Introduction to ENIG PCB
ENIG, which stands for Electroless Nickel Immersion Gold, is a surface finish used on printed circuit boards (PCBs). It is a chemical process that deposits a thin layer of nickel followed by a thin layer of gold on the exposed copper pads and other areas of the PCB that require protection and enhanced solderability.
ENIG has become one of the most popular surface finishes in the PCB industry due to its excellent properties, which include:
- Flat surface finish
- Good solderability
- Corrosion resistance
- Excellent shelf life
- Compatibility with lead-free soldering processes
- Suitable for fine-pitch components
In this article, we will delve deeper into what ENIG is, how it is applied, its advantages and disadvantages, and its applications in various industries.
The ENIG Process
The ENIG process involves several steps that are carefully controlled to ensure a high-quality finish. Here is a brief overview of the ENIG process:
-
Cleaning: The PCB is thoroughly cleaned to remove any contaminants or debris that could interfere with the plating process.
-
Microetching: The exposed copper surfaces are microetched to create a rough surface that will promote adhesion of the nickel layer.
-
Activation: The PCB is immersed in a palladium-based activator solution, which creates a catalytic surface for the nickel deposition.
-
Electroless Nickel Plating: The PCB is immersed in an electroless nickel plating solution, which deposits a thin layer of nickel (typically 3-6 µm) on the activated surfaces. The nickel acts as a barrier layer, preventing the diffusion of copper into the gold layer.
-
Immersion Gold Plating: The nickel-plated PCB is then immersed in an immersion gold solution, which deposits a thin layer of gold (typically 0.05-0.2 µm) on top of the nickel. The gold layer provides excellent solderability and protects the nickel from oxidation.
-
Rinsing and Drying: The PCB is rinsed with deionized water and dried to remove any residual chemicals.
The entire ENIG process is carefully monitored and controlled to ensure consistent quality and uniformity of the surface finish.
Advantages of ENIG PCB
ENIG PCBs offer several advantages over other surface finishes, making them a popular choice for many applications. Some of the key advantages of ENIG include:
-
Excellent Solderability: The thin gold layer provides excellent solderability, allowing for easy and reliable soldering of components to the PCB.
-
Flat Surface Finish: ENIG creates a flat, planar surface finish that is ideal for fine-pitch components and wire bonding applications.
-
Corrosion Resistance: The nickel layer acts as a barrier, preventing the diffusion of copper and providing excellent corrosion resistance.
-
Extended Shelf Life: ENIG PCBs have a long shelf life, typically up to 12 months, without significant degradation of solderability or surface finish quality.
-
Compatibility with Lead-Free Soldering: ENIG is compatible with lead-free soldering processes, making it a suitable choice for RoHS-compliant products.
-
Durability: The nickel and gold layers provide a durable surface finish that can withstand multiple soldering cycles and harsh environmental conditions.
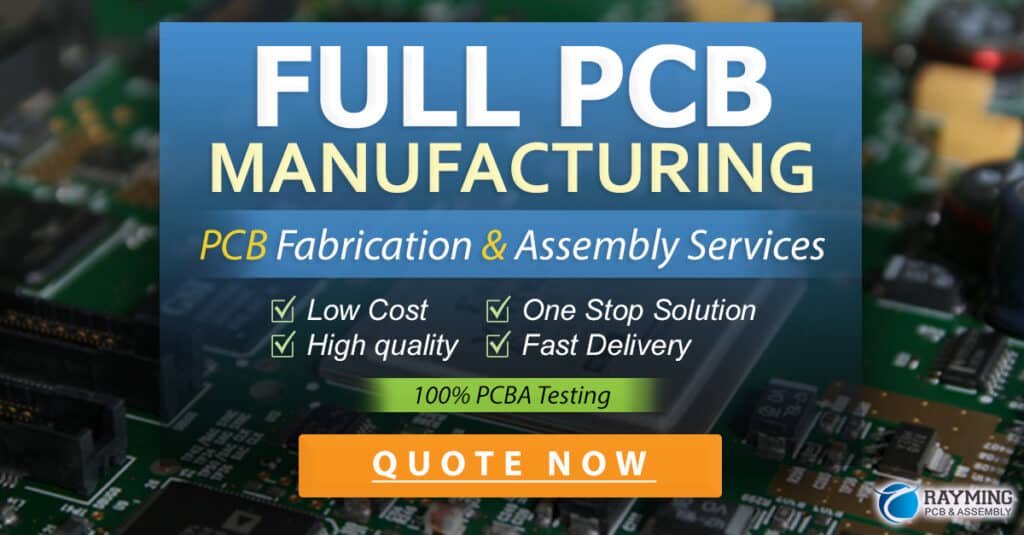
Disadvantages of ENIG PCB
Despite its many advantages, ENIG also has some disadvantages that should be considered when selecting a surface finish for a PCB. Some of the main disadvantages of ENIG include:
-
Higher Cost: ENIG is generally more expensive than other surface finishes like HASL (Hot Air Solder Leveling) or OSP (Organic Solderability Preservative) due to the use of gold and the multi-step process involved.
