Understanding Tg and its Importance in PCB Manufacturing
In the world of printed circuit board (PCB) manufacturing, various material properties play crucial roles in determining the performance, reliability, and longevity of the final product. One such property is the glass transition temperature, commonly known as Tg. This article will delve into the concept of Tg, its significance in PCB manufacturing, and how it influences the selection of materials for different applications.
What is Tg?
Tg, or glass transition temperature, is the temperature at which a polymer material transitions from a hard, glassy state to a soft, rubbery state. In the context of PCBs, Tg refers to the temperature at which the substrate material, typically a laminate, undergoes this transition.
When a polymer is below its Tg, it behaves like a rigid, glassy material with limited molecular motion. As the temperature increases and reaches Tg, the polymer chains start to move more freely, resulting in a decrease in stiffness and an increase in flexibility. Above Tg, the material becomes soft and rubbery, with significantly reduced mechanical properties.
The Importance of Tg in PCB Manufacturing
Tg is a critical parameter in PCB manufacturing because it determines the maximum operating temperature of the PCB. A PCB substrate material must maintain its mechanical and electrical properties throughout its intended operating temperature range to ensure reliable performance.
If a PCB is exposed to temperatures above its Tg, several issues can arise:
-
Dimensional instability: As the substrate material softens above Tg, it can expand, contract, or warp, leading to dimensional changes that can affect the alignment and integrity of the copper traces and components.
-
Reduced mechanical strength: The softening of the substrate material above Tg can result in reduced mechanical strength, making the PCB more susceptible to damage from vibration, shock, or handling.
-
Compromised electrical properties: The increased molecular motion above Tg can lead to changes in the dielectric constant and loss tangent of the substrate material, which can affect the electrical performance of the PCB, particularly at high frequencies.
Therefore, it is essential to select a PCB substrate material with a Tg that is sufficiently higher than the maximum expected operating temperature of the application. This ensures that the PCB maintains its mechanical and electrical integrity throughout its service life.
Common PCB Substrate Materials and their Tg Values
Several substrate materials are commonly used in PCB manufacturing, each with its own set of properties and Tg values. The choice of substrate material depends on factors such as the intended application, operating temperature range, electrical requirements, and cost. Some of the most widely used PCB substrate materials and their typical Tg values are listed in the table below:
Substrate Material | Tg Range (°C) |
---|---|
FR-4 | 130 – 180 |
High Tg FR-4 | 170 – 180 |
Polyimide | 250 – 400 |
PTFE (Teflon) | 327 |
Rogers RO4003C | >280 |
Rogers RO4350B | >280 |
Isola IS410 | 180 – 190 |
Isola IS620 | 200 – 210 |
FR-4, a flame-retardant epoxy-glass composite, is the most common PCB substrate material due to its good balance of electrical, mechanical, and thermal properties, as well as its relatively low cost. Standard FR-4 has a Tg range of 130°C to 180°C, which is suitable for most consumer electronics and general-purpose applications.
For more demanding applications that require higher operating temperatures or improved thermal stability, high Tg FR-4 or other advanced materials like polyimide, PTFE, or Rogers laminates can be used. These materials offer higher Tg values, ranging from 170°C to 400°C, making them suitable for automotive, aerospace, military, and high-performance electronics applications.
The Relationship Between Tg and Lead-Free Soldering
The transition to lead-free soldering in the electronics industry has brought new challenges related to Tg. Lead-free solders, such as SAC (tin-silver-copper) alloys, have higher melting temperatures compared to traditional tin-lead solders. As a result, lead-free soldering processes require higher reflow temperatures, typically in the range of 240°C to 260°C.
To accommodate these higher reflow temperatures without compromising the integrity of the PCB, substrate materials with higher Tg values are necessary. If the Tg of the substrate material is too close to the lead-free soldering temperature, the PCB may experience dimensional instability, warpage, or delamination during the soldering process.
As a general rule, the Tg of the PCB substrate material should be at least 25°C higher than the maximum soldering temperature to ensure reliable performance. For lead-free soldering processes, this means that the substrate material should have a Tg of at least 265°C to 285°C.
