Key Characteristics of HDI PCBs
HDI PCBs are characterized by several key features that set them apart from traditional PCBs:
-
Smaller Vias: HDI PCBs utilize micro vias, which are smaller than conventional through-hole vias. These micro vias can be as small as 50 microns in diameter, enabling higher density interconnections between layers.
-
Finer Pitch: The pitch, or the distance between the centers of adjacent pads or traces, is much smaller in HDI PCBs. This allows for a higher density of components and interconnections on the board.
-
Thinner Copper Layers: HDI PCBs often employ thinner copper layers compared to traditional PCBs. This helps in achieving finer trace widths and spacing, contributing to the overall high density of the board.
-
Multiple Layers: HDI PCBs typically have a higher number of layers compared to conventional PCBs. This allows for more complex routing and interconnections within a smaller footprint.
Advantages of HDI PCBs
The unique characteristics of HDI PCBs offer several advantages over traditional PCBs:
-
Miniaturization: The smaller vias, finer pitch, and thinner copper layers enable the design of more compact and lightweight electronic devices.
-
Improved Signal Integrity: The reduced trace lengths and optimized routing in HDI PCBs minimize signal distortion and crosstalk, resulting in improved signal integrity and overall performance.
-
Enhanced Functionality: With the ability to accommodate more components and interconnections in a smaller area, HDI PCBs enable the integration of advanced features and functionalities into electronic devices.
-
Reduced Power Consumption: The shorter trace lengths in HDI PCBs lead to reduced power consumption, as there is less resistance and capacitance in the interconnections.
-
Cost-Effective: Although the initial manufacturing costs of HDI PCBs may be higher due to the advanced processes involved, they often result in cost savings in the long run due to reduced assembly time, fewer components, and improved reliability.
HDI PCB Manufacturing Process
The manufacturing process of HDI PCBs involves several advanced techniques and technologies to achieve the desired high density and performance. Some of the key steps in the HDI PCB manufacturing process include:
-
Laser Drilling: Micro vias in HDI PCBs are typically created using laser drilling. Laser drilling allows for precise and small-diameter vias to be formed in the PCB layers.
-
Sequential Lamination: HDI PCBs often employ a sequential lamination process, where layers are added one at a time, allowing for the creation of buried and blind vias.
-
Copper Filling: After laser drilling, the micro vias are filled with copper to establish electrical connections between layers. This is typically done using electroplating or other advanced filling techniques.
-
High-Resolution Patterning: To achieve fine pitch and trace widths, HDI PCBs require high-resolution patterning techniques, such as photolithography or laser direct imaging (LDI).
-
Surface Finishing: HDI PCBs undergo surface finishing processes, such as ENIG (Electroless Nickel Immersion Gold) or ENEPIG (Electroless Nickel Electroless Palladium Immersion Gold), to protect the exposed copper and enhance solderability.
Applications of HDI PCBs
HDI PCBs find applications in various industries where miniaturization, high performance, and advanced functionality are crucial. Some of the common applications of HDI PCBs include:
-
Smartphones and Tablets: The compact size and advanced features of modern smartphones and tablets heavily rely on HDI PCBs to accommodate the dense packaging of components and interconnections.
-
Wearable Devices: Smartwatches, fitness trackers, and other wearable devices require HDI PCBs to achieve the necessary miniaturization and functionality within a small form factor.
-
Medical Devices: HDI PCBs are used in medical devices, such as implantable devices, diagnostic equipment, and monitoring systems, where reliability, precision, and compact size are essential.
-
Aerospace and Defense: In aerospace and defense applications, HDI PCBs are employed in avionics systems, communication devices, and radar systems, where high performance and reliability are critical.
-
Automotive Electronics: As vehicles become more technologically advanced, HDI PCBs are increasingly used in automotive electronics, such as infotainment systems, driver assistance systems, and powertrain control modules.
