Introduction to HDI PCB Design
High Density Interconnect (HDI) PCB design is a cutting-edge technology that enables the creation of highly complex and compact printed circuit boards. HDI PCBs are characterized by their fine pitch traces, small vias, and high layer count, which allow for greater functionality and performance in a smaller footprint. This technology has become increasingly important in today’s electronics industry, where the demand for smaller, faster, and more powerful devices continues to grow.
Key Features of HDI PCB Design
- Fine pitch traces: HDI PCBs feature traces with a width and spacing of 3 mil or less, allowing for higher circuit density and improved signal integrity.
- Small vias: The use of microvias and buried vias in HDI PCBs enables more efficient interconnections between layers, reducing the overall size of the board.
- High layer count: HDI PCBs often have 8 or more layers, providing ample space for complex circuitry and enabling 3D routing of signals.
Benefits of HDI PCB Design
Space Savings
One of the primary benefits of HDI PCB design is the significant space savings it offers compared to traditional PCB designs. By utilizing fine pitch traces and small vias, HDI PCBs can accommodate a higher density of components and circuitry in a smaller area. This is particularly important for applications where size is a critical factor, such as in mobile devices, wearables, and IoT sensors.
Improved Signal Integrity
HDI PCB design also contributes to improved signal integrity, which is essential for high-speed and high-frequency applications. The use of fine pitch traces and controlled impedance routing helps to minimize signal reflections, crosstalk, and electromagnetic interference (EMI). Additionally, the shorter signal paths made possible by the compact nature of HDI PCBs further reduce signal attenuation and distortion.
Enhanced Reliability
The high-density interconnections and advanced manufacturing techniques used in HDI PCB design contribute to enhanced reliability. The use of microvias and buried vias, for example, reduces the risk of thermal stress and mechanical damage compared to through-hole vias. Furthermore, HDI PCBs often employ advanced materials, such as low-loss dielectrics and high-temperature laminates, which improve the board’s durability and long-term performance.
HDI PCB Manufacturing Process
The manufacturing process for HDI PCBs is more complex and precise than that of traditional PCBs. It involves several advanced techniques and technologies to achieve the high-density interconnections and fine features required.
Laser Drilling
One of the key processes in HDI PCB manufacturing is laser drilling. Unlike mechanical drilling, which is used for larger vias, laser drilling is employed to create microvias with diameters as small as 50 microns. This process uses a focused laser beam to ablate the dielectric material, creating precise and clean via holes.
Sequential Lamination
HDI PCBs often require sequential lamination, a process in which the board is built up in stages. This involves laminating, drilling, and plating each layer separately before combining them into the final board stack-up. Sequential lamination allows for the creation of buried vias and enables more complex interconnections between layers.
Copper Filling
After laser drilling, the microvias need to be filled with copper to establish electrical connections between layers. This is typically done using electroless copper plating, followed by electrolytic copper plating. The copper filling process ensures reliable and low-resistance interconnections within the HDI PCB.
Surface Finishing
The final step in the HDI PCB manufacturing process is surface finishing. This involves applying a protective and conductive coating to the exposed copper surfaces of the board. Common surface finishes for HDI PCBs include Immersion Gold (ENIG), Electroless Nickel Electroless Palladium Immersion Gold (ENEPIG), and Organic Solderability Preservative (OSP). The choice of surface finish depends on the specific requirements of the application, such as solderability, durability, and cost.
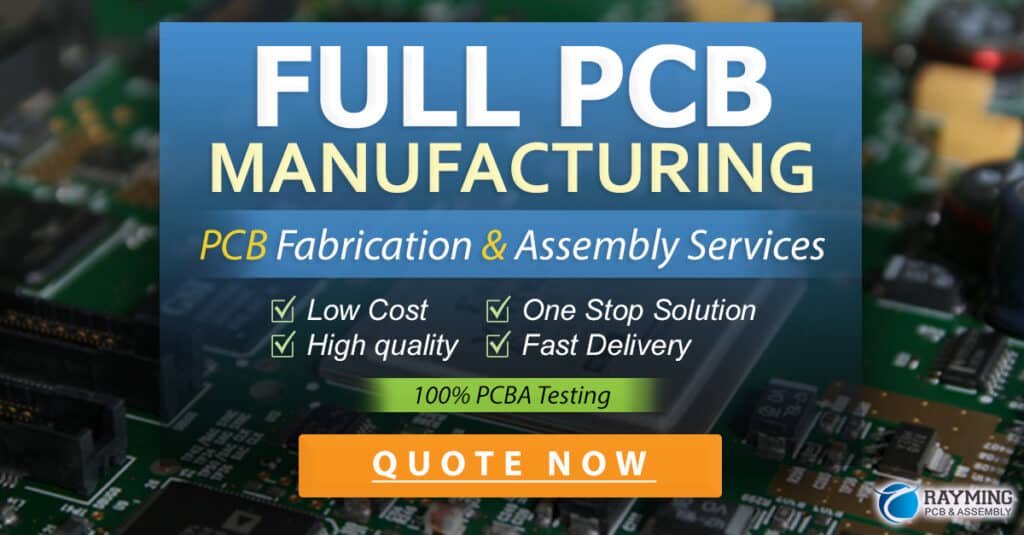
HDI PCB Design Considerations
Designing an HDI PCB requires careful consideration of several factors to ensure optimal performance, reliability, and manufacturability.
