Introduction to IPC Standards for PCB
IPC (Institute of Printed Circuits) is a global trade association that sets the standards for the electronics industry. IPC standards cover various aspects of electronic product design and manufacturing, including printed circuit boards (PCBs). These standards ensure consistency, reliability, and quality in PCB manufacturing processes.
Importance of IPC Standards in PCB Manufacturing
IPC standards play a crucial role in PCB manufacturing by:
- Establishing a common language and set of guidelines for the industry
- Ensuring the quality and reliability of PCBs
- Facilitating communication between designers, manufacturers, and customers
- Reducing costs and improving efficiency in the manufacturing process
Key IPC Standards for PCB
There are several IPC standards that specifically address PCB design and manufacturing. Some of the most important ones include:
IPC-2221: Generic Standard on Printed Board Design
IPC-2221 is a generic standard that provides guidelines for the design of printed boards and other related electronic packaging. It covers various aspects of PCB design, including:
- Board layout and routing
- Material selection
- Hole sizes and spacing
- Conductor width and spacing
- Solder mask and silkscreen requirements
This standard helps designers create PCBs that are manufacturable, reliable, and cost-effective.
IPC-6012: Qualification and Performance Specification for Rigid Printed Boards
IPC-6012 is a performance specification that defines the requirements for rigid printed boards, including:
- Material requirements
- Dimensional tolerances
- Hole size and placement tolerances
- Conductor width and spacing tolerances
- Surface finish requirements
This standard ensures that rigid PCBs meet the necessary quality and reliability standards for their intended applications.
IPC-A-600: Acceptability of Printed Boards
IPC-A-600 is a visual acceptance standard for PCBs. It provides a set of visual criteria for inspecting and accepting PCBs based on various defects and anomalies, such as:
- Scratches and dents
- Solder mask and silkscreen defects
- Hole and via defects
- Conductor defects
- Laminate defects
This standard helps manufacturers and customers determine whether a PCB meets the necessary quality requirements.
IPC-A-610: Acceptability of Electronic Assemblies
IPC-A-610 is an acceptance standard for electronic assemblies, including PCBs with components mounted on them. It provides criteria for inspecting and accepting electronic assemblies based on various factors, such as:
- Soldering quality
- Component placement and alignment
- Lead and termination requirements
- Cleanliness and contamination
This standard ensures that electronic assemblies meet the necessary quality and reliability requirements for their intended applications.
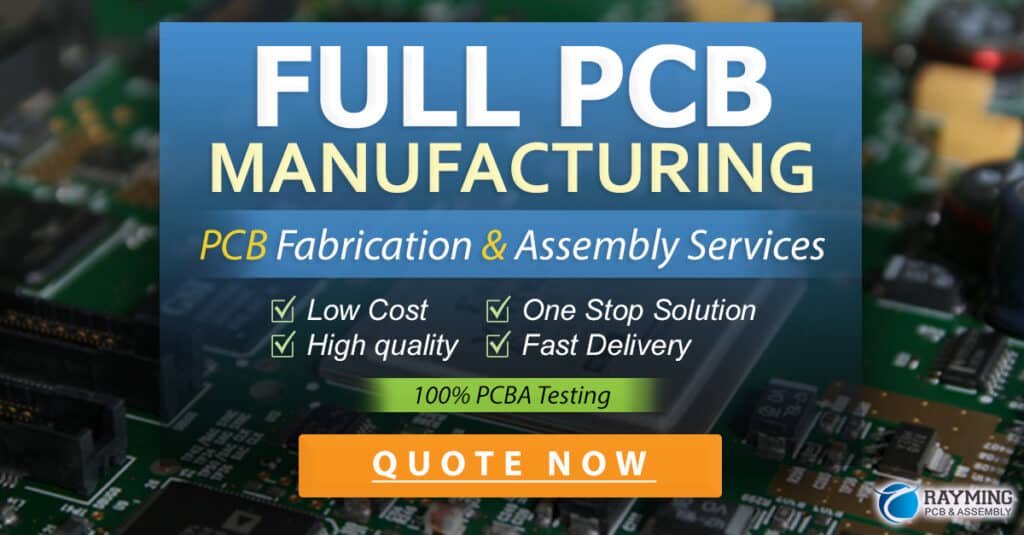
IPC Classification System for PCBs
IPC has a classification system for PCBs based on their intended end-use and the level of assurance required. The three classes are:
Class | Description |
---|---|
Class 1 | General Electronic Products |
Class 2 | Dedicated Service Electronic Products |
Class 3 | High-Performance Electronic Products |
- Class 1: These PCBs are used for general electronic products where the major requirement is function of the completed assembly.