High Tg FR-4, with a Tg range of 170°C to 180°C, is often used for lead-free soldering applications. However, for more demanding applications or higher-reliability requirements, substrate materials with even higher Tg values, such as polyimide or certain Rogers laminates, may be necessary.
Measuring and Specifying Tg
There are several methods for measuring the Tg of a polymer material, including differential scanning calorimetry (DSC), thermomechanical analysis (TMA), and dynamic mechanical analysis (DMA). Each method has its own advantages and limitations, and the choice of method may depend on factors such as the specific material, the available equipment, and the desired precision.
In the context of PCB manufacturing, Tg is typically specified using one of two methods: Tg by DSC or Tg by TMA. The values obtained from these two methods can differ slightly due to the different principles and measurement conditions involved.
-
Tg by DSC: This method measures the heat flow into or out of a sample as a function of temperature. The Tg is determined by identifying the temperature at which a change in the heat capacity of the material occurs, which is associated with the glass transition.
-
Tg by TMA: This method measures the dimensional changes of a sample as a function of temperature. The Tg is determined by identifying the temperature at which a change in the coefficient of thermal expansion (CTE) of the material occurs, which is associated with the glass transition.
When specifying the Tg of a PCB substrate material, it is essential to clearly indicate the measurement method used (e.g., Tg by DSC or Tg by TMA) to avoid confusion and ensure consistent interpretation of the value.
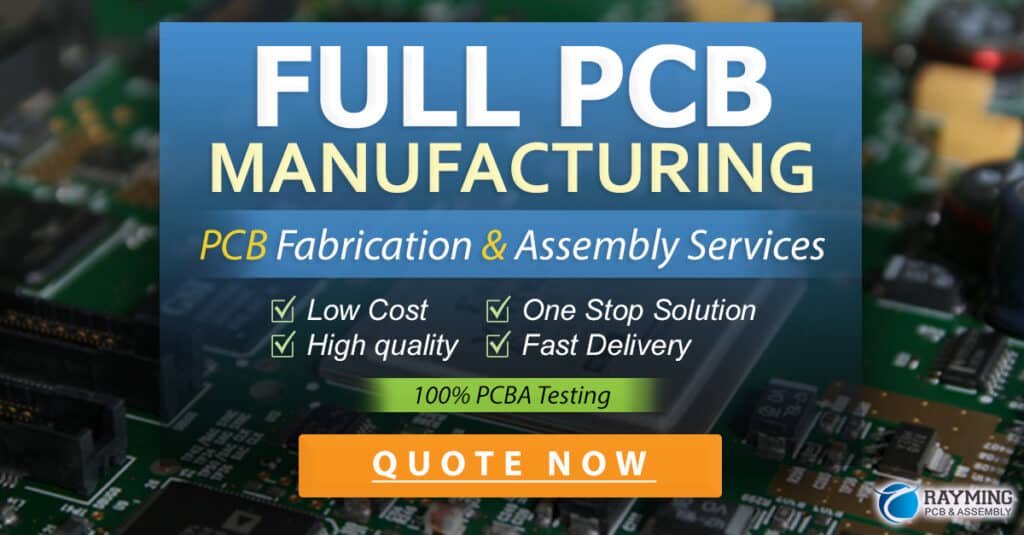
Factors Affecting Tg
Several factors can influence the Tg of a PCB substrate material, including:
-
Resin composition: The type and composition of the resin used in the substrate material can significantly impact its Tg. Different resin systems, such as epoxy, polyimide, or cyanate ester, have inherently different Tg values.
-
Filler content: The type, size, and amount of fillers used in the substrate material can affect its Tg. Fillers, such as glass fibers or ceramic particles, can increase the Tg by constraining the molecular motion of the polymer chains.
-
Curing conditions: The curing temperature, time, and pressure used during the manufacturing process can influence the Tg of the substrate material. Higher curing temperatures and longer curing times generally result in higher Tg values due to increased crosslinking of the polymer chains.
-
Moisture absorption: The absorption of moisture by the substrate material can plasticize the polymer and reduce its Tg. This is particularly relevant for hygroscopic materials like FR-4, which can absorb moisture from the environment.
