Introduction to Epoxy PCB Boards
An epoxy printed circuit board (PCB) is a type of circuit board that uses epoxy resin as the base material. Epoxy PCBs offer several advantages over traditional fiberglass-based PCBs, including better thermal and mechanical properties, improved electrical insulation, and higher resistance to moisture and chemicals. These properties make epoxy PCBs ideal for use in a wide range of applications, from consumer electronics to industrial equipment and aerospace systems.
Composition of Epoxy PCBs
Epoxy PCBs are made by combining a woven glass fabric with an epoxy resin. The glass fabric provides mechanical strength and dimensional stability, while the epoxy resin acts as a binder and provides electrical insulation. The combination of these two materials results in a composite material that has excellent thermal, mechanical, and electrical properties.
The most common type of epoxy resin used in PCBs is called FR-4 (Flame Retardant 4). FR-4 is a brominated epoxy resin that has been treated with flame retardants to improve its fire resistance. Other types of epoxy resins, such as high-Tg (glass transition temperature) resins, may be used in applications that require higher thermal stability or improved mechanical properties.
Manufacturing Process of Epoxy PCBs
The manufacturing process of epoxy PCBs involves several steps:
-
Preparing the substrate: The first step is to create the substrate, which is made by impregnating a woven glass fabric with epoxy resin. The substrate is then cured under heat and pressure to form a solid, stable material.
-
Applying the copper layer: A thin layer of copper is then applied to one or both sides of the substrate using a process called electroless plating. This copper layer will form the conductive traces and pads on the PCB.
-
Patterning the copper layer: The copper layer is then patterned using a photolithographic process. This involves applying a light-sensitive resist to the copper layer, exposing it to light through a patterned mask, and then etching away the unwanted copper to create the desired circuit pattern.
-
Applying the solder mask: A solder mask is then applied to the PCB to protect the copper traces and prevent short circuits. The solder mask is typically green in color, but other colors may be used for aesthetic or functional purposes.
-
Applying the silkscreen: Finally, a silkscreen layer is applied to the PCB to add text, logos, and other markings. This layer is typically white in color and is used to identify components and provide assembly instructions.
Advantages of Epoxy PCBs
Epoxy PCBs offer several advantages over traditional fiberglass-based PCBs:
Better Thermal Properties
Epoxy resins have a higher glass transition temperature (Tg) than traditional fiberglass-based materials. This means that epoxy PCBs can withstand higher temperatures without deforming or losing their mechanical properties. This is particularly important in applications where the PCB may be exposed to high temperatures, such as in power electronics or automotive systems.
Improved Mechanical Properties
Epoxy PCBs have better mechanical properties than traditional fiberglass-based PCBs. They are stronger, more rigid, and less prone to warping or twisting. This makes them ideal for use in applications where the PCB may be subjected to mechanical stress, such as in aerospace or military systems.
Higher Resistance to Moisture and Chemicals
Epoxy resins are highly resistant to moisture and chemicals. This makes epoxy PCBs ideal for use in harsh environments where the PCB may be exposed to water, humidity, or corrosive chemicals. This is particularly important in industrial or marine applications where the PCB may be subjected to harsh conditions.
Better Electrical Insulation
Epoxy resins have excellent electrical insulation properties. This means that epoxy PCBs can provide better isolation between conductive traces and reduce the risk of short circuits or signal interference. This is particularly important in high-frequency or high-voltage applications where signal integrity is critical.
Applications of Epoxy PCBs
Epoxy PCBs are used in a wide range of applications, including:
Consumer Electronics
Epoxy PCBs are commonly used in consumer electronics, such as smartphones, tablets, and laptops. They offer good thermal and mechanical properties, as well as excellent electrical insulation, which is important for ensuring the reliability and performance of these devices.
Industrial Equipment
Epoxy PCBs are also used in industrial equipment, such as motors, sensors, and control systems. They offer high resistance to moisture and chemicals, as well as good thermal and mechanical properties, which is important for ensuring the reliability and durability of these systems in harsh industrial environments.
Aerospace Systems
Epoxy PCBs are used in aerospace systems, such as avionics, satellites, and spacecraft. They offer excellent thermal and mechanical properties, as well as high resistance to moisture and chemicals, which is critical for ensuring the reliability and performance of these systems in the extreme conditions of space.