-
Black Pad: In some cases, the nickel layer can become brittle and separate from the copper, creating a “black pad” defect. This can lead to poor solderability and reduced reliability of the PCB.
-
Hyper-Corrosion: If the gold layer is too thin or has pinholes, the underlying nickel can be exposed to the environment, leading to rapid corrosion in the presence of moisture and an galvanic potential difference.
-
Limited Rework Capability: Reworking ENIG PCBs can be challenging, as the gold layer must be removed before soldering, and the nickel layer can be difficult to remove without damaging the copper pads.
Applications of ENIG PCB
ENIG PCBs are used in a wide range of industries and applications due to their excellent properties and reliability. Some of the common applications of ENIG PCBs include:
-
Consumer Electronics: ENIG is widely used in consumer electronics, such as smartphones, tablets, laptops, and wearables, where high-density packaging and reliability are critical.
-
Automotive Electronics: ENIG PCBs are used in automotive applications, such as engine control units, infotainment systems, and advanced driver assistance systems (ADAS), where they must withstand harsh environmental conditions and vibration.
-
Medical Devices: ENIG is used in medical devices, such as implantable devices, diagnostic equipment, and monitoring systems, where reliability and long-term stability are essential.
-
Aerospace and Defense: ENIG PCBs are used in aerospace and defense applications, such as avionics, radar systems, and satellite communications, where they must meet stringent reliability and performance requirements.
-
Industrial Equipment: ENIG is used in industrial equipment, such as process control systems, automation equipment, and power electronics, where durability and resistance to harsh environments are important.
ENIG vs. Other Surface Finishes
ENIG is just one of many surface finishes available for PCBs. Here is a comparison of ENIG with some other popular surface finishes:
Surface Finish | Advantages | Disadvantages |
---|---|---|
ENIG | – Excellent solderability – Flat surface – Corrosion resistance – Long shelf life |
– Higher cost – Potential for black pad and hyper-corrosion – Limited rework capability |
HASL (Hot Air Solder Leveling) | – Low cost – Good solderability – Suitable for leaded soldering |
– Non-planar surface – Thermal shock to PCB – Not suitable for fine-pitch components |
OSP (Organic Solderability Preservative) | – Low cost – Flat surface – Suitable for fine-pitch components |
– Limited shelf life – Sensitive to handling and storage conditions – Not suitable for multiple soldering cycles |
Immersion Silver | – Excellent solderability – Flat surface – Lower cost than ENIG |
– Limited shelf life – Prone to tarnishing and oxidation – Potential for silver migration |
Immersion Tin | – Good solderability – Flat surface – Lower cost than ENIG |
– Limited shelf life – Prone to tin whiskers – Not suitable for lead-free soldering |
The choice of surface finish depends on the specific requirements of the application, such as cost, solderability, shelf life, and compatibility with the assembly process.
Quality Control and Testing of ENIG PCB
To ensure the quality and reliability of ENIG PCBs, several quality control measures and testing procedures are employed during and after the manufacturing process. Some of the key quality control and testing methods include:
-
Visual Inspection: The PCBs are visually inspected for any defects, such as voids, pinholes, or discoloration in the surface finish.
-
Thickness Measurement: The thickness of the nickel and gold layers is measured using X-ray fluorescence (XRF) or cross-sectional analysis to ensure they meet the specified requirements.
-
Solderability Testing: The solderability of the ENIG surface is tested using wetting balance or dip-and-look methods to ensure good wettability and spreading of solder.
-
Adhesion Testing: The adhesion of the nickel and gold layers to the copper substrate is tested using a peel or tape test to ensure adequate bonding strength.
