Understanding High Frequency Signals
To understand the importance of high frequency PCBs, it is essential to first understand what high frequency signals are and how they differ from low frequency signals.
Definition of High Frequency Signals
High frequency signals are electrical signals that oscillate at a high rate, typically in the range of megahertz (MHz) to gigahertz (GHz). These signals have short wavelengths and can carry large amounts of information, making them ideal for applications that require high bandwidth and fast data transmission.
Characteristics of High Frequency Signals
High frequency signals have several unique characteristics that distinguish them from low frequency signals:
-
Short wavelengths: As the frequency of a signal increases, its wavelength decreases. This means that high frequency signals have very short wavelengths, often in the range of millimeters or even micrometers.
-
High bandwidth: High frequency signals can carry large amounts of information, allowing for high-speed data transmission and processing.
-
Sensitivity to impedance mismatches: High frequency signals are more sensitive to impedance mismatches than low frequency signals. Any discontinuities or variations in the characteristic impedance of a transmission line can cause reflections and signal distortion.
-
Susceptibility to noise and interference: High frequency signals are more susceptible to noise and interference from external sources, such as electromagnetic interference (EMI) and crosstalk from nearby signals.
Applications of High Frequency Signals
High frequency signals are used in a wide range of applications, including:
-
Wireless communications: High frequency signals are used in various wireless communication technologies, such as cellular networks (4G, 5G), Wi-Fi, Bluetooth, and satellite communications.
-
Radar systems: High frequency signals are used in radar systems for object detection, tracking, and imaging.
-
High-speed digital circuits: High frequency signals are used in high-speed digital circuits, such as microprocessors, memory devices, and field-programmable gate arrays (FPGAs).
-
Medical imaging: High frequency signals are used in medical imaging techniques, such as magnetic resonance imaging (MRI) and ultrasound imaging.
Challenges in Designing High Frequency PCBs
Designing high frequency PCBs presents several challenges that must be addressed to ensure optimal signal integrity and performance.
Signal Integrity Issues
Signal integrity is a major concern in high frequency pcb design. As the frequency of a signal increases, the wavelength decreases, making the signal more susceptible to various signal integrity issues, such as:
-
Reflections: Impedance mismatches along the signal path can cause reflections, leading to signal distortion and degradation.
-
Crosstalk: Electromagnetic coupling between adjacent signal traces can cause crosstalk, where a signal on one trace induces unwanted signals on nearby traces.
-
Attenuation: As a signal travels along a transmission line, it experiences attenuation due to dielectric and conductor losses, reducing the signal strength and quality.
-
Dispersion: Different frequency components of a signal may travel at slightly different speeds, causing the signal to spread out in time and leading to signal distortion.
EMI and EMC Considerations
Electromagnetic interference (EMI) and electromagnetic compatibility (EMC) are critical considerations in high frequency PCB design. High frequency signals can generate significant EMI, which can interfere with the operation of nearby electronic devices. Conversely, external EMI sources can also disrupt the operation of high frequency circuits.
To mitigate EMI and ensure EMC compliance, high frequency PCBs must incorporate various design techniques, such as:
-
Proper grounding and shielding: Effective grounding and shielding techniques help to minimize the effects of EMI and prevent unwanted radiation from the PCB.
-
Careful component placement: Strategic placement of components and signal traces can help to minimize EMI and crosstalk.
-
Use of EMI filters and suppressors: EMI filters and suppressors can be used to attenuate unwanted high frequency noise and prevent it from entering or leaving the PCB.
Material Selection
The choice of materials used in high frequency PCBs is critical to their performance. The dielectric materials used in the PCB substrate must have low dielectric loss and stable dielectric constant over the desired frequency range. Some commonly used high frequency PCB materials include:
-
Rogers RO4000 series: These materials offer excellent high frequency performance, with low dielectric loss and stable dielectric constant up to millimeter-wave frequencies.
-
PTFE (Teflon): PTFE-based materials, such as Rogers RT/duroid, offer very low dielectric loss and are suitable for high frequency applications.
-
Low-loss hydrocarbon ceramics: These materials, such as Rogers TMM and Taconic RF-35, provide a balance of good high frequency performance and cost-effectiveness.
The copper used for signal traces and ground planes must also be of high quality, with low surface roughness to minimize conductor losses.
High Frequency PCB Design Techniques
To address the challenges associated with high frequency PCB design, various techniques are employed to optimize signal integrity and minimize EMI.
