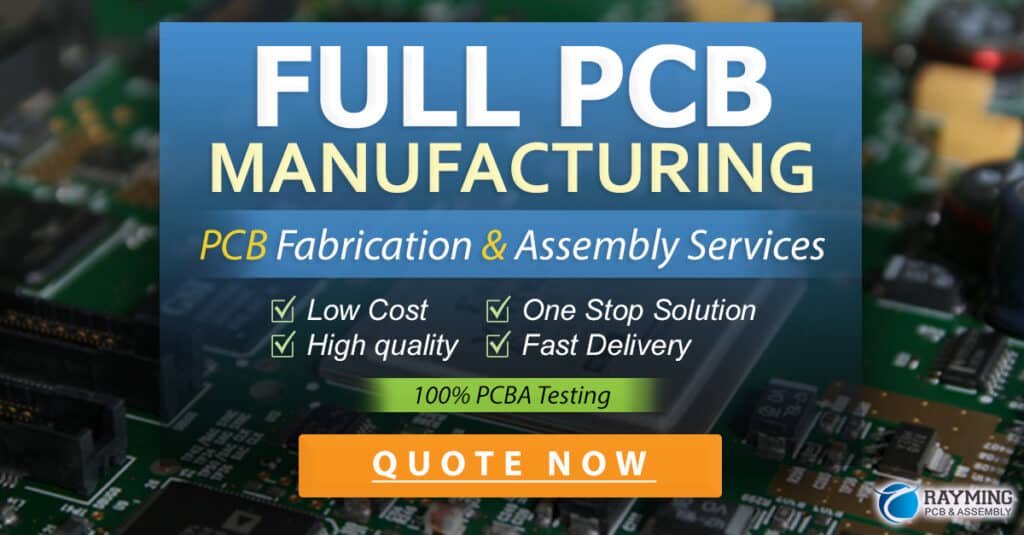
Applications of Orange PCBs
Orange PCBs find applications in a wide range of industries and products:
Consumer Electronics
Orange PCBs are commonly used in consumer electronic devices, such as:
- Smartphones
- Tablets
- Laptops
- Wearable devices
- Gaming consoles
The durability and aesthetic appeal of orange PCBs make them well-suited for these applications.
Industrial Equipment
Orange PCBs are also used in various industrial equipment, including:
- Control systems
- Automation equipment
- Monitoring devices
- Sensors
- Power supplies
The robustness and reliability of orange PCBs make them ideal for the demanding environments found in industrial settings.
Medical Devices
Orange PCBs are used in medical devices, such as:
- Patient monitoring systems
- Diagnostic equipment
- Surgical instruments
- Implantable devices
The high-quality manufacturing process and durability of orange PCBs ensure their suitability for critical medical applications.
Automotive Electronics
Orange PCBs are increasingly used in automotive electronics, including:
- Engine control units (ECUs)
- Infotainment systems
- Advanced driver assistance systems (ADAS)
- Sensors
- Lighting systems
The ability of orange PCBs to withstand harsh environmental conditions and vibrations makes them well-suited for automotive applications.
Frequently Asked Questions (FAQ)
-
Q: What is the difference between orange PCBs and green PCBs?
A: The main difference between orange and green PCBs is the color of the solder mask. Orange PCBs have a vibrant orange solder mask, while green PCBs have a green solder mask. The choice of color is often based on aesthetic preferences or specific application requirements. -
Q: Are orange PCBs more expensive than other types of PCBs?
A: The cost of orange PCBs is generally similar to that of other PCBs with different solder mask colors. The price may vary slightly depending on the specific manufacturer and the volume of the order. -
Q: Can orange PCBs be manufactured with different copper thicknesses?
A: Yes, orange PCBs can be manufactured with various copper thicknesses, typically ranging from 0.5 oz to 3 oz. The choice of copper thickness depends on the specific requirements of the application, such as current carrying capacity and mechanical strength. -
Q: Are orange PCBs suitable for high-temperature applications?
A: Orange PCBs can be suitable for high-temperature applications, depending on the specific solder mask material used. Some specialized orange solder masks are formulated to withstand higher temperatures, making them appropriate for use in demanding environments. -
Q: Can orange PCBs be used in flexible circuit applications?
A: Yes, orange PCBs can be manufactured as flexible circuits, also known as flex PCBs. Flex PCBs with orange solder masks offer the same benefits as rigid orange PCBs, such as durability and aesthetic appeal, while providing the added advantage of flexibility for use in applications where conformity to curved surfaces is required.
Conclusion
Orange PCBs are a unique and versatile type of printed circuit board, characterized by their vibrant orange solder mask. They offer a range of benefits, including excellent visibility, durability, aesthetic appeal, and reliable solderability. The manufacturing process of orange PCBs involves several critical steps, from PCB design to fabrication and assembly, ensuring the production of high-quality and reliable boards.
Orange PCBs find applications in various industries, including consumer electronics, industrial equipment, medical devices, and automotive electronics. Their ability to withstand harsh environments, provide insulation, and offer an attractive appearance makes them a popular choice for a wide range of products.
As technology continues to advance, the demand for high-quality and reliable PCBs, such as orange PCBs, is expected to grow. With their unique characteristics and versatile applications, orange PCBs are well-positioned to meet the evolving needs of the electronics industry.
Leave a Reply