Automotive Electronics
Epoxy PCBs are increasingly being used in automotive electronics, such as engine control units, infotainment systems, and advanced driver assistance systems (ADAS). They offer good thermal and mechanical properties, as well as high resistance to moisture and chemicals, which is important for ensuring the reliability and durability of these systems in the harsh automotive environment.
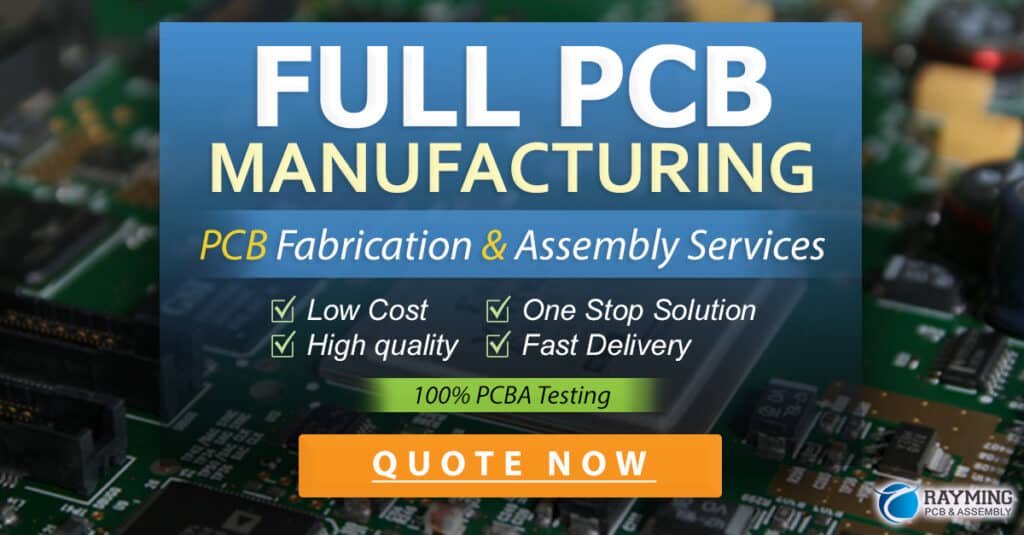
Comparison of Epoxy PCBs with Other PCB Materials
Epoxy PCBs offer several advantages over other PCB materials, such as:
Epoxy PCBs vs. Fiberglass PCBs
Fiberglass PCBs are the most common type of PCB material. They are made by combining a woven fiberglass fabric with a resin, typically epoxy or polyimide. Fiberglass PCBs offer good mechanical and electrical properties, but they are not as thermally stable or chemically resistant as epoxy PCBs.
Property | Epoxy PCBs | Fiberglass PCBs |
---|---|---|
Thermal stability | High | Moderate |
Mechanical strength | High | Moderate |
Chemical resistance | High | Moderate |
Electrical insulation | Excellent | Good |
Cost | High | Moderate |
Epoxy PCBs vs. Ceramic PCBs
Ceramic PCBs are made from a ceramic material, typically alumina or beryllia. They offer excellent thermal and mechanical properties, as well as high resistance to moisture and chemicals. However, they are more expensive and difficult to manufacture than epoxy PCBs.
Property | Epoxy PCBs | Ceramic PCBs |
---|---|---|
Thermal stability | High | Excellent |
Mechanical strength | High | Excellent |
Chemical resistance | High | Excellent |
Electrical insulation | Excellent | Excellent |
Cost | High | Very high |
Epoxy PCBs vs. Metal Core PCBs
Metal core PCBs are made by bonding a metal substrate, typically aluminum or copper, to a dielectric layer and a copper foil. They offer excellent thermal conductivity and heat dissipation, which is important for applications that generate a lot of heat. However, they are more expensive and have lower electrical insulation than epoxy PCBs.
Property | Epoxy PCBs | Metal Core PCBs |
---|---|---|
Thermal conductivity | Moderate | Excellent |
Mechanical strength | High | High |
Chemical resistance | High | Moderate |
Electrical insulation | Excellent | Moderate |
Cost | High | Very high |
Challenges and Limitations of Epoxy PCBs
Despite their many advantages, epoxy PCBs also have some challenges and limitations:
Higher Cost
Epoxy PCBs are more expensive than traditional fiberglass-based PCBs. This is due to the higher cost of the raw materials and the more complex manufacturing process. However, the higher cost may be justified in applications that require the superior thermal, mechanical, and electrical properties of epoxy PCBs.