- Class 2: These PCBs are used for dedicated service electronic products where high performance and extended life are required, and uninterrupted service is desired but not critical.
- Class 3: These PCBs are used for high-performance electronic products where continued performance and extended life are critical, and downtime cannot be tolerated.
IPC Training and Certification
IPC offers various training and certification programs to help professionals in the electronics industry stay up-to-date with the latest standards and best practices. Some of the key certification programs related to PCBs include:
Certification | Description |
---|---|
IPC-A-600 | Certified IPC Specialist (CIS) for Acceptability of Printed Boards |
IPC-A-610 | Certified IPC Specialist (CIS) for Acceptability of Electronic Assemblies |
IPC-6012 | Certified Interconnect Designer (CID) for Rigid Printed Boards |
IPC J-STD-001 | Requirements for Soldered Electrical and Electronic Assemblies |
These certifications demonstrate an individual’s knowledge and proficiency in the respective IPC standards and can be valuable for career advancement in the electronics industry.
Benefits of Adhering to IPC Standards
Adhering to IPC standards offers several benefits for PCB manufacturers and their customers, including:
- Improved quality and reliability of PCBs
- Reduced manufacturing costs due to fewer defects and rework
- Faster time-to-market by avoiding design and manufacturing issues
- Enhanced customer satisfaction and trust
- Increased competitiveness in the global market
Challenges in Implementing IPC Standards
While IPC standards offer numerous benefits, implementing them can also present some challenges, such as:
- Staying up-to-date with the latest revisions and changes to the standards
- Training personnel to understand and follow the standards correctly
- Investing in the necessary equipment and processes to meet the standards
- Balancing the cost of compliance with the benefits of adhering to the standards
Despite these challenges, the long-term benefits of adhering to IPC standards make it worthwhile for PCB manufacturers to invest in their implementation.
Future of IPC Standards in PCB Manufacturing
As the electronics industry continues to evolve, IPC standards will play an increasingly important role in ensuring the quality, reliability, and consistency of PCBs. Some of the trends and developments that are likely to shape the future of IPC standards in PCB manufacturing include:
- Increased focus on sustainability and environmental responsibility
- Adoption of advanced technologies, such as 5G, IoT, and AI
- Growing demand for high-density interconnect (HDI) and flexible PCBs
- Emphasis on supply chain transparency and traceability
- Continuous improvement and updating of standards to keep pace with industry developments
Conclusion
IPC standards are essential for ensuring the quality, reliability, and consistency of PCBs in the electronics industry. By adhering to these standards, PCB manufacturers can improve their products, reduce costs, and enhance customer satisfaction. As the industry continues to evolve, staying up-to-date with the latest IPC standards and best practices will be crucial for success in the competitive global market.
Frequently Asked Questions (FAQ)
1. What does IPC stand for?
IPC stands for the Institute of Printed Circuits, a global trade association that sets standards for the electronics industry.
2. Why are IPC standards important for PCB manufacturing?
IPC standards ensure consistency, reliability, and quality in PCB manufacturing processes. They establish a common language and set of guidelines for the industry, helping to reduce costs and improve efficiency.
3. What are some of the key IPC standards for PCBs?
Some of the key IPC standards for PCBs include:
– IPC-2221: Generic Standard on Printed Board Design
– IPC-6012: Qualification and Performance Specification for Rigid Printed Boards
– IPC-A-600: Acceptability of Printed Boards
– IPC-A-610: Acceptability of Electronic Assemblies
4. What is the IPC classification system for PCBs?
The IPC classification system for PCBs is based on their intended end-use and the level of assurance required. The three classes are:
– Class 1: General Electronic Products
– Class 2: Dedicated Service Electronic Products
– Class 3: High-Performance Electronic Products
5. How can professionals in the electronics industry stay up-to-date with IPC standards?
IPC offers various training and certification programs to help professionals in the electronics industry stay up-to-date with the latest standards and best practices. Some of the key certification programs related to PCBs include IPC-A-600, IPC-A-610, IPC-6012, and IPC J-STD-001.
Leave a Reply