Table of Contents
- What is Flux?
- The Role of Flux in PCB Assembly
- Types of Flux Used in PCBs
- Rosin Flux
- Water-Soluble Flux
- No-Clean Flux
- Advantages of Using Flux in PCBs
- Disadvantages of Using Flux in PCBs
- Flux Application Methods
- Foam Fluxing
- Spray Fluxing
- Wave Fluxing
- Cleaning Flux Residue
- Environmental Considerations
- Frequently Asked Questions (FAQ)
- Conclusion
What is Flux?
Flux is a chemical cleaning agent used in soldering to remove oxides and other contaminants from metal surfaces, promoting better wetting and a stronger bond between the solder and the metals being joined. In the context of printed circuit boards (PCBs), flux is applied to the board prior to soldering components to ensure a clean and reliable connection.
The Role of Flux in PCB Assembly
During PCB assembly, the board and its components are exposed to high temperatures, which can cause oxidation on the metal surfaces. This oxidation hinders the ability of the solder to adhere properly, leading to weak or faulty connections. Flux helps to:
- Remove oxides and contaminants from the metal surfaces
- Prevent re-oxidation during the soldering process
- Improve the wetting ability of the solder
- Promote the formation of a strong, reliable solder joint
Without flux, achieving consistent and high-quality solder connections would be extremely challenging, if not impossible.
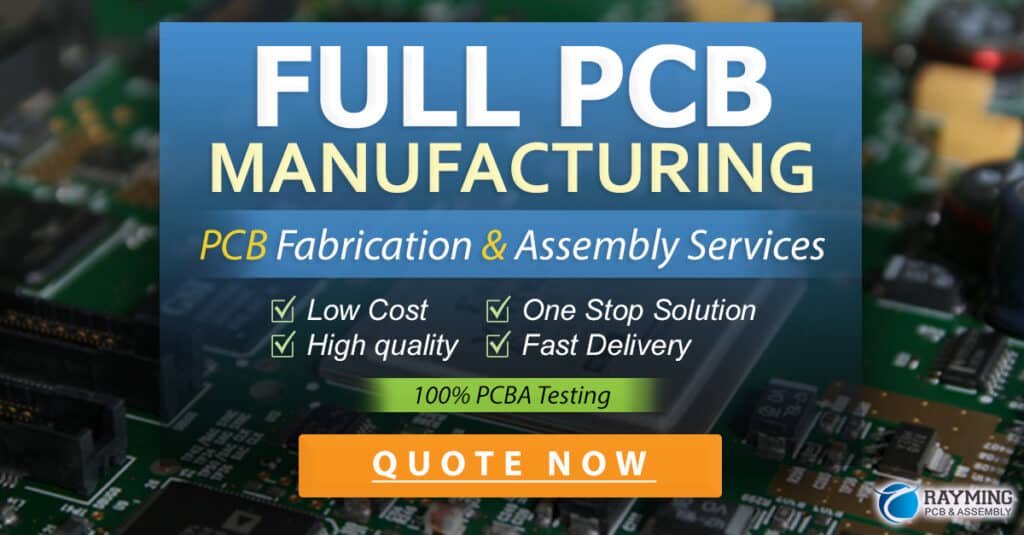
Types of Flux Used in PCBs
There are three main types of flux used in PCB assembly:
Rosin Flux
Rosin flux is a natural, non-conductive flux derived from pine tree sap. It is available in three activity levels:
Activity Level | Composition | Cleaning Required |
---|---|---|
Low (R) | Rosin + Solvent | Optional |
Intermediate (RMA) | Rosin + Solvent + Activators | Recommended |
High (RA) | Rosin + Solvent + Aggressive Activators | Required |
Rosin flux is widely used in electronics due to its excellent wetting properties and its ability to provide a protective coating on the soldered joint.
Water-Soluble Flux
Water-soluble flux is a highly active, inorganic acid flux that requires cleaning after soldering. It offers several advantages:
- Excellent oxide removal
- Superior wetting compared to rosin flux
- Easy to clean using water
However, water-soluble flux can be corrosive if not thoroughly cleaned, and the cleaning process adds an extra step to the assembly process.
No-Clean Flux
No-clean flux is a mild, low-residue flux that does not require cleaning after soldering. It is composed of weak organic acids and solvents that evaporate during the soldering process, leaving minimal residue. Benefits of no-clean flux include:
- Elimination of the cleaning step, reducing assembly time and costs
- Lower risk of damage to sensitive components during cleaning
- Compatibility with surface mount technology (SMT) and fine-pitch components
The main drawback of no-clean flux is that it may not be as effective at removing oxides as more active fluxes, which can lead to solderability issues on heavily oxidized surfaces.
