Understanding the Basics of Heatsinks
What is a Heatsink?
A heatsink is a passive heat exchanger that is designed to absorb and dissipate heat generated by electronic components, such as processors, power transistors, and voltage regulators. The primary purpose of a heatsink is to maintain the temperature of these components within their safe operating limits, preventing overheating and potential damage.
How Do Heatsinks Work?
Heatsinks work by providing a large surface area for heat to be transferred away from the heat-generating component and into the surrounding air. The heatsink is typically made of a material with high thermal conductivity, such as aluminum or copper, which allows heat to flow efficiently from the component to the heatsink.
The heatsink’s surface area is maximized through the use of fins or other protrusions, which increase the amount of air that can come into contact with the heatsink. As the air flows over the fins, it carries away the heat, effectively cooling the component.
The Importance of Heatsinks in PCB Design
Protecting Components from Overheating
One of the primary reasons for using heatsinks in PCB design is to protect components from overheating. Excessive heat can cause components to malfunction, degrade, or even fail completely. By dissipating heat away from these components, heatsinks help maintain their temperature within safe operating limits, ensuring reliable performance and extended lifespan.
Maintaining Optimal System Performance
In addition to protecting components from damage, heatsinks also play a crucial role in maintaining optimal system performance. Many electronic components, such as processors and power transistors, generate significant amounts of heat during operation. If this heat is not effectively managed, it can lead to reduced performance, as the components may throttle their speed or enter a protective shutdown mode to prevent damage.
By keeping components cool, heatsinks allow them to operate at their maximum potential, ensuring optimal system performance and preventing throttling or shutdown.
Enabling High-Power Applications
Heatsinks are particularly important in high-power applications, such as power electronics, automotive systems, and industrial equipment. In these applications, components often generate substantial amounts of heat due to the high currents and voltages involved. Without proper heat dissipation, these components would quickly overheat and fail, potentially causing system malfunctions or even safety hazards.
Heatsinks enable the use of high-power components by effectively managing the heat they generate, allowing for the development of more advanced and powerful electronic systems.
Types of Heatsinks Used in PCB Design
Passive Heatsinks
Passive heatsinks are the most common type of heatsink used in PCB design. They rely on natural convection to dissipate heat, without the use of any active cooling mechanisms. Passive heatsinks are typically made of aluminum or copper and feature fins or other protrusions to increase their surface area.
Passive heatsinks are often used in applications where the heat generated by the components is relatively low, or where the ambient temperature is not too high. They are also favored for their simplicity, reliability, and low cost.
Active Heatsinks
Active heatsinks, also known as fan-cooled heatsinks, combine a passive heatsink with a fan to provide forced convection cooling. The fan actively blows air over the heatsink’s fins, significantly increasing the rate of heat dissipation compared to passive heatsinks.
Active heatsinks are used in applications where the heat generated by the components is too high to be effectively managed by passive heatsinks alone. They are commonly found in high-performance computing systems, graphics cards, and power electronics.
However, active heatsinks do have some drawbacks, such as increased noise, power consumption, and potential failure points due to the presence of moving parts (the fan).
Heatpipes
Heatpipes are a more advanced type of heatsink that uses a phase-change mechanism to efficiently transfer heat from the source to a remote heatsink. A heatpipe consists of a sealed tube containing a working fluid, such as water or alcohol, that undergoes a phase change (evaporation and condensation) to transfer heat.
As the heat source warms the heatpipe, the working fluid evaporates, carrying the heat to the cooler end of the pipe. There, the fluid condenses, releasing the heat to the heatsink, and then flows back to the heat source through capillary action or gravity, completing the cycle.
Heatpipes are often used in applications where the heat source is located far from the heatsink, or where a high level of heat transfer efficiency is required. They are commonly found in laptops, high-end graphics cards, and some industrial applications.
Liquid Cooling Systems
Liquid cooling systems are the most advanced type of heatsink used in PCB design. They use a liquid coolant, such as water or a specialized dielectric fluid, to transfer heat away from the components. The coolant is pumped through a closed-loop system, which typically includes a cold plate (in contact with the heat source), tubing, a radiator, and a pump.
As the coolant flows through the cold plate, it absorbs heat from the component. The heated coolant then flows through the tubing to the radiator, where it is cooled by air flowing over the radiator’s fins. The cooled coolant then returns to the cold plate, completing the cycle.
Liquid cooling systems offer the highest level of heat dissipation performance, making them ideal for high-power applications or extreme overclocking in high-performance computing. However, they are also the most complex and expensive type of heatsink, and require careful design and maintenance to ensure reliable operation.