Limited Flexibility
Epoxy PCBs are more rigid and less flexible than traditional fiberglass-based PCBs. This can be a limitation in applications that require the PCB to be bent or flexed, such as in wearable devices or flexible electronics. However, this can also be an advantage in applications that require high mechanical stability and durability.
Difficulty in Reworking
Epoxy PCBs are more difficult to rework than traditional fiberglass-based PCBs. This is because the epoxy resin is a thermoset material that cannot be easily melted or reshaped once it has been cured. This can make it more challenging to repair or modify the PCB if changes are needed.
Future Trends and Developments in Epoxy PCBs
Epoxy PCBs are constantly evolving to meet the changing needs of the electronics industry. Some of the latest trends and developments in epoxy PCBs include:
High-Speed Digital Applications
Epoxy PCBs are increasingly being used in high-speed digital applications, such as 5G networks, data centers, and high-performance computing. These applications require PCBs with high signal integrity, low dielectric loss, and excellent thermal management. Epoxy PCBs with advanced materials, such as low-loss dielectrics and high-conductivity copper, are being developed to meet these requirements.
Miniaturization and High-Density Interconnects
As electronic devices continue to shrink in size and increase in functionality, there is a growing need for PCBs with smaller features and higher-density interconnects. Epoxy PCBs with advanced manufacturing technologies, such as microvias and embedded components, are being developed to enable the miniaturization of electronic devices.
Environmental Sustainability
There is a growing demand for environmentally sustainable PCBs that are free from hazardous substances and can be easily recycled or disposed of at the end of their life. Epoxy PCBs with halogen-free flame retardants and biodegradable materials are being developed to meet these requirements.
Conclusion
Epoxy PCBs are a versatile and high-performance alternative to traditional fiberglass-based PCBs. They offer superior thermal, mechanical, and electrical properties, as well as high resistance to moisture and chemicals. These properties make them ideal for use in a wide range of applications, from consumer electronics to industrial equipment and aerospace systems.
While epoxy PCBs have some challenges and limitations, such as higher cost and limited flexibility, they are constantly evolving to meet the changing needs of the electronics industry. With advanced materials, manufacturing technologies, and environmental sustainability, epoxy PCBs are poised to play a critical role in the future of electronics.
Frequently Asked Questions (FAQ)
-
What is the difference between epoxy PCBs and fiberglass PCBs?
Epoxy PCBs are made by combining a woven glass fabric with an epoxy resin, while fiberglass PCBs are made by combining a woven fiberglass fabric with a resin, typically epoxy or polyimide. Epoxy PCBs offer better thermal and mechanical properties, as well as higher resistance to moisture and chemicals, compared to fiberglass PCBs. -
Can epoxy PCBs be used in high-temperature applications?
Yes, epoxy PCBs have a higher glass transition temperature (Tg) than traditional fiberglass-based materials, which means they can withstand higher temperatures without deforming or losing their mechanical properties. This makes them suitable for use in applications where the PCB may be exposed to high temperatures, such as in power electronics or automotive systems. -
Are epoxy PCBs more expensive than other types of PCBs?
Yes, epoxy PCBs are generally more expensive than traditional fiberglass-based PCBs due to the higher cost of the raw materials and the more complex manufacturing process. However, the higher cost may be justified in applications that require the superior thermal, mechanical, and electrical properties of epoxy PCBs. -
Can epoxy PCBs be used in flexible electronics?
Epoxy PCBs are more rigid and less flexible than traditional fiberglass-based PCBs, which can be a limitation in applications that require the PCB to be bent or flexed, such as in wearable devices or flexible electronics. However, this can also be an advantage in applications that require high mechanical stability and durability. -
What are some of the latest trends and developments in epoxy PCBs?
Some of the latest trends and developments in epoxy PCBs include their use in high-speed digital applications, miniaturization and high-density interconnects, and environmental sustainability. Epoxy PCBs with advanced materials, manufacturing technologies, and environmentally friendly features are being developed to meet the changing needs of the electronics industry.
Leave a Reply