Stack-up Design
The stack-up design is a critical aspect of HDI PCB design. It involves determining the number of layers, the arrangement of signal, power, and ground planes, and the placement of vias. A well-designed stack-up ensures proper signal integrity, power distribution, and thermal management. It also takes into account the specific requirements of the application, such as impedance control and EMI shielding.
Via Types and Placement
HDI PCBs employ various types of vias, including through-hole vias, blind vias, buried vias, and microvias. The choice of via type and their placement depends on the design requirements and the manufacturing capabilities. For example, microvias are typically used for high-density interconnections between adjacent layers, while buried vias are used for connections between inner layers. Proper via placement is crucial for signal integrity, manufacturability, and reliability.
Trace Routing
Trace routing in HDI PCB design requires careful planning and execution to ensure optimal signal integrity and manufacturability. The use of fine pitch traces necessitates precise control over trace width, spacing, and impedance. Additionally, the routing strategy should minimize signal skew, crosstalk, and EMI. Advanced routing techniques, such as 3D routing and differential pair routing, are often employed in HDI PCB design to achieve these goals.
Thermal Management
Thermal management is a critical consideration in HDI PCB design, as the high density of components and circuitry can lead to increased heat generation. Proper thermal management involves the use of thermal vias, heat sinks, and other cooling solutions to dissipate heat effectively. The stack-up design also plays a role in thermal management, as the placement of power and ground planes can help to spread heat evenly across the board.
Applications of HDI PCB Design
HDI PCB design finds applications in a wide range of industries and products, where high performance, compact size, and reliability are essential.
Consumer Electronics
HDI PCBs are extensively used in consumer electronics, such as smartphones, tablets, laptops, and wearables. These devices require high-density interconnections and compact form factors to accommodate advanced features and functionality. HDI PCB design enables the integration of multiple functions, such as processors, memory, sensors, and wireless connectivity, into a single, compact package.
Automotive Electronics
The automotive industry is increasingly adopting HDI PCB design for advanced driver assistance systems (ADAS), infotainment systems, and vehicle networking. HDI PCBs provide the necessary performance, reliability, and space savings required for these safety-critical applications. They also enable the integration of multiple sensors, cameras, and communication modules, which are essential for autonomous driving and connected vehicle technologies.
Medical Devices
HDI PCB design is also finding applications in medical devices, such as implantable electronics, diagnostic equipment, and wearable health monitors. These devices require high reliability, small form factors, and low power consumption, which can be achieved through HDI PCB design. The use of biocompatible materials and advanced manufacturing techniques ensures that these devices meet the stringent safety and regulatory requirements of the medical industry.
Aerospace and Defense
The aerospace and defense industries rely on HDI PCB design for a range of applications, including avionics, radar systems, and satellite communications. HDI PCBs provide the necessary performance, reliability, and space savings required for these mission-critical applications. They also enable the integration of advanced technologies, such as phased array antennas and high-speed data processing, which are essential for modern aerospace and defense systems.
Future Trends in HDI PCB Design
As the demand for smaller, faster, and more powerful electronics continues to grow, HDI PCB design is expected to evolve to meet these challenges.
Advanced Materials
The development of advanced materials, such as low-loss dielectrics, high-temperature laminates, and embedded components, will enable further miniaturization and performance improvements in HDI PCBs. These materials will also contribute to enhanced reliability and durability, especially in harsh environmental conditions.
