Introduction to FPC PCB
Flexible Printed Circuit (FPC) PCB is a type of printed circuit board that is designed to be flexible and bendable. Unlike traditional rigid PCBs, FPC PCBs are made from thin, flexible materials such as polyimide or polyester film, which allows them to conform to various shapes and fit into tight spaces. This makes them ideal for applications where space is limited or where the board needs to flex or move, such as in wearable devices, medical equipment, and consumer electronics.
What are the Benefits of FPC PCB?
FPC PCBs offer several advantages over traditional rigid PCBs, including:
-
Flexibility: FPC PCBs can bend and flex without breaking, making them ideal for applications where the board needs to conform to a specific shape or move with the device.
-
Space-saving: Because FPC PCBs are thin and flexible, they can fit into tight spaces and reduce the overall size of the device.
-
Lightweight: FPC PCBs are much lighter than rigid PCBs, which can be important for portable or wearable devices.
-
High reliability: FPC PCBs are highly reliable and can withstand repeated flexing and bending without failing.
-
Cost-effective: FPC PCBs can be more cost-effective than rigid PCBs, especially for high-volume production runs.
Types of FPC PCB
There are several types of FPC PCBs, each with its own unique properties and applications.
Single-sided FPC PCB
Single-sided FPC PCBs have conductive traces on only one side of the substrate material. They are the simplest and most cost-effective type of FPC PCB, but they have limited routing options and may not be suitable for complex designs.
Double-sided FPC PCB
Double-sided FPC PCBs have conductive traces on both sides of the substrate material, which allows for more complex routing and higher component density. They are more expensive than single-sided FPC PCBs but offer greater design flexibility.
Multi-layer FPC PCB
Multi-layer FPC PCBs have multiple layers of conductive traces separated by insulating layers. They offer the highest level of design flexibility and can accommodate very complex circuits, but they are also the most expensive type of FPC PCB.
Rigid-Flex PCB
Rigid-Flex PCBs combine the benefits of both rigid and flexible PCBs. They consist of one or more rigid PCB sections connected by flexible PCB sections, which allows for greater design flexibility and improved reliability in applications where the board needs to flex or move.
FPC PCB Materials
FPC PCBs are made from a variety of materials, each with its own unique properties and benefits.
Polyimide (PI)
Polyimide is the most common substrate material used in FPC PCBs. It offers excellent thermal and chemical resistance, high dielectric strength, and good mechanical properties. Polyimide is also highly flexible and can withstand repeated bending without failing.
Polyester (PET)
Polyester is another common substrate material used in FPC PCBs. It is less expensive than polyimide and offers good electrical properties, but it is not as thermally or chemically resistant.
Liquid Crystal Polymer (LCP)
Liquid Crystal Polymer is a high-performance substrate material that offers excellent electrical and mechanical properties. It has very low moisture absorption, high heat resistance, and good dimensional stability, making it ideal for applications that require high reliability and performance.
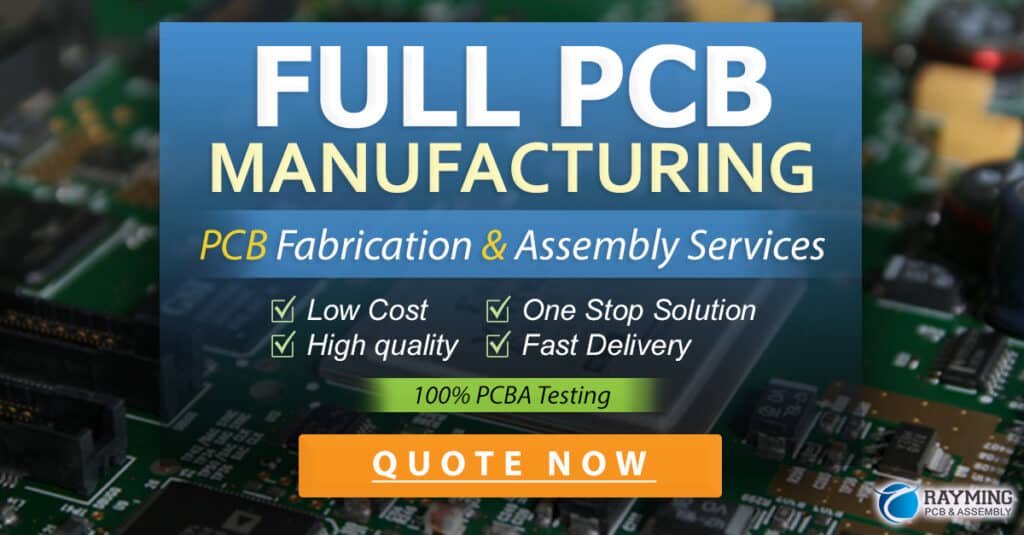
FPC PCB Manufacturing Process
The manufacturing process for FPC PCBs is similar to that of traditional rigid PCBs, but with a few key differences.
