What are the Key Features of Rigid Flex PCB?
1. Combination of Rigid and Flexible Substrates
The most distinguishing feature of a rigid-flex PCB is its ability to incorporate both rigid and flexible substrates within a single board. The rigid portions of the board provide structural support and house components that require stability, while the flexible portions allow for bending, folding, and twisting, enabling the board to fit into tight spaces or conform to unique shapes.
2. Multi-Layer Construction
Rigid-flex PCBs can be designed with multiple layers, allowing for greater circuit density and functionality. The number of layers can vary depending on the complexity of the design, with some boards having up to 20 or more layers. This multi-layer construction enables the integration of power, ground, and signal planes, as well as embedded components and interconnects.
3. High Reliability
Rigid-flex PCBs offer superior reliability compared to traditional PCBs. The flexible portions of the board are designed to withstand repeated bending and flexing without causing damage to the traces or components. Additionally, the use of advanced materials and manufacturing techniques ensures that rigid-flex PCBs can operate reliably in harsh environments, such as those with extreme temperatures, vibrations, or shock.
4. Space and Weight Savings
By combining rigid and flexible substrates, rigid-flex PCBs enable designers to create more compact and lightweight electronic devices. The ability to fold and bend the board allows for better utilization of available space, reducing the overall size of the device. This is particularly advantageous in applications where space and weight are critical factors, such as in aerospace, military, and medical devices.
What are the Applications of Rigid Flex PCB?
Rigid-flex PCBs find applications in a wide range of industries and products, thanks to their unique combination of flexibility, reliability, and space-saving features. Some of the most common applications include:
-
Aerospace and Defense: Rigid-flex PCBs are extensively used in aerospace and defense applications, where high reliability, compact size, and lightweight design are essential. They are found in avionics systems, satellites, missiles, and unmanned aerial vehicles (UAVs).
-
Medical Devices: The healthcare industry relies on rigid-flex PCBs for various medical devices, such as wearable monitors, implantable devices, and surgical instruments. The flexibility and compact size of rigid-flex PCBs make them ideal for these applications, where patient comfort and device miniaturization are crucial.
-
Automotive Electronics: As vehicles become increasingly complex and feature-rich, rigid-flex PCBs are being used to enable advanced driver assistance systems (ADAS), infotainment systems, and other electronic components. The ability to withstand harsh environments and vibrations makes rigid-flex PCBs well-suited for automotive applications.
-
Consumer Electronics: Rigid-flex PCBs are found in a variety of consumer electronic devices, such as smartphones, tablets, laptops, and wearables. The compact size and flexibility of these boards allow for the creation of sleek, lightweight, and highly functional devices that meet consumer demands.
-
Industrial Equipment: In industrial settings, rigid-flex PCBs are used in equipment such as robotics, automation systems, and process control devices. The ability to withstand extreme temperatures, vibrations, and other harsh conditions makes rigid-flex PCBs a reliable choice for industrial applications.
What are the Advantages of Using Rigid Flex PCB?
Rigid-flex PCBs offer several key advantages over traditional PCBs, making them an attractive choice for a wide range of applications. Some of the most notable benefits include:
1. Enhanced Design Flexibility
The ability to combine rigid and flexible substrates within a single board gives designers unprecedented freedom to create complex, three-dimensional structures. This flexibility allows for the creation of devices with unique shapes and configurations, enabling better integration with mechanical components and improved overall device functionality.
2. Improved Signal Integrity
Rigid-flex PCBs offer superior signal integrity compared to traditional PCBs. The use of advanced materials and manufacturing techniques minimizes signal loss, crosstalk, and electromagnetic interference (EMI). This is particularly important in high-speed and high-frequency applications, where maintaining signal integrity is critical for optimal performance.
3. Increased Durability and Reliability
The flexible portions of a rigid-flex PCB are designed to withstand repeated bending and flexing without compromising the integrity of the traces or components. This increased durability translates to higher reliability, as the board is less susceptible to damage caused by mechanical stress or vibrations. Additionally, rigid-flex PCBs can be designed to operate reliably in harsh environments, such as those with extreme temperatures or exposure to moisture and chemicals.
4. Reduced Size and Weight
By combining rigid and flexible substrates, rigid-flex PCBs enable designers to create more compact and lightweight electronic devices. The ability to fold and bend the board allows for better utilization of available space, reducing the overall size of the device. This is particularly advantageous in applications where space and weight are critical factors, such as in aerospace, military, and medical devices.
5. Simplified Assembly and Lower Costs
Rigid-flex PCBs can help simplify the assembly process and reduce overall manufacturing costs. By integrating multiple circuit boards into a single rigid-flex board, designers can eliminate the need for connectors and cables, reducing the number of components and assembly steps required. This streamlined assembly process can lead to lower labor costs, shorter production times, and improved product reliability.