3D Printing
The integration of 3D printing technologies into HDI PCB manufacturing is another potential trend. 3D printing can enable the creation of complex, three-dimensional structures, such as embedded cooling channels and conformal shielding. This technology can also accelerate prototyping and reduce manufacturing costs for low-volume production.
Artificial Intelligence and Machine Learning
The application of artificial intelligence (AI) and machine learning (ML) in HDI PCB design and manufacturing is expected to grow in the coming years. These technologies can help to optimize design parameters, predict potential issues, and improve manufacturing yields. AI and ML can also enable the creation of adaptive and self-healing HDI PCBs, which can automatically detect and correct faults during operation.
Conclusion
HDI PCB design is a critical technology that enables the creation of compact, high-performance, and reliable electronics. By utilizing fine pitch traces, small vias, and high layer counts, HDI PCBs offer significant space savings, improved signal integrity, and enhanced reliability compared to traditional PCB designs. The manufacturing process for HDI PCBs involves advanced techniques, such as laser drilling, sequential lamination, and copper filling, to achieve the required high-density interconnections and fine features.
Designing an HDI PCB requires careful consideration of factors such as stack-up design, via types and placement, trace routing, and thermal management. These considerations ensure optimal performance, reliability, and manufacturability. HDI PCB design finds applications in a wide range of industries, including consumer electronics, automotive, medical devices, and aerospace and defense.
As the electronics industry continues to evolve, HDI PCB design is expected to adapt and incorporate advanced materials, 3D printing technologies, and artificial intelligence to meet the growing demands for smaller, faster, and more powerful devices.
Frequently Asked Questions (FAQ)
1. What is the difference between HDI PCBs and traditional PCBs?
HDI PCBs differ from traditional PCBs in several ways. They feature finer pitch traces, smaller vias, and higher layer counts, enabling greater circuit density and improved performance in a smaller footprint. Traditional PCBs, on the other hand, have larger traces, vias, and fewer layers, making them suitable for less complex and less space-constrained applications.
2. What are the key benefits of using HDI PCB design?
The key benefits of HDI PCB design include:
– Space savings: HDI PCBs can accommodate a higher density of components and circuitry in a smaller area.
– Improved signal integrity: Fine pitch traces and controlled impedance routing minimize signal reflections, crosstalk, and EMI.
– Enhanced reliability: Advanced manufacturing techniques and materials contribute to improved durability and long-term performance.
3. What are the different types of vias used in HDI PCBs?
HDI PCBs employ various types of vias, including:
– Through-hole vias: These vias extend through all layers of the PCB.
– Blind vias: These vias connect an outer layer to an inner layer, but do not extend through the entire board.
– Buried vias: These vias connect inner layers without extending to the outer layers.
– Microvias: These are small, laser-drilled vias that typically connect adjacent layers.
4. What industries commonly use HDI PCB design?
HDI PCB design is commonly used in industries that require high-performance, compact, and reliable electronics. These include:
– Consumer electronics: Smartphones, tablets, laptops, and wearables.
– Automotive: Advanced driver assistance systems, infotainment systems, and vehicle networking.
– Medical devices: Implantable electronics, diagnostic equipment, and wearable health monitors.
– Aerospace and defense: Avionics, radar systems, and satellite communications.
5. What are some future trends in HDI PCB design?
Some future trends in HDI PCB design include:
– Advanced materials: Low-loss dielectrics, high-temperature laminates, and embedded components for further miniaturization and performance improvements.
– 3D printing: Integration of 3D printing technologies for creating complex, three-dimensional structures and accelerating prototyping.
– Artificial intelligence and machine learning: Application of AI and ML for optimizing design parameters, predicting issues, and improving manufacturing yields.
HDI PCB Feature | Description |
---|---|
Fine Pitch Traces | Traces with a width and spacing of 3 mil or less, allowing for higher circuit density and improved signal integrity. |
Small Vias | The use of microvias and buried vias enables more efficient interconnections between layers, reducing the overall size of the board. |
High Layer Count | HDI PCBs often have 8 or more layers, providing ample space for complex circuitry and enabling 3D routing of signals. |
HDI PCB Benefit | Description |
---|---|
Space Savings | HDI PCBs can accommodate a higher density of components and circuitry in a smaller area. |
Improved Signal Integrity | Fine pitch traces and controlled impedance routing minimize signal reflections, crosstalk, and EMI. |
Enhanced Reliability | Advanced manufacturing techniques and materials contribute to improved durability and long-term performance. |
Leave a Reply