Circuit Design
The first step in the FPC PCB manufacturing process is circuit design. The circuit is designed using specialized software that takes into account the unique properties of the flexible substrate material.
Printing
Once the circuit design is complete, the conductive traces are printed onto the substrate material using a screen printing or photolithography process. The traces are typically made from copper, although other conductive materials may be used in some applications.
Etching
After the conductive traces are printed, the excess copper is etched away using a chemical etching process. This leaves only the desired circuit pattern on the substrate material.
Lamination
If the FPC PCB is a multi-layer design, the individual layers are laminated together using heat and pressure. The layers are aligned and bonded together to form a single, cohesive board.
Coverlay Application
A coverlay film is applied to the surface of the FPC PCB to protect the conductive traces and provide insulation. The coverlay is typically made from a polyimide or polyester material and is bonded to the board using heat and pressure.
Cutting and Drilling
The FPC PCB is then cut to the desired shape and size using a laser or mechanical cutting process. Any necessary holes or cutouts are also drilled or punched at this stage.
Surface Finish
Finally, a surface finish is applied to the exposed copper traces to protect them from oxidation and improve solderability. Common surface finishes include ENIG (Electroless Nickel Immersion Gold), OSP (Organic Solderability Preservative), and Immersion Silver.
FPC PCB Manufacturing Process | Description |
---|---|
Circuit Design | The circuit is designed using specialized software that takes into account the unique properties of the flexible substrate material. |
Printing | The conductive traces are printed onto the substrate material using a screen printing or photolithography process. |
Etching | The excess copper is etched away using a chemical etching process, leaving only the desired circuit pattern on the substrate material. |
Lamination | If the FPC PCB is a multi-layer design, the individual layers are laminated together using heat and pressure. |
Coverlay Application | A coverlay film is applied to the surface of the FPC PCB to protect the conductive traces and provide insulation. |
Cutting and Drilling | The FPC PCB is cut to the desired shape and size using a laser or mechanical cutting process, and any necessary holes or cutouts are drilled or punched. |
Surface Finish | A surface finish is applied to the exposed copper traces to protect them from oxidation and improve solderability. |
FPC PCB Applications
FPC PCBs are used in a wide range of applications where flexibility, space-saving, and lightweight design are important. Some common applications include:
Consumer Electronics
FPC PCBs are commonly used in consumer electronics devices such as smartphones, tablets, and laptops. They allow for thinner, more compact designs and can accommodate the complex circuitry required for high-performance devices.
Medical Devices
FPC PCBs are also used in medical devices such as hearing aids, pacemakers, and insulin pumps. They offer high reliability and can withstand the harsh environments and repeated flexing required in these applications.
Automotive Electronics
FPC PCBs are increasingly being used in automotive electronics, such as in-vehicle infotainment systems, camera modules, and sensor applications. They offer high reliability and can withstand the extreme temperatures and vibrations encountered in automotive environments.
Wearable Devices
FPC PCBs are ideal for wearable devices such as smartwatches, fitness trackers, and medical monitoring devices. They allow for lightweight, flexible designs that can conform to the shape of the human body and withstand repeated movement and flexing.
Aerospace and Defense
FPC PCBs are used in aerospace and defense applications where weight and space are at a premium, such as in satellites, drones, and military communication devices. They offer high reliability and can withstand the extreme temperatures and vibrations encountered in these environments.
FPC PCB Design Considerations
Designing an FPC PCB requires careful consideration of several key factors to ensure reliability, performance, and manufacturability.
Bend Radius
One of the most important design considerations for FPC PCBs is the bend radius. The bend radius is the minimum radius that the board can be bent without damaging the conductive traces or causing the board to fail. The bend radius depends on several factors, including the thickness and type of substrate material, the thickness and spacing of the conductive traces, and the type of adhesive used.
Trace Width and Spacing
The width and spacing of the conductive traces on an FPC PCB must be carefully designed to ensure proper signal integrity and avoid signal interference. The trace width and spacing depend on several factors, including the circuit design, the operating frequency, and the substrate material.
Stiffeners
Stiffeners are often used in FPC PCB designs to provide additional support and prevent the board from bending or flexing in undesired locations. Stiffeners are typically made from a rigid material such as FR-4 or aluminum and are bonded to the board using an adhesive.
Strain Relief
Strain relief is an important design consideration for FPC PCBs to prevent damage to the conductive traces or components due to repeated flexing or bending. Strain relief can be achieved through the use of stiffeners, mechanical supports, or by designing the circuit to minimize stress on the components and traces.
Shielding
Shielding may be required in some FPC PCB designs to prevent electromagnetic interference (EMI) from affecting the circuit performance. Shielding can be achieved through the use of conductive materials such as copper or aluminum, or through the use of shielding tapes or coatings.
