Introduction to HASL in PCB Manufacturing
HASL, which stands for Hot Air Solder Leveling, is a widely used surface finish technique in the manufacturing of printed circuit boards (PCBs). This process involves applying a layer of molten solder to the exposed copper pads and through-holes of a PCB, followed by the use of hot air to remove excess solder and create a smooth, level surface. HASL has been a popular choice for PCB manufacturers due to its cost-effectiveness, reliability, and compatibility with a wide range of components and soldering techniques.
The Importance of Surface Finishes in PCB Manufacturing
Surface finishes play a crucial role in PCB manufacturing by providing protection against oxidation, enhancing solderability, and improving the overall reliability of the circuit board. Various surface finish options are available, each with its own advantages and disadvantages. Some common surface finishes include:
- HASL (Hot Air Solder Leveling)
- ENIG (Electroless Nickel Immersion Gold)
- OSP (Organic Solderability Preservative)
- Immersion Silver
- Immersion Tin
The choice of surface finish depends on factors such as the intended application, environmental conditions, cost, and compatibility with the components and soldering processes used.
The HASL Process
Step 1: Cleaning and Preparation
Before applying the HASL finish, the PCB undergoes a thorough cleaning process to remove any contaminants, such as dirt, grease, or oxidation, from the copper surfaces. This step is critical to ensure proper adhesion of the solder and to achieve a consistent finish.
Step 2: Fluxing
A thin layer of flux is applied to the exposed copper surfaces of the PCB. Flux is a chemical agent that helps to remove any remaining oxidation, improves the wetting of the solder, and promotes the formation of a strong metallic bond between the solder and the copper.
Step 3: Solder Dipping
The PCB is then dipped into a molten solder bath, typically consisting of a tin-lead alloy (e.g., 63/37 or 60/40). The solder bath temperature is carefully controlled, usually between 240°C and 260°C (464°F to 500°F), to ensure optimal wetting and flow of the solder.
Step 4: Hot Air Leveling
After the PCB is removed from the solder bath, it is subjected to a hot air knife or a series of air nozzles. The hot air removes excess solder from the surface of the PCB, leaving a thin, even layer of solder on the exposed copper areas. This process also helps to create a smooth, level surface, ensuring good contact with the components during the assembly process.
Step 5: Cleaning and Inspection
Following the hot air leveling process, the PCB is cleaned to remove any residual flux or contaminants. The board is then inspected visually and using automated optical inspection (AOI) systems to ensure the HASL finish meets the required quality standards.
Advantages of HASL
Cost-effectiveness
HASL is one of the most cost-effective surface finish options available, making it a popular choice for high-volume production runs and budget-constrained projects. The materials and equipment used in the HASL process are relatively inexpensive compared to other surface finishes like ENIG or Immersion Silver.
Compatibility
HASL is compatible with a wide range of components and soldering processes, including through-hole and surface mount technologies (SMT). It is suitable for both hand soldering and automated soldering processes, such as wave soldering or reflow soldering.
Durability
The HASL finish provides good protection against oxidation and corrosion, ensuring the long-term reliability of the PCB. The solder layer also offers a degree of mechanical protection to the copper traces and pads, reducing the risk of damage during handling and assembly.
Reworkability
PCBs with a HASL finish are relatively easy to rework or repair, as the solder can be easily removed and reapplied using standard soldering techniques. This is particularly advantageous for prototyping or low-volume production, where design changes or repairs may be more frequent.
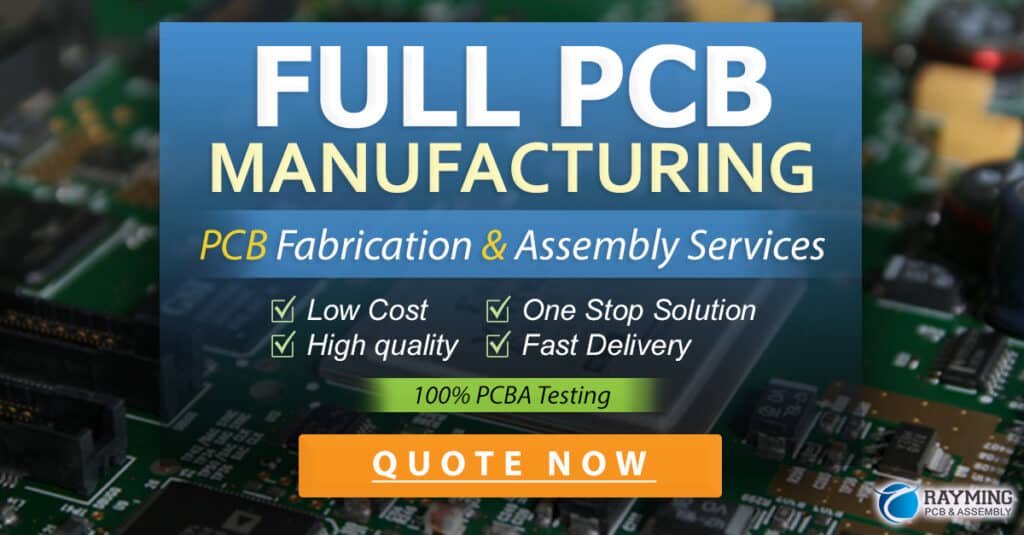
Disadvantages of HASL
Uneven Surface
One of the main drawbacks of the HASL process is that it can result in an uneven surface finish, particularly on fine-pitch components or high-density designs. The hot air leveling process may not completely remove all the excess solder, leading to variations in solder thickness across the board. This unevenness can cause issues with component placement and soldering, especially for surface mount devices with small pitch sizes.
