What is FR4 Material?
FR4 is a composite material made up of woven fiberglass cloth impregnated with an epoxy resin binder. The “FR” in FR4 stands for “Flame Retardant,” indicating that the material has been treated to resist burning. The “4” refers to the specific grade of the material, which is determined by the National Electrical Manufacturers Association (NEMA).
FR4 is a popular choice for PCBs because of its excellent properties, including:
- High mechanical strength and stiffness
- Good electrical insulation properties
- Excellent thermal stability
- Resistance to moisture absorption
- Flame retardant properties
FR4 PCB Manufacturing Process
The manufacturing process of FR4 PCB involves several steps, including:
-
Cutting the FR4 Laminate: The FR4 laminate is cut to the desired size and shape using a CNC machine or a laser cutter.
-
Drilling Holes: Holes are drilled into the FR4 laminate using a CNC drilling machine. These holes are used for mounting components and creating electrical connections between layers.
-
Copper Cladding: A thin layer of copper is laminated onto the FR4 substrate using heat and pressure. The copper layer is typically 1-2 oz in thickness.
-
Patterning the Copper Layer: The copper layer is then patterned using a photolithography process. This involves applying a photoresist layer onto the copper, exposing it to UV light through a photomask, and then developing the photoresist to remove the unexposed areas.
-
Etching the Copper: The exposed copper is then etched away using a chemical solution, leaving behind the desired copper pattern.
-
Applying Solder Mask: A solder mask layer is applied onto the PCB to protect the copper traces and prevent short circuits. The solder mask is typically green in color, but other colors are also available.
-
Applying Silkscreen: A silkscreen layer is applied onto the PCB to add text, logos, and other markings.
-
Surface Finish: A surface finish, such as HASL (Hot Air Solder Leveling), ENIG (Electroless Nickel Immersion Gold), or OSP (Organic Solderability Preservative), is applied onto the exposed copper pads to prevent oxidation and improve solderability.
FR4 PCB Properties
FR4 PCB has several properties that make it an ideal choice for a wide range of applications. These properties include:
Mechanical Properties
FR4 has excellent mechanical properties, including high strength and stiffness. It has a tensile strength of 310 MPa and a flexural strength of 415 MPa. This makes it ideal for applications that require high mechanical strength, such as automotive and aerospace electronics.
Electrical Properties
FR4 has good electrical insulation properties, with a dielectric constant of 4.5 at 1 MHz and a dielectric strength of 20 kV/mm. It also has a low dissipation factor of 0.02 at 1 MHz, which makes it suitable for high-frequency applications.
Thermal Properties
FR4 has excellent thermal stability, with a glass transition temperature (Tg) of 130-140°C and a decomposition temperature of 340°C. This makes it suitable for applications that require high-temperature resistance, such as power electronics and automotive electronics.
Flammability
FR4 is treated with flame retardants to make it resistant to burning. It has a flammability rating of UL94 V-0, which means that it will self-extinguish within 10 seconds after being exposed to a flame.
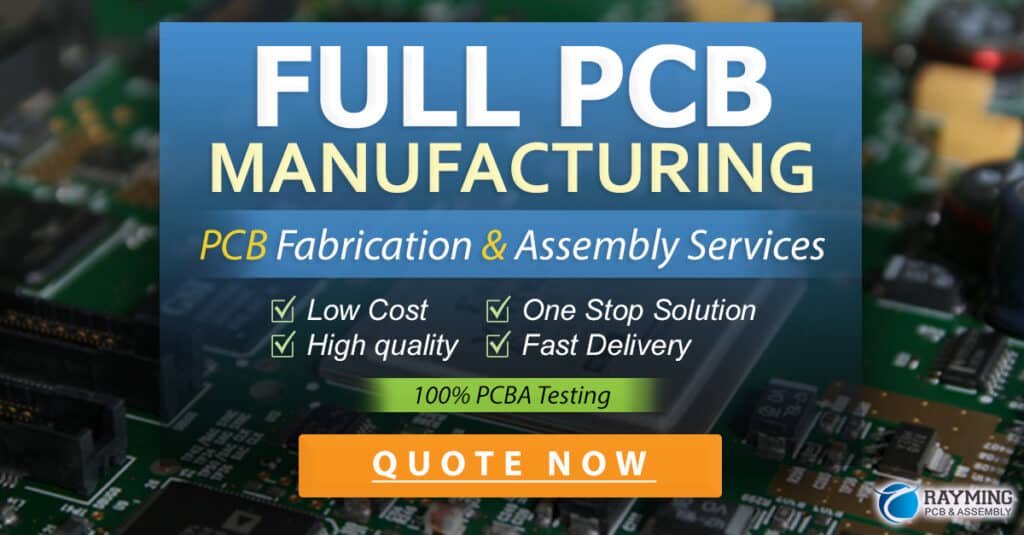
FR4 PCB Applications
FR4 PCB is used in a wide range of applications, including:
- Consumer electronics, such as smartphones, tablets, and laptops
- Automotive electronics, such as engine control units, infotainment systems, and advanced driver assistance systems (ADAS)
- Industrial electronics, such as controllers, sensors, and power supplies
- Medical electronics, such as patient monitors, diagnostic equipment, and imaging devices
- Aerospace and defense electronics, such as avionics, radar systems, and communication devices
Advantages of FR4 PCB
FR4 PCB has several advantages over other PCB materials, including:
- Lower cost compared to other high-performance PCB materials, such as polyimide and PTFE
- Excellent mechanical strength and stiffness, making it suitable for applications that require high reliability
- Good electrical insulation properties, making it suitable for high-voltage applications
- Excellent thermal stability, making it suitable for high-temperature applications
- Flame retardant properties, making it safer to use in applications where fire is a concern