FPC PCB Testing and Inspection
Testing and inspection are critical steps in the FPC PCB manufacturing process to ensure the quality and reliability of the finished board.
Visual Inspection
Visual inspection is the first step in the testing and inspection process. The board is visually inspected for any defects or anomalies, such as scratches, dents, or discoloration.
Continuity Testing
Continuity testing is performed to ensure that all of the conductive traces on the board are properly connected and that there are no open or short circuits. This is typically done using a multimeter or automated testing equipment.
Insulation Resistance Testing
Insulation resistance testing is performed to ensure that there is sufficient electrical insulation between the conductive traces and the substrate material. This is typically done using a high-voltage insulation tester.
Flexing Testing
Flexing testing is performed to ensure that the FPC PCB can withstand repeated flexing and bending without failing. The board is subjected to a series of bending and twisting tests to simulate real-world use conditions.
Environmental Testing
Environmental testing is performed to ensure that the FPC PCB can withstand the environmental conditions it will be exposed to in its intended application. This may include temperature cycling, humidity testing, and vibration testing.
FPC PCB Assembly
FPC PCB assembly is the process of attaching components to the board and connecting them to the conductive traces. FPC PCB assembly can be more challenging than traditional rigid PCB assembly due to the flexible nature of the board and the smaller size of the components.
Solder Paste Application
Solder paste is applied to the pads on the FPC PCB using a stencil or screen printing process. The solder paste consists of small beads of solder suspended in a flux matrix.
Component Placement
The components are placed onto the solder paste using a pick-and-place machine or by hand. The components must be carefully aligned with the pads on the board to ensure proper electrical connection.
Reflow Soldering
The board is then passed through a reflow oven, which melts the solder paste and permanently attaches the components to the board. The reflow profile must be carefully controlled to ensure proper solder joint formation and to avoid damaging the components or the board.
Inspection and Testing
After assembly, the board is inspected and tested to ensure proper functionality and reliability. This may include visual inspection, continuity testing, and functional testing.
FPC PCB Maintenance and Repair
Proper maintenance and repair of FPC PCBs can help extend their lifespan and ensure reliable operation over time.
Cleaning
FPC PCBs should be regularly cleaned to remove any dirt, dust, or contamination that may affect their performance. Cleaning can be done using specialized cleaning solutions and brushes or by using ultrasonic cleaning equipment.
Inspection
Regular visual inspection of FPC PCBs can help identify any signs of damage or wear, such as cracks, delamination, or discoloration. Early identification of these issues can help prevent more serious problems down the line.
Repair
If an FPC PCB is damaged or fails, it may be possible to repair it depending on the nature and extent of the damage. Common repair techniques include soldering, epoxy bonding, and replacing damaged components or sections of the board.
Conclusion
FPC PCBs offer many benefits over traditional rigid PCBs, including flexibility, space-saving, and lightweight design. They are used in a wide range of applications, from consumer electronics to medical devices to aerospace and defense. Proper design, manufacturing, testing, assembly, and maintenance are all critical to ensuring the reliability and performance of FPC PCBs over their intended lifespan.
As technology continues to advance and devices become smaller and more complex, the demand for FPC PCBs is only expected to grow. By understanding the unique properties and design considerations of FPC PCBs, engineers and manufacturers can create innovative and reliable products that meet the needs of today’s rapidly evolving market.
Frequently Asked Questions (FAQ)
-
What is the difference between an FPC PCB and a traditional rigid PCB?
FPC PCBs are made from flexible materials and can bend and flex without breaking, while traditional rigid PCBs are made from rigid materials and cannot flex. FPC PCBs are also typically thinner and lighter than rigid PCBs. -
What are the most common materials used for FPC PCBs?
The most common materials used for FPC PCBs are polyimide (PI) and polyester (PET). PI offers excellent thermal and chemical resistance and high dielectric strength, while PET is less expensive but not as thermally or chemically resistant. -
What are some common applications for FPC PCBs?
FPC PCBs are commonly used in consumer electronics, medical devices, automotive electronics, wearable devices, and aerospace and defense applications where flexibility, space-saving, and lightweight design are important. -
What is the bend radius of an FPC PCB?
The bend radius is the minimum radius that an FPC PCB can be bent without damaging the conductive traces or causing the board to fail. The bend radius depends on several factors, including the thickness and type of substrate material, the thickness and spacing of the conductive traces, and the type of adhesive used. -
How are FPC PCBs tested and inspected?
FPC PCBs are tested and inspected using a variety of methods, including visual inspection, continuity testing, insulation resistance testing, flexing testing, and environmental testing. These tests ensure that the board is free from defects and can withstand the environmental conditions it will be exposed to in its intended application.
Leave a Reply