How Metal PCBs Differ from Traditional PCBs
Substrate Material
The primary difference between metal PCBs and traditional PCBs lies in the substrate material. While traditional PCBs use an FR-4 substrate, which is a glass-reinforced epoxy laminate, metal PCBs use a metal substrate, typically aluminum or copper. The metal substrate provides a highly efficient thermal path for heat dissipation, allowing the PCB to maintain a lower operating temperature.
Thermal Management
Metal PCBs excel in thermal management due to their metal substrate. The metal substrate acts as a heat sink, quickly conducting heat away from the components and distributing it evenly across the board. This efficient heat dissipation helps to prevent component overheating, which can lead to reduced performance, shorter lifespan, and even failure.
Dielectric Layer
To electrically isolate the components from the metal substrate, metal PCBs feature a dielectric layer between the metal substrate and the copper circuit layer. The dielectric layer is typically made of a thermally conductive but electrically insulating material, such as aluminum oxide or boron nitride. The thickness and thermal conductivity of the dielectric layer can be optimized to achieve the desired thermal performance.
Advantages of Metal PCBs
-
Enhanced Thermal Management: Metal PCBs provide superior heat dissipation compared to traditional PCBs, allowing for better thermal management of high-power components.
-
Improved Reliability: By maintaining lower operating temperatures, metal PCBs can help to increase the reliability and lifespan of electronic components.
-
Reduced Size and Weight: Metal PCBs can often be made thinner and lighter than traditional PCBs, as they require fewer layers and less copper for heat dissipation.
-
Increased Power Density: With better thermal management, metal PCBs can support higher power densities, enabling more compact and efficient designs.
-
Cost-Effective: In applications that require extensive heat sinking or cooling solutions, metal PCBs can offer a more cost-effective solution by eliminating the need for additional thermal management components.
Applications of Metal PCBs
Metal PCBs are commonly used in applications that require efficient heat dissipation and thermal management. Some of the most common applications include:
-
Power Electronics: Metal PCBs are well-suited for power electronic applications, such as power supplies, inverters, and motor drives, where high currents and voltages generate significant heat.
-
LED Lighting: High-power LED lighting systems can benefit from metal PCBs, as they help to dissipate the heat generated by the LEDs, improving their performance and longevity.
-
Automotive Electronics: Metal PCBs are increasingly used in automotive applications, such as engine control units, power steering systems, and LED headlights, where reliable operation under harsh conditions is essential.
-
Telecommunications: High-power RF and microwave circuits, such as power amplifiers and transmitters, can use metal PCBs to manage the heat generated by the components.
-
Industrial Control Systems: Metal PCBs can be used in industrial control systems, such as programmable logic controllers (PLCs) and motor drives, where reliable operation in harsh environments is critical.
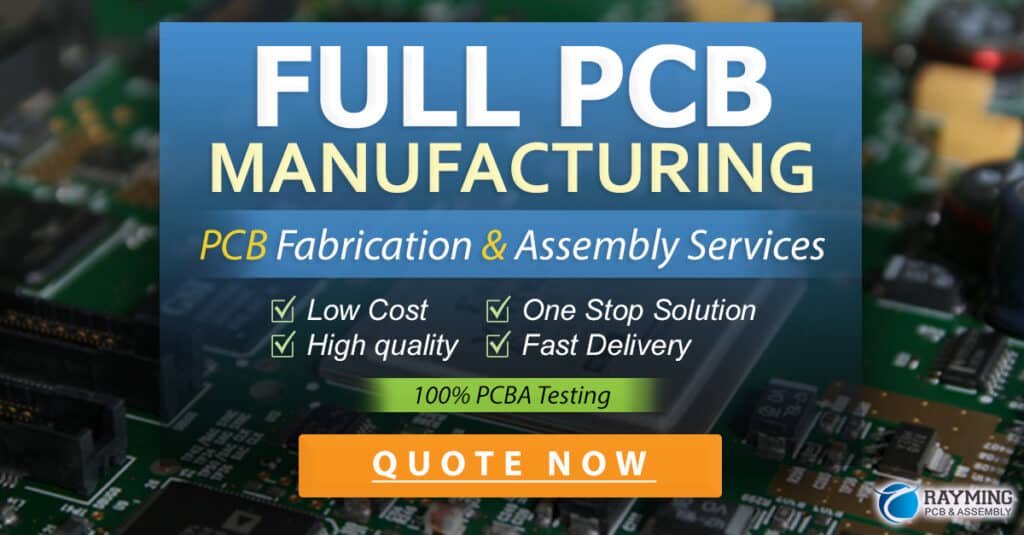
Types of Metal PCBs
There are several types of metal PCBs, each with its own unique features and benefits:
-
Insulated Metal Substrate (IMS): IMS PCBs feature a dielectric layer that is bonded to the metal substrate, providing electrical insulation while maintaining good thermal conductivity. IMS PCBs are the most common type of metal PCB.