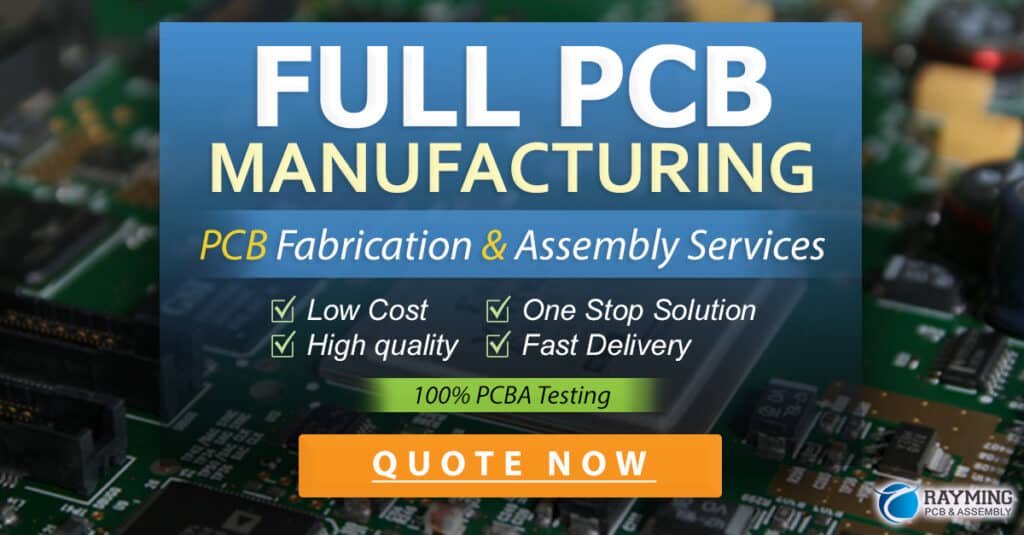
hdi pcb design Considerations
Designing HDI PCBs requires careful consideration of several factors to ensure optimal performance and manufacturability. Some key design considerations for HDI PCBs include:
-
Via Types and Placement: Designers must choose the appropriate via types (blind, buried, or micro vias) and their placement to achieve the desired interconnections while maintaining signal integrity and manufacturability.
-
Layer Stackup: The layer stackup of an HDI PCB should be carefully planned to optimize signal routing, impedance control, and power distribution. The stackup may include a combination of signal, power, and ground layers.
-
Trace Width and Spacing: To achieve high density, designers must adhere to the minimum trace width and spacing guidelines specified by the PCB manufacturer. This ensures proper fabrication and helps avoid signal integrity issues.
-
Component Placement: Proper component placement is crucial in HDI PCBs to minimize trace lengths, reduce crosstalk, and facilitate efficient routing. Designers should consider the component packaging, size, and pin layout when placing components on the board.
-
Signal Integrity Analysis: Due to the high density and high-speed nature of HDI PCBs, signal integrity analysis is essential to ensure proper signal propagation and minimize signal distortion. Tools like simulation software can help designers analyze and optimize signal integrity.
-
Thermal Management: With the increased density of components and interconnections, thermal management becomes critical in HDI PCBs. Designers should incorporate appropriate thermal relief pads, vias, and heat dissipation techniques to prevent overheating and ensure reliable operation.
HDI PCB Testing and Inspection
To ensure the quality and reliability of HDI PCBs, rigorous testing and inspection processes are employed. Some common testing and inspection methods for HDI PCBs include:
-
Automated Optical Inspection (AOI): AOI systems use high-resolution cameras and advanced image processing algorithms to detect surface defects, such as solder bridges, missing components, or incorrect component placement.
-
X-Ray Inspection: X-ray inspection is used to examine the internal structure of HDI PCBs, including the quality of micro vias, solder joints, and copper filling. X-ray systems can detect voids, cracks, or other hidden defects.