-
Thermal history: The thermal history of the substrate material, including exposure to elevated temperatures during processing or in-service conditions, can affect its Tg. Repeated thermal cycling or prolonged exposure to high temperatures can lead to changes in the polymer structure and, consequently, its Tg.
Understanding these factors and their impact on Tg is crucial for selecting the appropriate PCB substrate material and optimizing the manufacturing process to ensure the desired performance and reliability of the final product.
Designing PCBs with Tg in Mind
When designing PCBs, it is essential to consider the Tg of the substrate material in relation to the specific requirements of the application. Some key considerations include:
-
Operating temperature range: The maximum operating temperature of the PCB should be well below the Tg of the substrate material to ensure that the PCB maintains its mechanical and electrical integrity throughout its service life.
-
Soldering process: The Tg of the substrate material should be sufficiently higher than the maximum soldering temperature to prevent dimensional instability, warpage, or delamination during the soldering process. This is particularly important for lead-free soldering processes, which require higher reflow temperatures.
-
Thermal cycling: If the PCB will be subjected to repeated thermal cycling during operation, it is essential to select a substrate material with a Tg that can withstand the expected temperature fluctuations without compromising its performance or reliability.
-
High-frequency applications: For high-frequency applications, such as RF or microwave circuits, the choice of substrate material and its Tg can significantly impact the electrical performance of the PCB. Materials with higher Tg values, such as PTFE or Rogers laminates, are often preferred for these applications due to their lower dielectric loss and better thermal stability.
-
Cost considerations: While higher Tg substrate materials offer improved thermal stability and performance, they also tend to be more expensive than standard FR-4. Balancing the cost and performance requirements of the application is essential when selecting the appropriate substrate material.
By carefully considering these factors and selecting a substrate material with an appropriate Tg, PCB designers can ensure that their boards will perform reliably and meet the specific requirements of the intended application.
Frequently Asked Questions (FAQ)
- What is the difference between Tg and melting temperature?
-
Tg (glass transition temperature) is the temperature at which a polymer material transitions from a hard, glassy state to a soft, rubbery state. It is a reversible transition and does not involve a change in the material’s chemical structure. In contrast, the melting temperature is the temperature at which a material changes from a solid to a liquid state, involving a change in its chemical structure. Polymers used in PCBs typically do not have a well-defined melting temperature but rather a Tg.
-
Can a PCB be used above its Tg?
-
While a PCB can be used above its Tg, it is not recommended as it can lead to several issues, such as dimensional instability, reduced mechanical strength, and compromised electrical properties. It is essential to select a PCB substrate material with a Tg that is sufficiently higher than the maximum expected operating temperature of the application to ensure reliable performance.
-
How does moisture affect the Tg of a PCB substrate material?
-
Moisture absorption can plasticize the polymer and reduce its Tg. This is particularly relevant for hygroscopic materials like FR-4, which can absorb moisture from the environment. To minimize the impact of moisture on Tg, PCBs should be stored and processed in controlled environments with appropriate humidity levels, and proper drying procedures should be followed before soldering or other high-temperature processes.
-
What is the relationship between Tg and lead-free soldering?
-
Lead-free solders have higher melting temperatures compared to traditional tin-lead solders, requiring higher reflow temperatures (240°C to 260°C) during the soldering process. To accommodate these higher temperatures without compromising the integrity of the PCB, substrate materials with higher Tg values (at least 25°C higher than the maximum soldering temperature) are necessary.
-
How can I specify the Tg of a PCB substrate material?
- When specifying the Tg of a PCB substrate material, it is essential to clearly indicate the measurement method used (e.g., Tg by DSC or Tg by TMA) to avoid confusion and ensure consistent interpretation of the value. Different measurement methods can yield slightly different Tg values due to the different principles and conditions involved.
In conclusion, understanding the concept of Tg and its impact on PCB performance is crucial for designing and manufacturing reliable and high-quality printed circuit boards. By selecting substrate materials with appropriate Tg values, considering factors such as operating temperature, soldering process, and application requirements, and following best practices for storage and processing, PCB designers and manufacturers can ensure that their products meet the desired performance and reliability standards.
Leave a Reply