-
Porosity Testing: The porosity of the nickel layer is tested using a sulfur dioxide (SO2) or nitric acid vapor test to detect any pinholes or defects that could lead to hyper-corrosion.
-
Ionic Contamination Testing: The PCBs are tested for ionic contamination using a resistivity of solvent extract (ROSE) test or ion chromatography to ensure the cleanliness of the surface.
-
Accelerated Life Testing: The PCBs are subjected to accelerated life testing, such as thermal cycling or humidity exposure, to evaluate their long-term reliability under simulated environmental conditions.
By implementing these quality control measures and testing procedures, manufacturers can ensure that ENIG PCBs meet the required quality standards and perform reliably in their intended applications.
Future Trends in ENIG PCB
As the electronics industry continues to evolve, there are several trends and developments in ENIG PCB technology that are expected to shape its future. Some of the key trends include:
-
Thinner Gold Layers: There is a trend towards using thinner gold layers (0.05-0.1 µm) to reduce costs and improve the environmental sustainability of ENIG PCBs.
-
Alternative Nickel Processes: Researchers are exploring alternative nickel plating processes, such as electroless nickel-boron (EN-B) or electroless nickel-phosphorus (EN-P), to mitigate the risk of black pad defects and improve the reliability of ENIG PCBs.
-
Advanced Inspection Techniques: The use of advanced inspection techniques, such as automated optical inspection (AOI) and 3D x-ray inspection, is becoming more common to detect surface finish defects and ensure the quality of ENIG PCBs.
-
Environmental Sustainability: There is a growing emphasis on developing environmentally friendly ENIG processes that reduce the use of hazardous chemicals and minimize waste generation.
-
High-Frequency Applications: ENIG PCBs are finding increasing use in high-frequency applications, such as 5G wireless communication and millimeter-wave radar, due to their excellent surface finish and signal integrity properties.
As these trends continue to evolve, ENIG PCB technology is expected to remain a key enabler for the development of advanced electronic products and systems.
FAQ
-
What does ENIG stand for?
ENIG stands for Electroless Nickel Immersion Gold, which is a surface finish applied to printed circuit boards (PCBs). -
What are the main advantages of ENIG PCBs?
The main advantages of ENIG PCBs include excellent solderability, a flat surface finish, corrosion resistance, long shelf life, compatibility with lead-free soldering, and durability. -
What are the potential issues with ENIG PCBs?
Some potential issues with ENIG PCBs include higher cost compared to other surface finishes, the potential for black pad defects and hyper-corrosion, and limited rework capability. -
What industries commonly use ENIG PCBs?
ENIG PCBs are commonly used in industries such as consumer electronics, automotive electronics, medical devices, aerospace and defense, and industrial equipment. -
How can the quality of ENIG PCBs be ensured?
The quality of ENIG PCBs can be ensured through various quality control measures and testing procedures, such as visual inspection, thickness measurement, solderability testing, adhesion testing, porosity testing, ionic contamination testing, and accelerated life testing.
Conclusion
ENIG (Electroless Nickel Immersion Gold) is a widely used surface finish for printed circuit boards (PCBs) that offers excellent solderability, a flat surface finish, corrosion resistance, and long shelf life. The ENIG process involves depositing a thin layer of nickel followed by a thin layer of gold on the exposed copper surfaces of the PCB.
While ENIG PCBs offer many advantages, they also have some potential drawbacks, such as higher cost, the risk of black pad defects and hyper-corrosion, and limited rework capability. Despite these challenges, ENIG remains a popular choice for a wide range of industries and applications, including consumer electronics, automotive electronics, medical devices, aerospace and defense, and industrial equipment.
To ensure the quality and reliability of ENIG PCBs, manufacturers employ various quality control measures and testing procedures, such as visual inspection, thickness measurement, solderability testing, and accelerated life testing. As the electronics industry continues to evolve, ENIG PCB technology is expected to adapt to new trends and requirements, such as thinner gold layers, alternative nickel processes, advanced inspection techniques, environmental sustainability, and high-frequency applications.
By understanding the properties, advantages, and limitations of ENIG PCBs, engineers and designers can make informed decisions when selecting a surface finish for their specific application, ensuring optimal performance, reliability, and cost-effectiveness.
Leave a Reply