What is Pad Insulation?
Pad insulation refers to the material used to insulate and protect the inner layers of a printed circuit board (PCB) or other electronic components. It is typically made from dielectric materials that have high electrical resistance and excellent thermal stability. The primary purpose of pad insulation is to prevent short circuits and electrical interference between the conductive traces and components on the PCB.
Properties of Inner Layer Pad Insulation
To effectively serve its purpose, inner layer pad insulation must possess several key properties:
-
High dielectric strength: The insulation material should have a high resistance to electrical breakdown, ensuring that it can withstand the voltage levels present in the circuit.
-
Low dielectric constant: A low dielectric constant helps minimize the capacitance between the conductive traces, reducing signal distortion and improving the overall performance of the device.
-
Thermal stability: The insulation material should maintain its properties over a wide range of temperatures, as electronic devices often generate heat during operation.
-
Moisture resistance: Inner layer pad insulation must be resistant to moisture to prevent the formation of conductive paths that could lead to short circuits or corrosion.
-
Mechanical strength: The insulation material should have sufficient mechanical strength to withstand the stresses encountered during the manufacturing process and the normal use of the electronic device.
Applications of Inner Layer Pad Insulation
Inner layer pad insulation finds applications in various industries and products, including:
-
Consumer electronics: Smartphones, tablets, laptops, and other portable devices rely on inner layer pad insulation to ensure the proper functioning of their PCBs.
-
Automotive electronics: The harsh environmental conditions encountered in vehicles necessitate the use of robust inner layer pad insulation to protect sensitive electronic components.
-
Medical devices: Inner layer pad insulation is crucial in medical devices, where reliability and safety are of utmost importance.
-
Aerospace and defense: The extreme conditions encountered in aerospace and defense applications require high-performance inner layer pad insulation to ensure the proper functioning of electronic systems.
-
Industrial equipment: Inner layer pad insulation is used in various industrial equipment, such as sensors, controllers, and communication devices, to protect against harsh environments and ensure reliable operation.
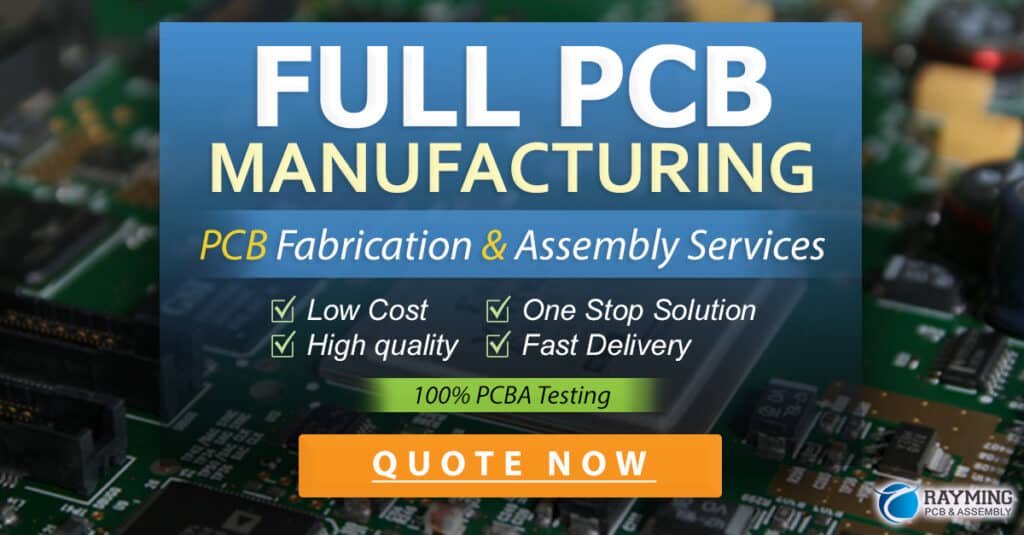
Types of Inner Layer Pad Insulation
There are several types of inner layer pad insulation materials available, each with its own unique properties and advantages:
-
FR-4: FR-4 is a commonly used glass-reinforced epoxy laminate that offers good electrical insulation, mechanical strength, and thermal stability. It is widely used in the production of PCBs for consumer electronics and industrial applications.
-
Polyimide: Polyimide is a high-performance polymer that offers excellent thermal stability, chemical resistance, and mechanical strength. It is often used in applications that require operation at high temperatures or exposure to harsh chemicals.
-
Teflon (PTFE): Teflon, or polytetrafluoroethylene, is a fluoropolymer known for its low dielectric constant, high thermal stability, and excellent chemical resistance. It is often used in high-frequency applications and in environments where chemical inertness is required.
-
Ceramic: Ceramic insulators, such as alumina and beryllia, offer high dielectric strength, excellent thermal conductivity, and good mechanical properties. They are often used in high-power and high-temperature applications.
-
Kapton: Kapton is a polyimide film developed by DuPont that offers excellent thermal stability, mechanical strength, and electrical insulation properties. It is widely used in the aerospace and defense industries, as well as in flexible electronics applications.
Factors to Consider When Selecting Inner Layer Pad Insulation
When choosing the appropriate inner layer pad insulation for a specific application, several factors must be considered:
-
Dielectric properties: The dielectric strength and dielectric constant of the insulation material should be appropriate for the voltage levels and signal frequencies encountered in the application.