Advantages of Using Flux in PCBs
Using flux in PCB assembly offers several key benefits:
- Improved solderability: Flux removes oxides and contaminants, promoting better wetting and stronger solder joints.
- Increased reliability: By ensuring clean metal surfaces and preventing re-oxidation, flux contributes to more reliable and consistent solder connections.
- Enhanced efficiency: Flux allows for faster and more efficient soldering, as it reduces the need for rework and touch-ups.
- Compatibility with various soldering methods: Flux can be used with hand soldering, wave soldering, and reflow soldering processes.
Disadvantages of Using Flux in PCBs
While the benefits of using flux are significant, there are also some potential drawbacks to consider:
- Residue: Some types of flux, particularly rosin and water-soluble fluxes, can leave residue on the PCB that may require cleaning.
- Corrosion: If not properly cleaned, certain fluxes can cause corrosion on the PCB and its components over time.
- Environmental concerns: Some flux formulations contain volatile organic compounds (VOCs) or other harmful substances that can have negative environmental impacts if not handled and disposed of properly.
Flux Application Methods
There are several methods for applying flux to a PCB during the assembly process:
Foam Fluxing
In foam fluxing, a tank filled with liquid flux is agitated to create a foam layer on the surface. The PCB is passed over the foam, which deposits a thin, even layer of flux on the board. This method is commonly used in wave soldering.
Spray Fluxing
Spray fluxing involves using a spray nozzle to apply a fine mist of flux to the PCB. This method allows for precise control over the amount and location of the flux application. Spray fluxing is often used in selective soldering processes.
Wave Fluxing
Wave fluxing is an inline process where the PCB is passed over a wave of molten solder. Just before the board enters the solder wave, a flux wave is applied to the bottom side of the PCB. This method ensures that the flux is applied evenly and only to the areas that will come into contact with the solder wave.
Cleaning Flux Residue
Depending on the type of flux used and the specific application requirements, cleaning the PCB after soldering may be necessary to remove flux residue. Cleaning methods include:
- Manual cleaning with solvents and brushes
- Automated cleaning using spray or immersion systems
- Vapor degreasing with solvents
It’s essential to choose a cleaning method that is compatible with the type of flux used and the components on the PCB to avoid damage.
Environmental Considerations
As environmental regulations become more stringent, there is a growing emphasis on using environmentally friendly flux formulations and minimizing the use of hazardous substances in PCB assembly. Some strategies for reducing the environmental impact of flux include:
- Using no-clean fluxes to eliminate the need for cleaning solvents
- Selecting flux formulations with low VOC content
- Implementing proper ventilation and filtration systems in the assembly area
- Disposing of used flux and cleaning solvents in accordance with local regulations
Frequently Asked Questions (FAQ)
-
Q: Can I use flux for rework and repair on PCBs?
A: Yes, flux can be used for rework and repair on PCBs. Apply a small amount of flux to the area being reworked to help remove oxides and promote better solderability. -
Q: How often should I change the flux in my wave soldering machine?
A: The frequency of flux change depends on factors such as the type of flux, the volume of PCBs being processed, and the level of contamination. Generally, it’s recommended to monitor the flux quality regularly and change it when it becomes excessively contaminated or loses its effectiveness. -
Q: Can I mix different types of flux?
A: Mixing different types of flux is not recommended, as they may have different chemical compositions and activity levels that could lead to unexpected results or compatibility issues. It’s best to use the flux type specified for your particular application. -
Q: How can I test the effectiveness of my flux?
A: Several methods can be used to test flux effectiveness, including: - Wetting balance test: Measures the wetting force and time of a solder ball on a fluxed surface
- Copper mirror test: Assesses the corrosivity and activity level of the flux
-
Surface insulation resistance (SIR) test: Evaluates the impact of flux residue on the electrical insulation properties of the PCB
-
Q: Are there any health risks associated with handling flux?
A: Some fluxes contain chemicals that can be harmful if inhaled or come into contact with skin. Always follow the manufacturer’s safety guidelines, use appropriate personal protective equipment (PPE), and work in a well-ventilated area when handling flux.
Conclusion
Flux is a critical component in the PCB assembly process, ensuring clean metal surfaces, improving solderability, and promoting the formation of strong, reliable solder joints. By understanding the different types of flux available, their advantages and disadvantages, and proper application and cleaning methods, you can optimize your PCB assembly process and produce high-quality, reliable electronic devices.
As environmental concerns continue to drive change in the electronics industry, it’s essential to stay informed about advances in flux technology and to adopt environmentally friendly practices wherever possible. By carefully selecting the appropriate flux for your application and implementing proper handling and disposal procedures, you can minimize the environmental impact of your PCB assembly process while still achieving excellent results.
Leave a Reply