-
Electrical Testing: Various electrical tests, such as continuity testing, insulation resistance testing, and high-potential (HiPot) testing, are performed to verify the electrical integrity of the HDI PCB and ensure proper connectivity between components.
-
Functional Testing: Functional testing involves powering up the HDI PCB and testing its functionality under real-world operating conditions. This helps identify any performance issues or compatibility problems.
-
Boundary Scan Testing: Boundary scan testing, also known as JTAG testing, is used to test the interconnections and functionality of components on the HDI PCB. It allows for the detection of faults and enables in-system programming of devices.
Future Trends in HDI PCBs
As technology continues to advance, HDI PCBs are expected to evolve to meet the growing demands for miniaturization, high performance, and advanced functionality. Some future trends in HDI PCBs include:
-
Increased Layer Count: HDI PCBs are likely to incorporate even more layers in the future to accommodate the increasing complexity of electronic systems. This will enable higher wiring density and more sophisticated routing.
-
Smaller Via Sizes: Advancements in laser drilling and other manufacturing technologies will allow for even smaller micro vias, enabling further miniaturization and higher interconnection density.
-
Advanced Materials: The use of advanced materials, such as low-loss dielectrics and high-performance laminates, will become more prevalent in HDI PCBs to improve signal integrity and thermal management.
-
Embedded Components: The integration of embedded components, such as capacitors, resistors, and active devices, directly into the PCB substrate will gain traction in HDI PCBs. This will lead to further miniaturization and improved performance.
-
3D Packaging: The adoption of 3D packaging techniques, such as package-on-package (PoP) and through-silicon vias (TSVs), will increase in HDI PCBs. These techniques enable vertical stacking of components and interconnections, resulting in higher density and reduced footprint.
Frequently Asked Questions (FAQ)
-
What is the difference between HDI PCBs and traditional PCBs?
HDI PCBs have higher wiring density per unit area compared to traditional PCBs. They feature smaller vias, finer pitch, thinner copper layers, and a higher number of layers, enabling miniaturization and improved performance. -
What are the advantages of using HDI PCBs?
The advantages of using HDI PCBs include miniaturization, improved signal integrity, enhanced functionality, reduced power consumption, and cost-effectiveness in the long run. -
What industries commonly use HDI PCBs?
HDI PCBs are commonly used in industries such as consumer electronics (smartphones, tablets), wearable devices, medical devices, aerospace and defense, and automotive electronics. -
What are some key design considerations for HDI PCBs?
Key design considerations for HDI PCBs include via types and placement, layer stackup, trace width and spacing, component placement, signal integrity analysis, and thermal management. -
What testing and inspection methods are used for HDI PCBs?
Common testing and inspection methods for HDI PCBs include automated optical inspection (AOI), X-ray inspection, electrical testing, functional testing, and boundary scan testing (JTAG).
Comparison | HDI PCBs | Traditional PCBs |
---|---|---|
Via Size | Smaller micro vias (down to 50 microns) | Larger through-hole vias |
Pitch | Finer pitch (smaller pad/trace spacing) | Coarser pitch (larger pad/trace spacing) |
Copper Layers | Thinner copper layers | Thicker copper layers |
Layer Count | Higher number of layers | Lower number of layers |
Density | Higher wiring density per unit area | Lower wiring density per unit area |
Applications | Miniaturized and high-performance devices | Larger and less complex devices |
In conclusion, HDI PCBs represent a significant advancement in printed circuit board technology, enabling the development of miniaturized, high-performance electronic devices. With their higher wiring density, smaller vias, finer pitch, and advanced manufacturing processes, HDI PCBs offer numerous advantages over traditional PCBs. As technology continues to progress, HDI PCBs are expected to evolve further, incorporating more layers, smaller via sizes, advanced materials, embedded components, and 3D packaging techniques. By understanding the characteristics, manufacturing processes, design considerations, and testing methods associated with HDI PCBs, engineers and designers can leverage this technology to create innovative and reliable electronic products across various industries.
Leave a Reply