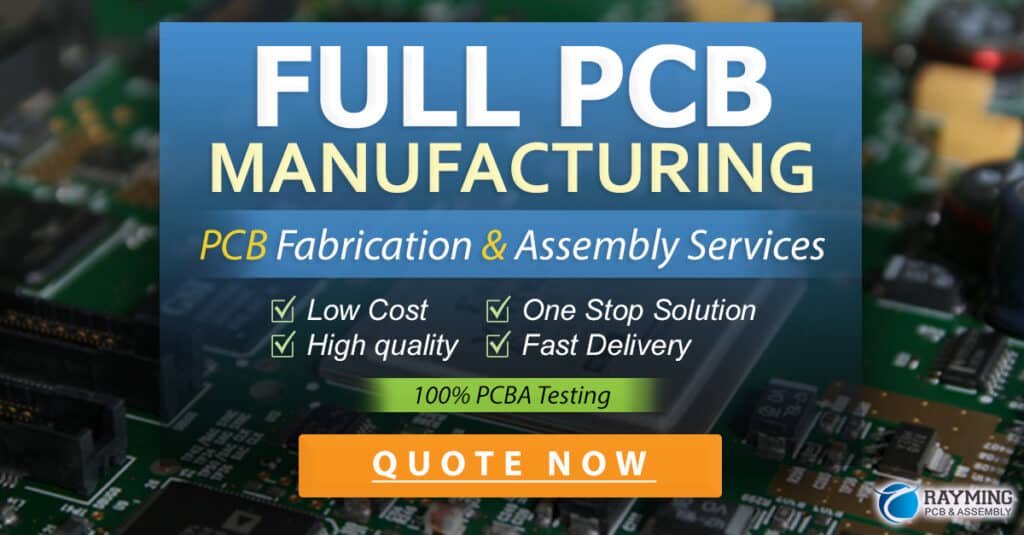
PCB Design Considerations for Heatsinks
Thermal Interface Materials
To ensure efficient heat transfer from the component to the heatsink, it is essential to use a thermal interface material (TIM) between the two surfaces. TIMs are designed to fill any microscopic air gaps or irregularities between the component and heatsink, which would otherwise impede heat transfer.
Common TIMs include thermal greases, thermal pads, and phase-change materials. Each type has its own advantages and disadvantages in terms of ease of application, thermal performance, and long-term reliability.
Heatsink Mounting and Orientation
Proper mounting and orientation of the heatsink are crucial for optimal heat dissipation. The heatsink should be securely attached to the component using an appropriate mounting mechanism, such as screws, clips, or adhesives. A loose or improperly mounted heatsink can result in poor thermal contact and reduced heat transfer efficiency.
The orientation of the heatsink should also be considered, particularly for passive heatsinks that rely on natural convection. In general, heatsinks should be oriented to allow for the most efficient airflow over the fins, typically with the fins aligned vertically to promote the natural convection of hot air rising.
Airflow and Ventilation
Adequate airflow and ventilation are essential for the proper functioning of heatsinks, particularly in enclosed systems such as computer cases or electronics enclosures. The placement of components and heatsinks should be optimized to ensure that there is sufficient space for air to flow around the heatsinks, and that hot air can be efficiently exhausted from the system.
In some cases, additional fans or ventilation holes may be necessary to provide adequate airflow and prevent heat buildup within the enclosure.
Frequently Asked Questions (FAQ)
-
Q: What materials are heatsinks typically made of?
A: Heatsinks are usually made of materials with high thermal conductivity, such as aluminum or copper. Aluminum is more commonly used due to its lower cost and weight, while copper offers better thermal performance but is more expensive and heavier. -
Q: How do I choose the right heatsink for my application?
A: When selecting a heatsink, consider factors such as the amount of heat generated by the component, the available space for the heatsink, the desired cooling performance, and the cost. It’s often helpful to use thermal simulation software or consult with a thermal engineer to determine the most appropriate heatsink for your specific application. -
Q: Can I use a heatsink without a thermal interface material?
A: While it is possible to use a heatsink without a thermal interface material, it is not recommended. The microscopic air gaps between the component and heatsink can significantly impede heat transfer, reducing the effectiveness of the heatsink. Always use an appropriate TIM to ensure optimal thermal performance. -
Q: How do I maintain my heatsink for optimal performance?
A: To maintain your heatsink’s performance, periodically clean it to remove any dust or debris that may accumulate on the fins. Dust can act as an insulator, reducing the heatsink’s ability to dissipate heat. In addition, ensure that the heatsink remains securely mounted to the component and that the thermal interface material is in good condition. -
Q: Can I use a heatsink designed for one component on another component?
A: In general, it is not recommended to use a heatsink designed for one component on another, as the thermal characteristics and mounting requirements may differ. However, in some cases, it may be possible to use a generic heatsink or adapt a heatsink designed for a similar component, provided that it offers adequate cooling performance and can be properly mounted to the component in question.
Conclusion
Heatsinks play a vital role in PCB design, ensuring that electronic components operate within their safe temperature limits and maintain optimal performance. By understanding the different types of heatsinks available and considering factors such as thermal interface materials, mounting, and airflow, designers can effectively manage heat dissipation in their PCB layouts.
As electronic systems continue to become more powerful and compact, the importance of effective heat management will only continue to grow. By staying informed about the latest heatsink technologies and design techniques, PCB designers can create reliable, high-performance systems that can withstand the demands of modern applications.
Leave a Reply