Controlled Impedance Design
Controlled impedance design is a critical aspect of high frequency PCB design. By carefully controlling the characteristic impedance of transmission lines, designers can minimize reflections and ensure efficient power transfer. This is typically achieved through the use of:
-
Microstrip lines: These are signal traces that run on the top layer of the PCB, with a ground plane on the layer beneath. The width of the trace and the thickness of the dielectric layer determine the characteristic impedance.
-
Striplines: These are signal traces that run on an inner layer of the PCB, with ground planes above and below. Striplines offer better shielding and lower radiation than microstrip lines.
-
Coplanar waveguides: These are signal traces that run on the top layer of the PCB, with ground planes on either side of the trace. Coplanar waveguides offer lower dispersion than microstrip lines and are suitable for very high frequency applications.
Grounding and Shielding
Proper grounding and shielding are essential for minimizing EMI and ensuring signal integrity in high frequency PCBs. Some key techniques include:
-
Ground planes: Using continuous ground planes on one or more layers of the PCB helps to provide a low-impedance return path for high frequency currents and minimizes EMI.
-
Via stitching: Placing closely spaced vias along the edges of ground planes helps to prevent high frequency currents from flowing around the edges and causing EMI.
-
Shielding: Metallic shielding enclosures can be used to contain EMI from high frequency components and prevent external EMI from interfering with the circuit.
High Frequency Layout Considerations
The layout of components and signal traces on a high frequency PCB is critical to its performance. Some important considerations include:
-
Component placement: High frequency components should be placed as close together as possible to minimize the length of signal traces and reduce signal attenuation and distortion.
-
Signal routing: Signal traces should be kept as short and straight as possible, with minimal bends and vias. Avoid routing high frequency signals parallel to each other to minimize crosstalk.
-
Trace width and spacing: The width and spacing of signal traces must be carefully controlled to maintain the desired characteristic impedance and minimize crosstalk.
-
Via design: Vias should be kept to a minimum, as they can cause discontinuities in the signal path and lead to reflections. When vias are necessary, they should be designed to minimize inductance and capacitance.
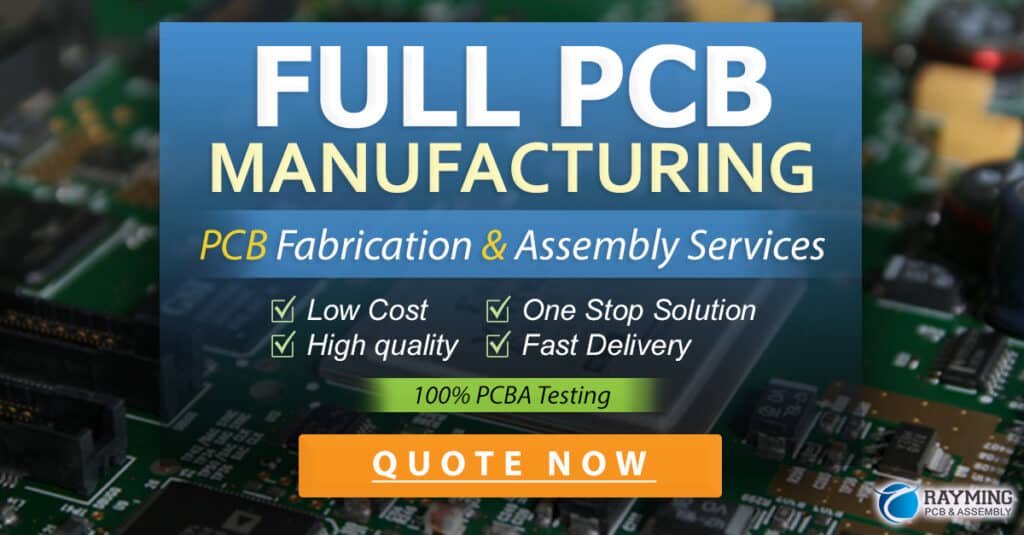
Manufacturing Considerations for High Frequency PCBs
Manufacturing high frequency PCBs requires specialized equipment and processes to ensure the highest quality and performance.
Material Handling and Processing
High frequency PCB materials are often more delicate and sensitive to moisture than standard PCB materials. Proper handling and storage of these materials is essential to prevent damage and ensure optimal performance. This includes:
-
Moisture control: High frequency PCB materials should be stored in a dry environment with controlled humidity to prevent moisture absorption, which can lead to delamination and other defects.
-
Controlled impedance processing: The manufacturing process must be carefully controlled to maintain the desired characteristic impedance of the transmission lines. This includes precise control of etching, lamination, and drilling processes.
Specialized Manufacturing Techniques
Manufacturing high frequency PCBs often requires the use of specialized techniques to achieve the necessary precision and quality. These may include:
-
High-resolution etching: High frequency PCBs require very fine trace widths and spacings, which can only be achieved using high-resolution etching processes, such as advanced photolithography or laser etching.