Thermal Shock
During the HASL process, the PCB is subjected to high temperatures when dipped into the molten solder bath. This sudden exposure to heat can cause thermal shock, potentially leading to warping or delamination of the board. The risk of thermal shock is higher for thicker boards or those with high layer counts.
Solder Bridging
The uneven surface created by the HASL process can also increase the risk of solder bridging between closely spaced pads or traces. Solder bridging can lead to short circuits and other functional issues, requiring additional inspection and rework.
Limited Shelf Life
PCBs with a HASL finish have a shorter shelf life compared to other surface finishes like ENIG or OSP. The exposed solder surface can oxidize over time, reducing solderability and potentially causing issues during assembly. Manufacturers typically recommend assembling HASL-finished boards within 6 to 12 months of production to ensure optimal solderability.
HASL vs. Other Surface Finishes
When comparing HASL to other common surface finishes, it is essential to consider the specific requirements of the application and the trade-offs between cost, performance, and manufacturability.
Surface Finish | Advantages | Disadvantages |
---|---|---|
HASL | – Cost-effective – Compatible with most components and soldering processes – Good durability and reworkability |
– Uneven surface – Risk of thermal shock and solder bridging – Limited shelf life |
ENIG | – Flat, even surface – Excellent solderability and shelf life – Suitable for fine-pitch components |
– Higher cost – Potential for “black pad” defect – Longer processing time |
OSP | – Low cost – Flat surface – Suitable for fine-pitch components |
– Limited shelf life – Not suitable for multiple reflow cycles – Potential for poor wetting |
Immersion Silver | – Flat, even surface – Good solderability – Suitable for fine-pitch components |
– Higher cost than HASL and OSP – Risk of silver migration – Potential for tarnishing over time |
Immersion Tin | – Flat, even surface – Good solderability – Suitable for fine-pitch components |
– Higher cost than HASL and OSP – Potential for tin whiskers – Limited shelf life compared to ENIG |
Frequently Asked Questions (FAQ)
1. What does HASL stand for in PCB manufacturing?
HASL stands for Hot Air Solder Leveling, a surface finish process that involves applying a layer of molten solder to the exposed copper pads and through-holes of a PCB, followed by the use of hot air to remove excess solder and create a smooth, level surface.
2. Is HASL suitable for fine-pitch components?
While HASL is compatible with most components and soldering processes, it may not be the best choice for fine-pitch components due to the potential for an uneven surface finish. Other surface finishes, such as ENIG, OSP, or Immersion Silver, may be more suitable for high-density designs with small pitch sizes.
3. What is the shelf life of a HASL-finished PCB?
PCBs with a HASL finish typically have a shelf life of 6 to 12 months, after which the exposed solder surface may oxidize, reducing solderability and potentially causing issues during assembly. It is recommended to assemble HASL-finished boards within this timeframe to ensure optimal solderability.
4. Can HASL-finished PCBs be reworked or repaired?
Yes, PCBs with a HASL finish are relatively easy to rework or repair, as the solder can be easily removed and reapplied using standard soldering techniques. This makes HASL a good choice for prototyping or low-volume production, where design changes or repairs may be more frequent.
5. What are the main advantages of using HASL as a surface finish?
The main advantages of using HASL as a surface finish include its cost-effectiveness, compatibility with a wide range of components and soldering processes, good durability, and ease of reworkability. These factors make HASL a popular choice for many PCB manufacturers and applications.
Conclusion
HASL (Hot Air Solder Leveling) is a widely used surface finish technique in PCB manufacturing, offering a cost-effective and reliable solution for protecting exposed copper surfaces and enhancing solderability. While it has some limitations, such as the potential for an uneven surface and limited shelf life, HASL remains a popular choice for many applications due to its compatibility with various components and soldering processes, as well as its durability and ease of reworkability.
When selecting a surface finish for a PCB project, it is essential to consider the specific requirements of the application, including the components used, the soldering processes involved, and the environmental conditions the board will be exposed to. By understanding the advantages and disadvantages of HASL and other surface finishes, PCB designers and manufacturers can make informed decisions that balance cost, performance, and manufacturability to ensure the success of their projects.
Leave a Reply