-
Thermal properties: The thermal stability and thermal conductivity of the insulation material should be suitable for the operating temperature range and heat dissipation requirements of the device.
-
Mechanical properties: The insulation material should have sufficient mechanical strength and flexibility to withstand the stresses encountered during manufacturing and normal use.
-
Chemical resistance: The insulation material should be resistant to the chemicals and solvents used in the manufacturing process and encountered in the operating environment.
-
Cost: The cost of the insulation material should be considered in relation to the performance requirements and production volume of the application.
Manufacturing Process of Inner Layer Pad Insulation
The manufacturing process of inner layer pad insulation typically involves the following steps:
-
Material selection: The appropriate insulation material is selected based on the requirements of the application, such as dielectric properties, thermal stability, and mechanical strength.
-
Lamination: The insulation material is laminated to the conductive layers of the PCB using heat and pressure. This process ensures a strong bond between the layers and prevents delamination.
-
Patterning: The desired pattern of the insulation layer is created using photolithography or laser ablation techniques. This process removes the unwanted portions of the insulation material, exposing the conductive traces where necessary.
-
Curing: The laminated and patterned PCB is subjected to a curing process, which involves exposure to high temperatures for a specific duration. This process ensures that the insulation material is fully cured and achieves its final properties.
-
Inspection: The finished PCB with inner layer pad insulation undergoes a thorough inspection to ensure that it meets the required specifications and quality standards.
Advancements in Inner Layer Pad Insulation Technology
Ongoing research and development in the field of inner layer pad insulation have led to several advancements in recent years:
-
High-frequency materials: The development of low-loss, high-frequency insulation materials has enabled the design of PCBs for applications operating at higher frequencies, such as 5G wireless communication and high-speed data transmission.
-
Thin-film insulation: The use of thin-film insulation materials, such as parylene and polyimide, has allowed for the miniaturization of electronic devices and the creation of more compact and lightweight PCBs.
-
Embedded components: The integration of passive components, such as resistors and capacitors, into the inner layers of the PCB has been made possible by advancements in insulation materials and manufacturing processes. This approach saves space and improves the overall performance of the device.
-
3D printing: The emergence of 3D printing technologies for electronics has opened up new possibilities for the fabrication of inner layer pad insulation. 3D printing allows for the creation of complex geometries and the integration of multiple materials in a single process, potentially leading to more efficient and cost-effective manufacturing.
Frequently Asked Questions (FAQ)
-
What is the purpose of inner layer pad insulation?
Inner layer pad insulation serves to prevent short circuits and electrical interference between the conductive traces and components on a PCB by providing electrical insulation and protection against environmental factors such as moisture, dust, and extreme temperatures. -
What are the key properties of inner layer pad insulation materials?
The key properties of inner layer pad insulation materials include high dielectric strength, low dielectric constant, thermal stability, moisture resistance, and mechanical strength. -
What are some common types of inner layer pad insulation materials?
Common types of inner layer pad insulation materials include FR-4, polyimide, Teflon (PTFE), ceramic, and Kapton. -
What factors should be considered when selecting inner layer pad insulation for a specific application?
When selecting inner layer pad insulation, factors such as dielectric properties, thermal properties, mechanical properties, chemical resistance, and cost should be considered in relation to the requirements of the application. -
What advancements have been made in inner layer pad insulation technology?
Recent advancements in inner layer pad insulation technology include the development of high-frequency materials, thin-film insulation, embedded components, and the use of 3D printing for the fabrication of insulation layers.
Conclusion
Inner layer pad insulation is a critical component in the design and manufacture of electronic devices, providing electrical insulation and protection against environmental factors. The selection of the appropriate insulation material depends on various factors, such as dielectric properties, thermal stability, mechanical strength, and chemical resistance. With ongoing advancements in materials science and manufacturing processes, inner layer pad insulation technology continues to evolve, enabling the development of more compact, reliable, and high-performance electronic devices.
Insulation Material | Dielectric Strength (kV/mm) | Dielectric Constant | Thermal Stability (°C) | Moisture Resistance | Mechanical Strength |
---|---|---|---|---|---|
FR-4 | 20-30 | 4.5-5.5 | 130-140 | Good | Good |
Polyimide | 200-300 | 3.5-4.0 | 300-400 | Excellent | Excellent |
Teflon (PTFE) | 60-80 | 2.0-2.2 | 260-300 | Excellent | Good |
Ceramic | 10-30 | 6.0-10.0 | 1000-1500 | Excellent | Excellent |
Kapton | 200-300 | 3.5-4.0 | 300-400 | Excellent | Excellent |
In summary, inner layer pad insulation is a vital aspect of electronic device design, ensuring the proper functioning, reliability, and longevity of PCBs and other components. By understanding the properties, applications, and types of inner layer pad insulation materials, engineers and manufacturers can make informed decisions when selecting the appropriate insulation for their specific needs. As technology continues to advance, it is essential to stay up-to-date with the latest developments in inner layer pad insulation to create electronic devices that meet the ever-increasing demands of modern applications.
Leave a Reply