-
Metal Core PCB (MCPCB): MCPCBs are similar to IMS PCBs but typically have a thicker metal substrate for even better thermal performance. MCPCBs are often used in high-power applications.
-
Hybrid Metal PCB: Hybrid metal PCBs combine a metal substrate with a traditional FR-4 substrate, allowing for the integration of both high-power and low-power components on the same board.
-
Flexible Metal PCB: Flexible metal PCBs use a thin, flexible metal substrate, such as copper or aluminum foil, to create a bendable circuit board. These PCBs are useful in applications where flexibility and thermal management are required.
Metal PCB Manufacturing Process
The manufacturing process for metal PCBs is similar to that of traditional PCBs, with a few key differences:
-
Substrate Preparation: The metal substrate is cleaned and prepared for bonding with the dielectric layer.
-
Dielectric Layer Application: The dielectric layer is applied to the metal substrate using techniques such as screen printing, lamination, or sputtering.
-
Copper Foil Lamination: A copper foil is laminated onto the dielectric layer using heat and pressure.
-
Circuit Patterning: The copper foil is patterned using standard PCB fabrication techniques, such as photolithography and etching.
-
Component Assembly: Components are soldered onto the metal PCB using standard surface mount or through-hole assembly techniques.
-
Finishing: The metal PCB may undergo additional finishing processes, such as solder masking, silkscreening, and surface finishes, depending on the application requirements.
Designing with Metal PCBs
When designing with metal PCBs, there are several key considerations to keep in mind:
-
Thermal Management: Ensure that the metal substrate and dielectric layer are properly sized and specified to provide sufficient thermal conductivity for the application.
-
Electrical Isolation: Verify that the dielectric layer provides adequate electrical isolation between the metal substrate and the copper circuit layer.
-
Component Selection: Choose components that are compatible with the thermal and mechanical properties of the metal PCB.
-
Layout Optimization: Optimize the PCB layout to maximize thermal performance, minimize thermal stress, and ensure proper grounding and shielding.
-
Manufacturing Constraints: Consider the manufacturing constraints of metal PCBs, such as minimum feature sizes, layer thicknesses, and material compatibility.
Frequently Asked Questions (FAQ)
-
Q: What is the typical thermal conductivity of a metal PCB?
A: The thermal conductivity of a metal PCB depends on the specific materials used, but it is typically in the range of 1-5 W/mK for the dielectric layer and 150-400 W/mK for the metal substrate. -
Q: Can metal PCBs be used in high-frequency applications?
A: Yes, metal PCBs can be used in high-frequency applications, but careful design considerations must be made to ensure proper signal integrity and minimize electromagnetic interference (EMI). -
Q: Are metal PCBs more expensive than traditional PCBs?
A: Metal PCBs can be more expensive than traditional PCBs due to the cost of the metal substrate and additional manufacturing steps. However, they can offer cost savings in applications that would otherwise require extensive heat sinking or cooling solutions. -
Q: What are the most common metal substrates used in metal PCBs?
A: The most common metal substrates used in metal PCBs are aluminum and copper. Aluminum is often chosen for its low cost and good thermal conductivity, while copper provides even better thermal performance but at a higher cost. -
Q: Can metal PCBs be used in flexible applications?
A: Yes, flexible metal PCBs are available that use thin, flexible metal substrates to create bendable circuit boards. These PCBs offer both thermal management and flexibility for applications that require it.
PCB Type | Substrate Material | Thermal Conductivity (W/mK) | Typical Applications |
---|---|---|---|
Traditional PCB | FR-4 | 0.3-0.4 | General electronics |
Insulated Metal Substrate (IMS) | Aluminum, Copper | 1-5 (dielectric), 150-400 (metal) | Power electronics, LED lighting, automotive |
Metal Core PCB (MCPCB) | Aluminum, Copper | 1-5 (dielectric), 150-400 (metal) | High-power applications |
Hybrid Metal PCB | FR-4, Aluminum, Copper | Varies | Mixed high-power and low-power components |
Flexible Metal PCB | Copper, Aluminum foil | Varies | Flexible applications with thermal management |
In conclusion, metal PCBs offer a superior solution for applications that require efficient thermal management and heat dissipation. By utilizing a metal substrate and a thermally conductive dielectric layer, metal PCBs can help to improve the reliability, performance, and power density of electronic systems. With their unique properties and growing range of applications, metal PCBs are becoming an increasingly important tool in the world of electronic design and manufacturing.
Leave a Reply