Disadvantages of FR4 PCB
Despite its many advantages, FR4 PCB also has some disadvantages, including:
- Limited high-frequency performance compared to other PCB materials, such as Rogers and Teflon
- Higher moisture absorption compared to other PCB materials, which can affect its electrical properties over time
- Lower thermal conductivity compared to other PCB materials, such as aluminum and copper
FR4 PCB vs Other PCB Materials
FR4 PCB is just one of many PCB materials available in the market. Other common PCB materials include:
Polyimide
Polyimide is a high-performance PCB material that is known for its excellent thermal stability and mechanical strength. It has a glass transition temperature (Tg) of 260°C and a tensile strength of 231 MPa. Polyimide is often used in applications that require high-temperature resistance, such as aerospace and defense electronics.
PTFE
PTFE, or polytetrafluoroethylene, is a high-performance PCB material that is known for its excellent high-frequency performance and low dielectric constant. It has a dielectric constant of 2.1 and a dissipation factor of 0.0002 at 10 GHz. PTFE is often used in applications that require high-frequency performance, such as radar systems and communication devices.
Aluminum
Aluminum PCBs are known for their excellent thermal conductivity and mechanical strength. They are often used in applications that require high power dissipation, such as LED lighting and power electronics.
Comparison Table
Property | FR4 | Polyimide | PTFE | Aluminum |
---|---|---|---|---|
Dielectric Constant (1 MHz) | 4.5 | 3.5 | 2.1 | – |
Dissipation Factor (1 MHz) | 0.02 | 0.002 | 0.0002 | – |
Thermal Conductivity (W/mK) | 0.3 | 0.2 | 0.2 | 150 |
Tensile Strength (MPa) | 310 | 231 | 25 | 310 |
Glass Transition Temperature (°C) | 130-140 | 260 | 327 | – |
Flammability Rating | UL94 V-0 | UL94 V-0 | UL94 V-0 | – |
As we can see from the table above, each PCB material has its own unique properties and advantages. The choice of PCB material depends on the specific requirements of the application, such as operating temperature, frequency, and power dissipation.
FAQ
1. What does FR4 stand for?
FR4 stands for Flame Retardant 4, which is a type of PCB material that is treated with flame retardants to make it resistant to burning.
2. What are the advantages of using FR4 PCB?
FR4 PCB has several advantages, including lower cost, excellent mechanical strength and stiffness, good electrical insulation properties, excellent thermal stability, and flame retardant properties.
3. What are the disadvantages of using FR4 PCB?
FR4 PCB has some disadvantages, including limited high-frequency performance, higher moisture absorption, and lower thermal conductivity compared to other PCB materials.
4. What are some common applications of FR4 PCB?
FR4 PCB is used in a wide range of applications, including consumer electronics, automotive electronics, industrial electronics, medical electronics, and aerospace and defense electronics.
5. How does FR4 PCB compare to other PCB materials?
FR4 PCB has different properties compared to other PCB materials, such as polyimide, PTFE, and aluminum. Each material has its own unique advantages and disadvantages, and the choice of material depends on the specific requirements of the application.
Conclusion
FR4 PCB is a popular choice for a wide range of applications due to its excellent mechanical, thermal, and electrical properties. It is a cost-effective solution for applications that require high reliability, good electrical insulation, and flame retardant properties. However, it also has some limitations, such as limited high-frequency performance and higher moisture absorption compared to other PCB materials.
When choosing a PCB material, it is important to consider the specific requirements of the application, such as operating temperature, frequency, and power dissipation. FR4 PCB is a good choice for many applications, but other materials such as polyimide, PTFE, and aluminum may be more suitable for certain applications.
In conclusion, FR4 PCB is a versatile and reliable PCB material that has been widely used in the electronics industry for many years. Its excellent properties and cost-effectiveness make it a popular choice for a wide range of applications, from consumer electronics to aerospace and defense. As technology continues to advance, it is likely that FR4 PCB will continue to play an important role in the electronics industry for many years to come.
Leave a Reply