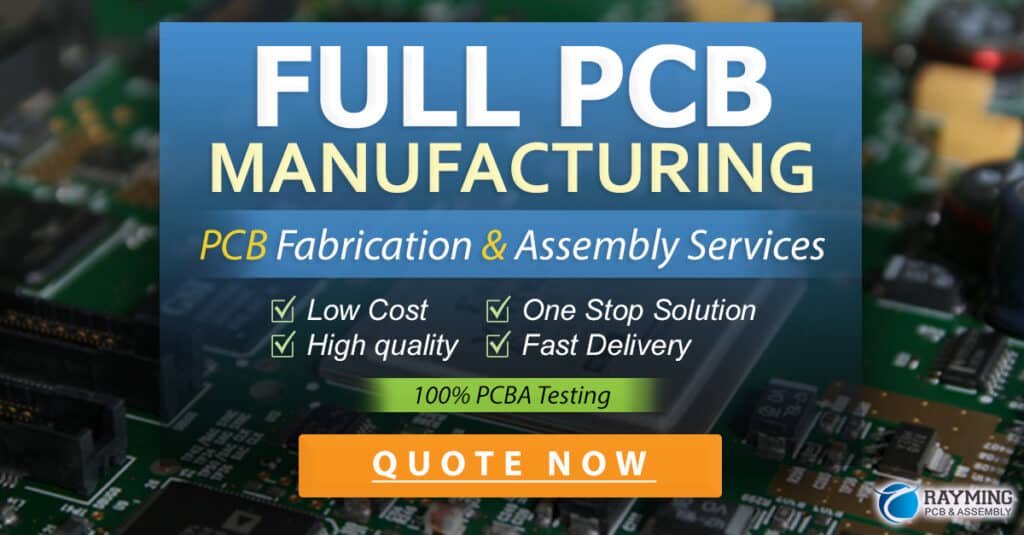
What are the Challenges Associated with Rigid Flex PCB?
While rigid-flex PCBs offer numerous benefits, there are also some challenges associated with their design, manufacture, and use. Some of the most significant challenges include:
1. Complex Design Process
Designing a rigid-flex PCB is more complex than designing a traditional rigid PCB. Designers must carefully consider the placement of components, the routing of traces, and the positioning of the flexible portions to ensure optimal performance and reliability. This complexity often requires specialized design software and expertise, which can increase development time and costs.
2. Higher Material and Manufacturing Costs
Rigid-flex PCBs typically require more advanced materials and manufacturing processes compared to traditional PCBs. The use of flexible substrates, specialized adhesives, and multi-layer construction can increase material costs. Additionally, the manufacturing process for rigid-flex PCBs is more complex and requires specialized equipment and expertise, which can result in higher production costs.
3. Limited Supplier Options
Due to the specialized nature of rigid-flex PCBs, there are fewer suppliers capable of manufacturing these boards compared to traditional PCBs. This limited supplier pool can result in longer lead times, higher costs, and reduced flexibility in sourcing options.
4. Difficulty in Rework and Repair
Reworking or repairing a rigid-flex PCB can be more challenging than a traditional rigid PCB. The presence of flexible substrates and the compact nature of the board can make it more difficult to access and replace components without causing damage to the surrounding areas. This can lead to increased rework times and costs, as well as a higher risk of board failure.
Frequently Asked Questions (FAQ)
1. What is the difference between a rigid PCB and a flex rigid PCB?
A rigid PCB is a traditional printed circuit board that is made entirely of rigid substrates, such as FR-4. In contrast, a flex rigid PCB combines both rigid and flexible substrates within a single board, allowing for bending, folding, and twisting of the flexible portions while maintaining the stability of the rigid sections.
2. Can rigid-flex PCBs be used in high-temperature environments?
Yes, rigid-flex PCBs can be designed to operate reliably in high-temperature environments. The use of advanced materials, such as polyimide or polytetrafluoroethylene (PTFE), can ensure that the board maintains its structural integrity and performance even when exposed to extreme temperatures.
3. How many layers can a rigid-flex PCB have?
The number of layers in a rigid-flex PCB can vary depending on the complexity of the design and the application requirements. Some rigid-flex PCBs can have up to 20 or more layers, including a combination of rigid and flexible layers. However, the most common configurations range from 4 to 12 layers.
4. Are rigid-flex PCBs more expensive than traditional rigid PCBs?
Yes, rigid-flex PCBs are generally more expensive than traditional rigid PCBs. The higher costs are attributed to the use of advanced materials, specialized manufacturing processes, and the need for expert design and assembly. However, the benefits of using rigid-flex PCBs, such as improved reliability, space savings, and design flexibility, often outweigh the increased costs in many applications.
5. What are the typical applications for rigid-flex PCBs?
Rigid-flex PCBs find applications in a wide range of industries, including:
– Aerospace and defense (avionics, satellites, missiles, UAVs)
– Medical devices (wearables, implantables, surgical instruments)
– Automotive electronics (ADAS, infotainment systems)
– Consumer electronics (smartphones, tablets, laptops, wearables)
– Industrial equipment (robotics, automation systems, process control devices)
In summary, flex rigid PCBs offer a unique combination of flexibility and rigidity, enabling the creation of highly complex, reliable, and compact electronic devices. Despite the challenges associated with their design and manufacture, the numerous benefits they offer make them an increasingly popular choice for a wide range of applications across various industries.
Leave a Reply