-
Tight tolerance drilling: The vias in high frequency PCBs must be drilled with very tight tolerances to minimize discontinuities and reflections. This requires the use of high-precision drilling equipment and strict process control.
-
Selective plating: In some cases, selective plating techniques may be used to apply different finishes or thicknesses of copper to different areas of the PCB, such as signal traces and ground planes.
Quality Control and Testing
Rigorous quality control and testing are essential to ensure that high frequency PCBs meet the required performance specifications. This may include:
-
Impedance testing: The characteristic impedance of transmission lines must be carefully measured and verified to ensure that it meets the design requirements.
-
Time-domain reflectometry (TDR): TDR is used to measure the impedance profile of transmission lines and identify any discontinuities or reflections.
-
S-parameter measurements: Scattering parameters (S-parameters) are used to characterize the high frequency performance of the PCB, including insertion loss, return loss, and crosstalk.
-
EMI and EMC testing: The PCB must be tested to ensure that it meets relevant EMI and EMC standards, such as FCC Part 15 or EN 55022.
Future Trends in High Frequency PCBs
As the demand for higher bandwidth and faster data transmission continues to grow, high frequency PCBs will play an increasingly important role in modern electronics. Some key trends and developments to watch include:
5G and Beyond
The rollout of 5G cellular networks is driving demand for high frequency PCBs that can support the higher frequencies and bandwidths required for 5G applications. As 5G evolves and future generations of wireless technology emerge, high frequency PCBs will need to continue to advance to keep pace.
Millimeter-Wave Applications
Millimeter-wave frequencies (30 GHz to 300 GHz) are becoming increasingly important for applications such as high-speed wireless communications, radar, and imaging. High frequency PCBs that can operate at these frequencies will be essential for realizing the full potential of millimeter-wave technology.
Advanced Materials
New high frequency PCB materials are being developed to offer even better performance and reliability than existing materials. These may include advanced ceramic materials, low-loss polymers, and nanomaterials that can provide superior dielectric and conductor properties.
Integrated Antenna Design
As wireless devices become smaller and more complex, there is a growing trend towards integrating antennas directly onto high frequency PCBs. This requires careful co-design of the antenna and PCB to ensure optimal performance and minimize interference.
Frequently Asked Questions (FAQ)
-
What is the difference between high frequency PCBs and standard PCBs?
High frequency PCBs are specifically designed to handle high frequency signals (typically in the MHz to GHz range) with minimal loss and distortion, while standard PCBs are designed for lower frequency applications. High frequency PCBs use specialized materials, design techniques, and manufacturing processes to achieve the necessary performance. -
What are some common applications of high frequency PCBs?
High frequency PCBs are used in a wide range of applications, including wireless communications (e.g., 5G, Wi-Fi, Bluetooth), radar systems, high-speed digital circuits, and medical imaging equipment. -
What are the main challenges in designing high frequency PCBs?
The main challenges in designing high frequency PCBs include maintaining signal integrity (minimizing reflections, crosstalk, attenuation, and dispersion), managing EMI and ensuring EMC compliance, selecting appropriate materials, and implementing effective grounding and shielding techniques. -
What materials are commonly used in high frequency PCBs?
Common materials used in high frequency PCBs include Rogers RO4000 series, PTFE (Teflon), and low-loss hydrocarbon ceramics. These materials offer low dielectric loss and stable dielectric constant over the desired frequency range. -
How can I ensure that my high frequency PCB meets the required performance specifications?
To ensure that your high frequency PCB meets the required performance specifications, you should work with an experienced PCB manufacturer that specializes in high frequency design and fabrication. They can help you with material selection, design optimization, and rigorous quality control and testing procedures, such as impedance testing, TDR, S-parameter measurements, and EMI/EMC testing.
Conclusion
High frequency PCBs are essential components in many modern electronic devices and systems that require high bandwidth and fast data transmission. Designing and manufacturing these PCBs presents unique challenges, including maintaining signal integrity, managing EMI, and selecting appropriate materials.
By understanding the characteristics of high frequency signals, employing specialized design techniques, and working with experienced PCB manufacturers, engineers can overcome these challenges and create high-performance PCBs that meet the demanding requirements of today’s high frequency applications.
As technology continues to advance, the demand for high frequency PCBs will only continue to grow. By staying up-to-date with the latest trends and developments in high frequency PCB design and manufacturing, engineers can position themselves to be at the forefront of this exciting and rapidly evolving field.
Leave a Reply